"I know what you're thinking. 'Did he fire six shots or only five'? Well to tell you the truth, in all this excitement, i kind of lost track myself. But being that this is a .44 Magnum, the most powerful handgun in the world, and would blow your head clean off, you've got to ask yourself one question: 'Do I feel lucky?' Well do ya, punk?"
Other than openly challenge the punk who's taken my work and claimed it his, along with the credit for the low-poly-count art movement in the UK design sphere - ludicrous peacock that he is - there isnt a lot I can do.
No wait, there's a lot I can do that he cant, because he's just a faker, not a maker.
Lets see if the punk can get up from a convex copper-jacketed surface like that of the slug fired by Harry's oversized weapon, shall we?
Retroactive Development
I'm pretty sure I've mentioned the concept of rolling back parallel development into Cardware and this is the result. Using the shielding from Decal and developing the geometry from Internet of condoms, I've revised the system completely.
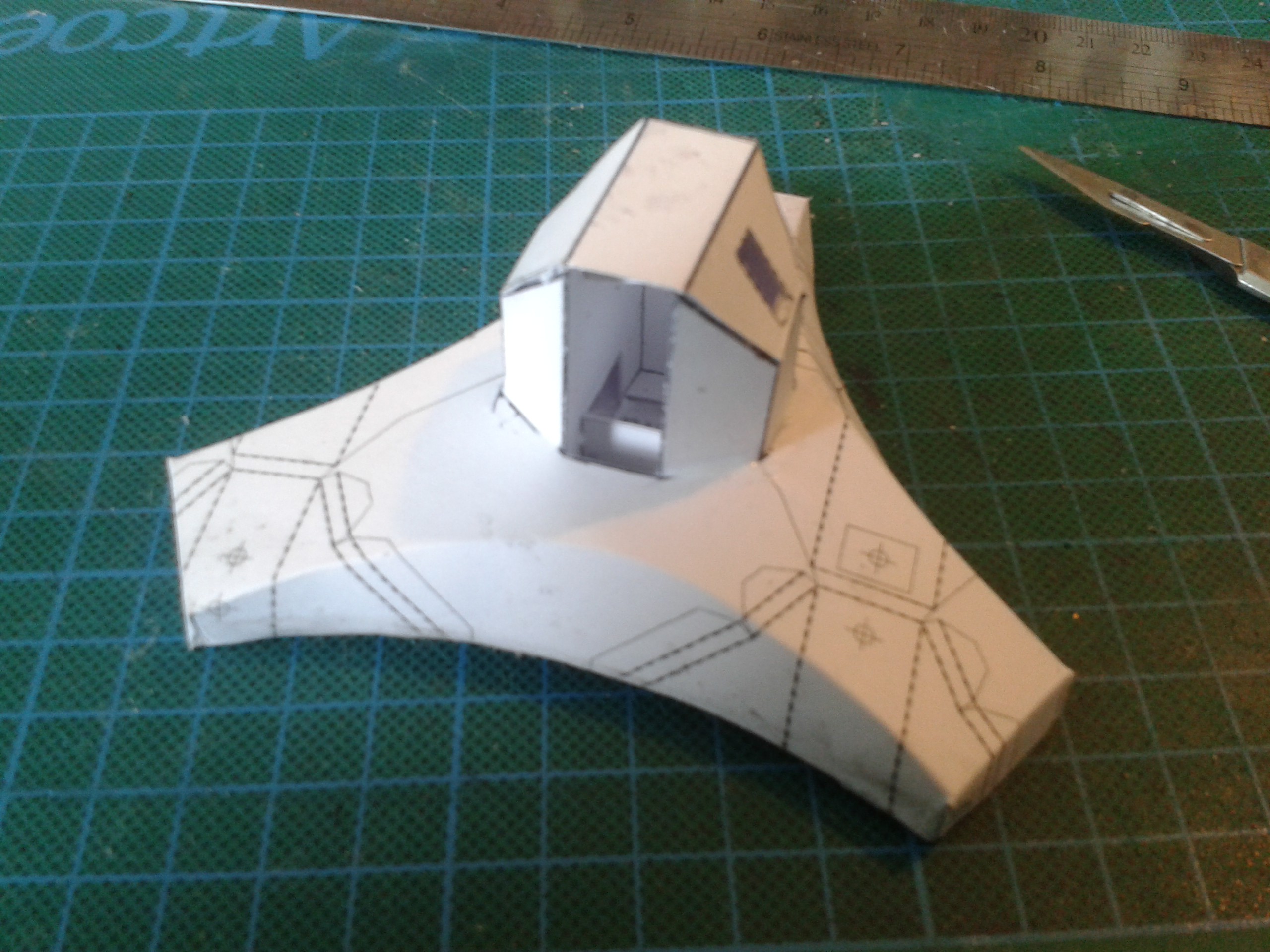
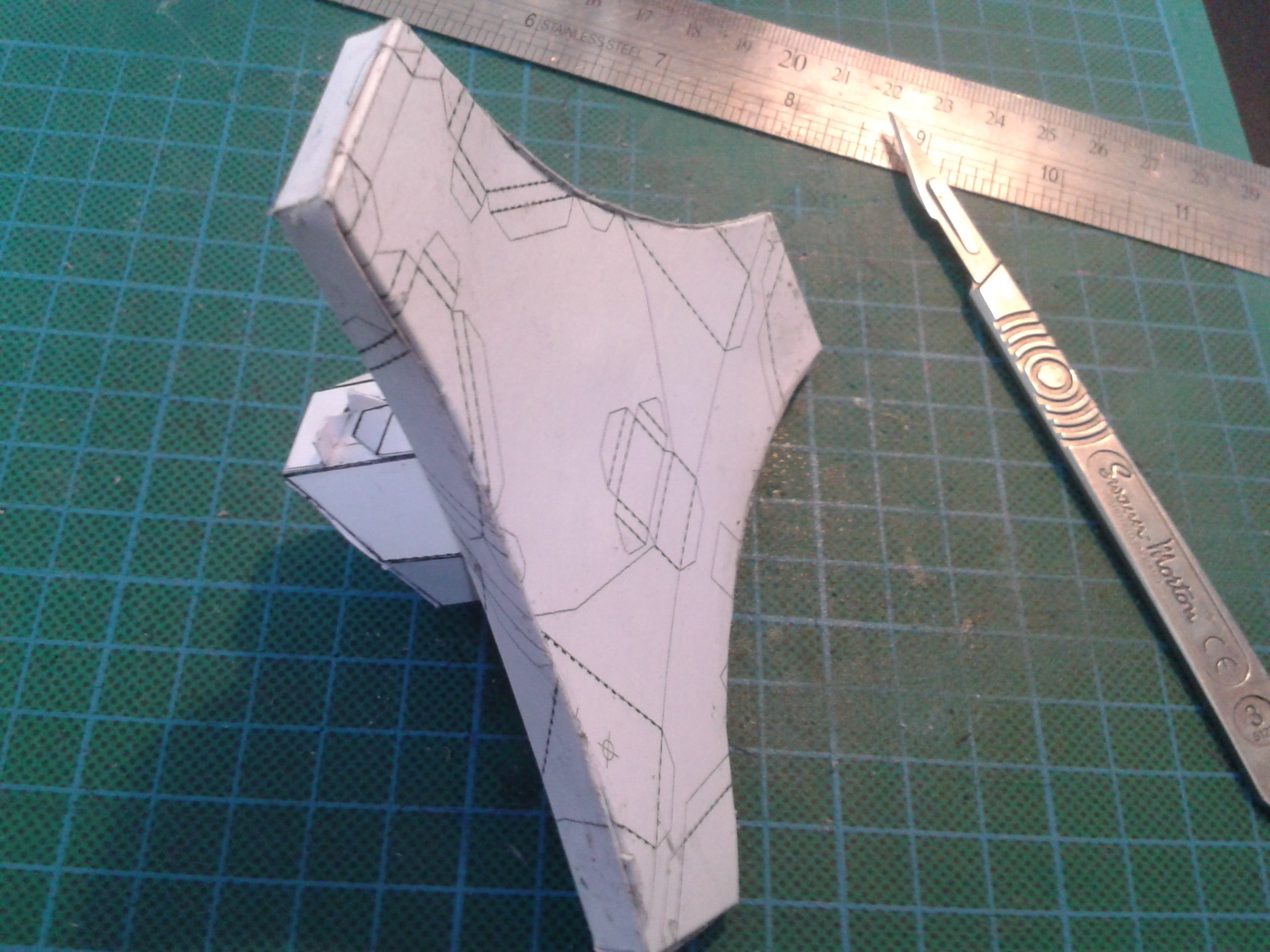
Thankfully, the maths for this is actually really simple, they are just Parabola. Same as the trajectory of a bullet. Not that it matters at this range.
Boom, headshot
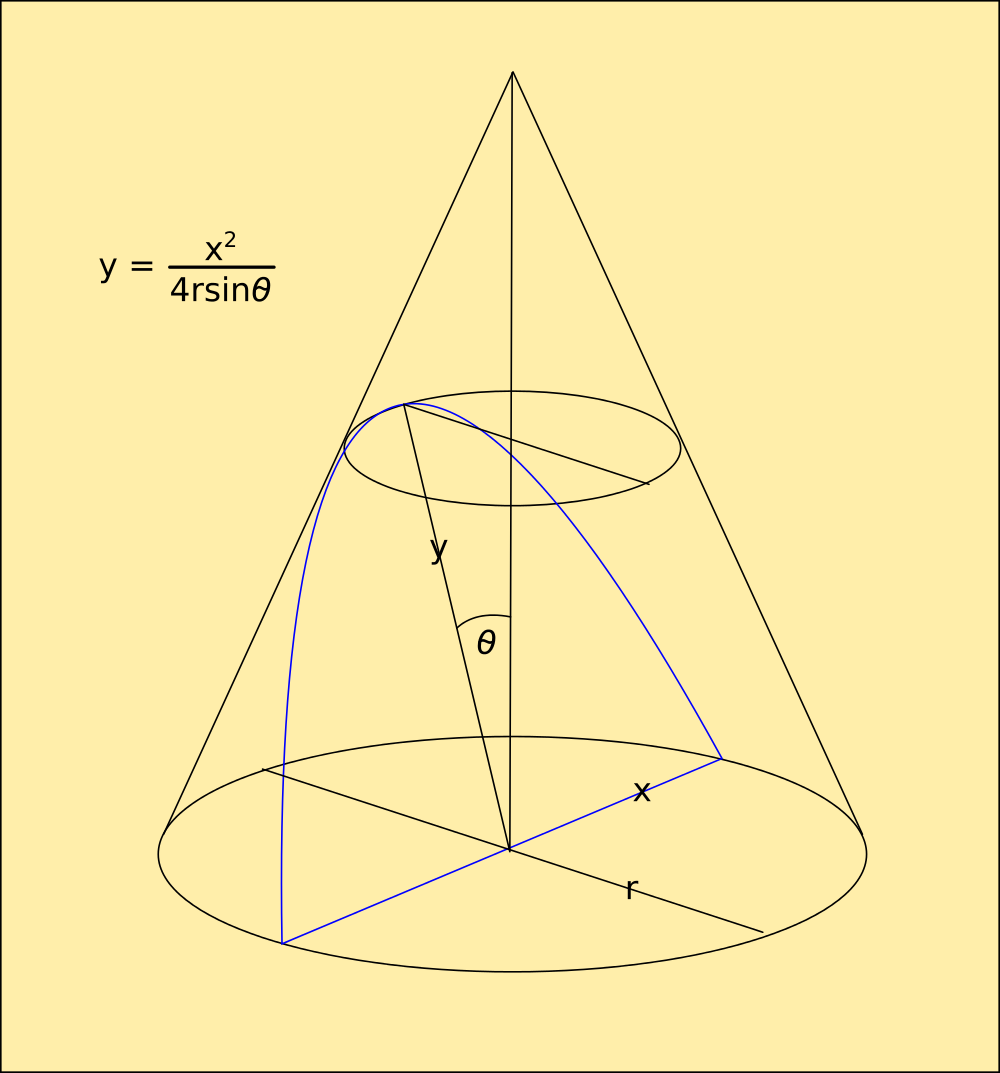
Did you follow that, Robin? Doubt it. You think Network Node Analysis is geometry. It isnt - LPC Art relies on statistical analysis of the nodes and their interconnects and doesnt require knowledge of the angles between them. You'd know this if you'd actually used the two entirely different types of mesh generated by the techniques.
A bit of heat, and you sag like your poncy perfumed candles.
I'm still not done. I've integrated Decal's laminar technology, adding structural integrity, EM shielding and a really nice aesthetic to it.
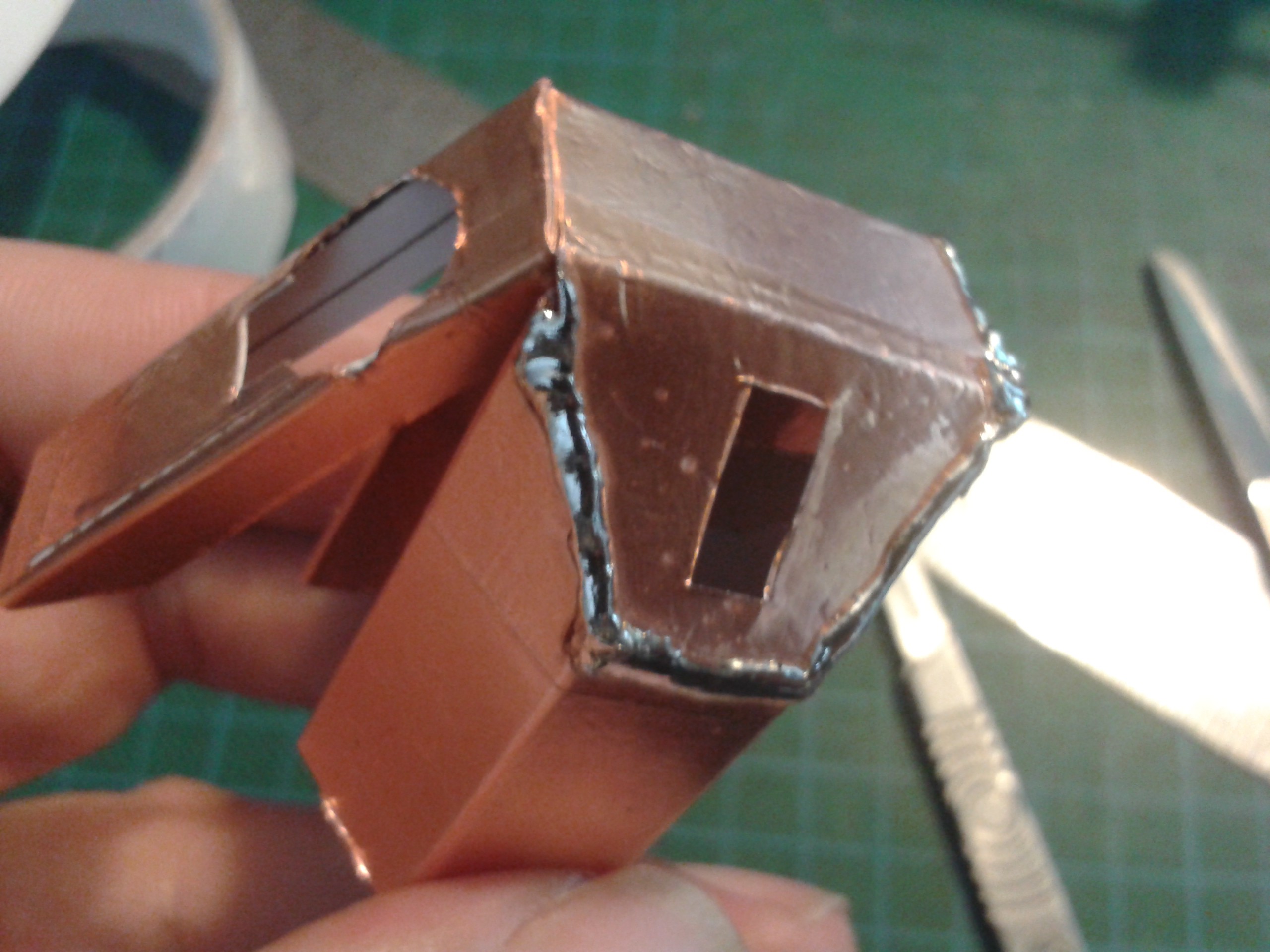
There's 3 layers to that, cardboard, copper and sticky-back plastic. I dont know what that is made of but it just vanishes without much in the way of smoke or residue and solders clean through with no trouble.
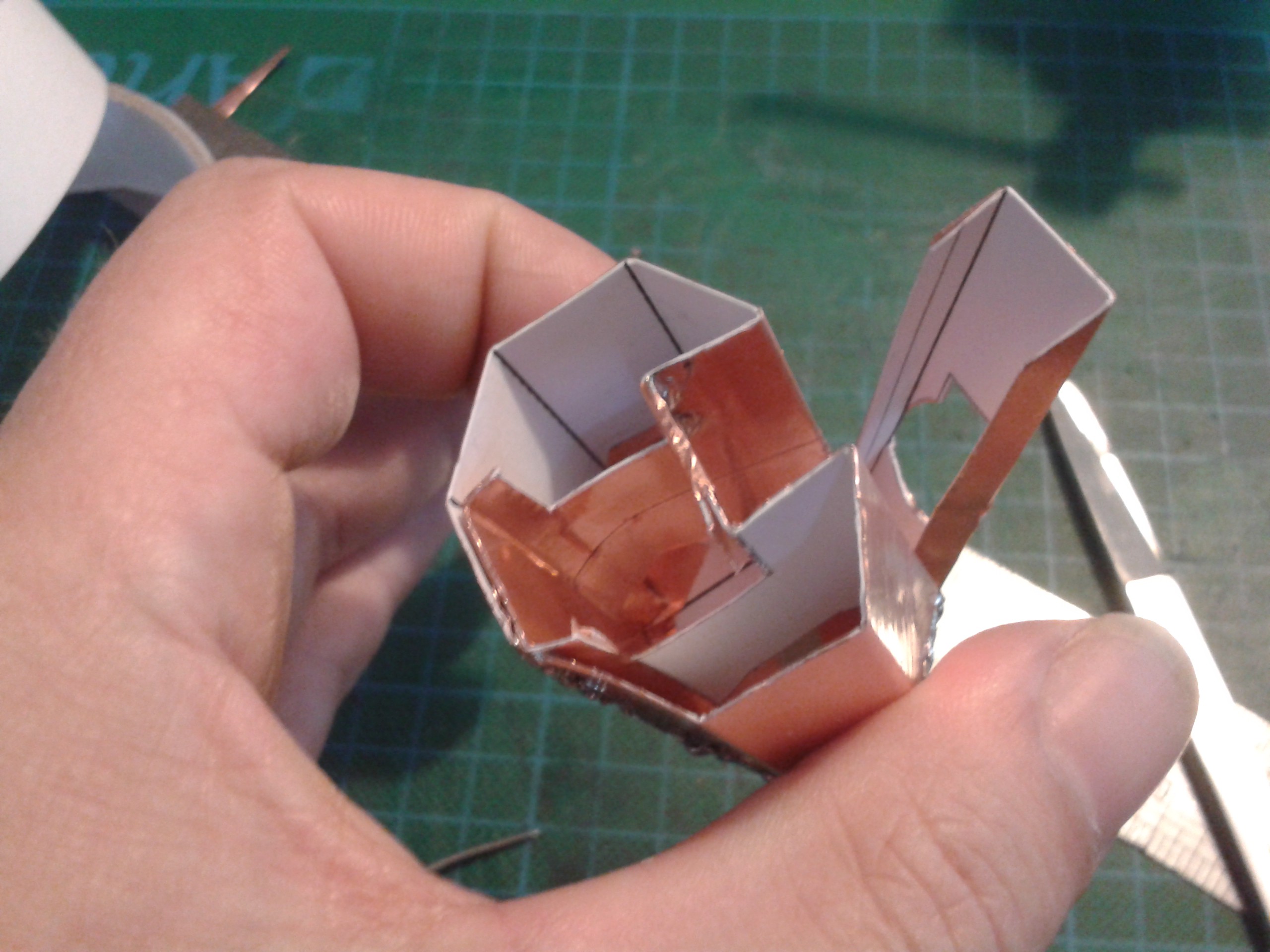
The only consideration with this technique is lapping the edges of the copper over the edge of the cardboard, because solder really doesnt like bridging these gaps. Unlike copper plate, it solders with a 15W iron because the copper is too thin to wick the heat away. It bends and curves like copper too, but cuts with a scalpel or scissors, can be glued and printed on and doesnt scuff or pick up fingerprints with the plastic coating.
Gold standard in modelling materials
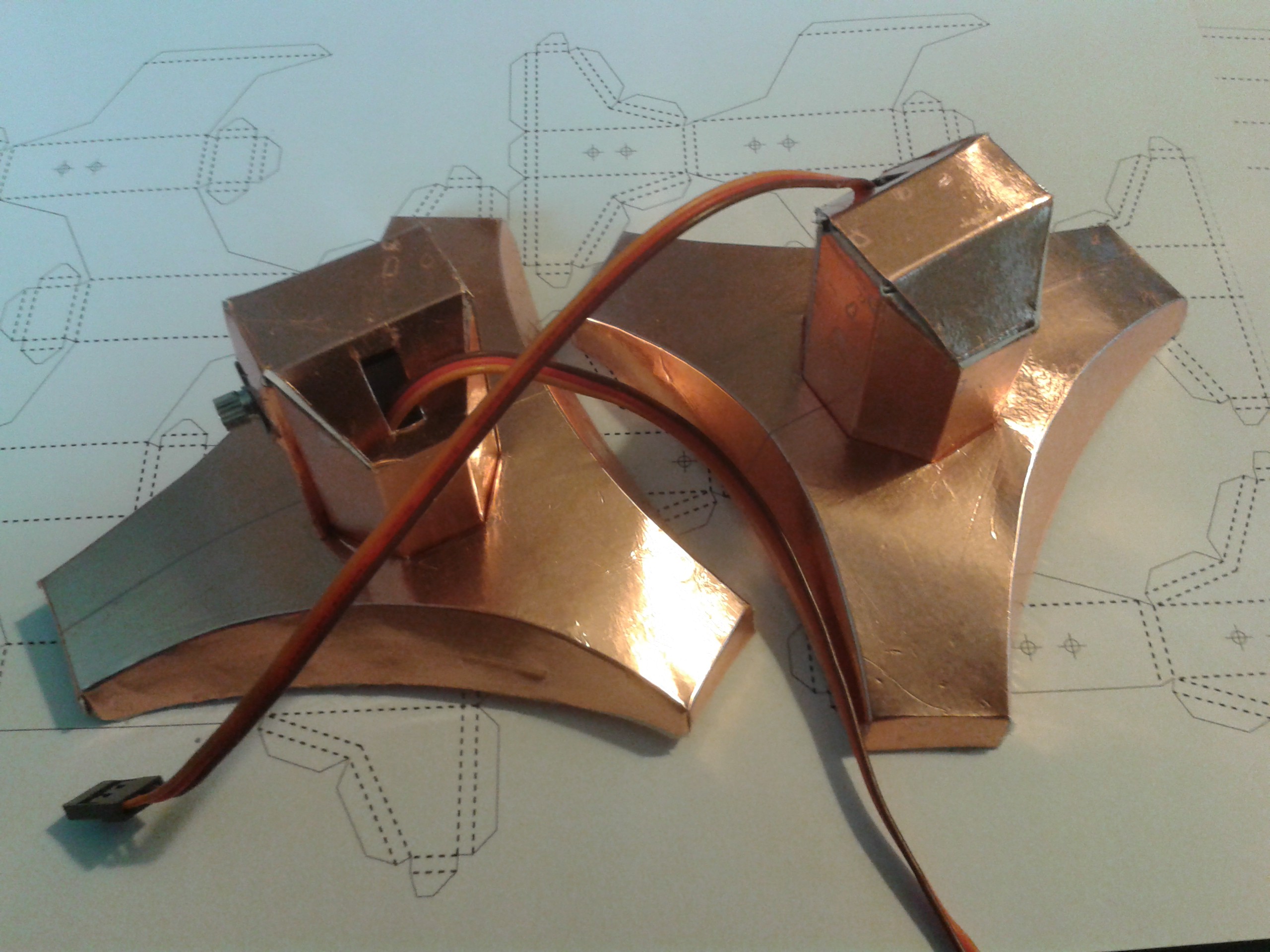
I've treated all the parts in similar fashion. Hard to believe that's cardboard and weighs almost nothing.
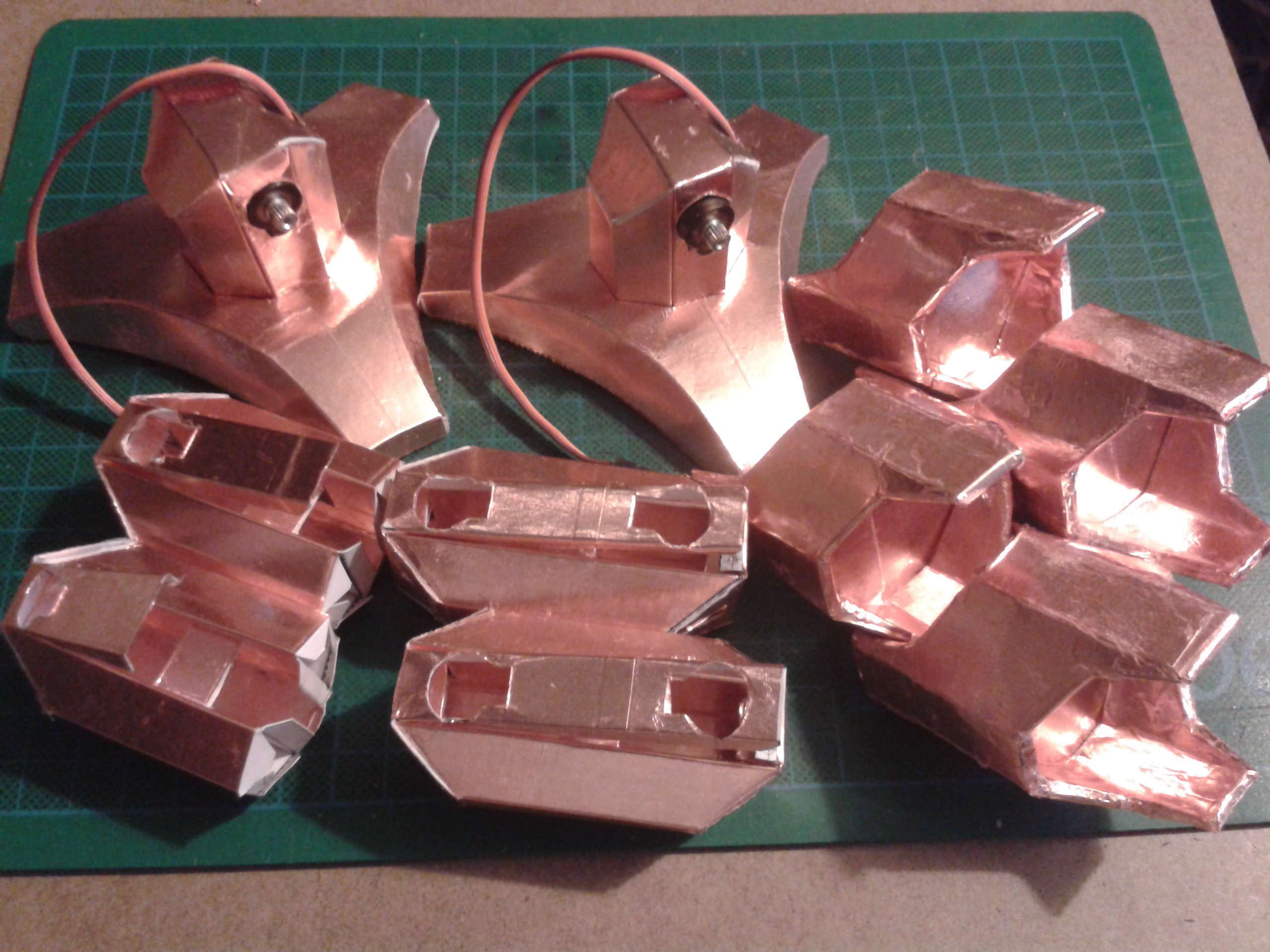
New sensors
Because Cardware weighs so little I had too much trouble using the QTC I'd planned. An entire leg barely registers, and because of the way it is manufactured each piece behaves slightly differently so it's hard to calibrate too.
Instead, I've added potentiometers to the joints and am using angular displacement to sense the robot's true position against the intended one. I had to use the micro potentiometers and modify them as well to get them to fit in the joint, but the bonus is they have replaced the hinge mechanism too.
I first used the plastic capped type and drove a screw into it to affix them but they turned out to be really weak and broke in minutes.
I've gone over to the metal-chassis type and modified the legs and wiper.
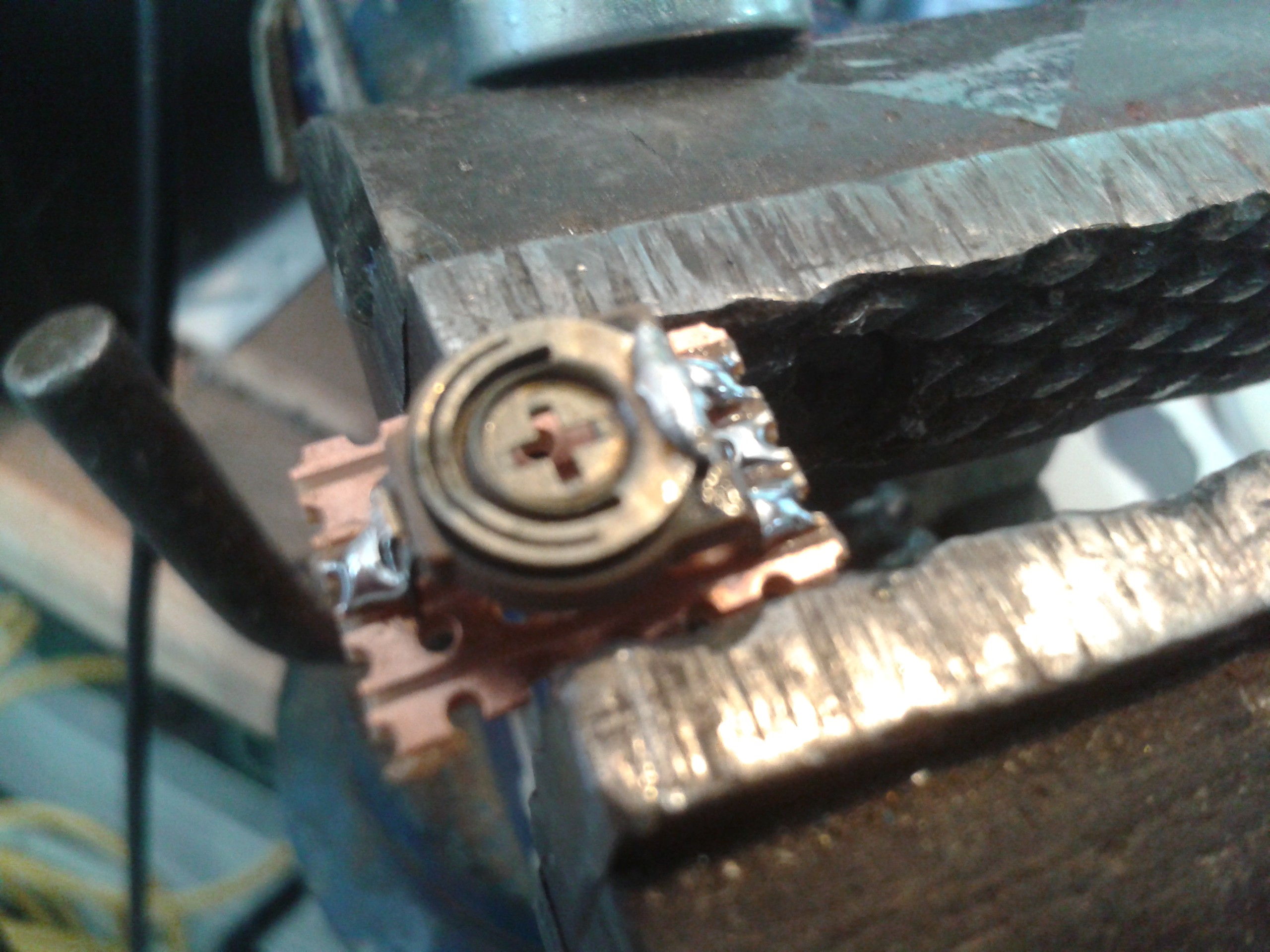
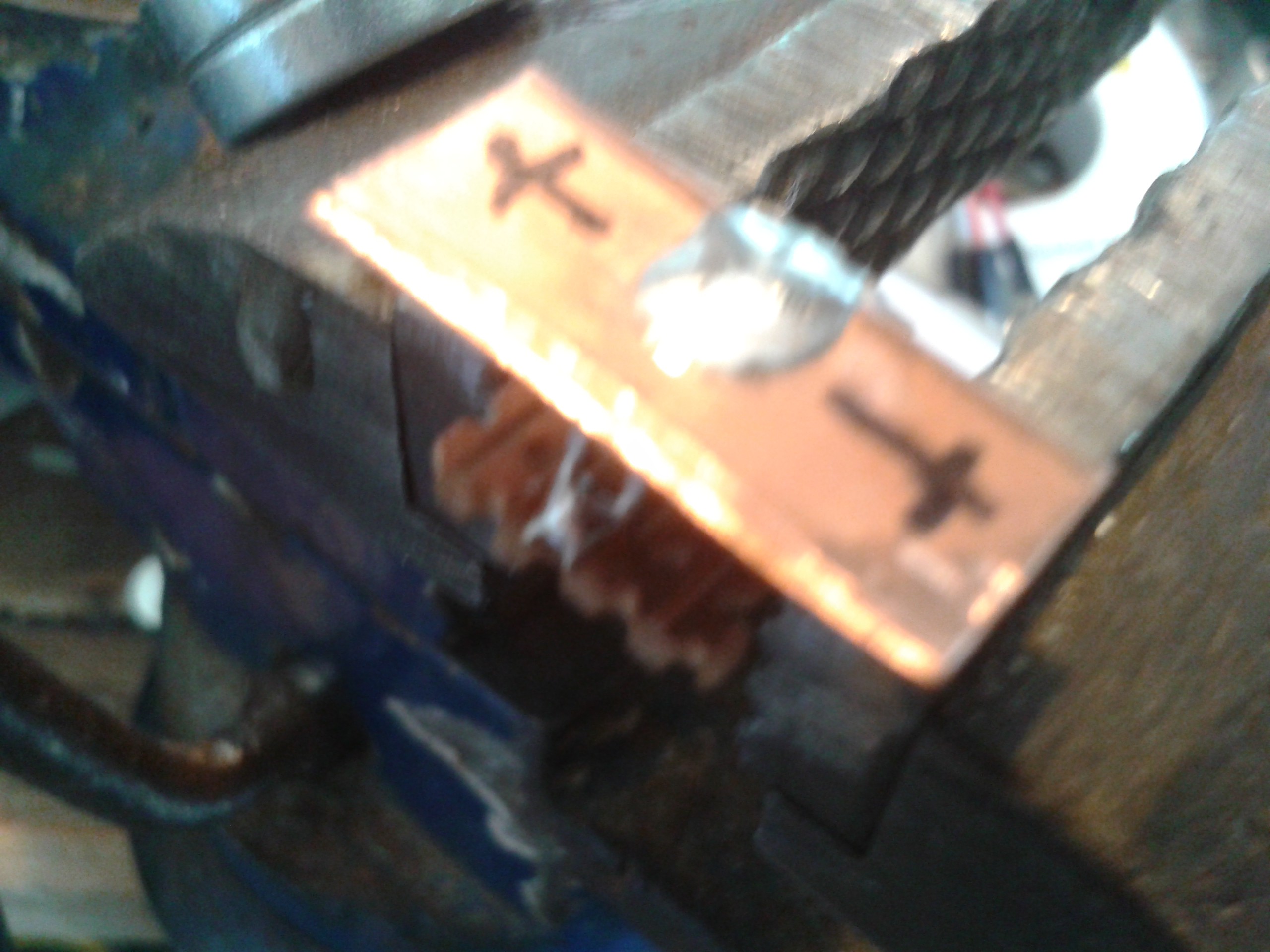
That now fits neatly into the gap between the powered and unpowered modules opposite the servo actuator.
Rejigging
After all the little bits of adjusting I'd done to each part I had to go back over the entire set to make sure they still fit together perfectly and behave as a system. This wasnt easy because the parts are universal; change one, you change all to match.
Finally I got them all to tessellate together. This is missing the radial servo from the top that rotates the entire limb so the robot can turn corners without shuffling, but otherwise displays the 5DOF - 180 degree throw on every plane I've been working towards.
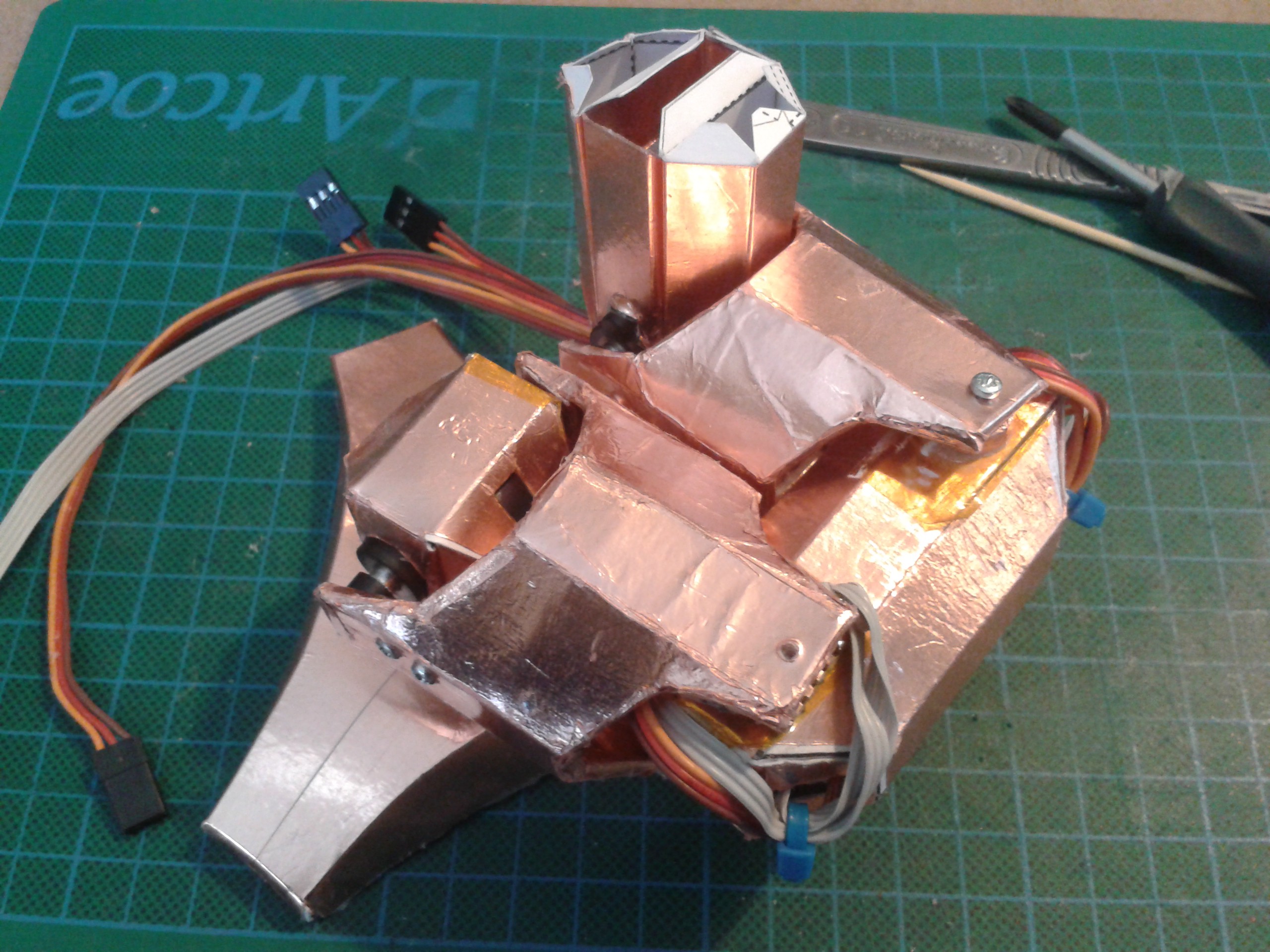
Discussions
Become a Hackaday.io Member
Create an account to leave a comment. Already have an account? Log In.
Classic Dave XD Thanks buddy :-))
Are you sure? yes | no
shiny :)
Are you sure? yes | no