The acetone softened the coating enough to allow it to be removed. I got about half way done before I realized I needed to be a bit more gentle with the bare silver though and ruined more than half of it.
Everything was looking good, until I held the resulting mirror up to the light and could see through it everywhere I had scratched. The silver coating was very, very thin. Just rubbing too hard would take it off.
So I ended up with one probably usable front surface mirror about 36mmx33mm and a good idea of how to do better next time.
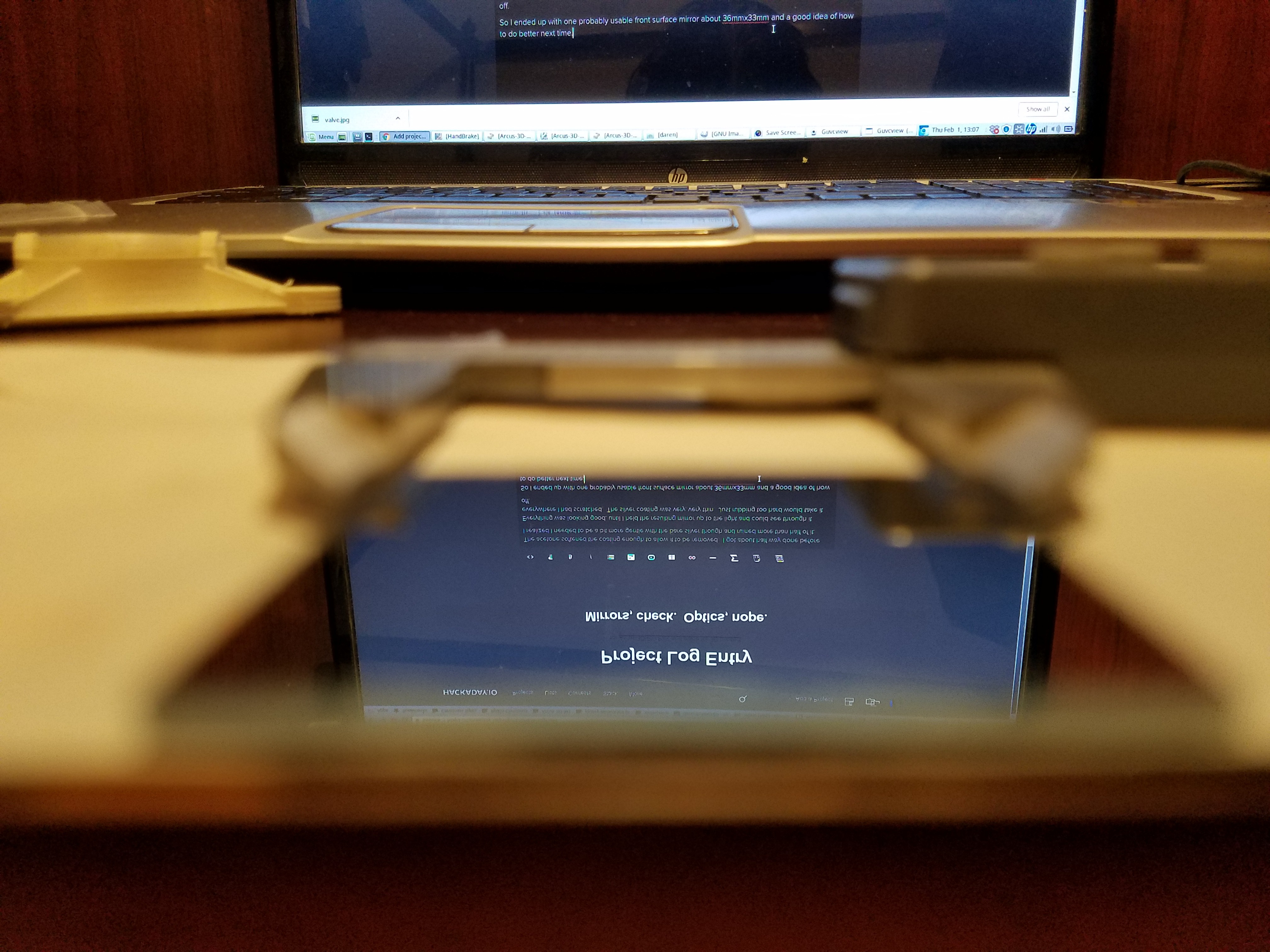
Next was to assemble a mockup of my optics to see how it worked. It doesn't.
The FOV of my endoscope camera was 67 degrees. That was far too large of a beam, so the plan was to reduce that to 33.5 degrees with a 2:1 telephoto cell phone camera lens placed in the beam path directly after the first bounce. This didn't work as I had hoped.
- The 2:1 telephoto lens was actually about 1.8:1.
- The telephoto lens had to be right on the endoscope or it pin-cushioned terribly.
- Putting it right on the endoscope meant I had to put it before the first mirror bounce. This increased the beam size dramatically, which then increased the mirror sizes required.
- The latter means my beam path now intersects with the side of the part being viewed.
- The minimum fixed focus distance when using the lens was increased to ~65mm.
None of these issues are show stoppers, but they all add up to larger and heavier mirrors located farther away will be needed. I was already near the limit of what I was willing to ask a 9g servo to do reliably.
If it starts to take longer than ~0.25 seconds to deploy and retract the mirrors, I might as well scrap this part of the plan and move to a dedicated up-looking camera. At that point I can move the entire head/part being viewed to a stationary camera faster. Simpler too..
Discussions
Become a Hackaday.io Member
Create an account to leave a comment. Already have an account? Log In.