Design-Concept
First, we use our Fusion360 engineering software to create a model of our keyboard. We do this by meticulously measuring the keyboard's size, placement of the keys, and other details.
Keyboard modeling was essential since it helped us create the frame that surrounds the keyboard.
Three keyboard holder components have been added to the rear of the keyboard; they are used to secure the keyboard membrane in place. The holders are tightened onto the screw bosses that are already present on the keyboard.
The frame section and the holder section made up the majority of the main model.
The frame is further separated into the left and right frame sections.
Two logo components and four M2 screws are used to join the frame together.
One of the two holders is used to secure the Pi in place, and the other holds the volume control circuit.
In addition, we incorporated a model of an accent section that was borrowed straight from the Dragon Ball series' Capsule Corp logo to give this keyboard model a faintly sci-fi feel. After the model was finished, it was exported into mesh files for 3D printing, using a single 0.6mm nozzle, 20% infill, and 0.2mm layer height.
We utilize clear PLA for the frame, orange PLA for the keyboard holder, and grey PLA for the pi holder.
XIAO HID Volume Knob
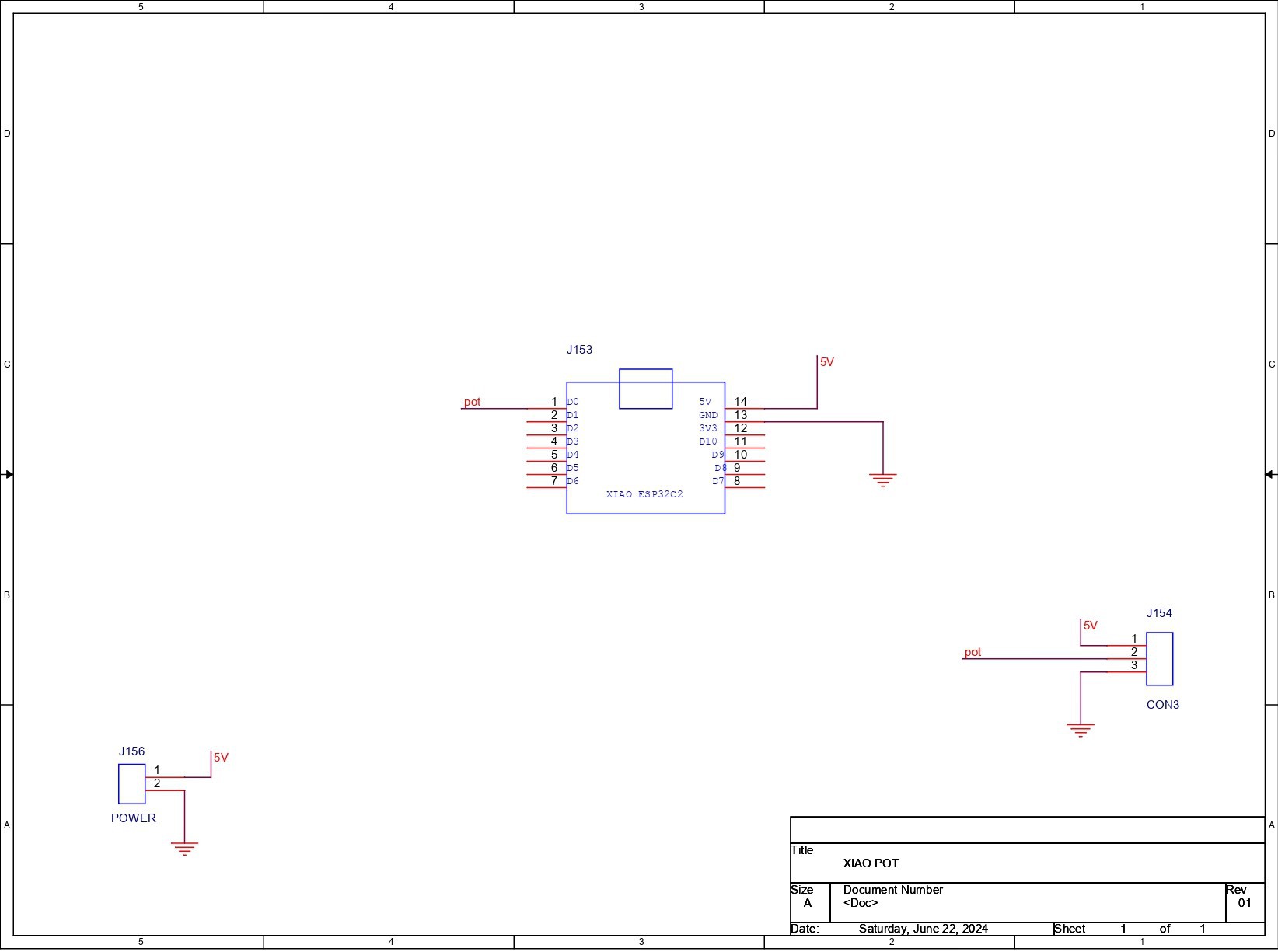
First, we created the schematic, which included a potentiometer and an XIAO SAMD21 microcontroller attached. Here, we are using a CON3 JST connector that is linked to GND, D0, and VCC. We will be using this connector to add a potentiometer to our XIAO.
Additionally, CON2, which is connected to XIAO's VCC and GND, is added.
There is no need for batteries or a power circuit because we will be directly connecting the XIAO and Raspberry Pi through the USB port to provide power.
We utilize the CAD file's measurements for the layout, which include the location of the XIAO and the mounting holes.
In addition, we added some attractive graphics to the PCB's top and bottom sides.
Seeed Studio Fusion
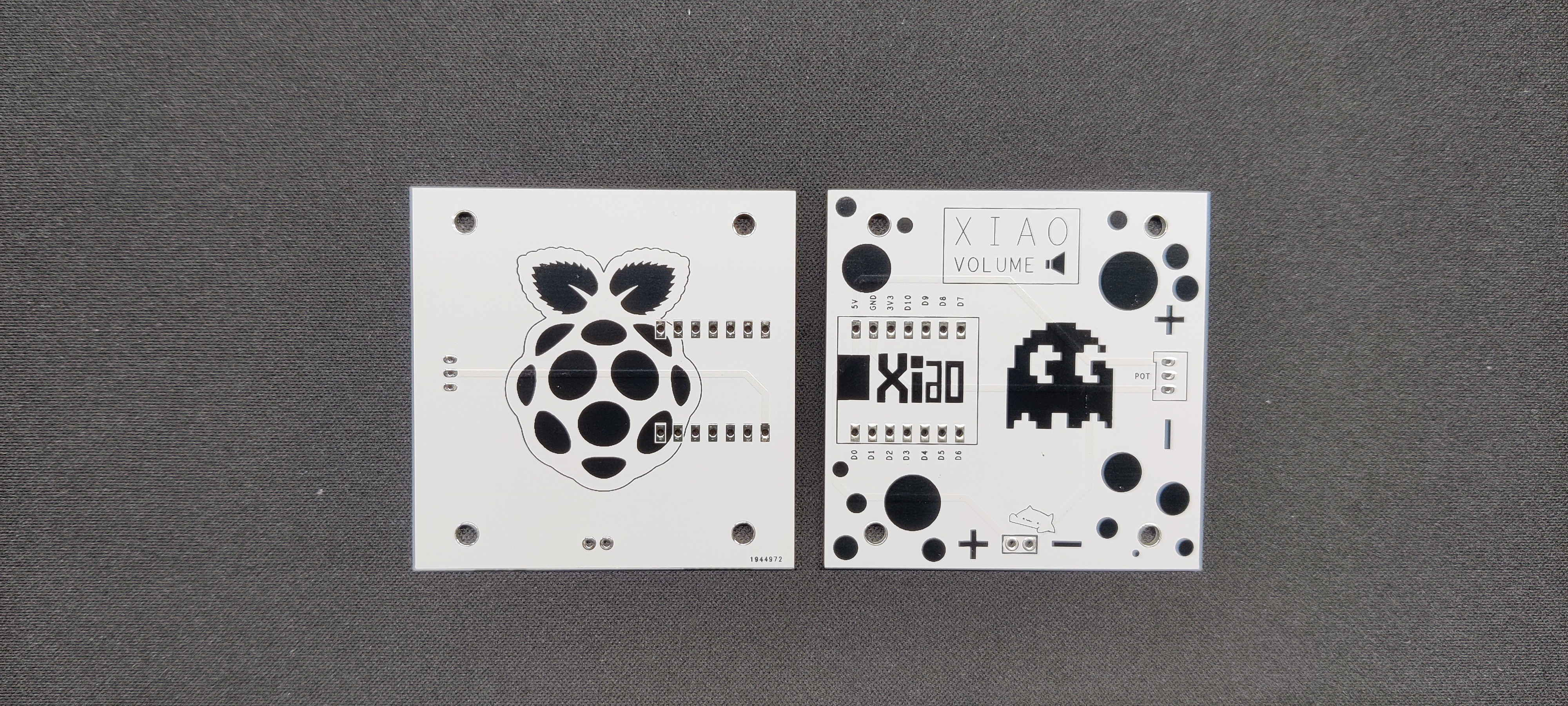
This project was made possible because of support from Seeed Studio Fusion.
We finished the PCB design, produced the Gerber data, uploaded the file to their quote page, and placed an order for the PCB with black silkscreen and white solder mask.
PCBs were received within a week, and the quality was super good considering the price, which was also pretty low.
Seeed Fusion offers one-stop prototyping for PCB manufacture and PCB assembly, and as a result, they produce superior-quality PCBs and fast-turnkey PCBA within 7 working days.
Seeed Studio Fusion PCB Assembly Service takes care of the entire fabrication process, from PCB manufacturing to parts sourcing, assembly, and testing services, so you can be sure that they are getting a quality product.
After gauging market interest and verifying a working prototype, Seeed Propagate Service can help you bring the product to market with professional guidance and a strong network of connections.