Pneumatic pistons are mechanical devices which use the power of compressed gas to produce a force in a reciprocating linear motion. You can see an example below:
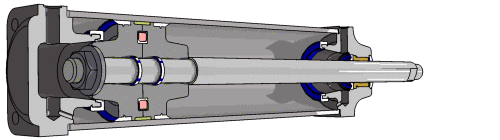
For the purpose of this project, we are only interested in the contracting effect. These were my immediate choice for the first tests. I sourced several sizes, thinking I will be able to integrate them with various body muscles. For the ankle, I opted for the CDJ2B10-100, with double acting and a 10-100mm shaft movement interval:
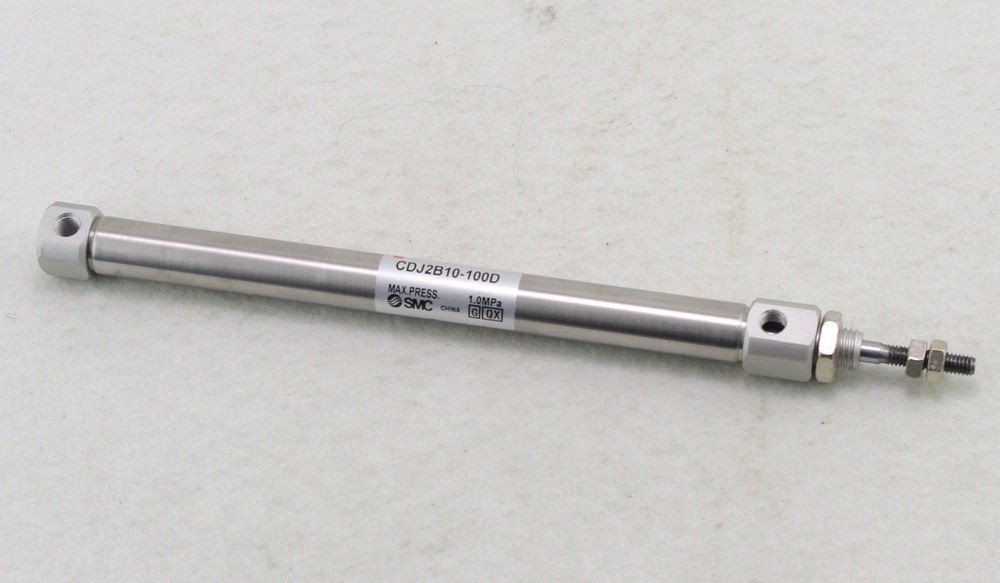
These are rated for max pressure of 1.5MPa and have a piston speed of 50-750mm/sec, making them suitable for the project's purpose.
Pneumatic artificial muscles, while lightweight and inexpensive, pose difficult control problems. To make them work I needed compressed air, pneumatic hoses and electromechanical valves, not exactly compact hardware.
I needed solenoid valves to control the air flow going into this piston. The air needs to be rushed in and out periodically, to keep paste to user's movements. The electro-valves where 12V heavy duty variants, stressing the heavy part of the word:
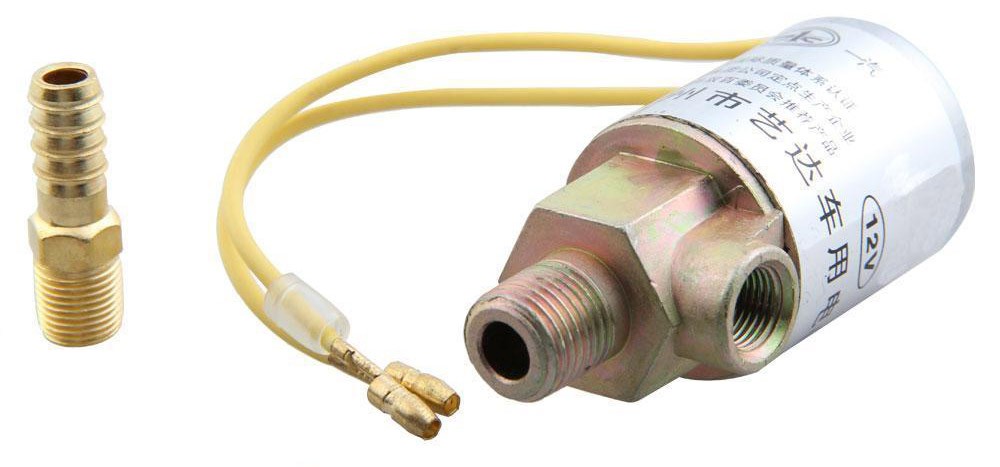
The entire system was thought of operating on 3S Lithium batteries, for about 12V of nominal voltage.
The compressed air source was a portable auto car electric air compressor, of max 300PSI used to inflate tires:
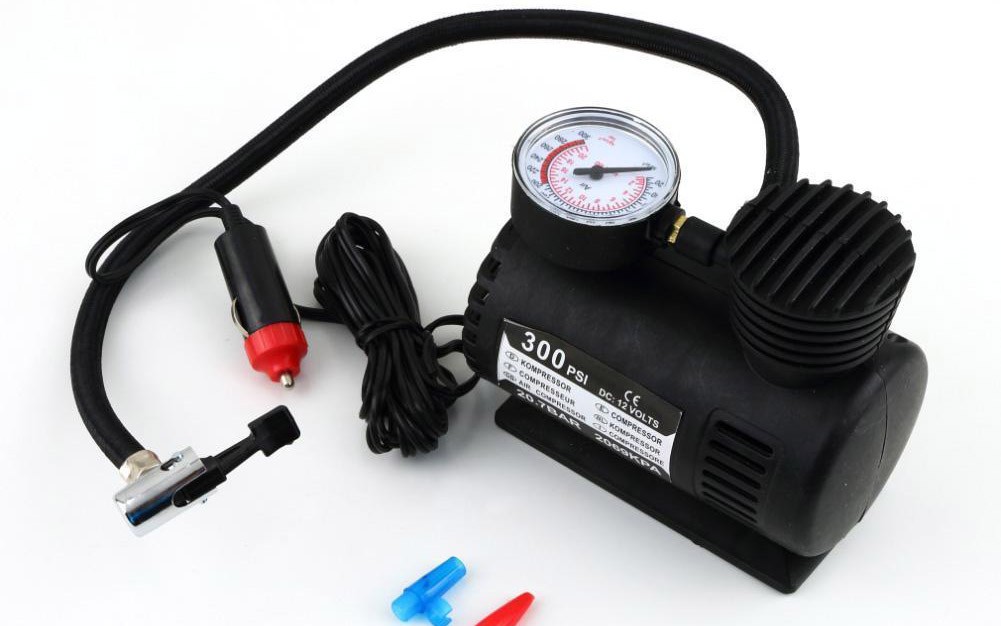
And finally, besides the various connectors and accessories, the pneumatic hose used:
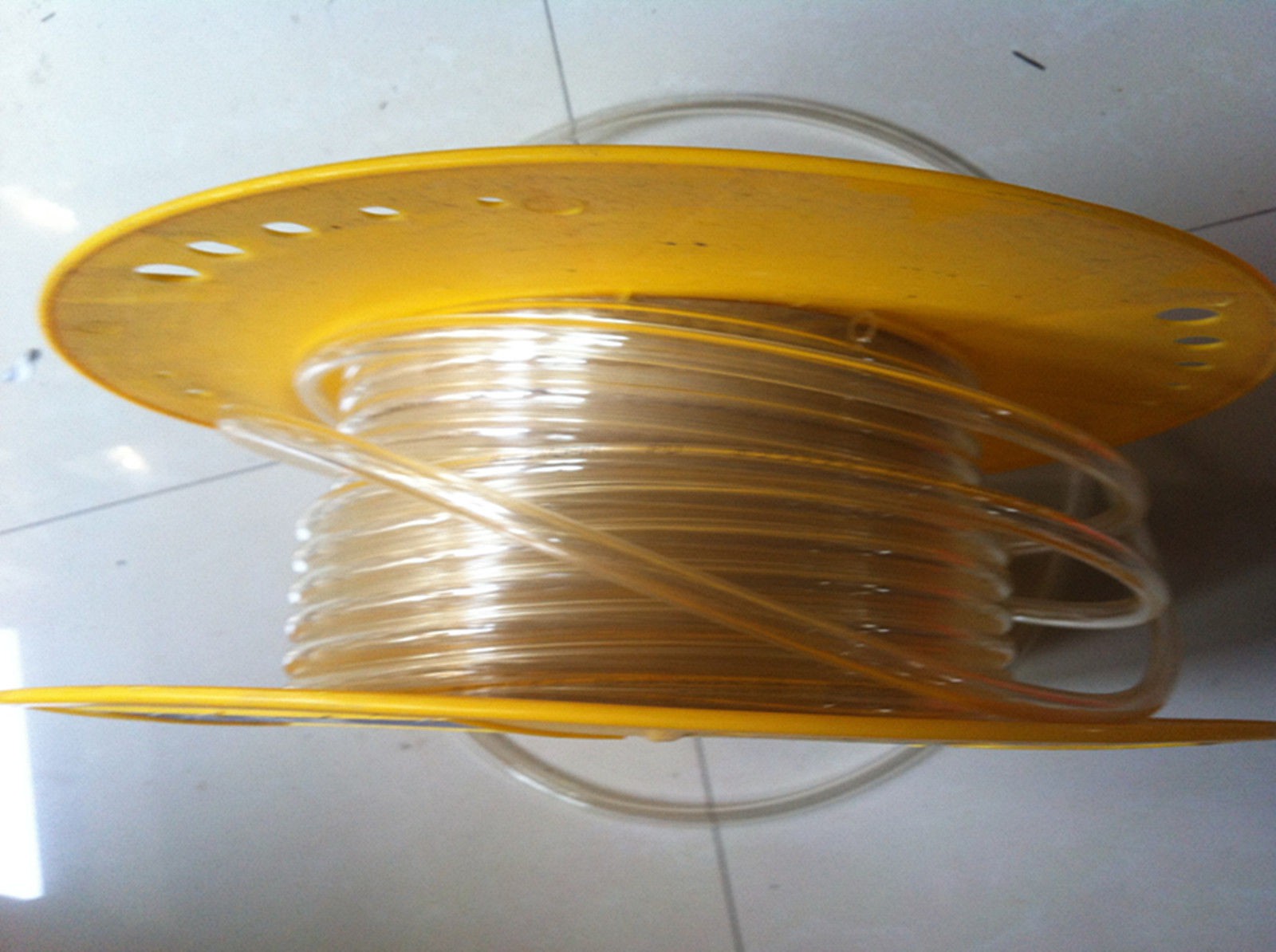
The first tests
All I had to do was to power the air compressor using a 3S battery, and connect it to the pneumatic piston. The results where good, and it appeared promising.
Load tests
I need about 10kgf per leg and considering the running speed, a piston operational frequency of at least 1Hz. So what I did was to put about 2L of water (2kg) in a plastic container, and hook it up to the piston to test the contracting movement:
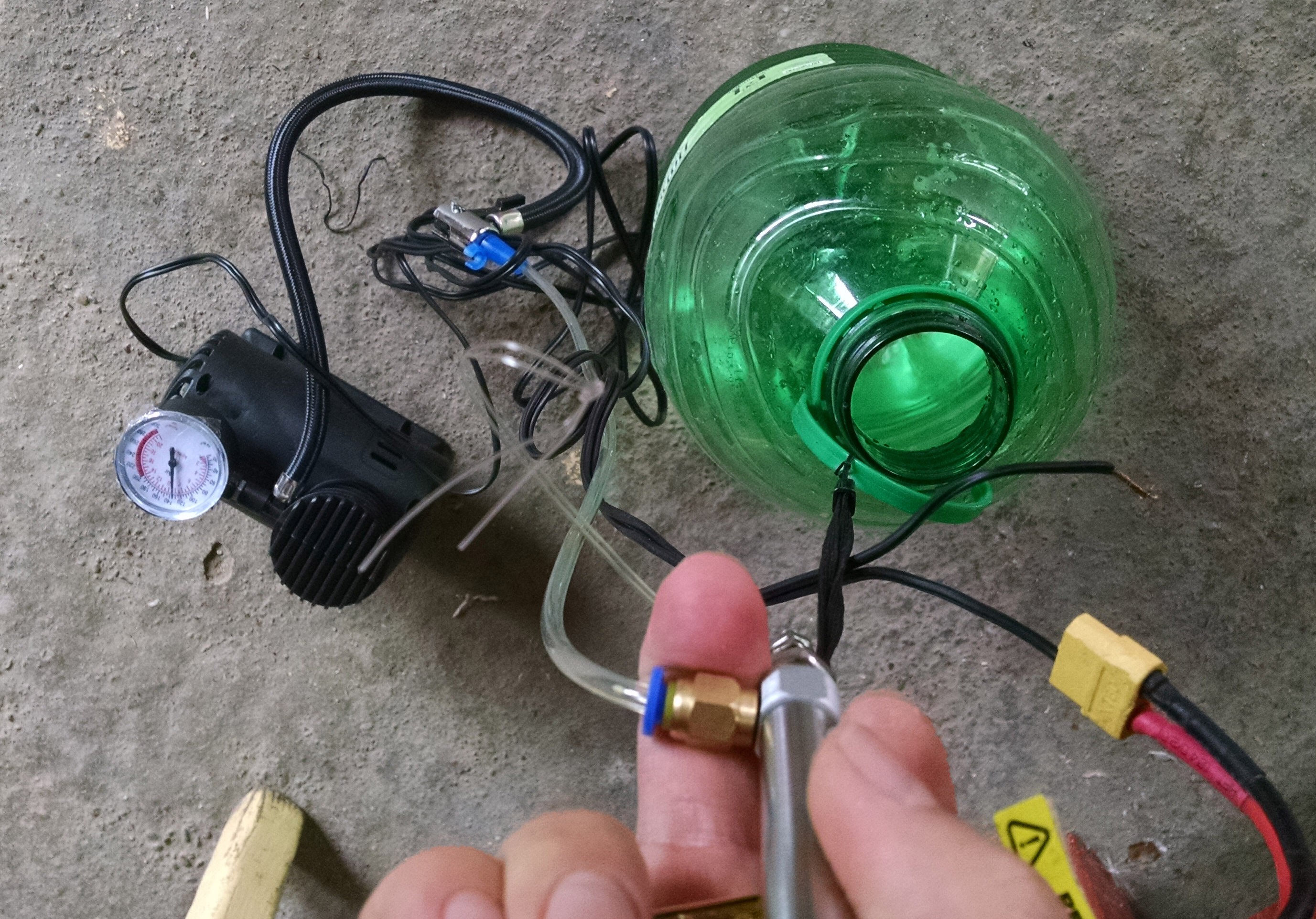
Results? The setup failed to raise the load which remained stuck at ground level.
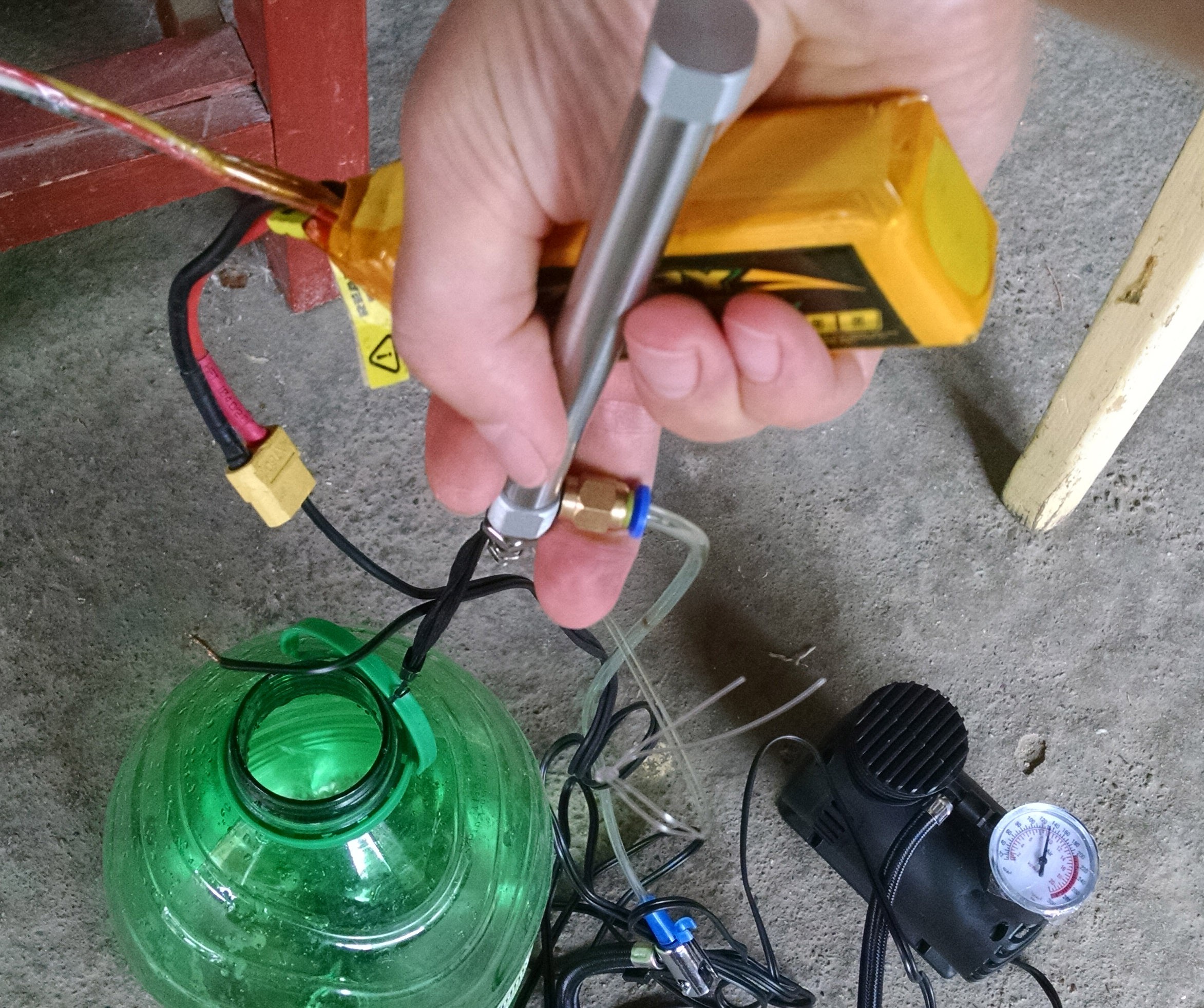
Conclusion
While this approach certainly has the potential, I didn't use the right components, proper pistons and a proper compressed air source. To simplify the design, it is possible to use a container with compressed air and drop the electric air compressor. Nevertheless, bigger pistons and higher pressure is needed to achieve the desired results. I decided to look for alternatives (available in my toolbox)
Discussions
Become a Hackaday.io Member
Create an account to leave a comment. Already have an account? Log In.