Over the past couple of weeks (plus some extra to start writing this probably last log entry), I've ordered everything and started soldering and assembling.
PCB after soldering? All okay and everything works. It wasn't a very complex one to begin with, but still it is always nice when something is just correct.
3D print parts: printed very nicely, but didn't fit. In the picture below how the lid of the box housing the PCB should have looked. Unfortunately, on the initial print, the cable feedthrough hole was misaligned by at least 5mm.
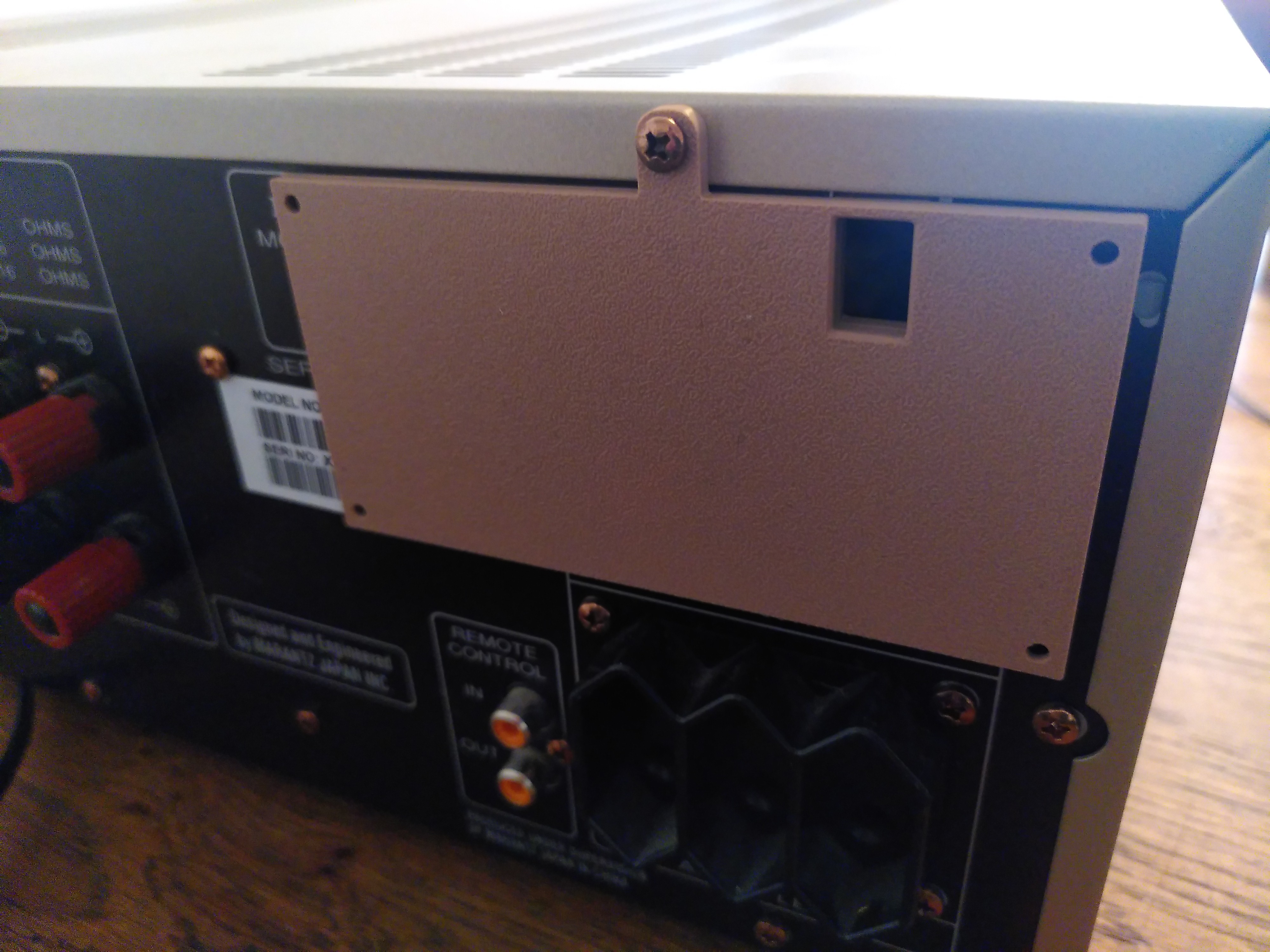
What went wrong with the alignment: initially, I had planned another mounting method on the back of the amp, not really using the cable feedthrough. I had measured the back of the amp with my caliper, but only roughly drew the feedthrough in FreeCAD as reference, without proper measurements. I didn't update it (or think of it) when I changed directions.
When I worked as a professional CAD-designer, my credo was "Always draw everything and correctly". This has been another lesson in that and could have easily be prevented. (The "measure twice and saw/drill/print once" statement also comes to mind...)
So after redoing the measurements, updating the design and ordering a new print of the lid (thanks again 3dk.berlin!) it fit nicely, resulting in the following assembly. Note that the housing isn't filled with components yet here.
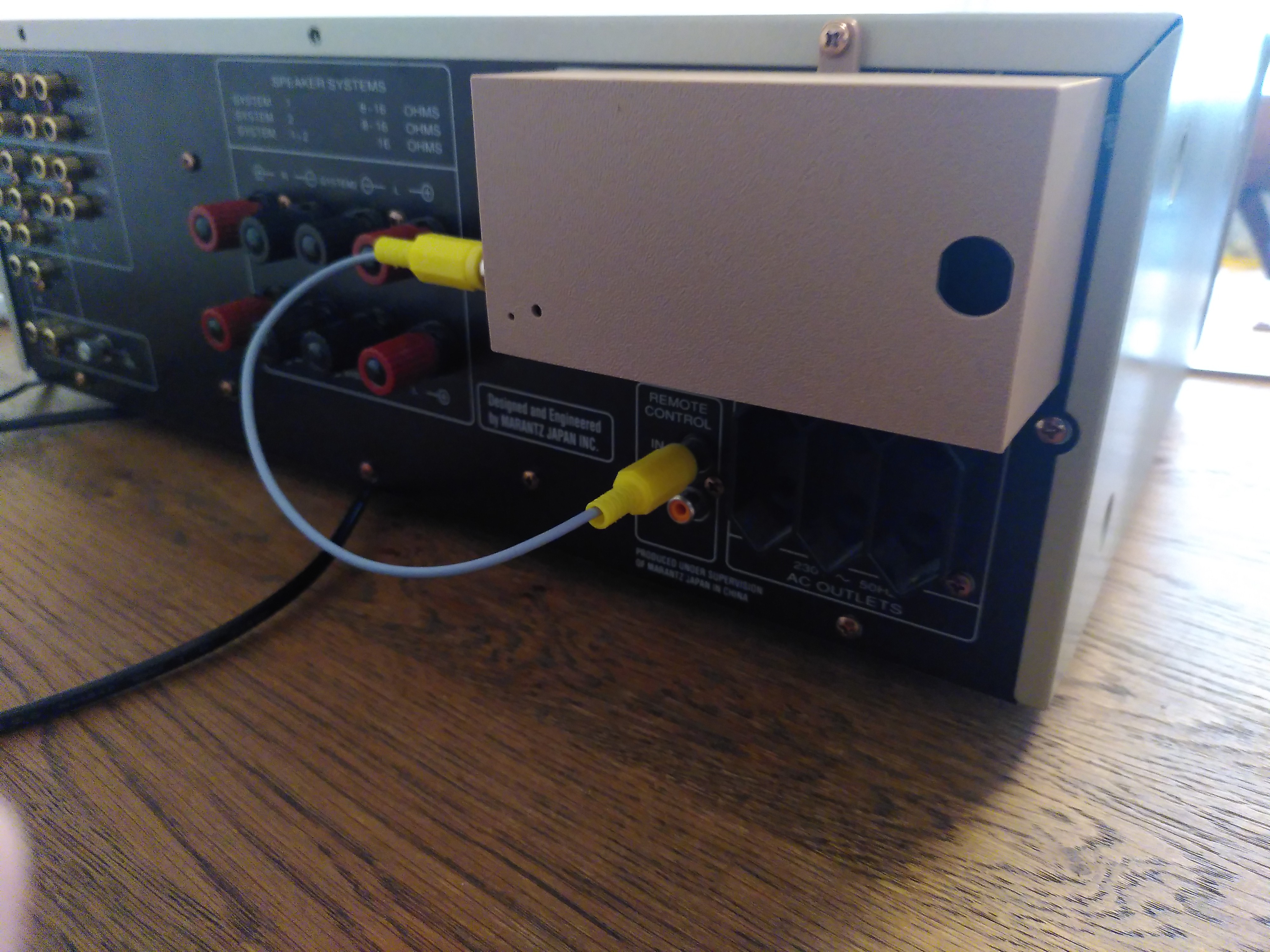
The next challenge
So, on to the final assembly and the next thing I didn't think about:
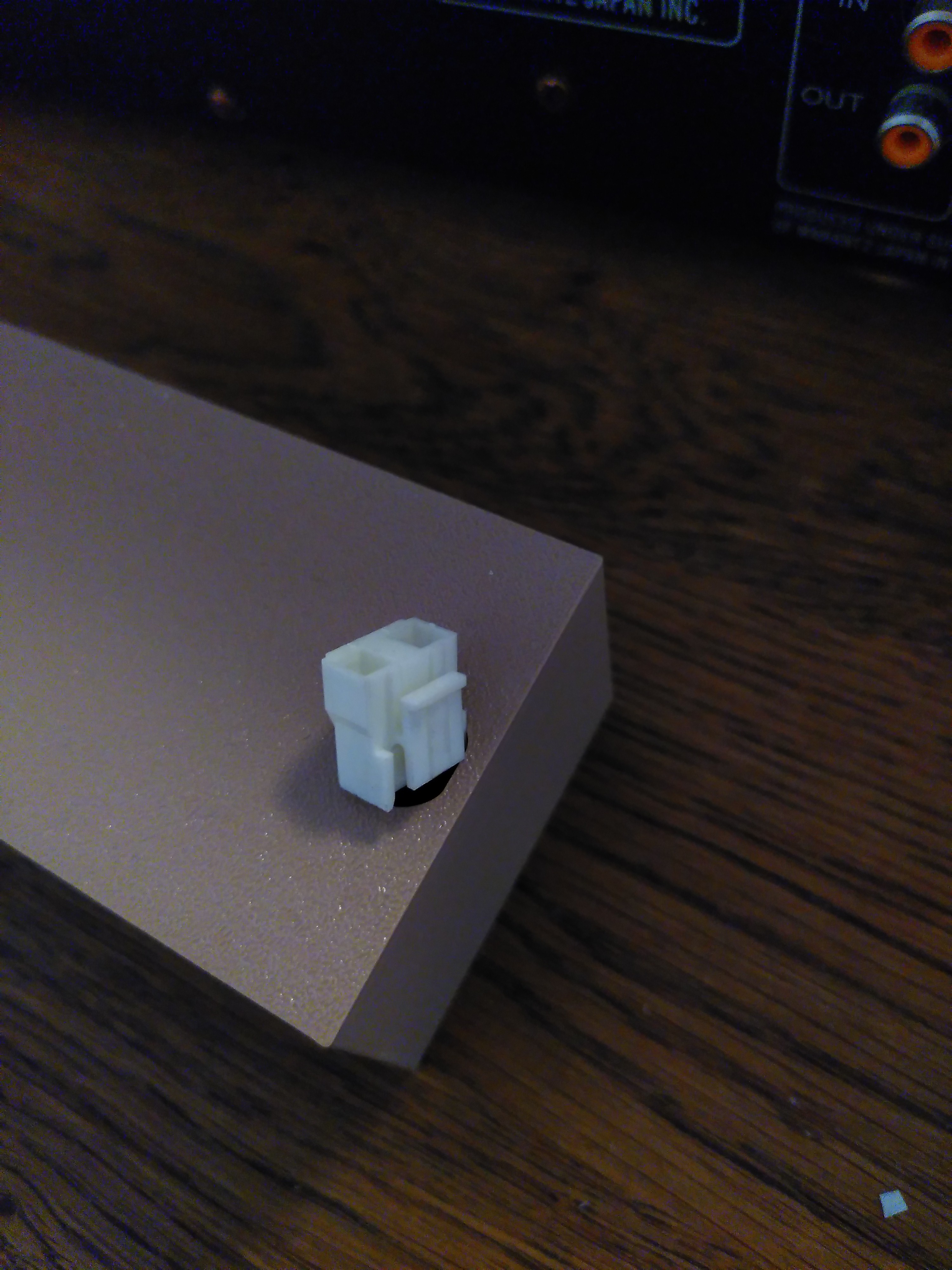
Inserting the power cord with the JST plug on the amp side into the box. Great idea, bad execution, because that didn't fit the cable entry reserved for a strain relief (a TME SR-F42 I still had from a previous project). Luckily, I could remove the 2 cable crimps misusing an iFixit SIM ejection tool bit. On the front side of the connector, there was a small slit beneath the contact, in which it could be inserted and by fummeling around a bit and pulling on the cable, the inserts could be removed. The iFixit bit has seen better times now though. It definitely is not an official extraction tool for these type of connectors...
Assembly
After that, it all went a bit better and everything could be fit in the housing.
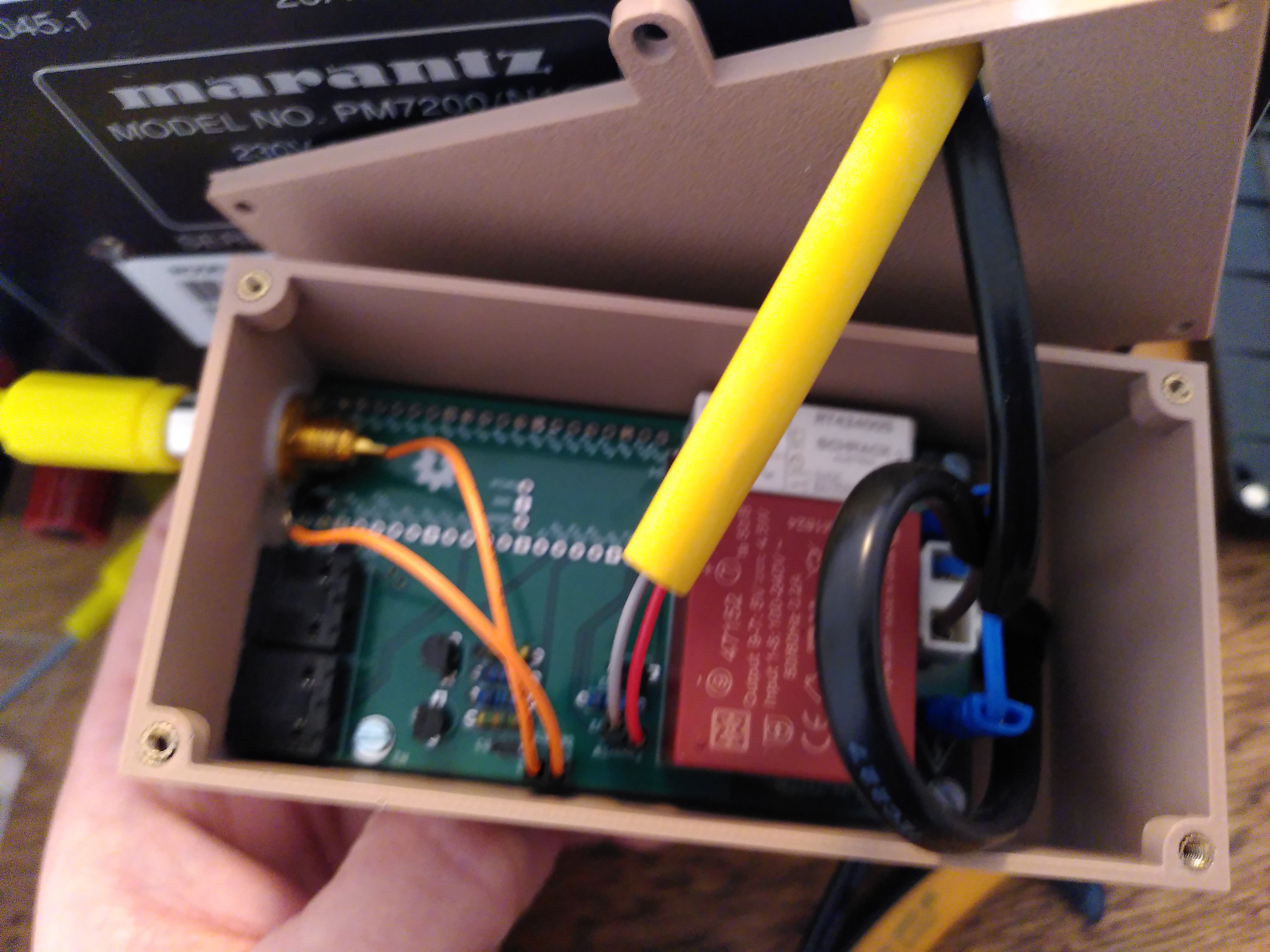
On the right side, the re-assembled JST-connector, providing mains input to the PCB. 2 fastons are used as switched mains output, these connect to the mains input of the amp (after the power switch, see previous log).
Furthermore, there are 2 wires connected to the RCA output, providing the remote control signal and 2 wires connected to the repurposed power switch (see log). I now soldered them and added some extra shrink sleeve, since I didn't think the wires were good for mains isolation.
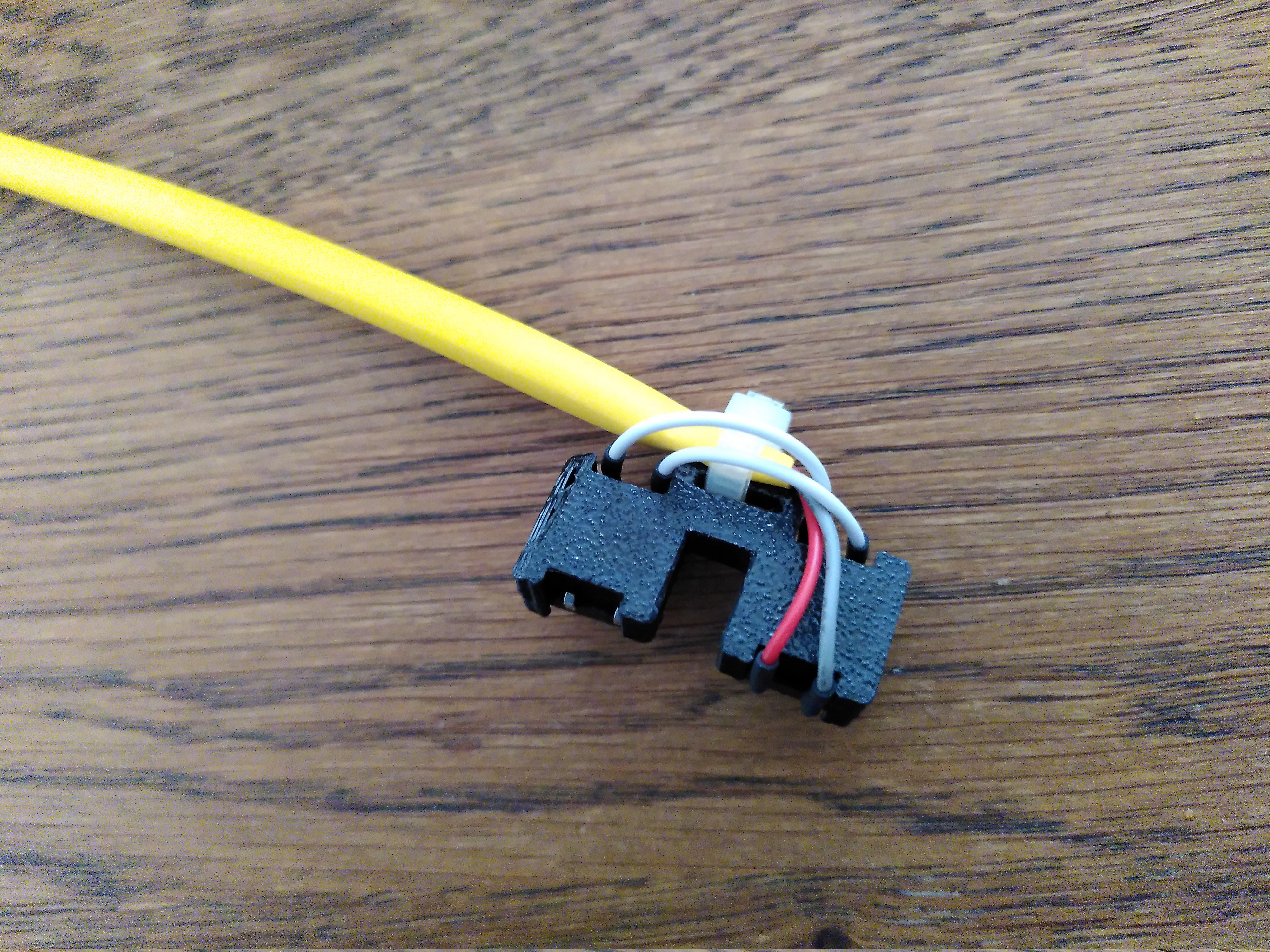
Inside the amp, it now looked like in the picture below. Note that I removed the cable tie from the switch assembly again, as the tension of the sleeve permanently triggered one of the micro switches.
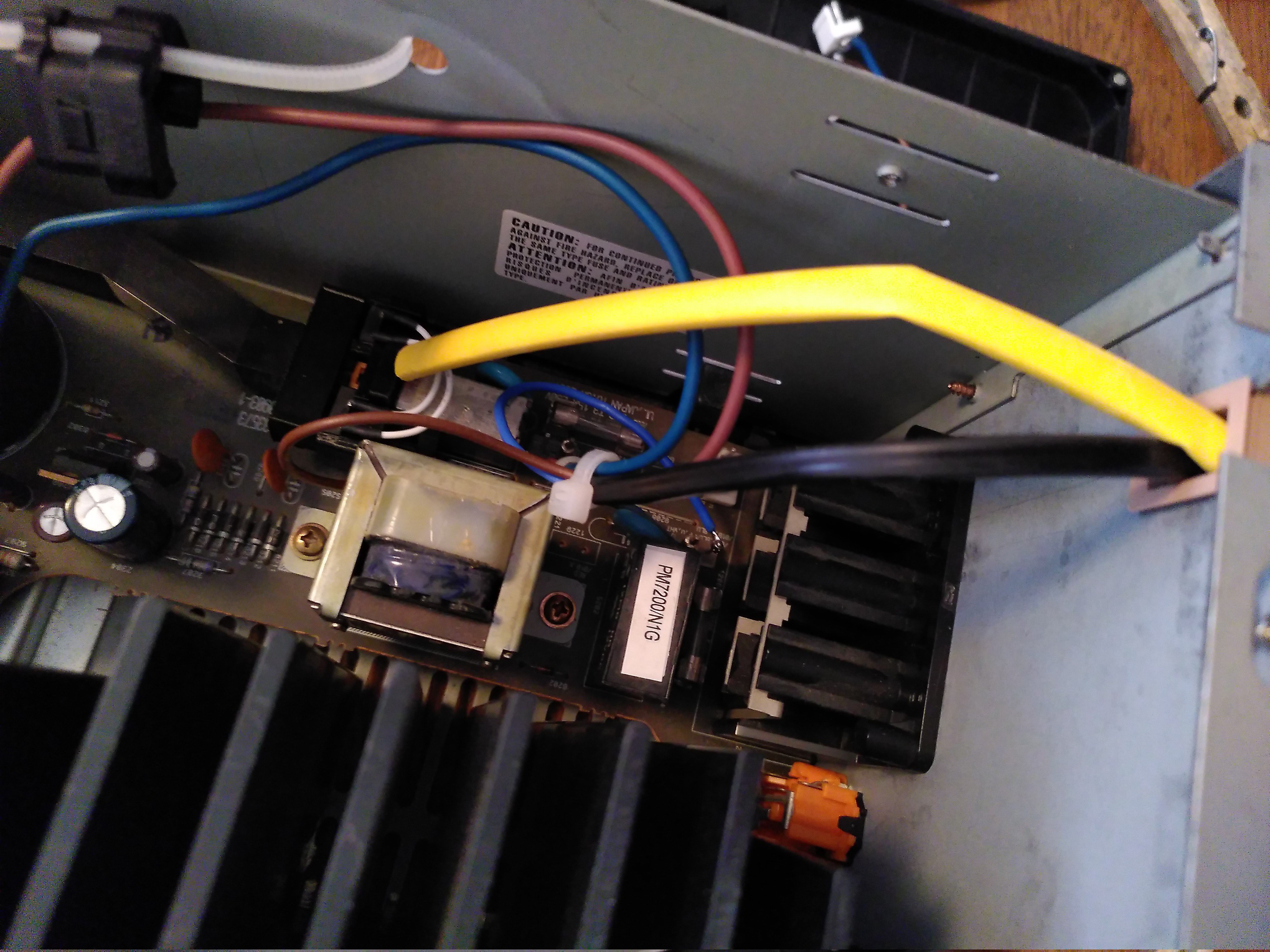
After screwing the 3D printed housing and the amp shut, the result looked like in the picture below.
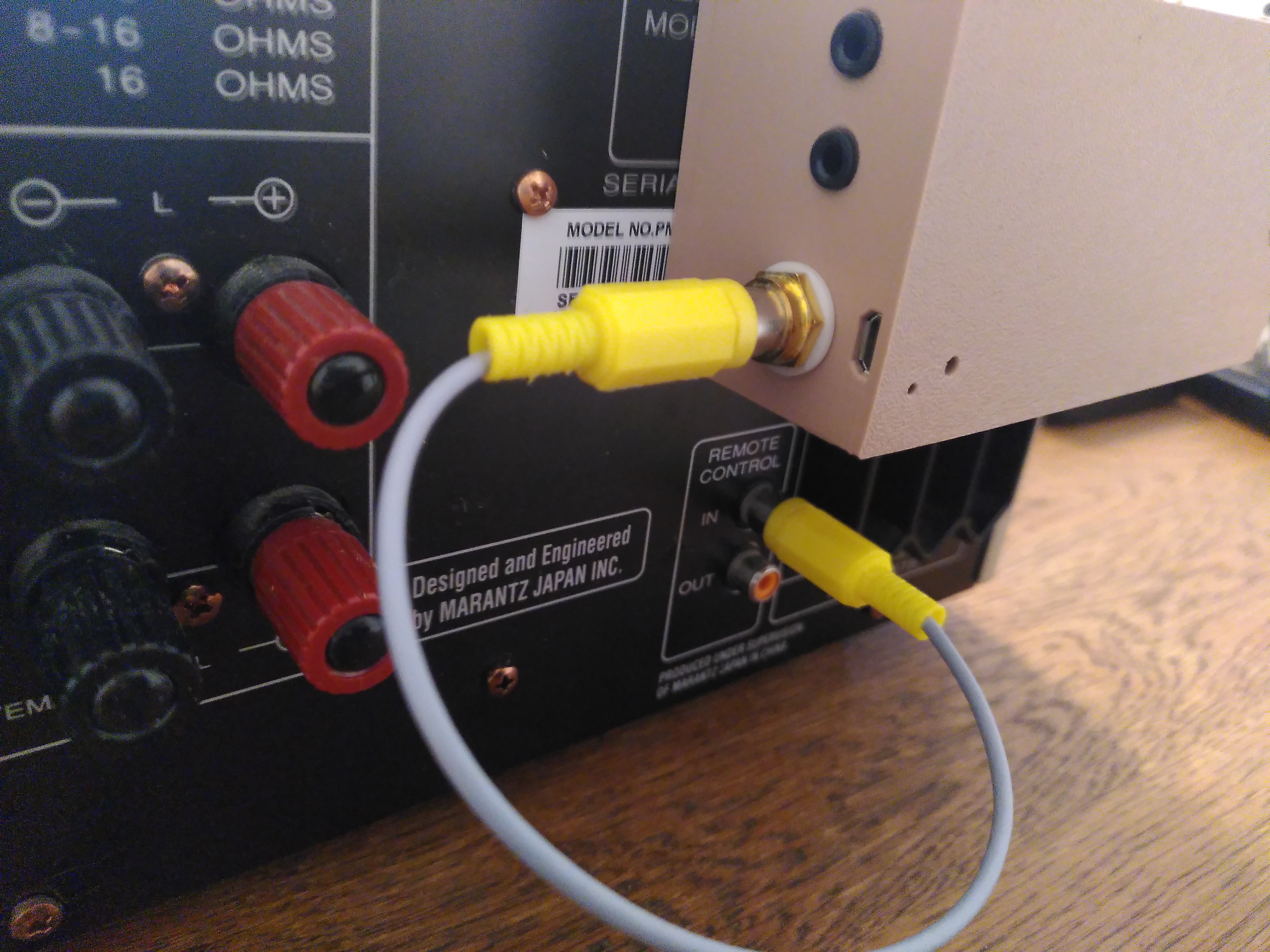
For now, the TRS jacks are note connected, but I can connect a button/dial to it at a later point. The micro USB connector of the Pico is also available for reprogramming if required, as is the switch of the Pico through a hole in the back.
Conclusion
Controlling the amplifier actually works great. I now have buttons for volume and source control in Home Assistant that send the commands over MQTT to the Pico, but any command the amp accepts is available. Furthermore, the same Pico controls power of the amp by the integrated relay, which works completely flawless so far. I really like the fact that it is all concentrated in one device now and semi-permanently attached to the amp.
Last thing: finding a place to host the KiCad, FreeCad and firmware files and share those..
Discussions
Become a Hackaday.io Member
Create an account to leave a comment. Already have an account? Log In.