Assembly Pack and Go and Assembly Exploded View video
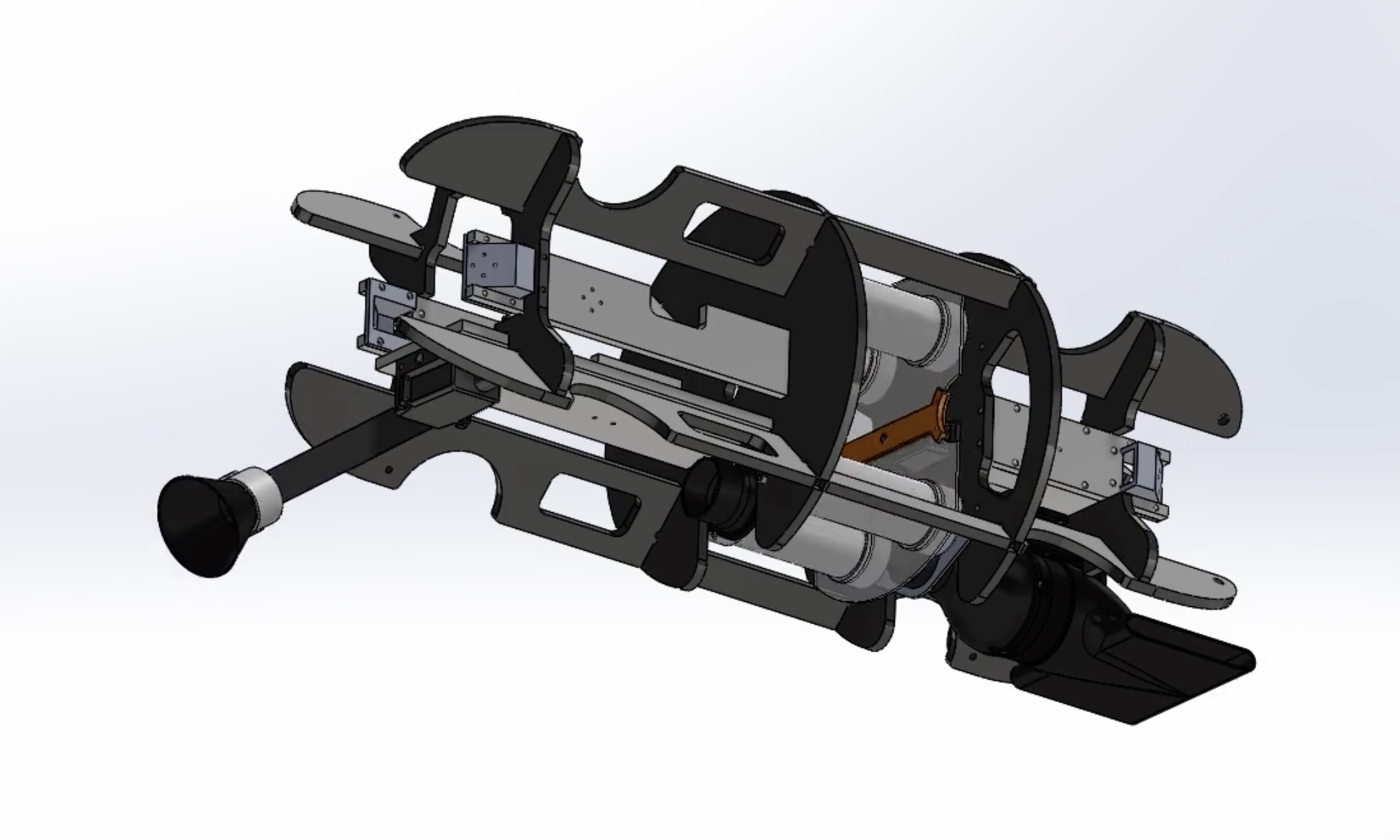
Need Statement
- Matt and his team need a way to collect antarctic under-ice flora and/or fauna using the modified BlueROV2 provided so that they can expand the current capabilities of the Subzero UROV.
Significance
- Our payload will be used to further the research of Matt’s team in the Antarctic. Ideally, our attachment will be used for a wide variety of sample types, however, it is specifically designed to collect brittle stars. One specific study these samples will contribute to involves DNA analysis of two different species of brittle stars found in the region.
- Our system is designed to utilize open source hardware and can be modified to suit other UROV designs for various sample collection purposes.
Stakeholders
- Queensland University of Technology
- Australian Antarctic Division (Australian Government)
- Matt Dunbabin- CI who has been asked to use UROV for sample collection, the stakeholder we have direct contact with
- Researchers aim to collect samples of flora and fauna along the antarctic seafloor using the UROV. For this task, an attachment to the UROV needs to be developed.
- Sea life- don't heavily disturb populations/environments
Project Background
- Professor Dunbabin was asked to modify a BlueROV2 for use in an Antarctic research expedition. His modified UROV, called Subzero, will be deployed through a 40cm hole in Antarctic ice, and upon reaching the floor, will collect flora and fauna samples. The intended samples are brittle stars & algae & seagrass. They will be used for DNA analysis to gain a better understanding of the life in the region.
Critical Requirements and Specifications
More details can be found in the requirements/specs Excel file.
REQUIREMENTS | SPECIFICATIONS |
Retrieve samples | - stores and collects multiple samples |
Reach sea floor | - operate at an expected depth of 100m below sea level, with a max depth of 150m. |
UROV operates without entangling flora and excessive disturbance of sea floor | - operate from 20-30cm above the sea floor |
It fits within a 40 cm hole | - fits within the diameter of Subzero UROV: 350mm - sample storage fits within the length of payload space: 200 mm |
Integrates with UROV system | - operates within the camera's line of sight - utilizes <4 communication ports ( 4 available) - easily removable/attachable under 30 mins |
Operates in Antarctic waters | - withstands water pressure at the sea floor - functions in freezing water and below-zero air temperature |
Design Process
We approached idea generation and brainstorming by considering the two main components we needed to address independently: the collection mechanism and the storage mechanism. A lot of our initial ideas for collection mechanism ended up combining with storage because they would only work for one sample. A core requirement is the ability to hold multiple samples, so these would not work. Below outlines the ideas we explored further and eventually settled on.
- Collection Mechanism:
- Grabber arm- complicated articulation mechanism to retrieve multiple samples
- Net- didn't fit in size constraints
- Suction
- Storage Mechanism:
- A lot of our initial ideas didn't work to store multiple samples, which was a main requirement.
- one big storage tub- weakened suction, no separation of samples
- net- didn't fit in size constraints
- rotating dividers within a big canister-> rotating smaller canisters
- A lot of our initial ideas didn't work to store multiple samples, which was a main requirement.
How de we create suction power?
- Use thrusters already on UROV?
- Use freestanding thruster?
- easier to design parts around, affects motion of UROV less.
Other questions we had to consider once settling on rotating canisters and suction:
- Will we have enough suction power with the gaps necessary in the system to allow rotational clearance?
- How will we attach suction tube to the UROV and articulate it?
- What are the buoyancy and weight requirements for the UROV?
- What size will our sample canisters need to be and how many can we have?
- How do we make the canisters and the whole system removable easily without disassembling the frame of the UROV.
More details can be found in design sprint review pdfs.
Design Description
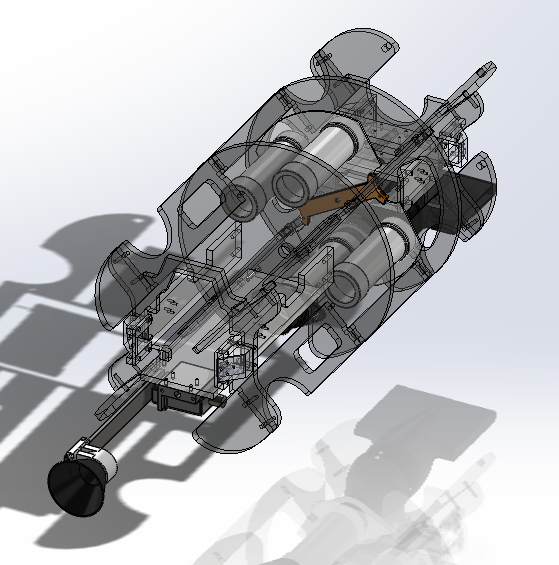
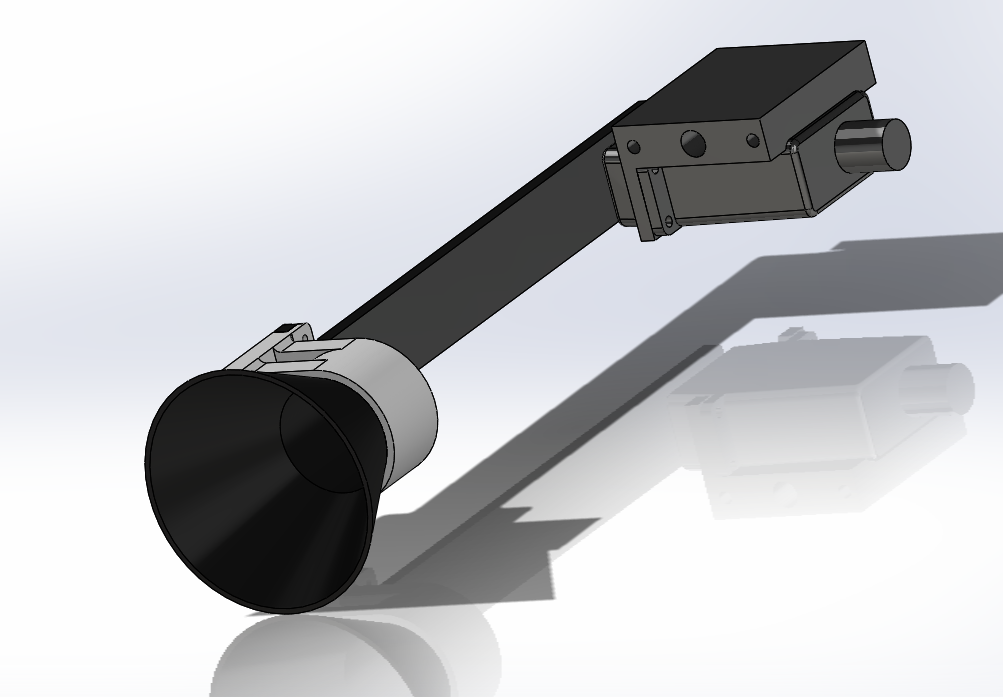
Tube and Inlet: To improve the flexibility and longevity of our water input system, we're using industrial-grade swimming pool tubing, which is known for its strength and capacity to handle a variety of environmental stressors, making it suitable for extended usage. In addition, we are adding a 3D-printed component to the top of the tube to widen the range of suction, allowing for more efficient water intake. The swimming pool tube provides a flexible foundation that can be adjusted to different positions and angles without losing integrity, which is essential for negotiating obstacles and reaching varied water depths. In addition to that, with the attachment to the arm and the servo, we can do the arm articulation test and show that the arm is moving at different angles.
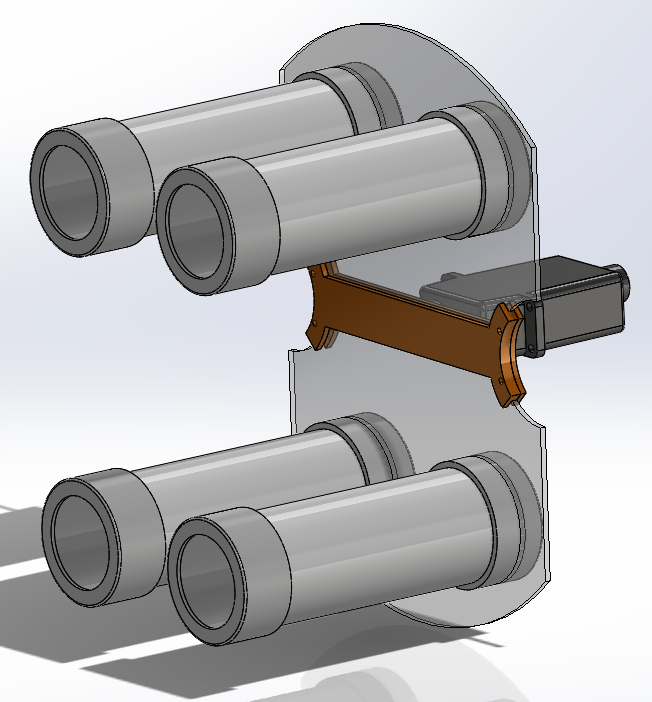
Canister: The spinning canister has a modular baseplate that can contain four pipes, allowing for continuous sample collection by simply rotating to an empty pipe when one is filled, resulting in maximum efficiency. The servo connection features an inventive double-sided clamp mechanism that simplifies assembly and disassembly. This user-friendly design requires only one screw to secure the servo, greatly simplifying maintenance and operation. The inclusion of a movable baseplate and an easily attachable servo improves overall functionality, making sample collecting more efficient and convenient for the user.
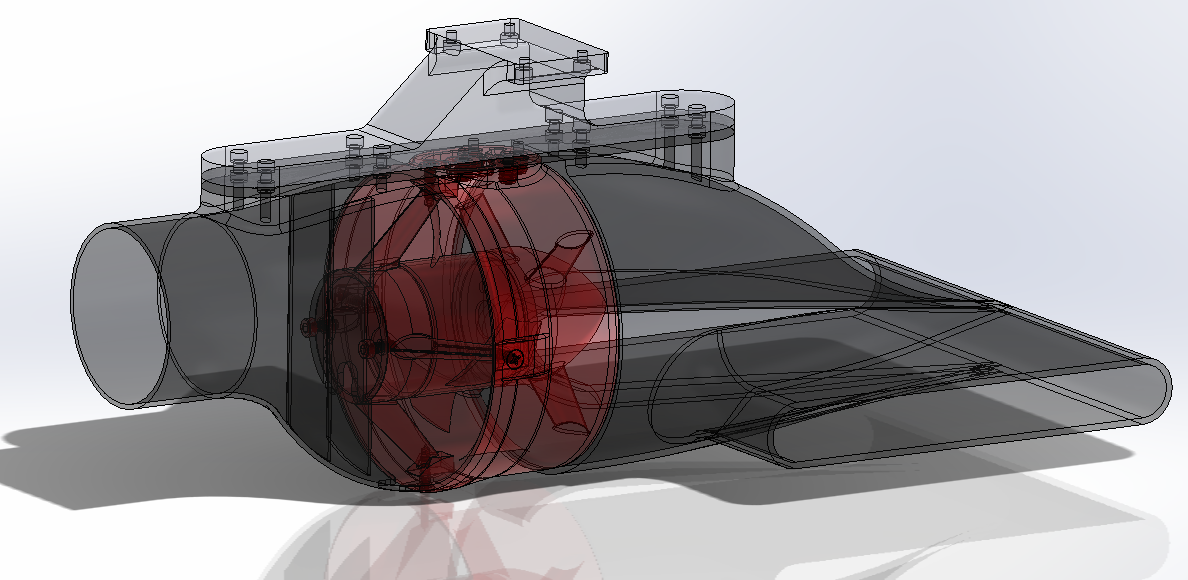
Thruster and Outlet: At the end of the system, a metal mesh is incorporated into the canister to filter out undesirable debris, ensuring that only the needed samples are gathered while reducing the inclusion of extra rocks and sand. The thruster's design incorporates physics principles, allowing water to flow symmetrically to both sides during suction. This balanced flow eliminates disruptions to the robot's movement, ensuring stability and efficiency in functioning. The combined effort of the metal mesh and the cleverly constructed thruster ensures precise sample collecting while allowing the robot to traverse.
Testing
- Because of the 5-week time constraint, we broke down our payload into 3 subsystems for testing purposes.
- Suction tube
- The suction mechanism was tested with seals added between all components and one stationary canister replacing the rotating system.
- Samples -- small plants and bits of plastic -- were successfully collected and stored .
- Thrust power was much stronger when the direction was reversed, which indicates the rotor blades were optimized for the wrong direction and that there were leaks in the system.
- Rotating Canisters
- Assembled the system / mounted it to the UROV and then tested rotation by hand (as opposed to turning on the servo).
- Function successful for the scope of the test, however friction fit of canisters, and canister stability was weak and caused slight misalignment.
- Arm Articulation
- Arm and suction tube successfully switch between default and deployed positions.
- Default position fit within the 40cm diameter of the UROV.
- Length in deployed position allowed for operation 20-30cm above sea floor.
- The tube did not bunch or experience unnecessary strain.
- When in the deployed position, the tube slid into the attached storage canister, making for a more secure connection than expected.
Conclusion
Our prototype served as a successful proof-of-concept for a suction based approach to sample collection for the Subzero UROV. Testing revealed multiple areas that could use revision.
Suction Tube:
- The main takeaway was that unanticipated gaps between components decreased suction power much more than expected
- Gaps were observed in:
- End of the suction tube
- Connection between motor and turbine inlet nozzle
- Gaps were observed in:
- Motor suction power issue should be fixable by flipping the motor around and reinstalling -- it was simply installed the wrong way.
- Reversing the suction to thrust highlighted leaks and screw holes that were left empty, which weakened suction.
Rotating Canisters:
- Behaved as expected.
- Installing the system into the UROV was much more time-consuming than anticipated.
- The tolerances on the rotating plate were too inaccurate and caused instability.
- The servo mount was effective and intuitive.
Arm Articulation:
- Behaved better than expected.
- Acrylic used for the arm-to-tube attachment was too flexible, causing concerns about durability.
- Snug fit caused by tube movement was promising.
Recommendations
- Add rubber for more secure fit and seal between storage canisters and connecting tubes
- Add friction between rotating plate and canisters for better fit
- Add a second rotating plate and extend servo connection point to the other end of payload space to keep canisters in line.
- If a hole is drilled in a part and nothing is screwed into it, seal it before use
- Make arm-to-hose attachment out of stronger material (aluminum?).
- Improve accuracy of all tolerances.