Internal Assembly
Here's what it looks like (ignore the jumper - that's where a fuse might go. It currently won't allow the ATtiny85 to be reprogrammed in circuit with the battery power connected and the jumper was faster than disconnecting the JST on the rear):

Endurance
I did some testing for battery duration. It's clearly less efficient in "On" mode than I expected but that's fine - I still got around 2hrs runtime constantly. The lower than expected duration could also be due to the charging of the battery, as the current firmware allows the "Always On" mode to run while charging, so there will be a base current which may affect the cut-off point of the TP4056 charge profile.
In "Always On" mode, I set it going and left it in my car. For 2 weeks. Here it is after 14 days in temperatures between -5C and 12C:


Shrinking the Inductor
I managed to find a 2.2mH inductor that is drastically smaller than the other ones, with a reasonable resistance of 1.2 Ohms, the Bourns SRF3216 Series Type 3216 Wire-wound SMD Inductor with a Ferrite Core. They are also 20% of the cost of the larger one's I've been using. You can see it bodged onto the larger footprint here (by the JST plug):

I think this means the next revision of the board will have all components on one surface, giving more flexibility over the mounting with battery and TP4056 module.
Wireless Charging
Finally for this log, I want to admit I have finally realised that a "safe" and simple charging setup should have considered wireless charging a long time ago! I recently saw a product that implemented it well in a prototype and I looked into it more, I want to fit the coil in quite a small enclosure, so I went for this wireless charging module which is rated for 300mA (I have a module charging a 250 mAh battery, so this suits a 1C charge rate - BTW, you need to change the charge current resistor on the TP4056 module if you want to charge small LiPos at a safe 1C rate).

It doesn't charge through aluminium (unsurprisingly but I had to just check). Ignore the power supply in the background - it just draws full current and heats the charging chips, so I turned it off:

Finally, here's the proof of concept GIF showing the ability to transfer the charging current (into the motor). Note the 100 mA standing current that the charging transmitter circuit uses even when the receiver coil isn't in working proximity. The other thing to mention is that the direction of the coils appears to be significant - the ~250mA peak in the GIF rises to over 400 mA (ie the max I set the power supply to, for safety) if you flip one coil over.
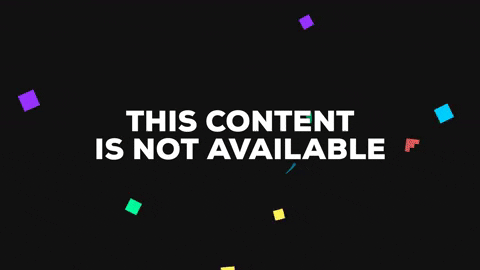
Next Up
Integrate the coil, print a replacement for the aluminium end panel, machine the button hole and LED window slot in the enclosure and perhaps mould an epoxy window in the slot. Oh, and make a charging dock...
Discussions
Become a Hackaday.io Member
Create an account to leave a comment. Already have an account? Log In.
Looking good!
I wonder if the brightness decrease you see with the PTC fuse in place would be solved with some extra capacitance across the supply (after the fuse)? I could easily see the PTC limiting the peak current, which some capacitors could fix. Maybe a few tens to a few hundred uF, depending on what currents you are actually using.
Also: what is that volt-amp-watt meter you are using?
Are you sure? yes | no
Thanks @Ted Yapo! Can you just confirm what you mean by the capacitor position? One lead at Vbat and the other lead between the fuse and the MOSFET?
My cheapo power supply is a Ruideng 50V 5A buck converter, mounted in an Alu enclosure. I feed it with a quite nice PC ATX 12v supply (that does double duty powering my 3D printer). I'm not clever enough to notice the difference between this and a proper power supply but they're so cheap and I love the ability to protect my circuits from my bad design/implementation using the current limiting feature!
Here's a link to one: https://m.banggood.com/DPS5005-50V-5A-Buck-Adjustable-DC-Constant-Voltage-Power-Supply-Module-Integrated-Voltmeter-Ammeter-p-1062473.html
Are you sure? yes | no
https://i.imgur.com/FzwZcQB.png
This way the capacitor can provide current for brief pulses, but the PTC will limit the average current drawn from the cell in case of a stuck MOSFET.
I don't know why that image didn't show up in-line.
Are you sure? yes | no
The way you have it in the other log, with the fuse in between the inductor and MOSFET will also kill your efficiency.
Are you sure? yes | no
Ahh! Great, thank you once again @Ted Yapo.
Are you sure? yes | no
Sure. For the always-on mode, maybe 10 uF would be OK. With your higher power-modes, probably a lot more. Hundreds or more uF.
Are you sure? yes | no