This is another one of those old projects I never documented. Back around 2001, I was looking for a small red flashlight for astronomy, but hated dealing with dead batteries. It didn't need to be very bright, so a single ultrabright LED would do. I finally stumbled upon the idea of using an old servo as a generator. I threw the thing together in a half-hour, and it's lasted 17 years so far. The gears are a little worse for wear, but it still works.
Here's the schematic:
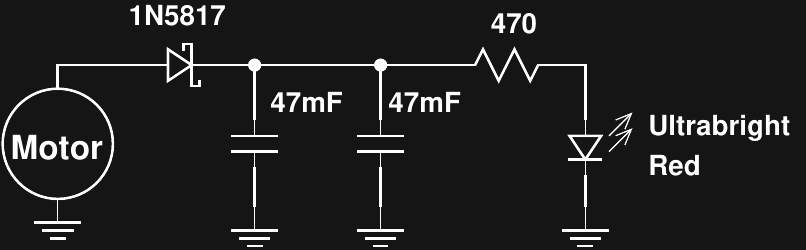
It doesn't get much simpler than this. A Schottky diode protects the capacitors from discharging back into the motor (and from reverse polarity if you turn the horn the wrong way). A pair of 47mF/5.5V capacitors store the energy from the motor-turned-generator, while the 470-ohm resistor limits the current to the LED and stretches out the run time.
I removed the servo brains, and replaced them with the above circuit. I left the two ceramic noise-suppression capacitors that were soldered to the motor, but they don't really do anything for the flashlight. If you build one, you will need to modify the servo for continuous rotation. In some cases, this is as simple as removing the feedback potentiometer; for other servos, you may need to modify a gear slightly. You'll figure it out.
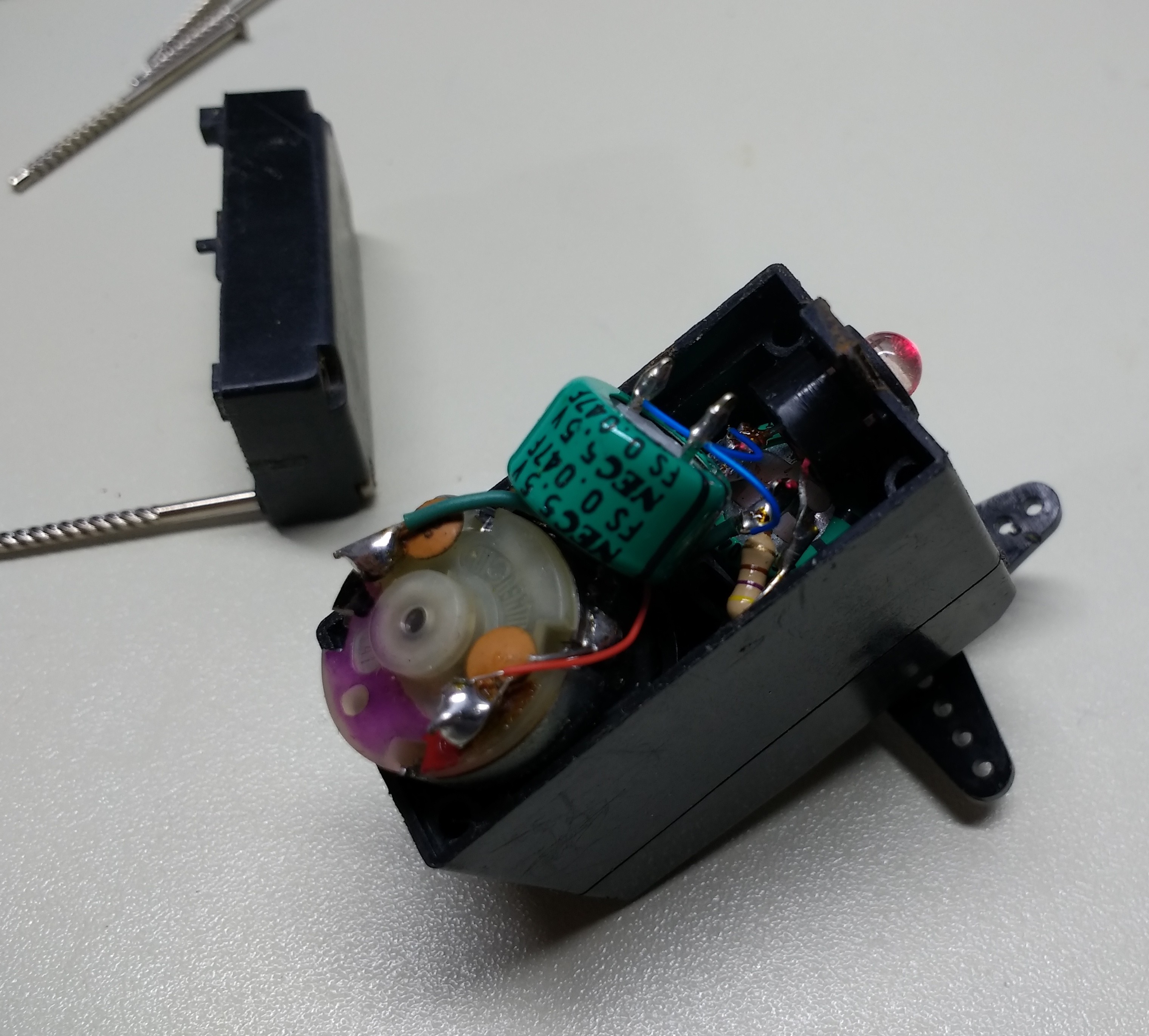
That's it. Very simple and reliable. It only takes a few cranks to get the LED going, and it will run for a few minutes, slowly growing dimmer. As a general-purpose flashlight, it's not that impressive, but it's perfect for preserving night vision.
I'm planning an update, using a modern LED, boost regulator, and 3D printed crank (turning the servo horn is tough on the fingers). I'll document it in the build logs as I go.
Heh, sweet gearbox too. Well spotted, love it dude. :-D