woody is using BMX cranks because they allow very small sprockets. Below is one of two assemblies before welding. The bottom bracket was turned on the lathe, and the two plates were made by sendcutsend.
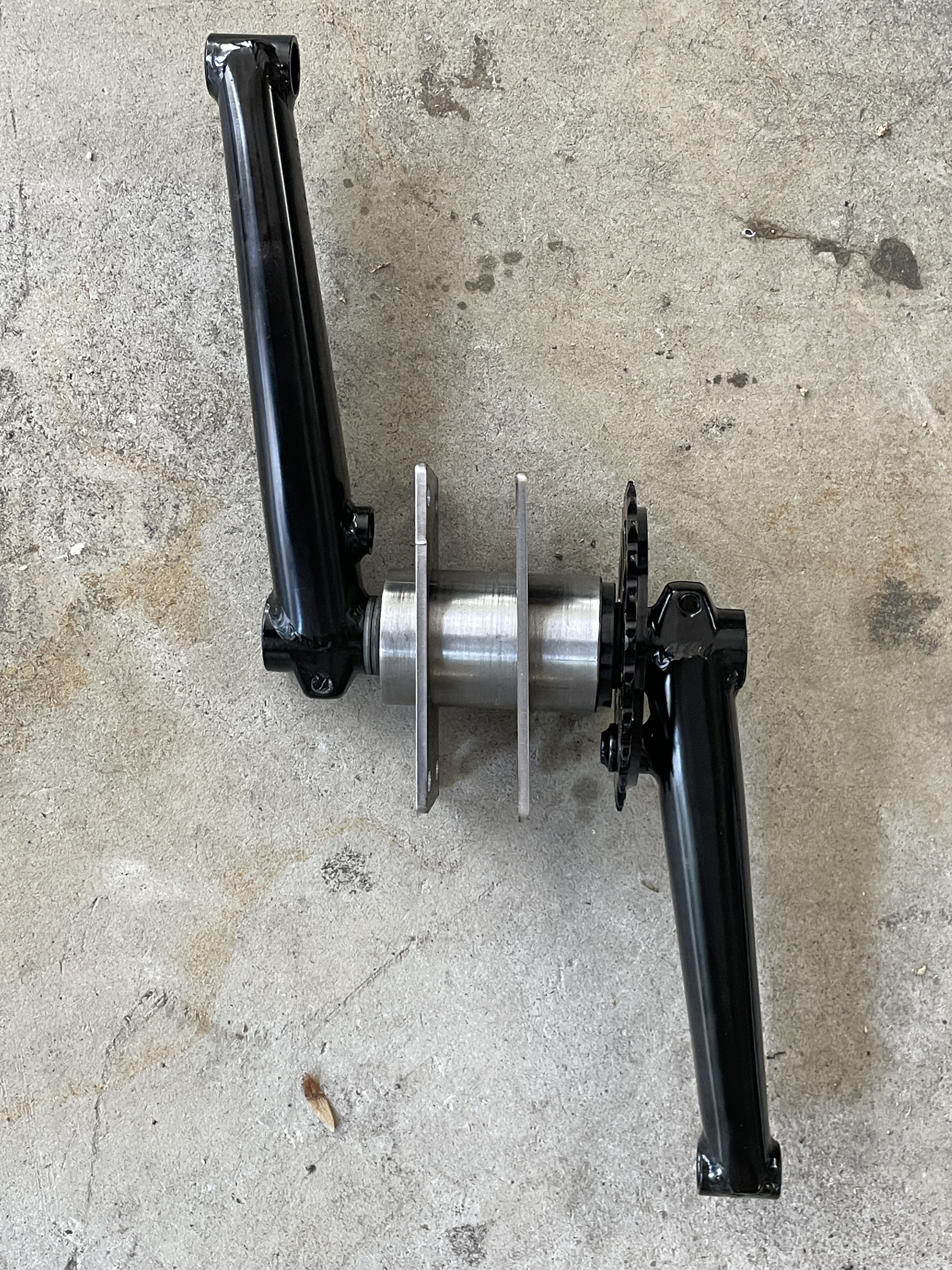
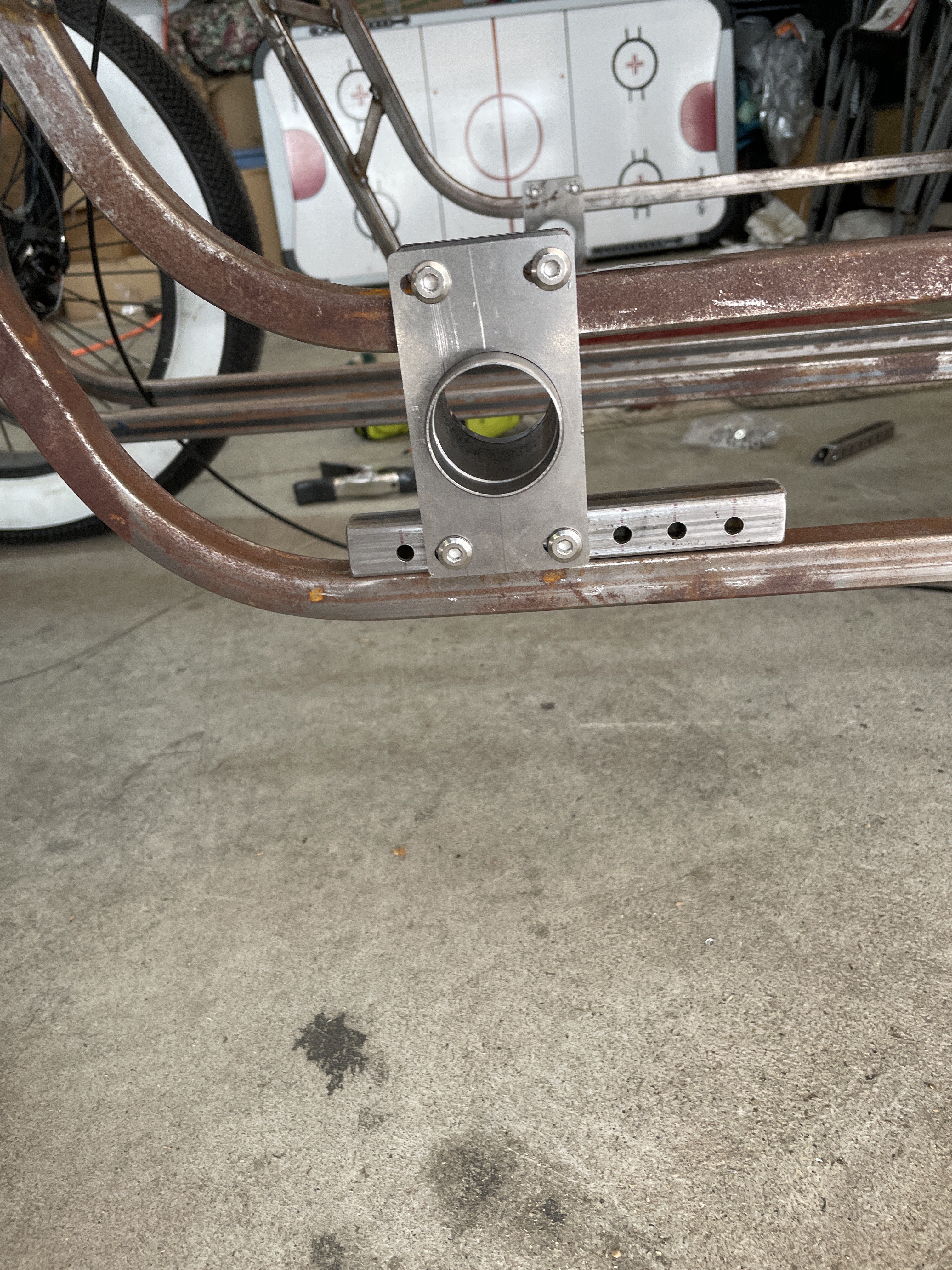
And here it is bolted in place. The holes are slightly more than 0.75” long to allow chain tensioning. The lower piece was added to help raise the crank height a bit.
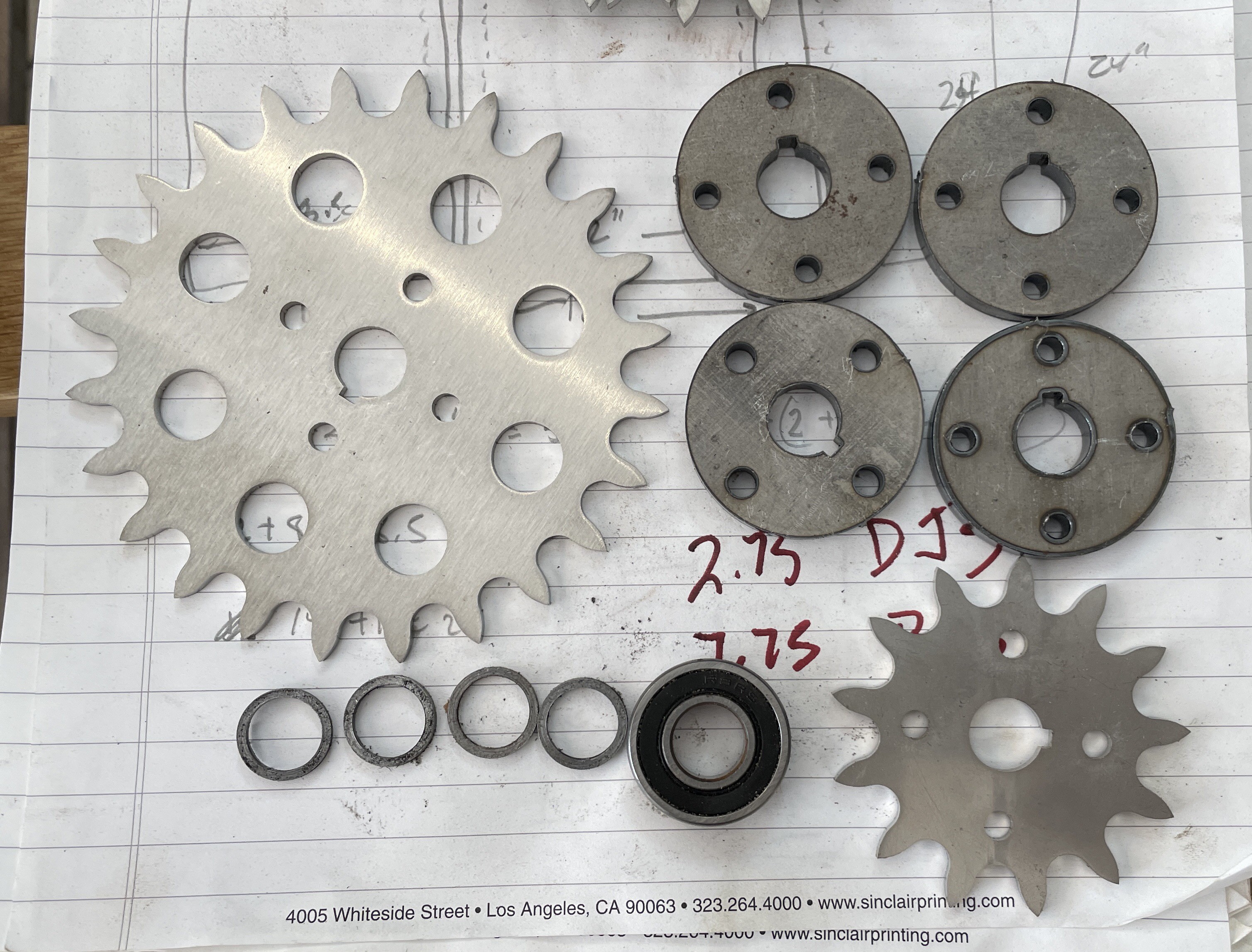
These are the sprockets, bearings, sprocket flanges as well as some small washers cut on the lathe to prevent rubbing against the bearing seals.
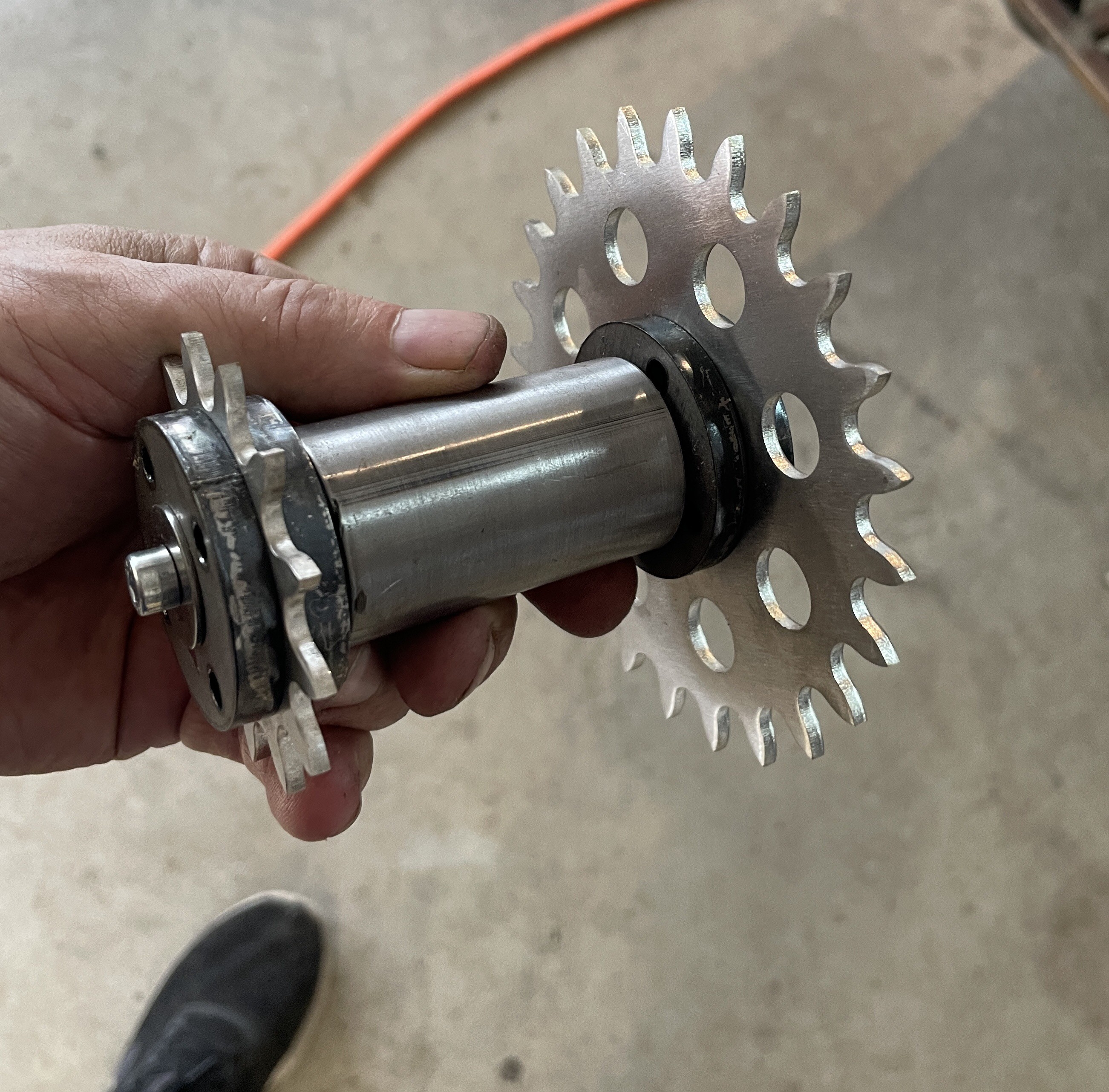
And this is what an assembled Jack shaft looks like. Note two different gear sizes, this gives a gain of two across the Jack shaft, allowing the front sprocket to be half its normal diameter and yet still get a useful gear range.
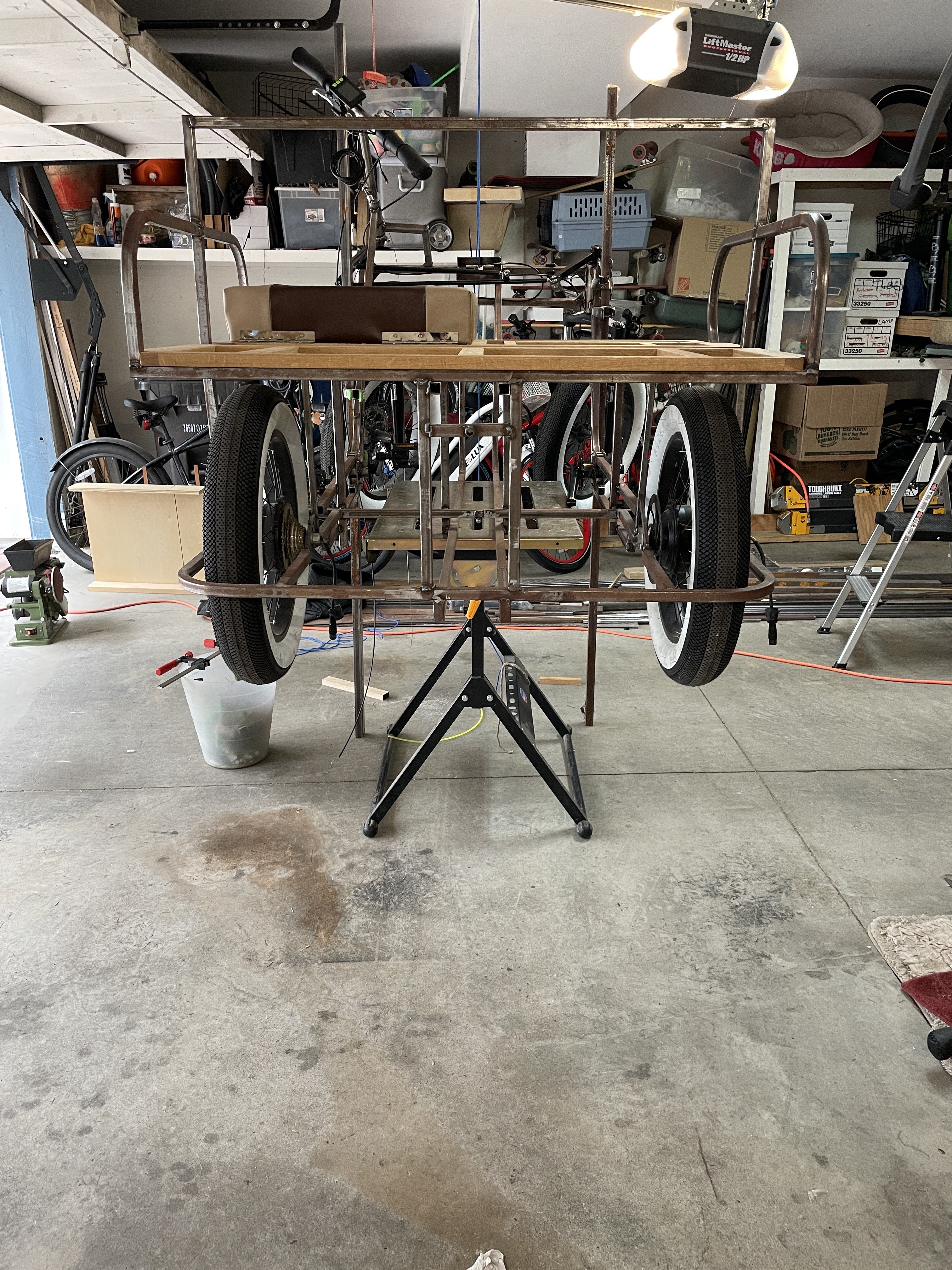
The whole bike was moved up on top of a welding table to make it easier to install components.
Making 1.25” diameter holes in sheet metal was beyond my drill press capabilities so a quick trip to Harbor Freight and I bought a chassis punch set. However, 1 1/4 conduit is a bit bigger than 1.25” OD tubing. So I hammered a bit of steel wire thinner to shim the tubing into the hole.
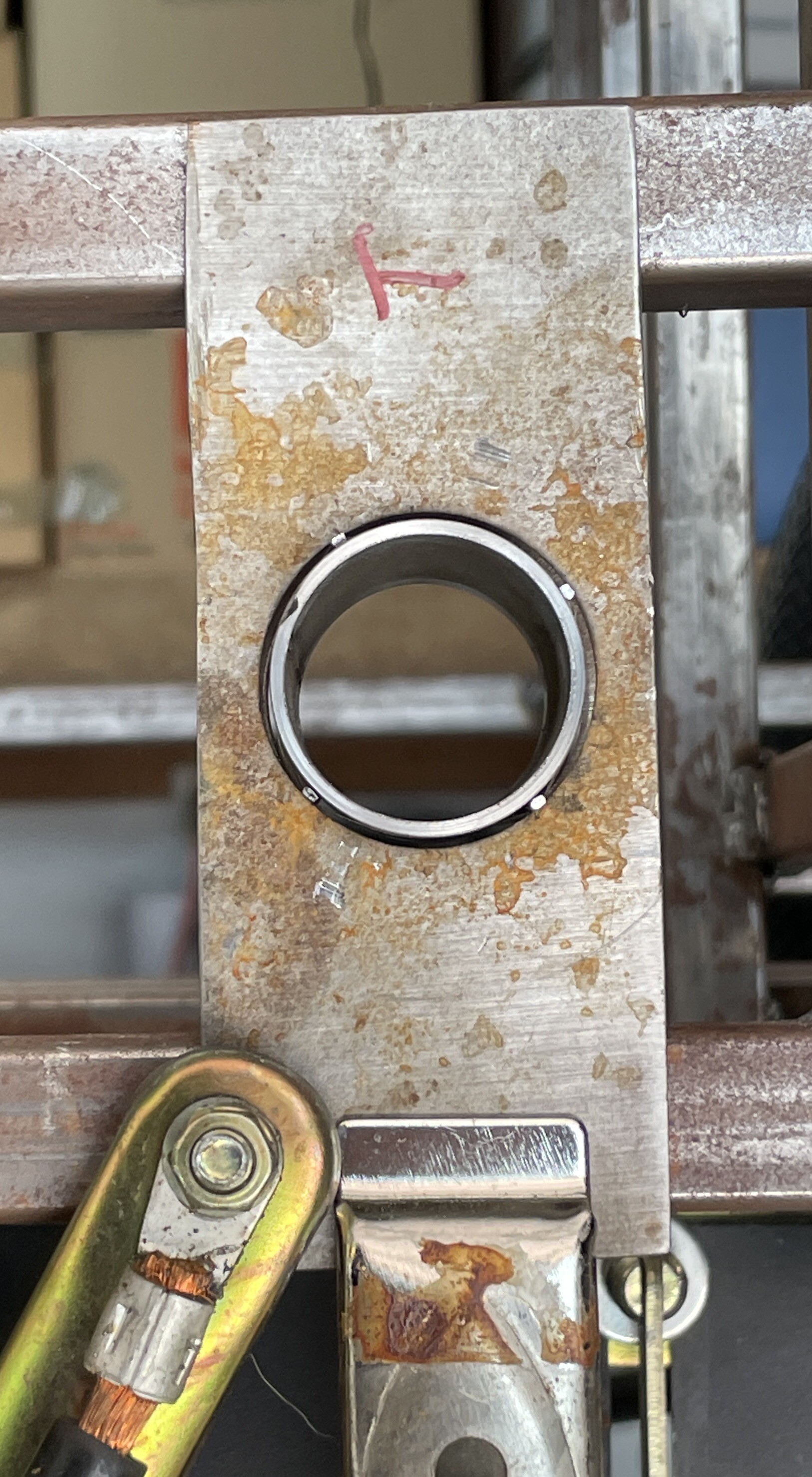
With bike elevated I tackled an easy task, installing the torque arm. Evidently I designed for socket head screws but bought button head. This two screws are missing. The torque arm contact the two flat sides of the axle, allowing torque from the motor to transfer to the frame without the axle spinning.
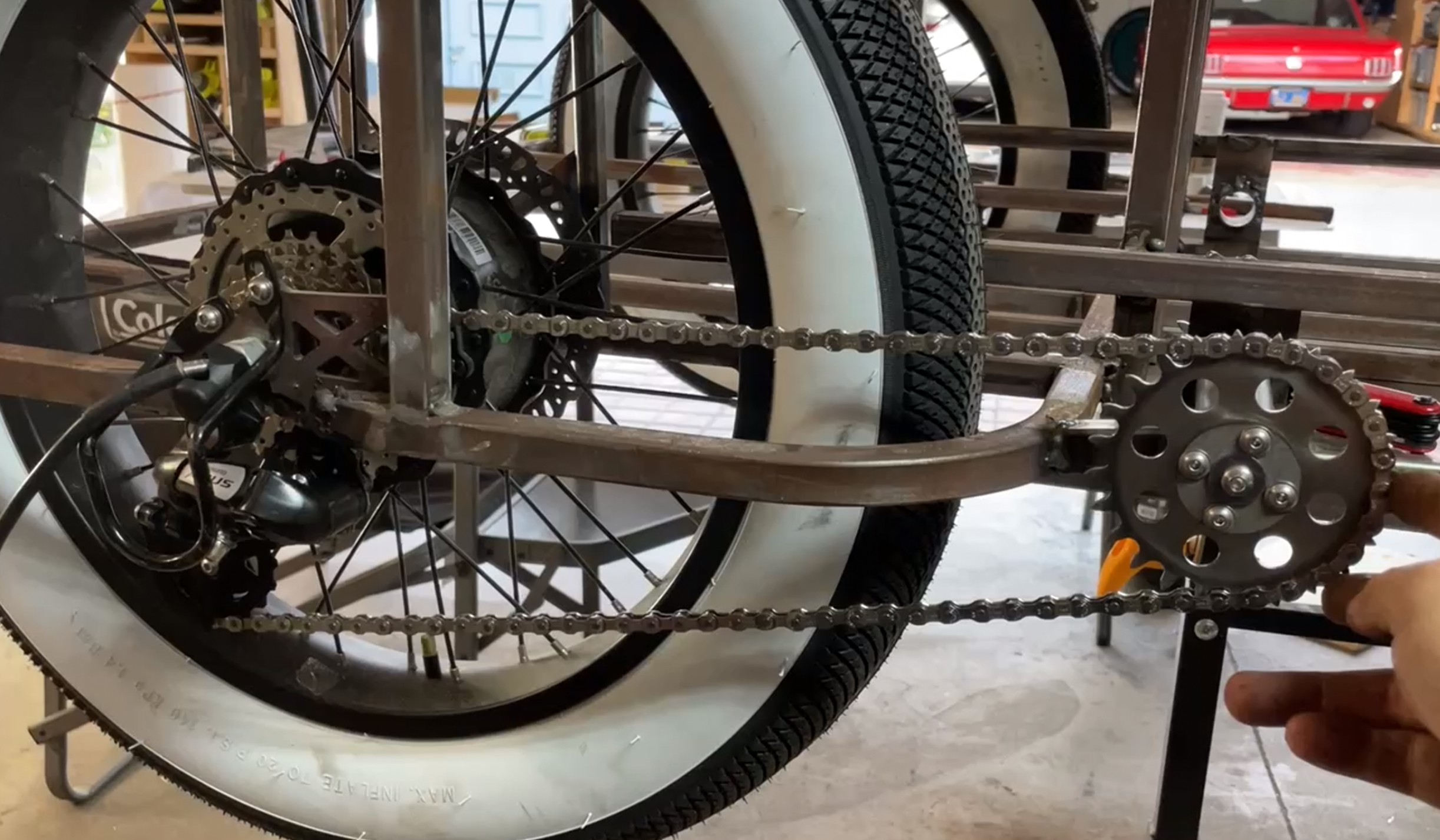
Discussions
Become a Hackaday.io Member
Create an account to leave a comment. Already have an account? Log In.