After finishing the GNS 430 installation, I moved on to the analog instruments of the dashboard.
A great source of inspiration, as well as Fusion 360 designs, is Captain Bob's YouTube channel, which features a variety of aviation-related projects. Inspired by his content, I decided to try his design for a Turn Coordinator. I used his design almost unchanged; however, I applied the same technique for the text and graphics on the instrument that I also used in the GNS 430 build: instead of using stickers, I embossed the text and lines directly onto the 3D-printed faceplate and then painted them white with a paint pen:
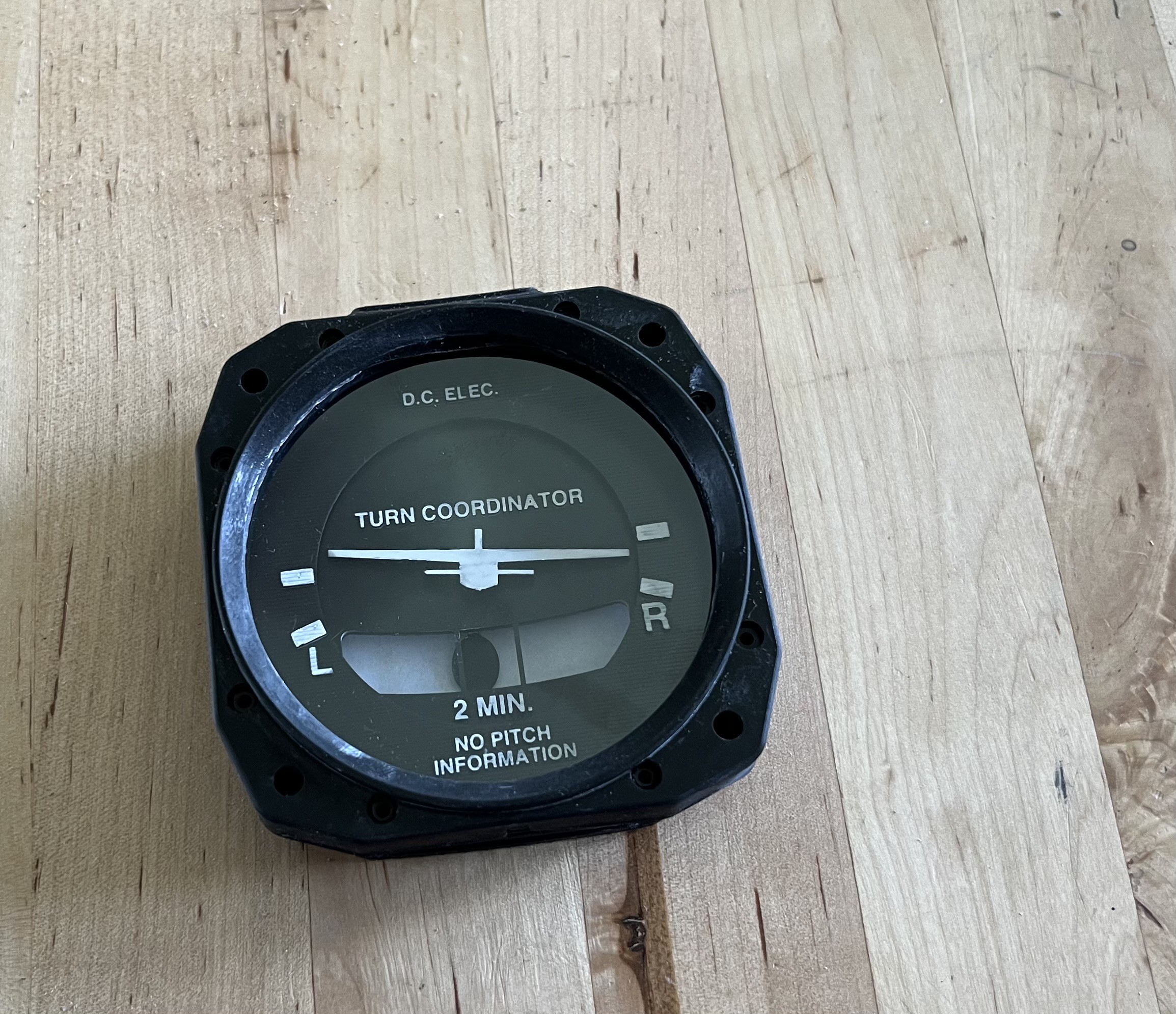
Although Captain Bob's design was intended for FDM printers, I had no trouble adapting it for my resin printer. Additionally, since I don't own a laser cutter, the clear screen is not a laser-cut piece of acrylic glass as originally designed, but rather a simple overhead transparency sheet cut with my trusty eight-year-old Silhouette Portrait cutter. It looks surprisingly convincing and also serves as dust protection for the instrument.
After a first dry fit, I decided to redesign the little airplane needle, as Captain Bob’s version is tailored for a Cessna 172, whereas I am building a dashboard for a Piper Arrow III. Using close-up screenshots from my flight simulator as a reference, I designed this alternative instrument needle in Fusion:
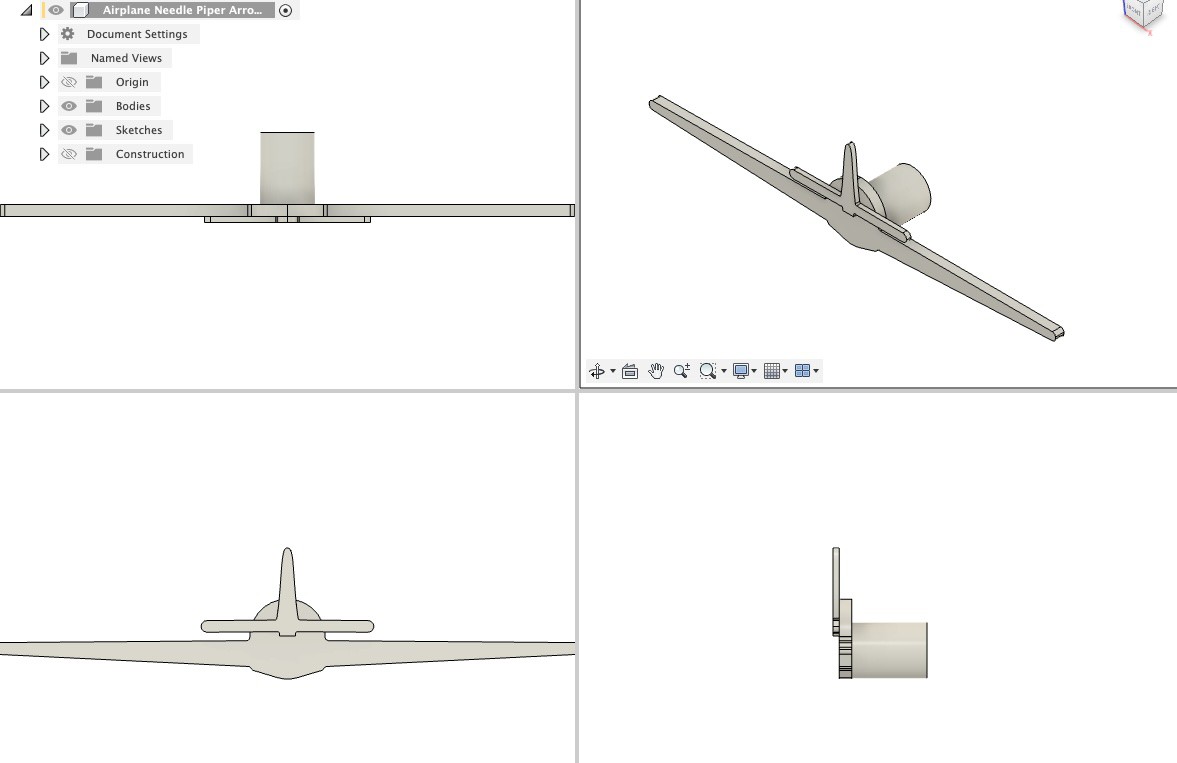
If someone is interested, here's the Fusion file: https://bitbucket.org/zaggo/pa-28-dashboard
And here's the final design:
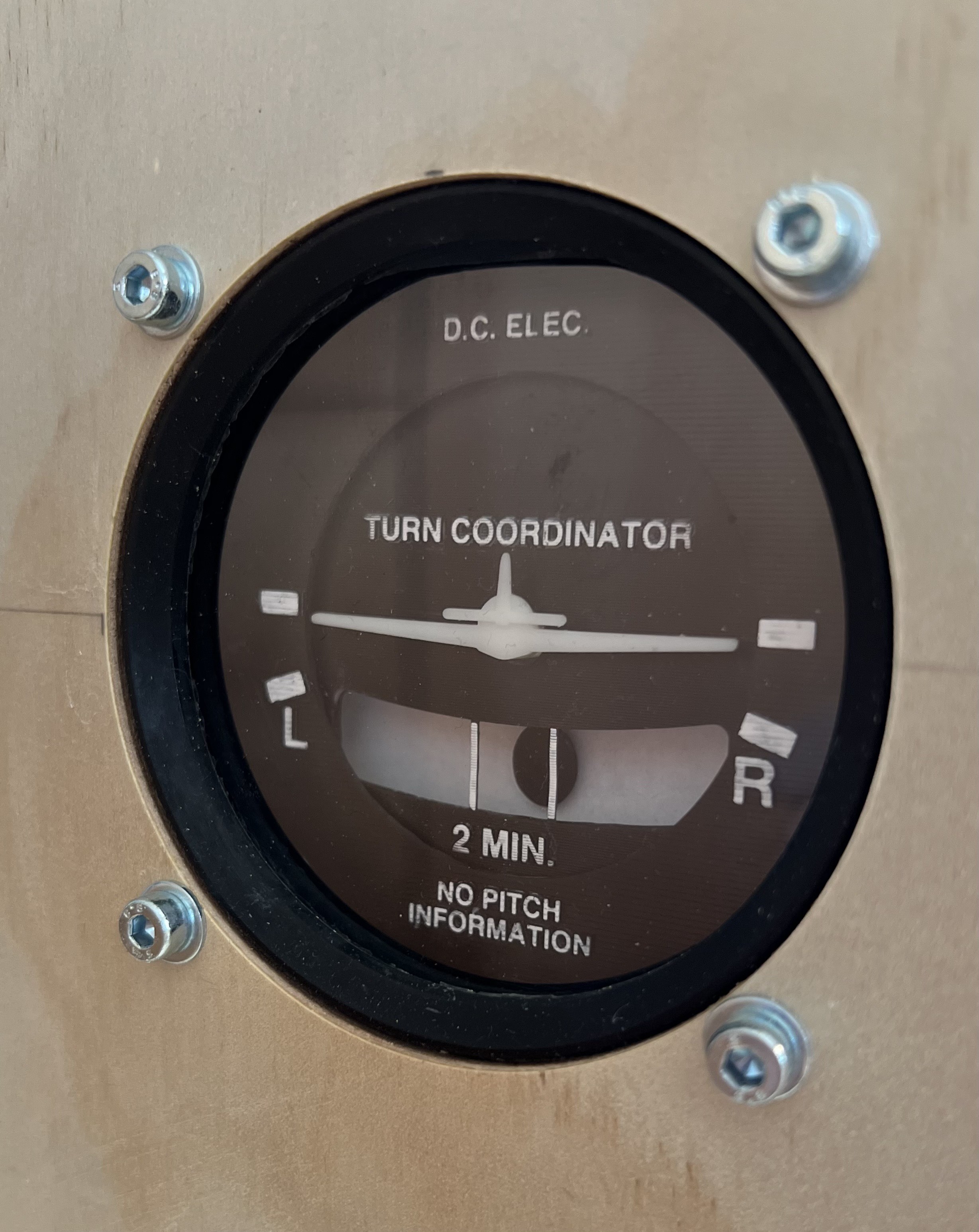
The instrument is powered by two X27-168 stepper motors, one driving the airplane needle (turn rate) and the other controlling the "ball" (slip rate). Unfortunately, I encountered issues when trying to drive these motors directly from AirManager, even though these motors are used in their example code for driving stepper motors. After discussing this in their forums, I received a suggestion to reduce the motor speed in the code, which kind of worked. However, the motion of the needles was still quite jerky and slow, which I found unsatisfactory. During this process, I also experimented with controlling the motors using an Arduino sketch and the SwitecX25 library. This approach worked immediately and was significantly smoother than the jerky AirManager driver.
Fortunately, AirManager also offers a library for Arduino, SiMessagePort, which facilitates communication between AirManager and any Arduino sketches. Therefore, I decided to integrate an additional dedicated "Stepper Driver" Arduino into my build.
Here's the current simple sketch for driving the X27 motors based on commands sent via the SiMessagePort by AirManager:
#include <SwitecX25.h>
#include <si_message_port.hpp>
// standard X25.168 range 315 degrees at 1/3 degree steps
#define STEPS (315*3)
SiMessagePort* messagePort;
// For motors connected to digital pins 4,5,6,7
SwitecX25 motor1(STEPS,4,5,6,7);
SwitecX25 motor2(STEPS,8,9,10,11);
static void new_message_callback(uint16_t message_id, struct SiMessagePortPayload* payload) {
if (payload == NULL) { return; }
if (payload->type != SI_MESSAGE_PORT_DATA_TYPE_FLOAT) { return; }
float relPos = payload->data_float[0];
messagePort->DebugMessage(SI_MESSAGE_PORT_LOG_LEVEL_INFO, (String)"Received position: "+relPos+" for motor: "+message_id);
switch(message_id) {
case 1:
motor1.setPosition(relPos * STEPS);
break;
case 2:
motor2.setPosition(relPos * STEPS);
break;
}
}
void setup(void)
{
// Init library on channel A and Arduino type MEGA 2560
messagePort = new SiMessagePort(SI_MESSAGE_PORT_DEVICE_ARDUINO_MEGA_2560, SI_MESSAGE_PORT_CHANNEL_P, new_message_callback);
// run the motor against the stops
motor1.zero();
motor2.zero();
// start moving towards the center of the range
motor1.setPosition(0);
motor2.setPosition(0);
messagePort->DebugMessage(SI_MESSAGE_PORT_LOG_LEVEL_INFO, (String)"Servos zeroed and driver ready");
}
void loop(void)
{
messagePort->Tick();
// the motor only moves when you call update
motor1.update();
motor2.update();
}
And here's the companion LUA script in AirManager:
function new_message(id, payload) -- Do something with the message from the Arduino end servo_driver = hw_message_port_add("ARDUINO_MEGA2560_P", new_message) function turnrate_callback(deg) -- value between 0.0 ... 1.0, 0.5 = 0° 0.2=-90° 0.78=+90° local clippedDeg = var_cap(var_round(deg,3), -110, 110) local v = 0.5 + (clippedDeg/90) * 0.29 -- print("Turnrate: "..deg.." clipped: "..clippedDeg.." v = "..v) hw_message_port_send(servo_driver, 1, "FLOAT", v) end xpl_dataref_subscribe("sim/cockpit2/gauges/indicators/turn_rate_roll_deg_pilot", "FLOAT", turnrate_callback) function sideslip_callback(deg) -- value between 0.0 ... 0.156 0° = 0.082 local zeroPos = 0.087 local clippedDeg = var_cap(var_round(deg,3), -90, 90) local v = zeroPos + (clippedDeg/90) * (0.156-zeroPos) local clippedV = var_cap(v, 0, 0.156) -- print("Sliprate: "..deg.." clipped: "..clippedDeg.." v = "..v.." clippedV = "..clippedV) hw_message_port_send(servo_driver, 2, "FLOAT", clippedV) end xpl_dataref_subscribe("sim/cockpit2/gauges/indicators/sideslip_degrees", "FLOAT", sideslip_callback)
With this setup, the Turn Coordinator works well, and the extra Arduino is not only driving these two X27 motors but also potentially other steppers and other unique devices in the future.
It would be ideal if AirManager could natively support these commonly used steppers more effectively. However, I must acknowledge that they offer a valuable workaround with their SiMessagePort library for Arduino, which opens up a lot of potential for future expansions.
Discussions
Become a Hackaday.io Member
Create an account to leave a comment. Already have an account? Log In.