I measured some runout on the shaft couplers.
Discovered I had made a mistake when modeling the D shaft and corrected it.
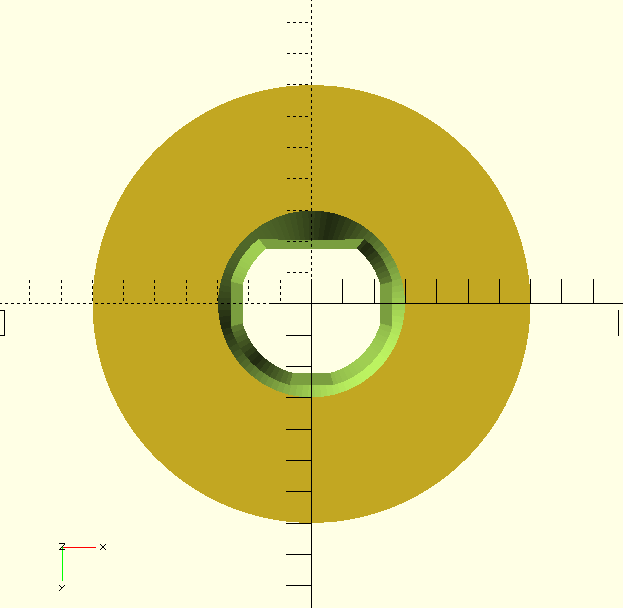
The new ones are printing.
EDIT: Nope. This made it worse. I rotated the part 180 degrees and printed again just to make sure it wasn't a calibration issue with my printer. It wasn't.
I had the same result in both ABS and nylon.
I think the part is actually distorting when I push it on the shaft due to it being a tight press fit.
The D shaft profile is "perfect" as designed with the flat removing 1/10th of the total diameter, but once I pressed onto an actual stepper, it warps the centerline towards the flat on the D (angularly, concentrically it's still basically perfect). This results in my stepper wobbling about as I rotate the shaft. I wouldn't care except that it as it does it, it also affects the line length.
I need a tight press fit here to maintain concentricity of the stepper to the spooling rod shaft, or I will need to either nix my vibration isolators or add another bearing. I've built some pretty loud printers in the past, so the vibration isolators are staying.
I tried angling the D indentation slightly to see if that compensated to no avail. I'm iterating now to see what else will correct this.
EDIT 2: Turns out my D shaft profile was fine.
To give the AL rods some better grip when I glued them into the couplers, I had knurled the end with a pair of linesman pliers and wasn't consistent enough. When I turned the AL rod around to the smooth end which normally goes into the bearing, the wobble went away.
Well at least I got a slightly refined shaft coupler out of this little exercise.
Saw this live when it came to Chicago back in the day..
Discussions
Become a Hackaday.io Member
Create an account to leave a comment. Already have an account? Log In.