Everything seems to be made to fall to bits at the slightest provocation these days.
I saw an advert on TV featuring a graphic number of ways your mobile screen would need replacing, from leaving the phone on the car roof and driving off, to sitting on it while making out. Is that a phone in your pocket or are you just pleased to actually see me... Lol... Anyway, it wasnt an ad for a phone repair shop, it was a carrier advertising a free screen replacement with my new phone.
I'll keep my wrist harness thanks, the current Z3 is over two years old, paid for and still in near-perfect condition. I replaced the Galaxy S3 that preceded it because I took it out of the harness while moving furniture and put it in my back pocket, then landed on it going up a flight of steps. Oh well... It takes lovely pictures though, and remains cabled to my PC for documenting my work.
Last I looked, anything that needs free repairs when sold was broken before it was bought, hook line and sinker at that. Nightmare. It doesnt help that things are made of crap that falls apart, so even if the thought is there for end quality it makes no difference.
I've spent weeks waiting for orders, searching online and testing potentiometers to find something half decent;
These things fell apart spectacularly quickly, they didnt even make it into service and broke during assembly. The rivet came out leaving the wiper soldered to the plate. There wasnt a lot of solder there, but its still stronger than the working parts...
I had an awful lot of trouble with these too. After splitting the harvested ones I first tried by driving a screw into them, I bought some 'quality' ones and glued them to a bearer.
Unfortunately the glue capillaried up one of the channels and got on the track or wiper and locked most of them solid. Only a couple worked and those I freed off read open circuit.
Not that it made any difference really, they were advertised as 5% tolerance. Somebody couldnt count and I was pretty sure it wasnt me. They were all pretty bad except for one, which measured 99.7K. I suppose that constituted the 5% out of the batch that could be called within tolerance. Hmmm... This isnt what I call quality, those are K's its out by. Errors in hundreds of Ohms I can understand, but as a voltage divider that is utterly useless.
I shopped around a bit. The one on the left looked promising until I discovered sneakily soldering those tabs to the wiper plate and then to a plate left specks of flux all over the track so it had dropouts in it. I couldnt clean them up and all but gave up.
I remembered there is already one in the servo, and I had resigned myself to the possibility of ripping out the servo circuit and driving it off the processor via an H-Bridge up in the chassis and cabling the motor and potentiometer. I pulled some broken ones apart for the motors and had a look to see if they were harvestable instead. They arent any stronger than the others, and rely on the servo shell as a bearing as well, I couldnt just cut them down and solder a plate to them.
While I was looking online I discovered a previously unknown description for them. I'd tried potentiometers, variable resistors, trimmers but hadnt thought of Presets. Thats what these are apparently. And Squires had them in stock, so I got them local too.
At last something solid that I can keep glue out of and find an interface for! I shaved off the bezels so they would lay flat on the cardboard and covered the backs with metal tape before turning to my favourite metal of all to build something to turn them with. Something that I could also secure to a flat surface.
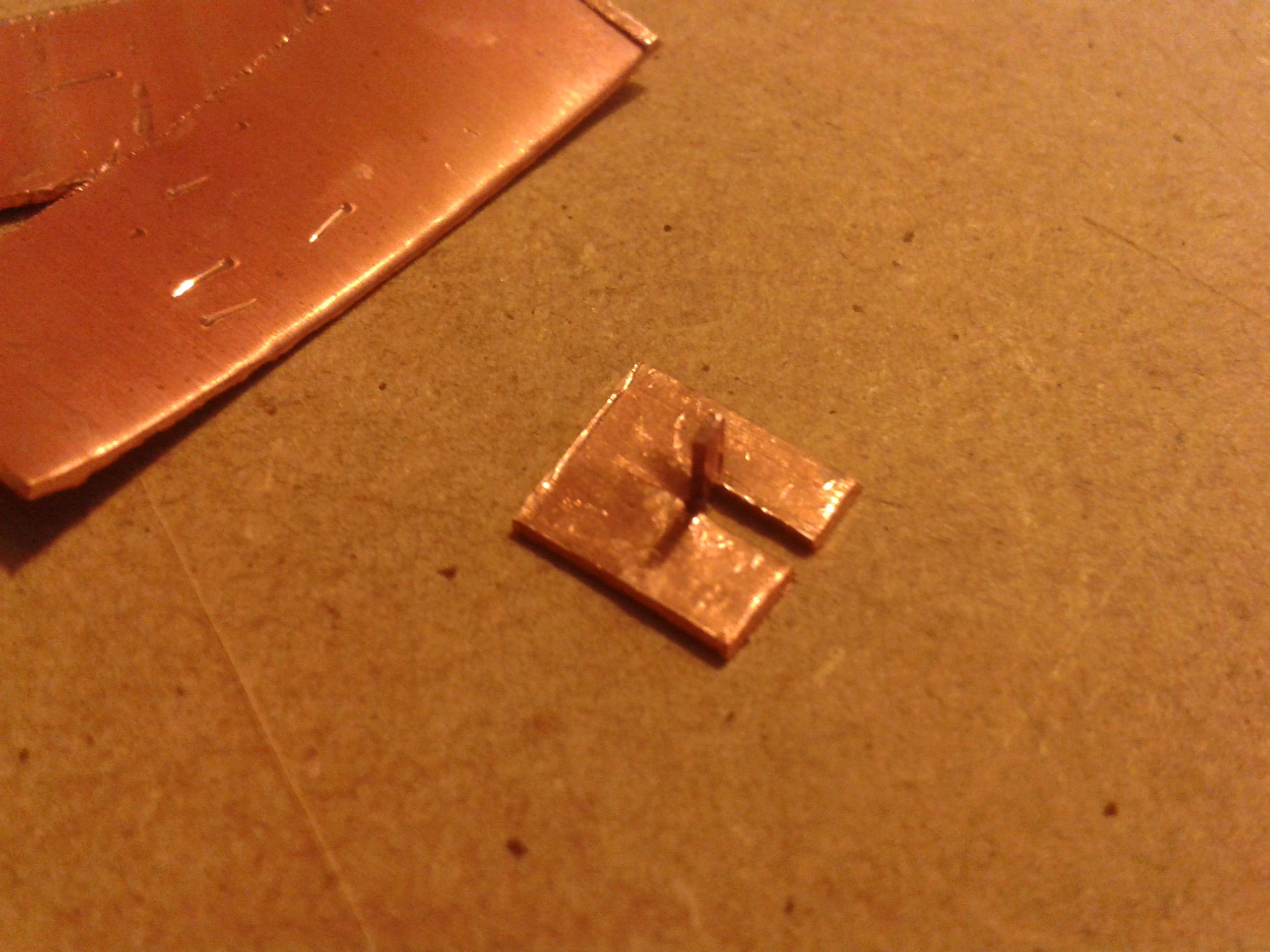
That works like a charm, although I did have a bit of a hiccup halfway through assembling the rest... They were bought as a batch, all from Iskra, all 100K presets and all pretty much identical (even the tolerances were close) except for one vital feature.
The copper pin didnt fit the slot quite right and there was a little bit of play so I fitted it across the arrow instead. That worked a treat until I got to number 4 and discovered the remaining half werent completely identical. There's two different types of arrow... Nice one, Iskra. I dont know which is the old spec, but I think it may have something to do with the one on the right being impossible to read without magnification let alone in a dark recess lit by the backs of LEDs. I just hope thats the old one. A bit of filing sorted it out anyway...
And it fits even better than all the trimmers, some of which worked out over 6mm high with the circuit board to mount them. These are under 5mm high.
A bit of wiring later...
Thats got the limbs reassembled with working angular sensors, and without having to take apart a brand new set of servos. I may have a go at hacking these at some point after reading Radomir's #Ensmarten Your Servos
but I'm not entirely happy with the idea of buying broken new hardware and hacking it. Servo's are older than I am, moan, whinge, etc.. ;-)
I also had some servo trouble at the top end and had to redesign the interface to the tops of the limbs. They were driven directly by the servo shaft, but limitations with the materials and the rather ancient design of the mountings meant I had to fall back to the barbaric practise of chassis-mounts and push-rods. Every time I see that mechanism, I also see flapping canvas and flying-ace goggles spattered with engine oil, followed by a plume of smoke. :-D
The bearings are made from 'paper metal', which has turned out to be another interesting and useful hybrid of materials. The rods for the thigh pieces are made by wrapping a sheet of paper around a metal rod and securing the end with a piece of metal tape several layers deep. It is burnished with a piece of dowel before being wrapped with another piece of metal tape glue-outwards. Finally this is wrapped in a sheet of paper and secured with more tape. The resulting bearing and shaft set weighs very little, is as strong as plastic, fits perfectly and can be greased to further extend the life of the working surfaces, which are all-metal.
Amazing what you can make with a sheet of paper and sticky tape.
All I have to do now is trim that up, plug the tops of the tubes with something I can screw a lever to, and then mount the servos as per a model aircraft. Shudder...
I have had time to make a lid while I was waiting for parts, in between catching up on other projects. I used the MorningStar maths for this, as that is what it was originally intended for. ;-)
Wiring is next, and Ars' #ZeroPhone - a Raspberry Pi smartphone also provided me with a battery solution; I had to buy some anyway and I can just run voltage regulators off pairs of these in series:
Anyone remember Batteries Not Included? :-D
Discussions
Become a Hackaday.io Member
Create an account to leave a comment. Already have an account? Log In.