POWER Pi Version 1
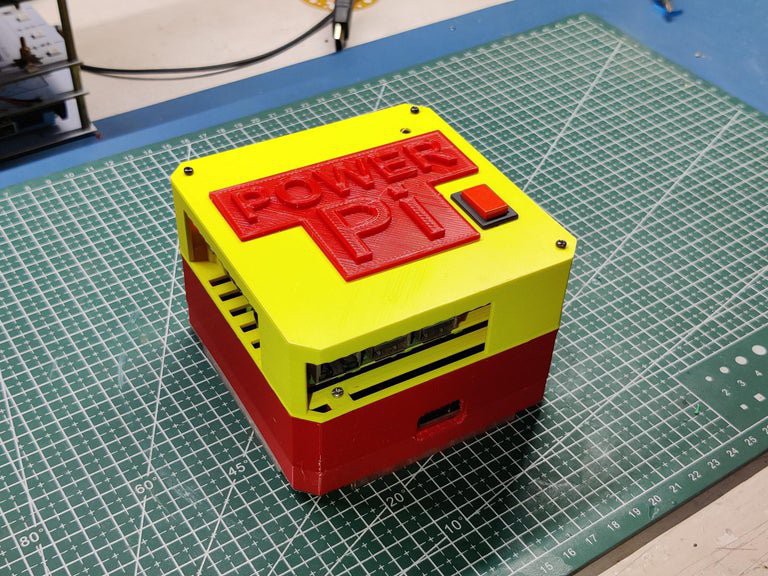
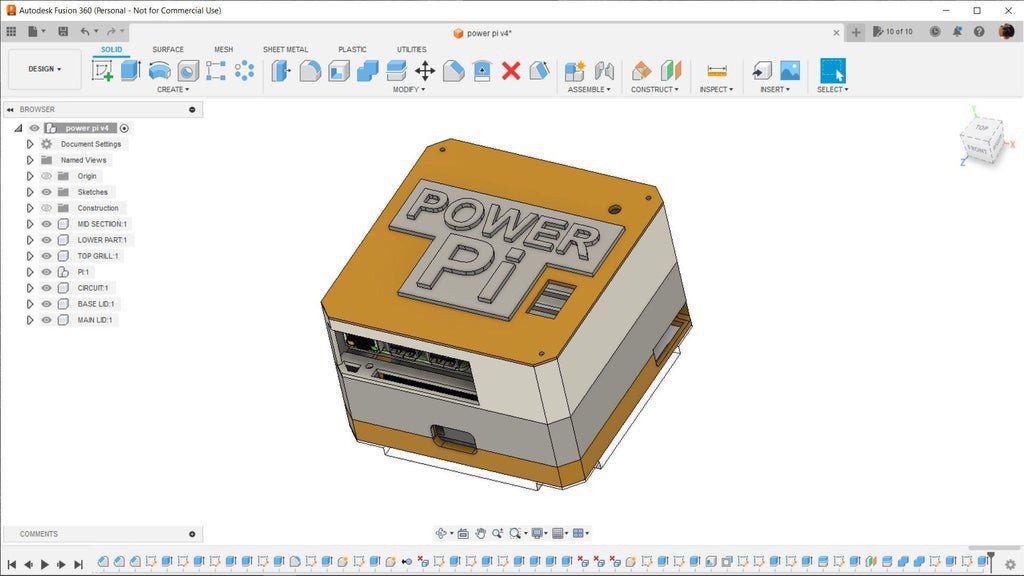
Let us explore the Power Pi that was previously constructed.
The primary component of the previous version was the power management board, which powered the Raspberry Pi board with four 3.7V 18650 cell holders.
In order to hold the power management board and Raspberry Pi together, we modeled a base and added a second Raspberry Pi holding part.
The configuration worked, but it had a few body-related problems that made it less durable overall. Next, there was a problem with the power management circuit, so we built our own battery pack using custom PCBs and installed two of them to power the Raspberry Pi in the updated version.
You can checkout the previous version at the below link:
https://www.hackster.io/Arnov_Sharma_makes/rgb-led-board-for-power-pi-2-4e7f7d
New Version: DESIGN
Given its five-section design, the Power Pi Version 2 is larger than its predecessor. The sections in question are as follows:.
TOP Section:
This is the top portion of the model, and it has two main components: the fan assembly part, which draws air into the Power Pi for air circulation, and the handle, which attaches to the outside of the top portion using two M3 bolts from each side.
To keep the Pi cool, a fan holder was added. This holds a standard small DC PC fan from the inside.
It is entirely redundant to add a fan, but if your workload involves more than just running retro emulators, do it in order to keep the Pi operating at its optimal temperature.
Pi Holder:
The pi holder is the section where we place the raspberry pi.
Because the Pi Holder is open on two sides, users may access all of the Raspberry Pi's I/O ports, including the power, HDMI, and USB ports on one side and all of the Ethernet and USB ports on the other.
In order to hold the Pi's position, we added four screw bosses that elevate the Raspberry Pi a few millimeters off the bottom face, creating a space between the Pi Holder's inside face and the Raspberry Pi's back.
Middle Section:
Between the Pi Holder section and the Battery Holder section, the middle section serves as a separating layer. This component essentially attaches the battery holder and Pi holder together.
Battery Holder Section:
One main function of the battery holder portion is to mount the battery pack PCB in the correct position.
We have modeled. a PCB with an SMD lithium cell holder; this is a PCB-based battery pack.
PCB standoffs are used to stack two PCBs on top of one another in order to increase the capacity of the battery pack.
We additionally mount both PCBs with the battery holder part using these standoffs.
We have slots on one side for adding switches and a DC jack for charging. The switches will be used to turn the Raspberry Pi and LED board on and off.
RGB LED Holder/Base:
This model's base part, the RGB LED holder or base, serves as the solid foundation for the entire structure.
Our design now has an RGB element and a gamer-like appearance thanks to the addition of an RGB circuit inside that lights up the entire base.
The RGB LED Holder/Base will be printed with transparent PLA to diffuse the RGB LEDs placed inside.
The following sets comprised the overall structure of the design.
We used three different PLA colors for each part: marble PLA for the Pi Holder and battery holder, orange PLA for the center area, and transparent PLA for the top section and base.
Furthermore, we have included a few nametags and logos with a cyberpunk theme.
By stopping the print in the middle and switching out the filament for a different color, we were able to print the nametags and logos utilizing double PLA color. We had to do this since we were using Ender 3, but if you are using a multicolor printer, you can bypass this setup completely.
Battery Board
The BMS and the DC Buck Module were the project's two primary components; therefore, we began the electronics design process by creating a schematic for the battery board. A battery management system, or BMS, is used to control or effectively charge and discharge lithium cells while they are in use.
We are utilizing a 15A BMS, which enables a 3-series cell setup, which requires connecting three lithium cells in series with the BMS. This device has a nominal voltage of 11.1V and a maximum voltage of 12.6V.
The battery pack only requires 13 volts to be charged because it has both low- and high-cut features. This is because the cells require a voltage greater than 12.6V to be fully charged; therefore, 13V is sufficient to prevent potential deference.
The battery management system (BMS) controls the cycle of cell charging. If a cell has an uneven voltage, for instance, one cell has 3.5V and the other two have 3.7V, the BMS will stabilize the voltage of each cell and bring them all to the same level, meaning that once the battery is changed, all of the cells will have 4.2V.
Our objective in the PCB design is to mount the BMS on the board, as it has some pads on the bottom and all the components are placed on the top, enabling us to solder it as a module on a circuit and then install the battery pack on a circuit using an SMD 18650 Cell Holder coupled with the BMS.
In order to create a 3S configuration, we added three 18650 cell holders to the schematic and linked them all in series. Next, we connected the GND of each cell to the GND port of the BMS; the 3.7V of the first cell goes to the 3.7V port, the 7.4V of the second cell to the 7.4V port, and the 11.1V of the cell to the BMS 11.1V port.
To obtain the cell output, we use the VCC and GND ports on the BMS. This part is controlled by BMS ICs and quite a few mosfets. When the cell voltage hits a minimal cutoff threshold, which is approximately 2.5V, the mosfets cut the power of the VCC, preventing any device from totally discharging the cells.
In addition to the 12V ports, we also added a few more parts, such as an SMD diode coupled with an LED and a resistor that is connected to a CON2 port, which is used to charge the battery pack. The diode is directly linked to the VCC port and drops the extra voltage that is coming from the CON2 port.
When power is applied to the CON2 port via an LED and resistor, the LED illuminates and functions as a charging indicator when the charger is plugged in.
A DC-DC Buck converter module has also been added. It accepts a 12V input and steps it down to a stable 5V/3A for powering the Raspberry Pi.
Following the completion of the project's schematic, we created the board file utilizing the PCB layout from the Cad design, placing the cell holders on the bottom and all SMD components on the top.
PCBWAY Service
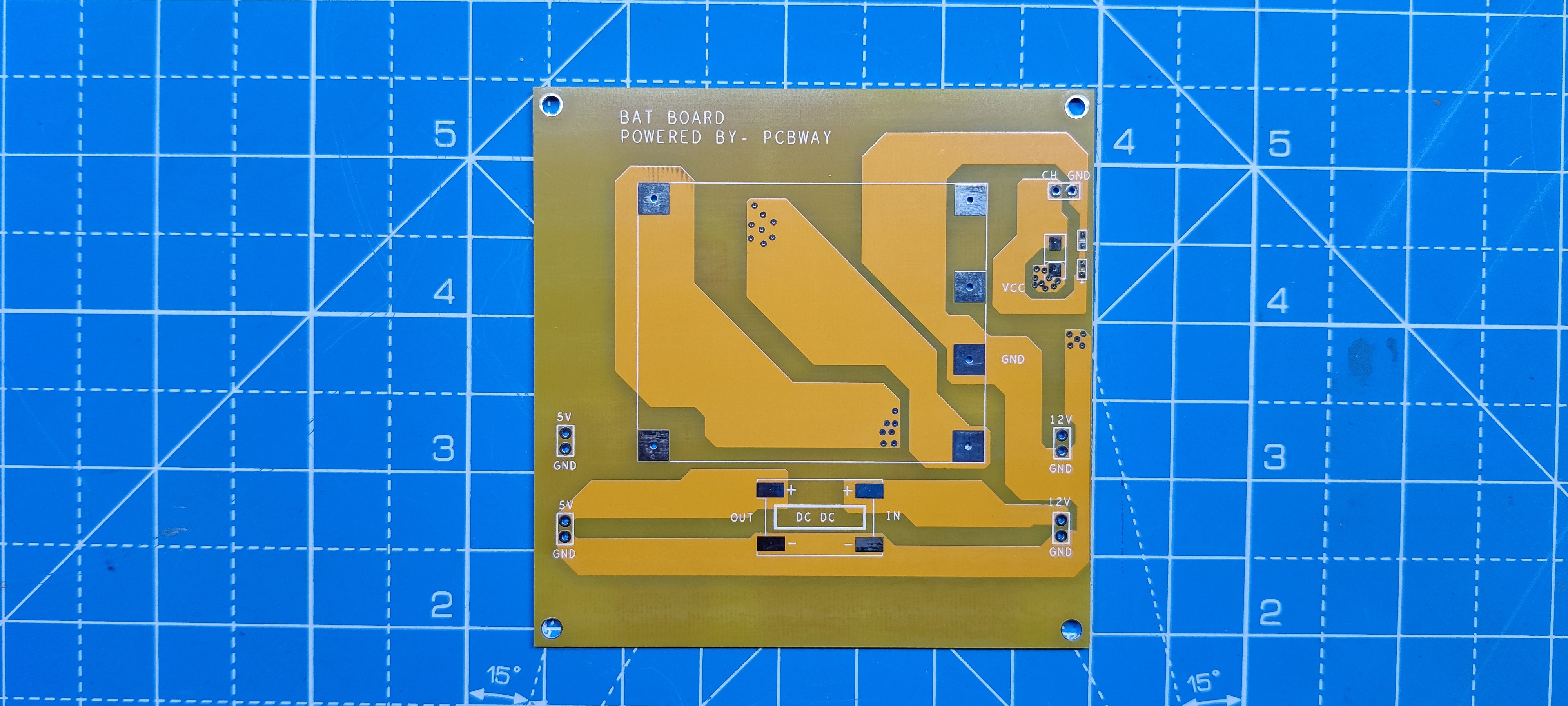
We placed an order for a yellow Solder mask with white silkscreen board.
After placing the order, the PCBs were received within a week, and the PCB quality was pretty great.
Over the past ten years, PCBWay has distinguished itself by providing outstanding PCB manufacturing and assembly services, becoming a trusted partner for countless engineers and designers worldwide.
Their commitment to quality and customer satisfaction has been unwavering, leading to significant growth and expansion.
You guys can check out PCBWAY If you want great PCB service at an affordable rate.