The end effector needs constant down force from the push rod to be stable. It also needs to pivot up to 30 degrees and always apply it's down force to the virtual center of the end effector. Problem is the nozzle and bowden tube also needs to go right down the center.
So it has a U joint. The hinges of the joint do not need to be super accurate as they will have very little effect on positioning. They just need to carry a constant load. To keep it simple I am using nylon filament as my hinge, but to keep my filament hinge in place it needs to be permanent. That would suck for working on the bowden fitting.
Binder clip to the rescue.
But first, making the filament hinge.
Mushroom the inner ends on a soldering iron and then put them in.
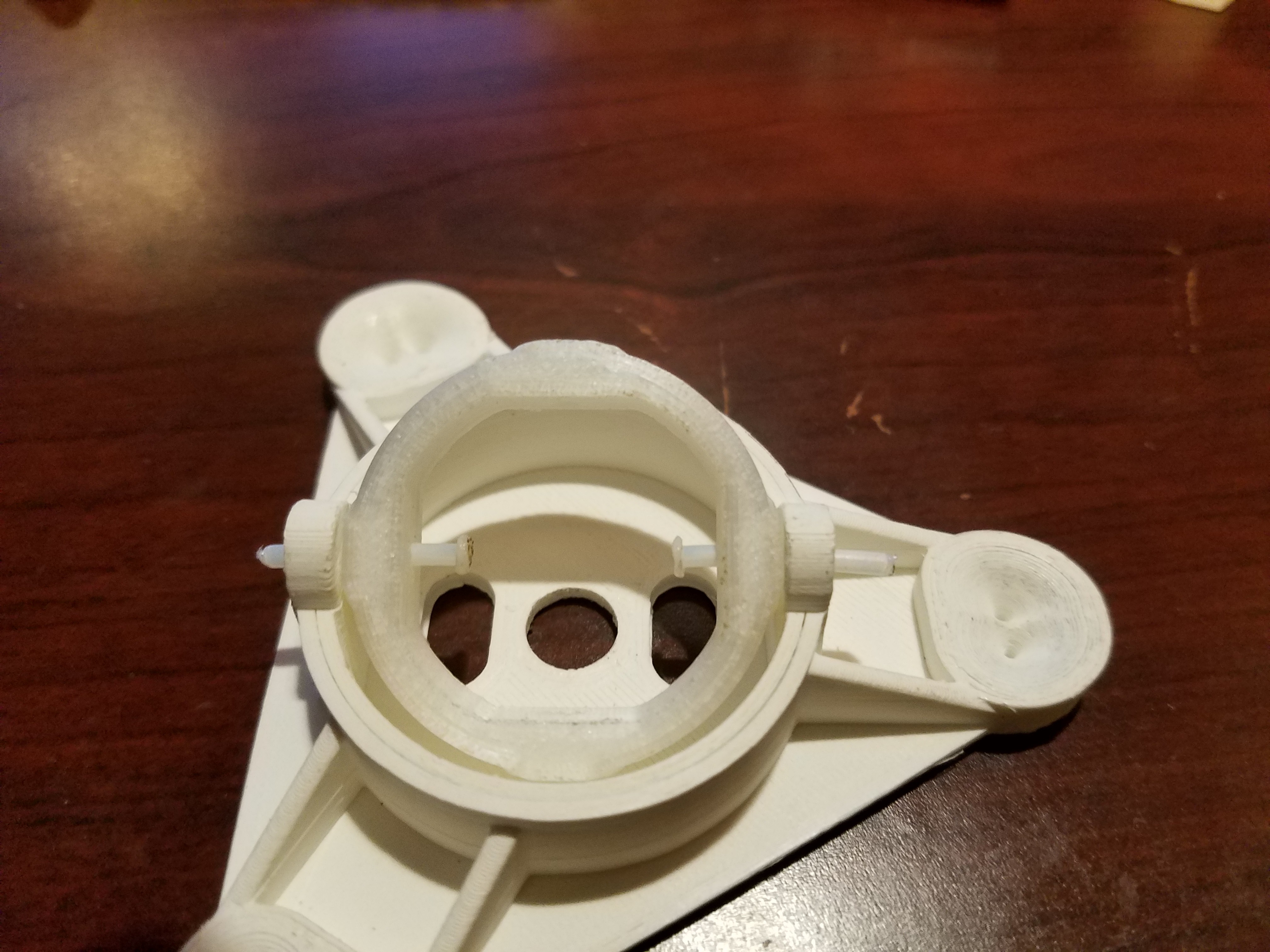
Cut to length. Leave about the diameter of the filament sticking out.
Then mushroom the outer ends. Please pardon the shaky left handed while wielding a soldering iron cameraman.
I replaced the inner U joint hinge with a binder clip spring. So now it's removable again for accessing my bowden fitting. A little excessive, but it works.
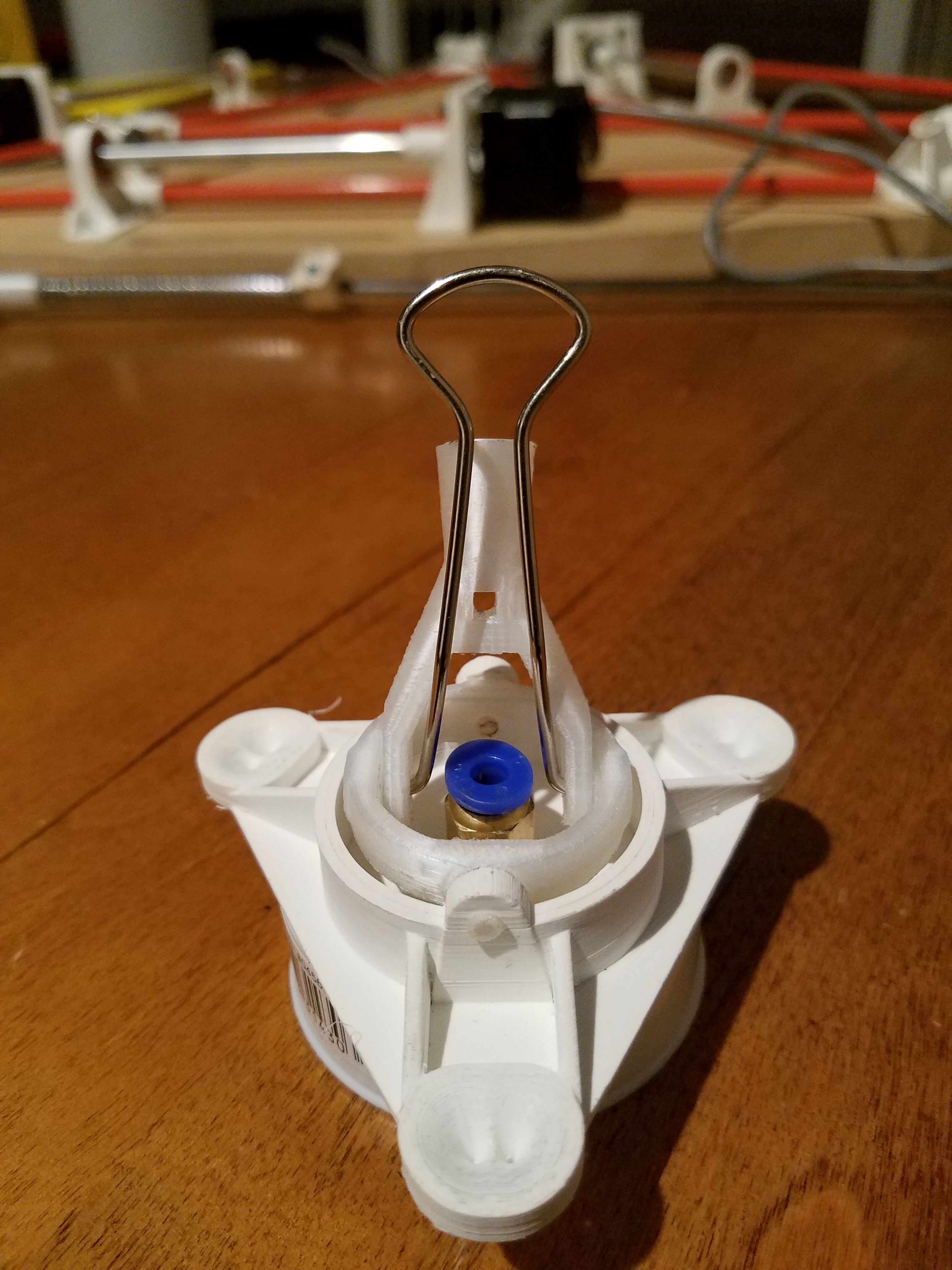
Looking good.. Now I need something that gets hot.
Discussions
Become a Hackaday.io Member
Create an account to leave a comment. Already have an account? Log In.