Summary of the EverySwerve Project
The EverySwerve project is being designed as a 1:1 replacement drivetrain for the FRC Kit of Parts. The goal is to design a high performing, swerve drive chassis with high maneuverability, easy assembly and lower cost. EverySwerve is comprised of four identical wheel module subassemblies held together by a frame of aluminum 1”x2” extrusions. Each wheel module has a hub motor for propulsion which simplifies power transfer through the steering joint(See Figures 1 & 2). A central hollow steering axis allows for a slip ring or wire bundle to pass through, eliminating the need for coaxial shafts and torque drive components used in popular COTS swerve modules.
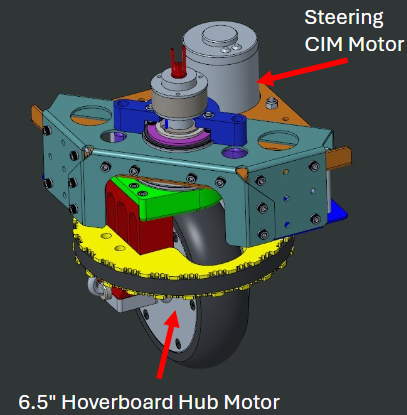
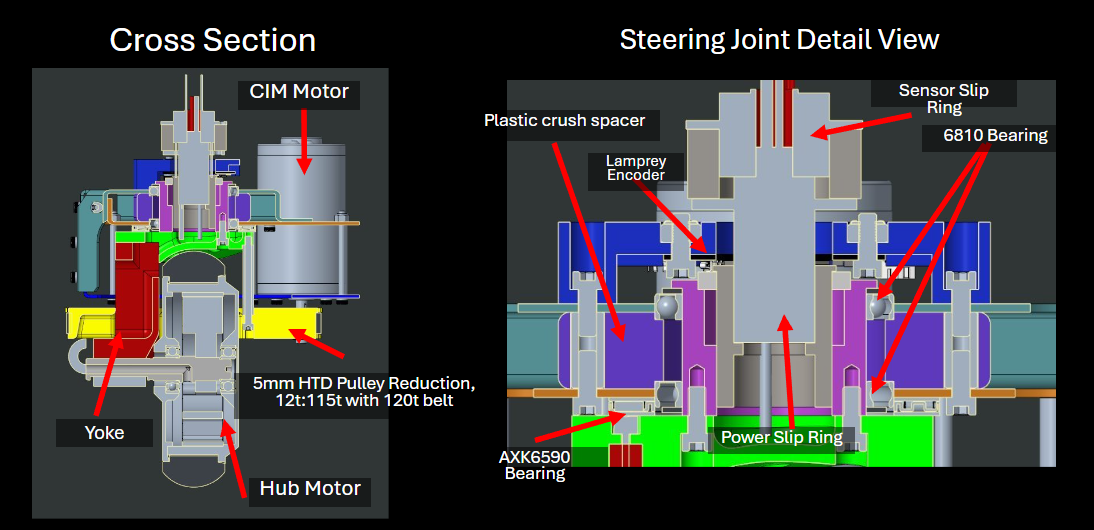
Progress
In order to design an FRC-rules-compliant and efficient swerve drive module, Team EverySwerve conducted numerous types of analysis; including loaded stress analysis, bolt, bearing analysis, thermal analysis, and motor and timing belt analysis. This guided much of our material and architectural designs in creating our final blueprint. Some key aspects to highlight are:
- Our use of cold-formed aluminum parts which have high yield stress and bending resistance, while maintaining ease of machinability
- Use of CNC manufactured components to prototype die-castings
- Determination of bolt preload values
Conclusion
From November 9th-23rd, Team EverySwerve has completed all the preliminary analysis for the EverySwerve module. FEA stress analysis on billet and Sheetmetal components has been completed and modifications to hotspots have been taken care of. Torque preloads have been determined for the bolted joints and simple thermal calculations proved that there is minimal concern with the heat generated by the motor within our design case(See Figure 3).
Prior to the start of the 2025 spring semester Team EverySwerve will begin procuring COTS components, manufacturing the custom components and generating the assembly instructions of the EverySwerve device. Beginning these tasks will permit us more time for building and validating the device later in the semester. Additionally, it will allow time for unforeseen issues with the assembly and performance of the device to be resolved.
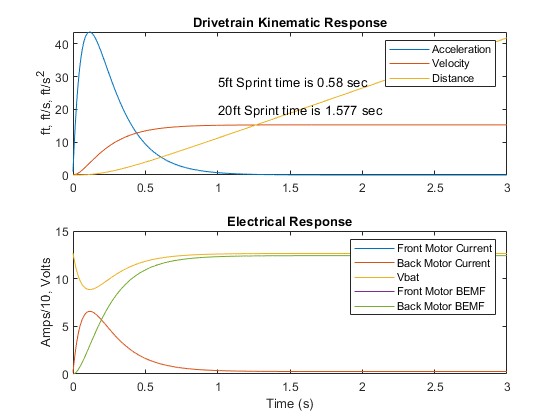
Discussions
Become a Hackaday.io Member
Create an account to leave a comment. Already have an account? Log In.