Success in metal casting is achieved through ever-tighter process control. This week I spent many hours on chasing the wax models to remove any small concave geometry left from removal of sprues & scaffolding required to cast in silicone. When wax is steamed out in the pressure canner, any small concave negatives become small investment positives. Even though UltraVest is high quality, a few bits of the material hanging on a thin neck will always break off due to gravity, shaking, or by force of metal entering the mold.
To take care of bubbles getting stuck in concave corners (the ones I have to leave in because they are part of the design) VacuFilm can be mixed with Methyl Alcohol and brushed on, almost like mold release when silicon casting:
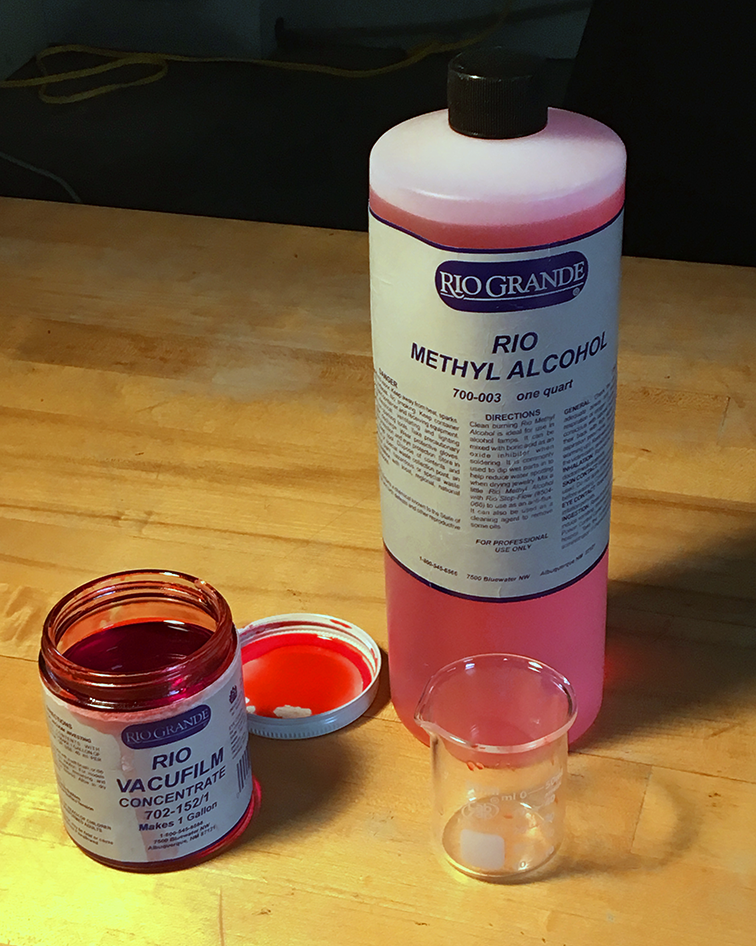
Here's also a botched test cast from this week - still encouraging because almost the entire model came out this time.
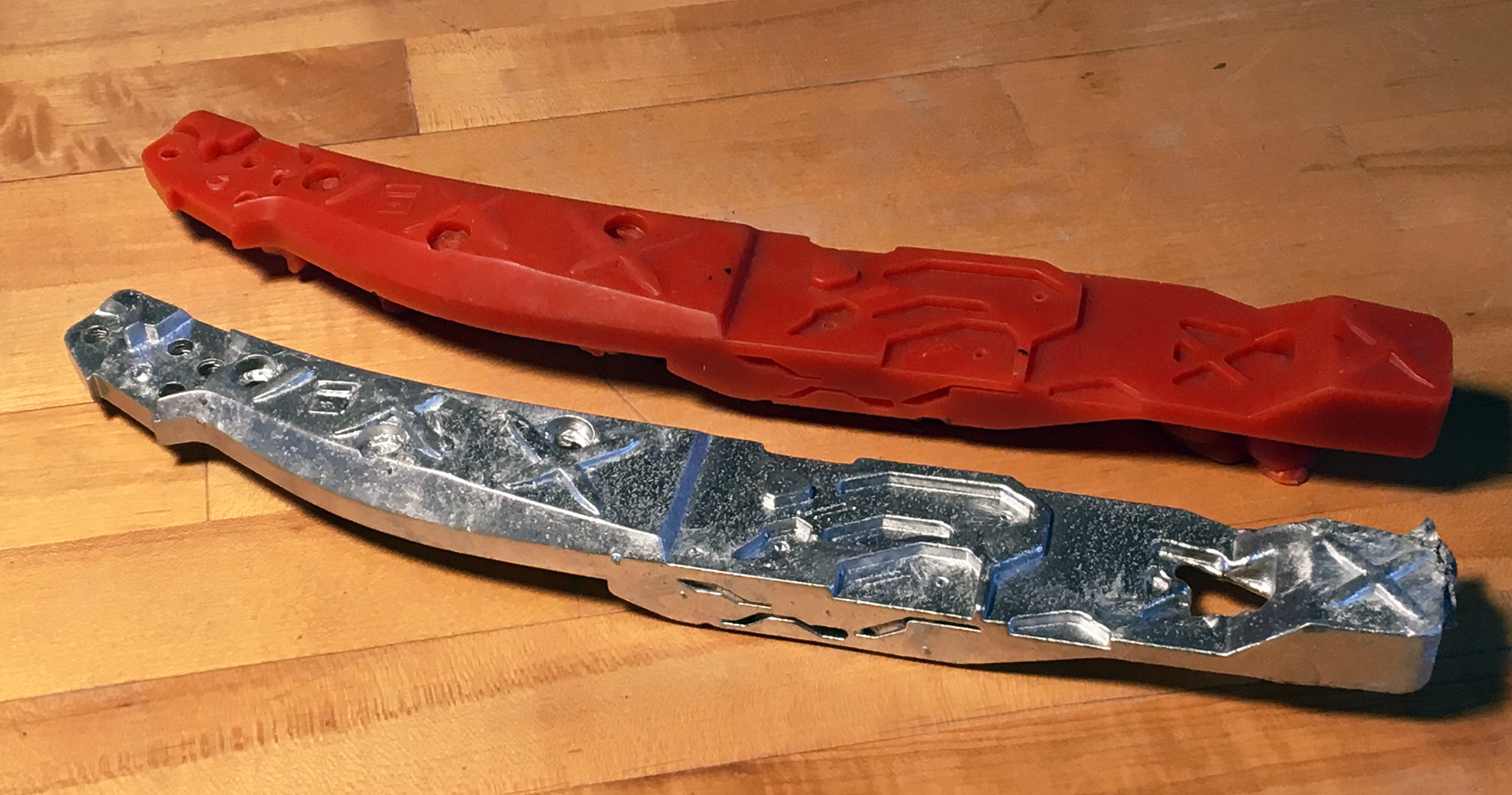
It's interesting to note that the butt of the model (with the square cross) is blurry compared to the rest of the model because it was partially exposed to the surface. That means to achieve good results throughout, the model needs to be as deep inside the mold as possible, with only a thin sprue leading out. Otherwise it must be mixing with hydrogen from the atmosphere and failing to fill.
Discussions
Become a Hackaday.io Member
Create an account to leave a comment. Already have an account? Log In.