Professor Matt Dunbabin, Professor at QUT and Chief Investigator at the Australian Centre for Robotic Vision (ACRV), has asked us to help co-design an element in his robot the Blue ROV2 to collect data while researching in Antarctica. The RSV Nuyina is a research vessel that will traverse “uncharted areas of the deep ocean and study the upper reaches of the atmosphere,” (Minister Ley). The Hull will travel to collect unique data about the underwater species and subsystems of the Southern Ocean and its ecosystems. While in Antarctica, Matt plans on surveying and collecting possible biosecurity risk specimens off the sides of the Hull. We want to find a way for the RSV Nuyina Hull to be inspected through collection of biosecurity risk via the Blue ROV2.
The co-designed attachment will need to be attached to the BlueROV2 payload since the robot will need to be used for many facets. Similarly, we need a way to collect bio foul from the hull, sea chest, and any site of interest such as the moon pools onboard. We also need to be within the frame of the pan tilt camera.
In Preliminary brainstorming we decided on three main elements to our collection device. The first consisted of utilizing a suction vacuum system; BlueRobotics T200 Thruster will be the compatible and optimal component to incorporate into the tail end of the arm. The second system consists of motorized bristles spinning with planetary gears powered by BlueRobotics M200 motor. This planetary gear system subsequently connects through bearings in six individual sites to brush heads. And the last element mitigates debris spread, this element is a conical open netting concept that is boned with flexible TPU printed plastic and will fasten to the head of the motor.
In testing prototype A, we concluded from our design consisting of the mesh net and suction thruster that it was capable of creating enough suction to collect sediments of both fine and larger debris. In addition to this prototype, our makeshift filter on the tail end of the tube worked to prevent damaging and jamming of debris into the thruster and could catch the samples. In prototype B testing, we found the M200 powered brush schematics and attachment needed an additional agent to prevent gears from flying out. Similarly, we decided on a material type for the bristle brush heads - nylon with a medium stiff bristle type. Lastly in our final prototype testing, we were successfully able to incorporate the coalition of elements to function as a whole system. Despite setbacks, the bristles and planetary system worked with the aid. Additionally, both suction and motorized gear spinning worked simultaneously and collectively up took sediments and debris.
Recommendations and Conclusions
Gear Hold
Based on our testing, we discovered that the connector that we used for our bristle head and the gear that was slotted in the bearing need to be stronger so that it does not snap very easily. We would like to test a couple of approaches in the future. One is to make the shaft bigger so that it is more resistant to shear stress. The other way is to make the gear and the connector one solid body by 3D printing it instead of laser cutting each piece and super gluing them together. The updated file is in the folder section but is not part of the assembly yet.
Seal System
Since our current prototype has the specimen chamber open to the ocean bio foul would flow out the chamber while traversing the hull. Using a double door check valve that operates on two flap springs that are opened using the suction generated from the thruster prevents the bio foul from polluting the ocean while also utilizing the existing thruster to generate the opening and closing mechanism.
Debris Mitigation Skeleton
For further iteration and recommendation on the construction skeleton of the mesh net, the structural shape should change to reflect shapes that can compress. The posts should be thinner than the current 5 mm used in our final prototype, and would better bend with slots in the center of the posts, utilizing a honeycomb linear pattern, or using a crisscross scissor leg-like post. In our prototype we used a TPU flexible plastic, however, it was still stiff during testing. The mesh worked well as it was doubled to prevent debris, however using a stronger mesh would come with drawbacks because of the stiffness.
Internal Hinge and specimen chamber
Since prevention of bio foul escaping into the ocean is a high priority it’s important that the specimen chamber remains leak proof. To make collection out of the collection chamber feasible an internal or external hinge that is rubber sealed could be installed onto the chamber. To further simplify collection netting could be installed throughout the specimen chamber that can then be collected from the hinge door.
Materials
Since the Nuyina will be traversing in frigid waters, we wanted to take this into account when researching what bristles, plastics, and possible final materials used to prevent freezing and brittle cracking. Due to the epoxy resin seal on the exterior on the Nuyina, we found either polystyrene or Nylon in a medium soft to medium stiff strength would work best to clean all extraction sites. Additionally, metals that are rust resistant and won't corrode and brittle in the piercingly cold waters.
Overall, in this co design process we discovered and tested valuable elements to provide a starting point.
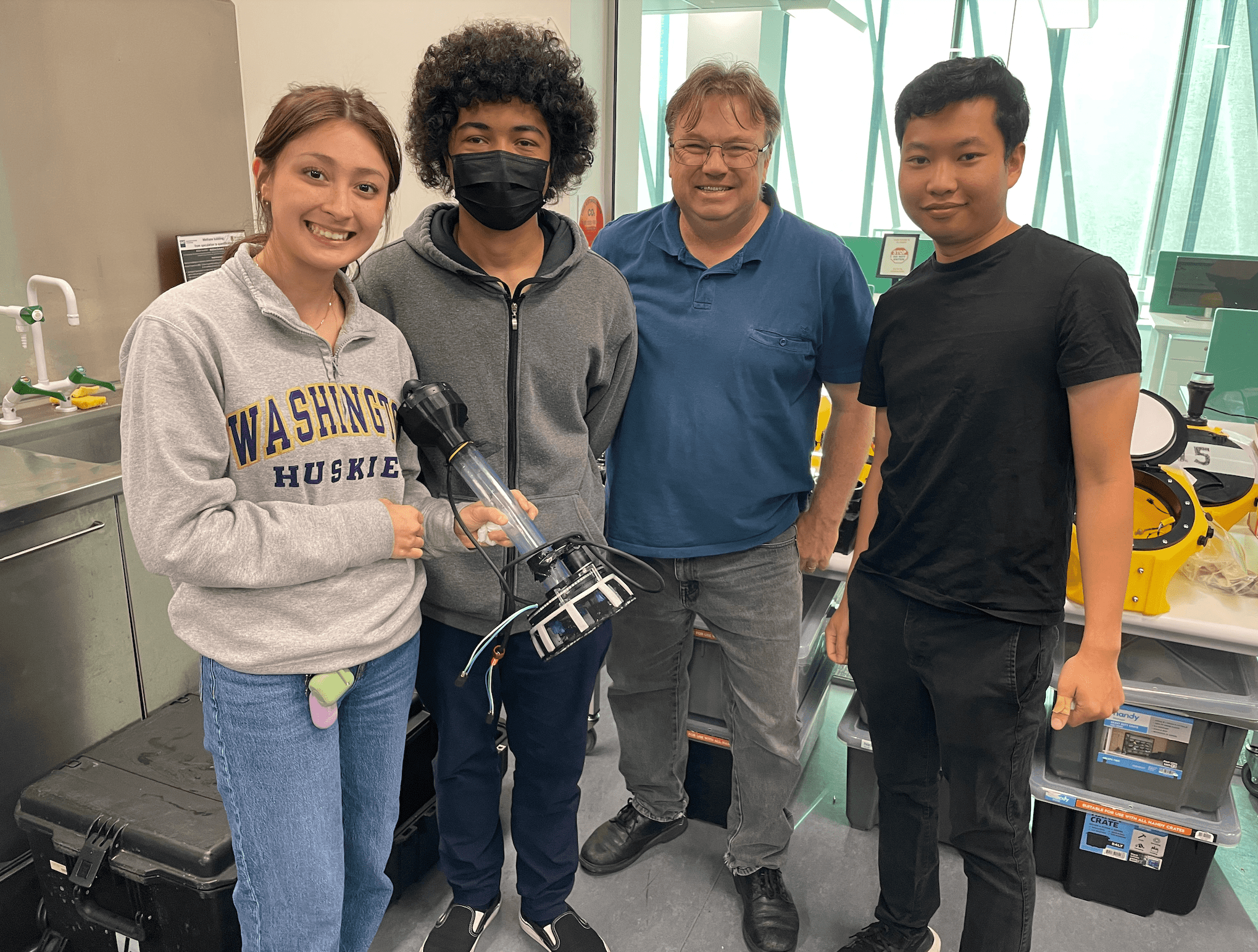