Noticed that at the edges of the build area, I was getting some offset from planar on the end effector, not related to the virtual pulleys. The difference in tension between the near and far lines looked to be bending the top corner brackets. On closer inspection, they weren't bending, but instead just wobbling where they slid onto the rods.
To allow them to be removable, I needed them to be a little looser than a press fit, or you end up breaking them when you take it back apart.
So I've updated the top corners to add some more depth (18mm is now 24mm) to the pockets the support rods go into, and added the bit I've applied to other parts of adding flat spots to the inside of shaft pockets to allow for a tight, but slip fit over a greater range of error in either the rod diameter or the extrusion.
The driveway markers I have vary in diameter over a range of about 0.2mm, which is a huge 2.5% variance given their nominal OD of 7.9mm.
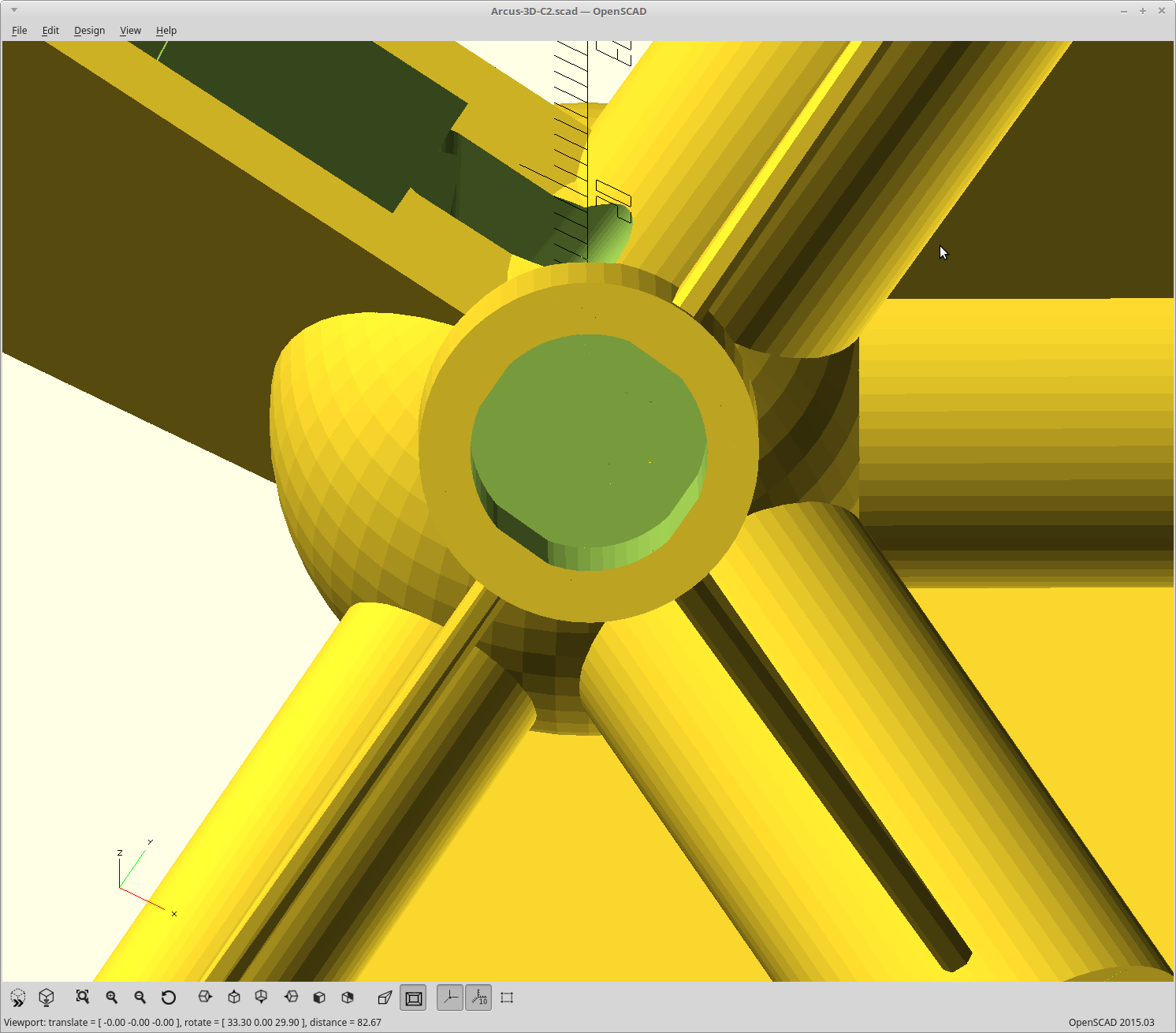
Reprinted.
Adding the flats seems to have done the trick.
Assembling using the updated parts now.
Discussions
Become a Hackaday.io Member
Create an account to leave a comment. Already have an account? Log In.