After my version-3 Charge Controller became popular on web,I received mails and comments with request for making a higher rating Controller. So we are designing our Version-4 Charge Controller which is more advanced, greater capacity and useful more potential applications.When the project complete, it should be useful for off grid electricity users, control of autonomous street lights and signs, and many other applications that need medium power levels and efficient reliable operation
I would like to give special thanks to Keth Hungerford , Petar, aplavins and Chinmay who are the new members to my project and actively contributing to it. Keith is playing the key role for designing this new version Charge controller.
For the time being we are planning to see the following changes in existing version charge controller.
Changes at the moment are:
- Increase panel voltage rating to allow for panels with 60 cells (i.e up to 40 V, so-called "grid connect" panels);
- Higher current rating, at least 20 amps and preferably 40 amps;
- Metering current on the battery and load;
- Improve design robustness to ensure external conditions do not cause any failures;
- Design that allows multiple controllers to feed into a power distribution switchboard;
- Optimal battery management for several different battery types, such as Lead Acid (several variants), NiFe, LiFePO;
- Ability to control more than one load output – either to allow for greater capacity, or timing control of when the output is on or off.
- Real time clock with date to enable time stamping of statistics and timer control of loads.
- Operational configuration capability (buttons or via WiFi?);
- Greater data collection to get illumination statistics, battery performance statistics, load statistics.
- Higher battery voltage (to 24 or 48 V) and associated higher solar panel voltages;
- Much higher panel voltage (to 150 V or so)
- Multiple Load outputs regulated to close to 12 V
- Panel safety and overload disconnect
In addition there are some "internal" matters that are worthy of investigation:
- Focus on maximising efficiency
- Fail-safe software or self-recovery features
- MPPT algorithm refinements
- will it all fit in Arduino Nano? or selecting another Arduino Board ?
You can find all the ongoing activities here
I request to all of my followers,team members and viewers to give suggestions on it.
You can write your suggestions/feedback in the comment section below.
Discussions
Become a Hackaday.io Member
Create an account to leave a comment. Already have an account? Log In.
Thanks for sharing this great content online for best franchise in India visit
<a href="https://www.al-baik.com/">albaik franchise</a> www.al-baik.com
Are you sure? yes | no
Thanks for sharing this great content online for best franchise in India visit
<a href="https://www.al-baik.com/">albaik franchise</a> https://www.al-baik.com/
Are you sure? yes | no
Thank you for looking up technologies on <a href="https://takeoffprojects.com/">embedded systems projects</a>
Are you sure? yes | no
Hey folks. I'm back. So many things had to be done. But i tried to build prototype, using v3 tutorial from instructables.com. But when i finished part with ir2104 driver and mosfets i noticed , that PWM signal from Arduino UNO v3(i used this board) don't have common ground with driver. So how it works? i tried to find explanation, but failed? Sorry if this question is has very obvious answer, but i stuck in this point. I tried to power Arduino with Vin from solar panel and in this case i had common ground, but in this case ir2104 have always closed HO and always opened LO. Maybe you have similar situation?
Are you sure? yes | no
I have now put the latest design analysis spreadsheet on my Google docs folder. If anyone wants to look at it, please send me your email address (by email) and I will add you to get access to this folder. This spreadsheet contains all the formulas for calculating inductance, core loss, etc.
Are you sure? yes | no
Pls, me mixa.dior@gmail.com
Are you sure? yes | no
I have added you. Please check and let me know if you have any problem. The main thing you will want is MPPTC design v1.6.xls
Are you sure? yes | no
pls, me hoangvanngoc2158@gmail.com
Are you sure? yes | no
I have added you. Keith
Are you sure? yes | no
Hi, great work, can you share with me the files? i want build a mppt regulator for my system. 40amp 12v required.
thanks
Carlos_mgv@hotmail.com
Are you sure? yes | no
Hi Carlos,
I have looked some more at the TI design you suggested (http://www.ti.com/tool/TIDA-00120). I have not studied it thoroughly, but found it interesting.
I think the interleaved design (two parallel converters) is a good way to relieve stress on key components, especially the IN side capacitors (C1, C2).
Note that most of the components are surface mounted, which may be a challenge for the home or hobby constructor.
I am a bit dubious about the assertion that current capacity can be increased to 40A by using TO220 MOSFETs. I think some other components may also need to be upgraded, in particular C1, C2 may need to be doubled. I have not checked my spreadsheets (you can easily do that) but I think at 20A that these capacitors are already at the limit of their AC ratings.
Note that the testing with a 12V battery was using an electronic load to simulate the battery, and a panel voltage of 15 to 22V DC, also simulated I believe. These test conditions may not fully expose all of the potential problems with the design, in particular possible start-up problems with reverse current flow from the battery.
In the design we were working towards (not yet complete) we used several MOSFETs in parallel to reduce the ON resistance (to improve efficiency) and also several capacitors in parallel to reduce the ESR and also increase the AC capability. You can find manufacturer data on ESR and AC capacity on the internet (eg http://pdf1.alldatasheet.com/datasheet-pdf/view/514810/NICHICON/UHE1H102MHD3.html). Although ESR reduces and AC (ripple) rating increases with increasing capacitance, it is not always linear. In some cases there are benefits in having several smaller components. When I was doing the design last year I had trouble finding the manufacturer data, and may not have chosen the optimum combination.
If you want to use the converter with a higher panel voltage (eg 30V panel with 12 V battery) the ripple current in the input capacitor(s) (ie C1, C2 in the TI design) increases further (see my spreadsheets for numbers). To get to a 40A design, I was thinking I needed to go to a quadruple interleaving design.
Another comment on the TI design (which I have not verified) is that I think it does not have explicity support for DCM (discontinuous current mode) which is the reason the efficiency collapses very badly at low current levels. In the Arduino I used the more sophisticated timing capability of Timer 1 to support DCM and achieve good efficiency even at low current levels. I don't know if the TI MCU has the equivalent function (I may well do, I have not checked, but if there it seems not to be used in this design).
I hope this helps your research and decision making. Keith
Are you sure? yes | no
Thanks keith, i couldn´t open the pcb or schematic files of tida-00120, i´m still trying- I´ve asked for some free sample components to TI, and i´m planing to try with 2 of this controllers (one for each of my 250W panels) and then try with a modified one, with 60V to220 mosfet and i think i have to change the inductor too, what do you say?
regards
Are you sure? yes | no
I have been calculating the efficiency of the design in order to make sure the components are a) sufficient and b) not overspecified (because that may make them not cost effective). I have also been working on the PWM hardware/software subject (more on that later).
I think I am very close to having some good answers.
Ihave completed the spreadsheet model of the converter efficiency. You may have seen the earlier version(s). I am now reasonably happy with it. It calculates inductor losses of 3 sorts (DC resistance, AC resistance, and core loss). It also calculates Resistive, Capacitive and Switching losses for the 3 transistor positions Q1 to Q3. It also calculates resistive losses in the two capacitors C1 and C2 (due to ESR). It deals with power loss at the solar panels due to voltage ripple (which moves the instantaneous operating point away from Maximum Power, even if the mean point is the maximum); and deals with excessive ripple into the Battery by assuming the Battery has a high resistance to AC current.
The big challenges have been (first) getting the core losses calculated; and (second) dealing with Discontinuous Current Mode (DCM). I think I have done them correctly now, but will be very happy for some review and comments when I publish them.
Having got that model, which calculates each sort of loss and adds them up, I then wrote a macro (in LibreOffice Basic) which goes through a list of conditions and generates data and summary tables. The conditions can be adjusted by typing values into the Charts sheet, and then running the macro. I have been going through all of the Vp and Vb and power level combinations I put in the original Requirements document (there are 42 of them), and tabulating the efficiency for each combination as a function of PWM period/frequency. The results are quite interesting. Some of the losses go up with increasing frequency, some go down. There is usually an easy to find minimum in a U shaped curve, with an optimum PWM frequency which gives minimum losses.
DCM takes over at low power levels, typically around 4% of full load. We will need to make joint decision about whether to
cater for this condition, or simply sacrifice a certain amount of power. It is basically a matter of software development. I don't think is is
all that hard.
I will now summarise the components of the design, and the efficiency performance data.
Inductor: Uses a powdered iron toroid type T225A-26. This has an outside diameter of 57mm, an inside diameter of 38 mm and a thickness of 25.4 mm. The winding uses 4 strands of AWG number 12 enamelled wire (about 2 mm diameter and 3.3 mm^2 area) wound evenly around the toroid to make 22 turns. According to my calculations it fits with some margin. This yields an inductor with an inductance of 77 Microhenries and a DC resistance of 2.6 milli ohms.
Switching MOSFETs: Two types are used, both in TO220 through-hole packages. We need 12 of type PSMN3R3-80PS which are used 4 in parallel in each of the transistor positions Q1, Q3 and Q4. We need 12 of type FDP150N10A all of which are used in parallel in position Q2. The PSMN3R3-80PS has a very low RdsON resistance, but a rather sluggish switching time which makes it unsuitable in the Q2 position. The FDP150N10A has a good fast switching time, but a somewhat higher RdsON resistance, therefore we need more of them in parallel. Both MOSFET types are available at reasonable prices, if you hunt around on the internet.
Capacitors. We need capacitors with a low ESR (Equivalent Series Resistance). I have specified C1 as 800 microfarads and ESR of 5 milli Ohms, and C2 as 400 microfarads and ESR of 10 milli ohms. I am a bit concerned that we may have trouble finding suitable components that have a low enough ESR. We may have to sacrifice some efficiency if we cannot find capacitors with a low enough ESR. This is an area for continuing research.
Here are the results of my analysis of the converter efficiency for all the applicable Panel and Battery voltage combinations, and for a realistic set of illumination (power) levels.
Tabulation T225A-26 PSMN3R3-80PS FDP150N10A
Panel voltage 18 30 60 30 60 60
Battery voltage 12.5 12.5 12.5 25 25 50
Load current
% Amps Efficiency Eff Eff Efficiency Efficiency Efficiency
1% .4 95.21% 91.56% 88.93% 97.40% 91.67% 97.61%
5% 2 98.04% 96.72% 95.65% 98.92% 97.07% 99.02%
10% 4 98.85% 98.11% 97.41% 99.37% 98.23% 99.41%
20% 8 99.16% 98.74% 98.23% 99.54% 98.81% 99.59%
50% 20 99.01% 98.80% 98.51% 99.47% 99.03% 99.62%
80% 32 98.66% 98.54% 98.38% 99.31% 98.97% 99.55%
100% 40 98.40% 98.32% 98.22% 99.18% 98.89% 99.50%
Overall efficiency average 97.94%
My original (rather arbitrary) target was to achieve at least 96% efficiency in all modes of operation.
It is clear that this is very difficult to achieve at low illumination levels. However at least the average across all conditions is nearly 98% and it is only at the 1% power level that the target is consistently not met. Remember these figures do not include any provision for overheads, such as running the Arduino itself, or WiFi and LCD modules.
These efficiency values are based on using Arduino Timer1 to generate 2 synchronised PWM signals, one for the IN pin of the IR2104 MOSFET driver, and the other for the SD pin of the same driver. When in Continuous Current Mode (CCM), only the IN pin is driven with a PWM signal, but in Discontinuous Current Mode (DCM) both pins have a PWM signal, the SD pin having the longer duration.
Furthermore, the above efficiency values are based on achieving the optimum switching period/frequency for the PWM. This varies with voltage configuration and power levels. An adaptive algorithm is required.
I think the best approach to this is to base the PWM parameters on the Output power level (ie not the input power level as used in V3) and adaptively adjust both period and duty cycle(s) to maximise the output power. This is my current thought anyway.
The calculated optimum switching period for maximum efficiency ranges from 7 microseconds to 135 microseconds (compared to a fixed value of 20 microseconds for the V3 controller).
I will be posting the full spreadsheet analysis, and some descriptive material, on the Google Drive area dedicated to this project.
Please let me know what you think of the above, and make any suggestions.
Keith
Are you sure? yes | no
Hello all. I'm also interested in building cheap mppt controller. I have learned previous MPPT 3.0 project and Keith's thoughts about 4.0, my knowledge are still poor, but i saw one thing - inductor it was chosen without deep research. 40 amps of current will produce huge magnetizing force that according to this curve http://micrometals.com/images/curves/26pctpermDCmagforce.html will reduce permiability, so inductance will be lower, so you need to compensate this with turns of wire, as i know copper have resistance so it will provide heat which will also lowering effectivity of iron powder core and push to its degradation. There are some recomendations to turns amount, wire diameter and core size - http://micrometals.com/images/curves/DCInductorExTable.html , but only up to 30 amps. Also there is software tool - http://micrometals.com/software_index.html which can help to calculate inductor core size and material (26/52/8/52B... etc) .
Thanks for you project. If there is any way how i can help you with this project implementation don't hesitate to ask.
Are you sure? yes | no
Hi Mykhail, Thank you for your posting which I have just seen.
Please have a look at my report, just written today.
Would it be possible for you to do some analysis using the references you have given, to show us the actual inductance we will achieve with the selected toroid and winding, for various current levels?
If you need help with more details I may be able to provide them. Keith
Are you sure? yes | no
Hi Mykhail, I have now looked at the web sites you listed and downloaded and run the software. I think Micrometals have provided a lot of useful information. I used other parts of their information in the original design work.
Let me go through the design steps I followed, so that if you (or anyone else) thinks we need to make changes you can assess it.
I first tried a smaller core, larger than the one used in the V3 design. It was a T106-26. However I found that when I calculated the DC resistive loss, the AC resistive loss (which is higher due to skin effect) and the core loss, it was over the permissible power dissipation in the core. So I decided to go for a significantly larger core.
I found that a larger core, T225A-26, is readily availabe on EBay. It has outside diameter of 57.15 mm, inside diameter of 37.7 mm and a thickness of 25,4 mm. The material (No. 26) is one of the iron powder types that is recommended for use in this type of application. Its power dissipation ratings are 6.8 Watts for a 25 C temperature rise, and 11.9 Watts for a 40 C temperature rise. The data sheet shows this core to yield 1600 microhenries per 100 turns.
I next calculated the minimum inductance I needed for a reasonable ripple current in 40 Amps at a 50 kHz switching frequency. The result was 20 micro Henries (it turns out this number was not so important, but it provided a starting point). This requiired 12 turns of wire. Since we need a low resistance in the magnet wire, but it should not be so thick as to be hard to wind onto the toroid, I decided to look at a composite wire made up of several strands, which will make it more flexible and easy to construct the winding. With 4 strands of AWG number 12 wire, I could actually get 22 turns onto this toroid, and the DC resistance was just 2.6 milli Ohms, which is low enough to still keep the power loss from 40 Amps well within the dissipation limit. 40 Amps times 2.6 milli Ohms is 4.2 Watts. With 22 turns that gives us 77 micro Henries, rather than the minimum of 20.
Having a higher inductance (22 turns comared to the minimum of 12 turns) is good for other aspects of performance, since it lowers the ripple current and allows a longer PWM period which will reduce MOSFET and capacitor losses.
I then calculated the AC resistance due to skin effect and put the relevant equations into my spreadsheet model. It turns out that the ripple current is not high enough to cause significant extra heating due to skin effect.
Next I calculated the magnetic flux, and the associated core losses based on charts from the Micrometals web site. This was the most difficult part of the process. The heating, and losses from the magnetic flux variation, arising from the ripple current, are significant. For example, the worst case is when the DC current is 40 Amps and (assuming 77 micro Henries) an AC current of 0.65 Amps RMS (2.25 Amps peak to peak).
From this I calculated the flux density in the core as 153 Gauss and the core loss as 37 milli Watts per cubic cm. With the core volume of 37 cm^3 this gives a core loss power of 1.38 Watts.
When added to the DC resistive loss of 4.2 Watts, and an AC resistive loss of 0.05 Watts, the core loss takes us to 5.6 Watts, which is less than the limit for a 25 C temperature rise. So I reckon this is OK.
What I did not consider was that the DC current of 40 Amps will reduce the permeability of the core.
A new calculation give the DC magnetising force in our 22 turn inductor as 80 Oersteds (H=0.4 pi N I / magnetic path length). According to the first link you provided, this means the permeability will be reduced by 50%. Thus our actual inductance will be more like 38.5 micro Henries, and the ripple current will be 1.3 Amps RMS (4.5 Amps peak to peak). The AC resistive loss (from skin effect) goes up to 0.018 Watts. The core loss (1.38 Watts) does not change because it is a function of the voltage across the core, not the current through it. So our total loss is now 5.6 Watts, which is effectively unchanged from the original calculation and still acceptable.
As you said in your post, the DC inductor design example sheet is not very useful because it stops at 30 Amps, and we are running 40 Amps. Also all the examples are using higher inductances with more turns of thinner wire than we need.
I loaded the inductor design software tool from the link you provided. I can run it on my computer without any problems. When I put in Inductance 38.5 microHenries, I=40 Amps, Vp=60V, Vb=12.5V, Frequency 50 kHz and "Full window" I get a list of possibilities, including a T225-52B core which is very similar the T225A-26 core I have been working with. The loss and temperature rise figures are all similar to the ones I have derived.
The most interesting thing here was the price given of $1.34, which is much lower than the prices I have been able to find on Ebay.
Given all of these results, I feel reasonably happy with the selection and recommendation I have made.
Any further comments please?
Keith
Are you sure? yes | no
Hi, Keith. Perfect analysis, nothing to add more. But i have several questions.
1. How did you calculated minimum inductance? Why so low value?
2. you calculated for CCM or DCM?
3. Yep, T225A-26 and T225-52B have very similar parameters, as i know 52 material was developed to replace 26 (most often used) and have lower losses on frequiencies higher than 500kHz.
4. Currently i'm trying to understand CCM and DCM basics and also pros and cons. Can you suggest any articles or books about this, if its not difficult for you?
P.S.
I stay tuned and read all the thoughts every day and if i have any new info or research that i can provide i'll post it. I'm pleased, that links i have provided has some value for this project.
Are you sure? yes | no
Hi Mykhail, thank you for the kind words about my analysis.
As I said, the calculated minimum inductance is not so important in the final analysis. It just gives us a place to start, so that we are looking in the right zone. The curious thing is that as the current in the converter rises, the inductance required gets smaller. That is assuming the same percentage ripple current. Using our FETs in Q2 and Q3 positions, we alternate between increasing the inductor current (Q2 on) and reducing it (Q3 on). The load end capacitor C2 evens out the current flow to the battery and load. The lower the ripple current, the less stress on C2. When Debasish did his V3 design, he assumed a ripple current limit of 35% at full load. I used a similar criterion. The absolute value of the ripple current stays the same as the current reduces, until eventually the ripple current becomes larger than the average current and for part of the cycle current flows the "wrong way" through the inductor.
"CCM":, or Continuous Current Mode, is when the current flows in the same direction through the inductor. Synchronous and Asynchronous buck converters behave the same way in CCM.
"DCM", or Discontinuous Current Mode, is when the ripple current peak exceeds the average current in an Asynchronous buck converter.
In an Asynchronous buck converter, there is a diode, not a MosFet, in the Q3 position. That diode prevents any current from flowing backwards through the inductor. Therefore, if the switching period is long enough for the current to drop to zero, the current then just stays at zero until Q2 comes on and starts the inductor current flowing again in the "forward" direction.
In a Synchronous buck converter, there is a MosFet in the Q3 position. It behaves as a low value resistor when it is turned on, and will allow current to flow in either direction. In the nominal regime, the duty cycle of the PWM is the ratio of the battery voltage to the Panel voltage. For example, with a 30 volt panel and a 12.5 volt battery, the PWM duty cycle should be 41.666 percent. We make relatively small adjustments to this ratio to find the maximum power point of the panel, and to match the best charging voltage of the battery.
If our switching period is fixed, and our PWM duty cycle is (almost) fixed, then when the power from the panel is low (eg a cloudy day) then there will be current flowing in alternating directions in the inductor, supplied at both ends by the charge in the two capacitors C1 (at the panel end) and C2 (at the battery end). This results in greater losses than would occur in an Asynchronous buck converter.
The existence of DCM, or alternatively of reverse current flow, is inevitable at some load level. There is always some load level below which either DCM, or reverse current flow, will occur. The load level at which this starts can be reduced by shortening the PWM period, or by increasing the size of the inductor.
I aim to get the best of both worlds in our V4 design - that is, the benefit of a low impedance Q3 when in CCM, and a transition to DCM when required by a low current level. We can do this by running two synchronised but different PWM cycles for the IN and SD pins of the mosfet driver IR2104.
The documents I used when learning this stuff include:
A Texas Instruments Application Report called "Understanding Buck Power Stages in Switchmode power supplies"
Another TI report called "Efficiency of synchronous versus nonsynchronous buck converters" by Rich Nowakowski and Ning Tang
Another reference is a set of presentation slides titled "Introduction to Discontinous Conduction Mode (DCM).
I think you should be able to find these, and probably more, by searching on the internet.
If you have trouble understanding my writings above, please let me know and I will try to clarify.
Keith
Are you sure? yes | no
Hi all ,
We need 3 current sensors in our design to measure solar panel,battery charging and load current.The maximum current to be measured is 40A.
I choose ACS758xCB hall effect current sensor to meet the requirement.Its cost is also reasonable.
Here is the data sheet and eBay link.
http://www.allegromicro.com/~/Media/Files/Datasheets/ACS758-Datasheet.ashx
http://www.ebay.com/itm/ACS758LCB-050B-PFF-T-Bidirection-Hall-Effect-High-Current-Sensor-GTS-/251923025835?pt=LH_DefaultDomain_0&hash=item3aa7c84fab
What you think ? If you have any suggestions please comment below.
Thanks
Are you sure? yes | no
Hi Debasish, I think you have found the right products. 50 Amps gives us enough capacity to accommodate high ripple currents. We need the bidirectional model for the battery connection, and I think it makes things simpler to use the same one for Load and Panels as well.
From the specs and pictures this seems to be a better device than the ACS712 used in V3.
Thanks, Keith
Are you sure? yes | no
I have posted the full analysis on Google Drive. If you send me an email I will provide access so you can look at the details (not for the faint hearted). keith.hungerford@gmail.com
Are you sure? yes | no
Thanks Keith for such a wonderful analysis. I am learning a lot from you.I will share all the details in this log.So anyone can directly access it.I request all to give comments and suggestions on it.
Are you sure? yes | no
Here is the updated folder link
http://www.instructables.com/files/orig/FKK/GI2X/IBKML22R/FKKGI2XIBKML22R.zip
Are you sure? yes | no
This is a further report on my work on the design. I have now completed the efficiency analysis of the design given in my previous report. Behind this are power dissipation values for each component in the design. There are two problems that emerged. a) the inductor is going to get too hot. I discovered and fixed an error in my original analysis, which meant that my original assessment was wrong. b) the efficiency is quite unsatisfactory at low current levels. Efficiency is OK at high current levels and achieves my design target of 96%. At low current levels (corresponding to poor illumination of the solar panels) the efficiency drops off very badly.
I will do some more analysis looking for solutions to there problems.
Below is one of the efficiency tables I produced. There are two, because of using either SMD or TO220 MOSFETS. They are very similar. This is the one for TO220 MOSFETS.
Tabulation T-130-26 PSMN3R3-80PS FDP150N10A
Panel voltage 18 30 60 30 60 60
Battery voltage 12.5 12.5 12.5 25 25 50
Load current
% Amps Efficiency Efficiency Efficiency Efficiency Efficiency Efficiency
1% 0.4 69.59% -8.21% -128.73% 82.10% -127.07% 64.30%
5% 2 93.90% 78.36% 54.33% 96.42% 54.62% 92.87%
10% 4 96.84% 89.14% 77.17% 98.16% 77.31% 96.43%
20% 8 98.22% 94.38% 88.46% 98.97% 88.61% 98.16%
50% 20 98.80% 97.27% 94.93% 99.33% 95.18% 99.12%
80% 32 98.70% 97.78% 96.39% 99.31% 96.71% 99.30%
100% 40 98.56% 97.85% 96.80% 99.25% 97.17% 99.34%
Overall efficiency average 78.24%
Keith
Are you sure? yes | no
This is a progress report my work on the main 40 Amp converter. I have suggestions / recommendations for the inductor, MOSFETs and capacitors. At the,moment I am just giving the bare component information. I will follown that up a bit later with more detailed explanation of how I got to these components.
Any comments or suggestions will be appreciated.
Inductor: 2 toroid cores T130-26, which are yellow-white OD 33mm ID 20 mm Height 11 mm. They are placed side by side and wound with 10 turns of a compound wire made with 4 strands of AWG 12 (2mm diameter) enamelled wire twisted together. It takes about 3.5 m of AWG12. An alternative if AWG 12 is hard to find is to use 7 strands of 1.5mm diameter enamelled wire, twisted together in the same way.
Capacitors: There are 2 capacitors in the main circuit, C1 and C2. Low ESR is a key requirement, especially for C1. ESR information on capacitors is a bit hard to come by. For C1 I suggest 8 capacitors in parallel, each 100 microfarads. For C2 I suggest 4 capacitors in parallel, each 100 microfarads. Debasish tells me that the V3 capacitors have an ESR of 35 milli Ohms, I am assuming the 100 uF capacitors in this new design will have similar ESR values.
MOSFETs: There are two options. Option 1 (the best option) is to use 16 MOSFETs type CSD19502Q5B. I found them for sale at $1.38 each. 4 are used in parallel in each position Q1, Q2, Q3 and Q4 in the current V3 schematic. These transistors have good Rds ON and excellent rise and fall times. Unfortunately this MOSFET is only available in a surface mount package, which may present a challenge for our constructors.
Therefore I developed a second option, which has nearly the same performance as Option 1, but costs about twice as much! All the MOSFETs are in TO220 packages. Q1, Q3 and Q4 are each 4 of PSMN3R3-80PS, which as very good RdsON but relatively slow rise and fall times. It is available for $2.82. The Q2 position is filled with 12 (yes 12!) of FDP150N10A. Its rise and fall times are quite good (but not as good as CSD19502Q5B) and RdsON is quite high. Hence there are so many of them. They are cheap at $1 each.
I will provide more details about the working for each of these suggestions in later log postings. In the meantime, other collaborators could you please consider the above, and give any feedback. Also consider re PCB layout (we have a big current to carry to, from and between these components. They have been selected to keep losses to a minimum, so we do not want to incur much loss in the connections.
Regards, Keith
Are you sure? yes | no
Hi Keith!
You are done very good work! Thank you!
I think that the power mosfets must be in TO220 package because in Q5B package the PCB board should have at least 4 layers. This will increase its price and will not be possible to produce at home.
I don't understand why you suggest FDP150N10A for Q2?
Regards!
Are you sure? yes | no
Hi Petar, Thanks for quick reply. I admit I am concerned about using the surface mount device. However I don't understand why it would require a 4 layer board. I can see a bit of a challenge in getting enough copper cross section to carry the current we need, which is about 12 amps per MOSFET. Is that why you say we need 4 layers, to separate the Source and Drain and Gate connections onto different layers? Maybe we can be a bit creative about that.
As for the FDP150N10A for Q2: This transistor has Tr=16ns and Tf=5ns. Not as good as the CSD19502Q5B but still pretty good. However the PSMN3R3-80PS has Tr=43ns and Tf=44 ns, much longer. Especially when running with the 60 V panel voltage, this produces a very high power dissipation, impacting the efficiency significantly, especially with a 50 kHz switching frequency. I have not fully explored the trade-offs between frequency, inductor, capacitors and MOSFETs, and when that is done the answer may look a bit different. But right now, on the analysis I have done so far, we probably cannot achieve a 96% efficiency just using the PSMN3R3-80PS.
Regards, Keith
Are you sure? yes | no
Hi! You can calculate how power will produce every transistor. When they are SMD this heat will be dissipated by the PCB. For that reason i suggest at least 4 layers. You can view Brush Motor Speed Controller for reference.
Thank you for reply! Regards!
Are you sure? yes | no
According to my arithmetic, the highest power dissipation in any of these MOSFETS with this design is less than 0.4 Watts (it is actually 1.23 Watts distributed over 4 MOSFETS in position Q3).
According to the data sheet, thermal resistance from junction to package is 0.8 degrees C/Watt, which gives us 0.32 degrees C temperature rise; and 50 degrees C/Watt, giving 20 C temperature rise. This is mounted on a 6.45 cm^2 copper pad on a normal PCB.
So I think we have to be careful about how we design the PCB but there is some margin before we run into trouble with heat.
I think we need quite wide copper areas anyway just to handle the current, so maybe there is a way through this.
There are some relevant diagrams on page 4 of the data sheet which I do not fully understand.
Regards, Keith
Are you sure? yes | no
Hello Keith
Nice research work on Components. I looked into page 4 , where recommended thermal design is mentioned . So here are my feedback on it.
1. You can very well use them , not hard or challenging to solder them. Hand Soldering is possible.
2. You can use 1 sq inch pad with 2 oz or 4oz copper as recommended, but we can do a smart thing here. we can use mini heat sinks solder to PAD directly. This process is not expensive and well practiced in Industry. (This the beat option I would recommed)
3. Or you can use MCPCB (Metal core PCB), widely used in LED Lights. It is little more expensive but it very good solution. You can solder all MOSFET on MCPCB and wire-connect corresponding Source, drain and gate to base PCB.
-Chinmay
Are you sure? yes | no
Hi Keith,
Can I know why you suggest 8x100uf and 4x100uf instead of single 800uF and 400uf capacitors for C1 and C2.The main problem in this case is space they occupy.
I think you suggest this to reduce the effective ESR value as the capacitors are in parallel.Is this the main reason ? If so then we can search for low ESR capacitor.The most problematic thing is seller do not providing the ESR value.
So I request all to suggest capacitor with the above rating with low ESR and low cost.
Thanks
Are you sure? yes | no
Yes Debasish, you are right it is getting a low ESR that is critical. We need less than 5 milli Ohms in C1, and less than 10 milli Ohms in C2.
You told me an ESR value for the capacitors you used in V3. How did you get that, and were both C1 and C2 the same ESR, even though they are of different capacitance? Regards, Keith
Are you sure? yes | no
I got it from local shop.It is local made capacitor.Here the shop man do not give all technical details. I asked the ESR value and he told 35mohm.I have not measured it.
Today I was searching for low ESR capacitor from digikey,got in the range of 40mohm to 50ohm.
Regarding the 12 AWG magnet wire,I searched at local shop.They have stock.
The cost is 650 INR ( approx $11) per Kg.
Are you sure? yes | no
I have been studying the main 40 Amp converter. This is a form of progress report, and also a request for input from anyone experienced and skilled in the science and art of design in this area.
A key component is the inductor. It has to carry 40 Amps plus a ripple current, maybe a total of 55 A peak. I am aiming for a low series resistance, and low magnetic field losses, both to achieve good efficiency (ie with the input energy going to the battery or load) and to avoid too much heating of the components, thereby easing thermal design and improving reliability (cool components are not as likely to fail).
My idea has been to select a suitable toroid core and using its data calculate the required number of wire turns, select a suitable wire size, calculate the path length and resistance, and see how that looks in terms of losses. Debasish's selections for V3 gave me a starting point, although the inductor used in V3 has much too high a DC resistance for us to use it directly. I also want to check the peak magnetic flux (if too high this can be a source of losses and heating). I also found there is an issue with the "skin effect" where an AC current will flow mainly in the surface of a conductor due to eddy currents induced by the main current flow.
Skin depth varies inversely with the square root of the frequency. At 50 kHz, the skin depth in a copper wire is about 0.296 mm. 20 gauge wire used by Debasish has a diameter of 0.81 mm, which means that the ratio of area in the "skin" to the total wire cross section area is about 95% - so maybe it is not too bad. I have not seen a reference where this analysis is done, but my guess is that we need to calculate the AC resistance as being about 5% to 10% higher than the DC resistance, due to the skin effect.
There is also an effect similar to the skin effect caused by current in adjacent wires. I have not found a good reference showing how to model this quantitatively. This effect (of adjacent wires) is clearly most significant if there is more than one layer of winding on the toroid, and is less if the number of turns is much less than the maximum possible with turns that are closely spaced around the inner circumference of the toroid. The effect will be most significant in that part of the coil that crosses the inner surface of the toroid, and least significant across the outer surface of the toroid.
Another aspect I have not seen a model for, is that our inductor has a DC current component as well as the AC component (which is a triangular wave). I am assuming that the DC component is affected by the eddy currents generated by the AC component. However I am not sure this is correct.
So some assistance on the skin effect and adjacent conductor effect, such as a good clear reference on how to model it mathematically, would be great.
The peak magnetic flux question is I think not too hard. There is an equation to calculate the flux, and some general guidance on maximum values generally used.
There is a range of toroid cores available on the market. Ebay has many listings, and no doubt other places do as well. They usually cost a few dollars each; larger ones are more expensive than small ones. The reference provide by Debasish in his instructions, to the document from AMIDON inc. has the required data about many toroid types. The material number 26 appears to be the best for this application.
If it turns out we cannot make a single inductor, we have the option of using two or more in parallel (so each inductor has to be a higher value, but carries less current).
We can also do some tuning of the period of our PWM signal. It does not have to be a single value, but could vary with load and solar illumination conditions.
Once we have an inductor sorted out, I think the calculation of switching losses will be straightforward. We have a choice of staying with the synchronous design (which has higher losses when the load is light) or an asynchronous design (which has lower losses under light load, at the expense of higher losses when the load is big). There may be some hybrid solution if the gains are sufficient.
Comments anyone? Keith
Are you sure? yes | no
Hello Keith
Please correct me if I got understanding on this above post wrong. My understanding from above post is " you are looking for Mathematical Model or Simulation application where you can design an Inductor by giving in all the parameters for core, wire, size etc. and getting results of various behaviour w.r.t Current , heat , losses. So that you can optimize it w.r.t circuit required efficiency" Right???
I don't know /deal with making Inductor (rather we get them as per our specification from China manufacture), so I am unaware of available of any such Inductor Design Simulator. But I do deal with making process core for Motor, Generator . So there is a non-commercial research based application/ Simulator available for that. And pretty much put everything like core material, wire thickness, core design into it and it gives out simulation result of magnetic flux, current losses etc. And I think you can use it for your purpose.
you can find it here http://www.femm.info/wiki/HomePage
a quick tutorial here http://www.femm.info/wiki/MagneticsTutorial
Some useful Examples here http://www.femm.info/wiki/Examples
Brief Introduction
"Finite Element Method Magnetics (FEMM) is a finite element package for solving 2D planar and axisymmetric problems in low frequency magnetics and electrostatics. The current version of the program program runs under runs under Windows 2000, XP, Windows 7 and Windows 8. The program has also been tested running in Wine on Linux machines. The program can be obtained via the FEMM home page at http://www.femm.info. The package is composed of an interactive shell encompassing graphical pre- and postprocessing; a mesh generator; and various solvers. A powerful scripting language, Lua 4.0, is integrated with the program. Lua allows users to create batch runs, describe geometries parametrically, perform optimizations, etc. Lua is also integrated into every edit box in the program so that formulas can be entered in lieu of numerical values, if desired. (Detailed information on Lua is available from http://www.lua.org/manual/4.0/) There is no hard limit on problem size—maximum problem size is limited by the amount of available memory. Users commonly perform simulations with as many as a million elements, though simulations with tens of thousands of elements are typical."
I don't practice with it, but my team told me it is one of its type to solve this kind of issue , also reliable.
I hope this will help you some how, if it does let me know .
-Chinmay
Are you sure? yes | no
Hi, Thank you very much Chinmay for your suggestion. I will look into it.
I think I have managed to crack this problem mainly using the application notes on the Micrometals web site. However I would like to run my solution through this analyser to find out if there is something I have missed or got completely wrong.
I discovered from my analysis that once I had the right toroid (the one I chose at first was too small) that the AC resistive losses due to skin effect and adjacent conductor effect were small, and the core loss due to magnetic flux hysteresis was also small. The dominant source of loss ended up being the DC resistance of the winding wire. I think that is a good result, because I am reasonably confident that the DC resistance calculation is correct, and even a factor of 2 error in the other losses won't make a real impact.
But as I said, I will look into using the FEMM simulator to check my spreadsheet analysis results.
Thanks again,
Keith
Are you sure? yes | no
Hi Chinmay, I have had a look at the FEMM materials. Interesting. I was hoping there might be an example of a toroidal inductor analysis which would be a good springboard for what I would like to do. But there is no such example. Searching separately on the internet I found a PhD these on a somewhat related topic that included a 2D finite element analysis of a toroid, so that might help. My problem right now is TIME. I don't have the 3 years of so that a PhD takes, or even a month. So my pragmatic approach is to keep going with the analysis I have, and build a sample and measure it's performance.
I still have not really worked out how to do that, but I think it is the best approach for the moment. I think the FEMM way is a good one and will get back onto it when some of the other main issues are put to rest.
Thanks again,
Keith
Are you sure? yes | no
Hi guys! In Drive I add new file voltage_stabilizer.xls with calculation for Step Down Converter. But power dissipation is 78W. This makes it inappropriate.
I looked at a few Voltage Boost Converters and stopped at TPS61175. I did stimulation. You can see the results here:
Vin = 5V
Vout = 12V
Iout = 800mA
Are you sure? yes | no
Hi!
What do you think for these "add-ons":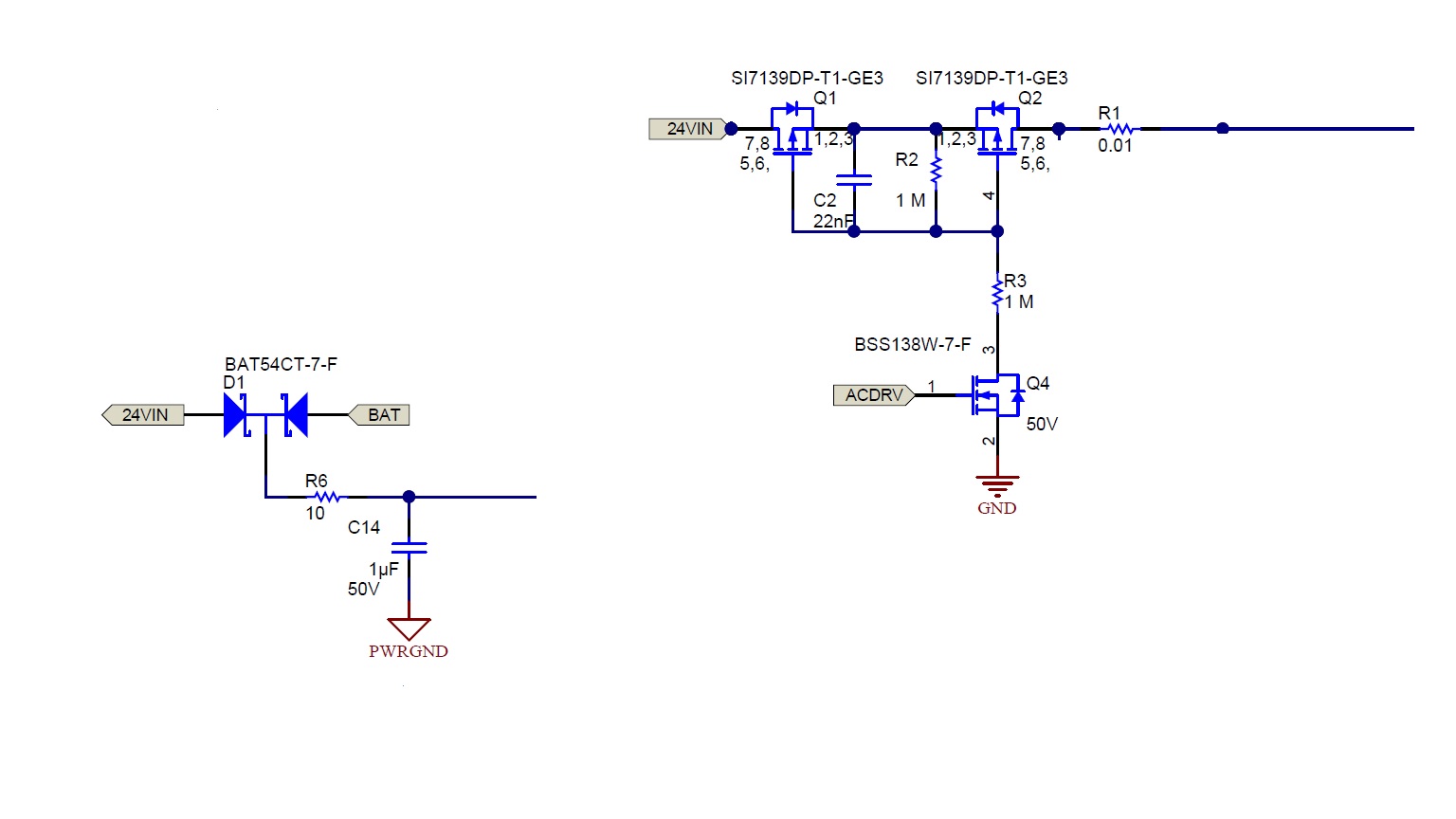
Left: Power from Battery or Solar Panel.
Right: Removed Q1, D1 and R5 in first scheme can be exchanged with this. We can use only one transistor.
In shared folder you can see file LM5007QuickStartCalculator.xls. I entered our values.
Are you sure? yes | no
Hi Petar, I thought your first sketch had 2 Zener diodes, but I realise now these are just normal diodes. I think the idea is that the MPPT controller can take its power from either battery or solar panel, so it does not rely on the connection of the battery to operate. If we do this, we can have a controller that can work with just a DC load and solar panels, with no battery. Is that your concept?
I must confess I do not understand your second proposal, with the 3 MOSFETs. Can you explain please?
Are you sure? yes | no
Hi Keith! These diode is SMD Schottky Barrier Diodes. This is exactly what I had in mind. :)
In first Debasish's schematic Q1 blocking the power from battery to solar panel during night. This scheme replaces Q1, D1 and R5 because P transistor produces less heat.
Are you sure? yes | no
Hi Petar, Thanks for reply. Re the Q1 alternative, we removed these components (Q1, D1, R5) altogether because they are not necessary. So I don't think there is a need for your alternative (which I still don't understand the circuit, but maybe that does not matter).
Re getting internal power from either battery or solar panels. I think this may be a good idea (maybe other contributors have a view) and it seems to be pretty simple assuming we discard item 12 on our original list of enhancements (ie much higher panel voltage).
Our internal power requirements are for 5V (mostly), 3.3V (for WiFi module) and 10 V (for MOSTFET gate driver). I think we are close to settling all of these - Regulator based on LM5008 for 5 V, and derive 3.3 V from 5V with a linear regulator. I have in mind to use a very simple voltage doubler circuit to get 10v (very small current required) from t he 5V rail.
I am thinking we need a complete power schematic showing all of these. Ideally we will have supporting calculations for each item. The main thing we are missing is for the 10 V supply.
When you select the feeding diodes, please check the ratings are sufficient (with a bit of margin, which helps reliability).
Would you be willing to put this together for us? Thanks,
Keith
Are you sure? yes | no
Hello Petar and Keith
I am Chinmay , friend of Debasish. I am into EMS- electronics Manufacturing Services and I mostly design Circuits. I have been following this discussion for a while. As we deals with many power circuits and from my field experience I would recommend this from previous post
"It appears LM5007/LM5008 is a good solution, but it's output current rating is limited for your multitasking circuits. I would recommend to have a stable 12V 2A source in your circuit from the HV 48V Battery pack. Getting any desire voltage from 12V source is much more easy and cost effective. So I think you can go for 2 stage conversion e.g 80V to 12V, then 12V to 5V or 3.3V(if you want to use WiFI chips). "
As Debasish mentioned the max load current required by circuit is 350-400mA. So LM5007 with 0.7A output seems good, but again if you are going to use linear VR like LM1117 to get 3.3V from 5V , Input current may not sufficient for the Linear Regulator.
Keith your idea to use Voltage Doubler Circuit to get 10V from 5V source is good and quick and easy solution. But again it depends on Source Current. I wish, if LM5007 could give 1000mA, then everything will match perfect.
For SMD Schottky Barrier Diodes you can use SS56 (5A-60V) or SS36(3A-60V) which has much more high ratings and widely used in Power Circuits.
-Chinmay
Are you sure? yes | no
Thanks Chinmay, I really appreciate your input. I made a mistake in my previous posting in suggesting we go with LM5008. Its current
capacity is too low and gives us almost no margin. The LM5007, which has a just sufficient voltage rating and about double the current rating compared to LM5008, seems to be a feasible choice. I would still prefer a similar converter with a slightly higher voltage rating, and about double the current (like 1 or even 2 Amps). However we have not found it yet. It may well exist.
I don't find the LM5116 attractive because it needs external switching transistors - which I guess is why it can supply much more current.
I think the linear regulator, like LM1117, to supply the WiFi module at 3.3 V, should be OK. The current required by the WiFi module is 215 mA at 3.3V. Although a buck converter would give us some current gain, the difference would be fairly small. The best we could do would be a reduction from 215 mA to maybe 160 mA. For that we would need to add not only another buck converter IC, but also another 4 external components (2 capacitors, 1 diode, 1 inductor). The LM1117 is much simpler.
Regarding the diodes, I understand the SS56 and SS36 are surface mount devices. I think we need through-hole mounting, for ease of construction by our Hackaday audience. I discovered dual diodes that may be suitable, but would like your opinion. They are BYQ30E-100 or BVY44.
I hope Petar will come up with a design for the voltage doubler.
Regards.,
Keith
Are you sure? yes | no
Hey Keith
SS56 and SS36 are larger enough to have hand soldering , I have done that many times without any issue. I prefer to use commonly available components, because the are cost effective. anyways we can choose which is best suitable for the application. Both BYQ30E-100 (16A) or BYV44 (30A) are good for this application.
Does any one from the team doing Cost Estimation on BOM ?
Again I consider about LM1117 and it came to my mind, Arduino MCU is not going to consume 100mA always. if Codes are optimized, then it can run at 25mA in always active mode. Only it consume higher current when Internal ADC is active. So if we limit use of ADC, we can save over 60% current for MCU. and that current will give you some margin for other interfaces.
-Chinmay
Are you sure? yes | no
Thanks again Chinmay,
Re your questions:
We have not started doing a Bill of Materials yet. However we have a shared spreadsheet which the project contributors are using for detailed calculations of various design parameters. I think it would be logical to add a BOM sheet to this spreadhsheet.. We can do this soon and add to it progressively as the design is developed over the next few weeks.
Control of power consumption is a matter that we have not started working on yet. I hope that we can do some reasonably simple but effective power management. We need this particularly in the night time when the sun is not shining so we (and the loads) are entirely dependent on the battery. The biggest single loads are the Arduino MCU and the WiFi interface. Hopefully we can implement a "sleep" mode that minimises power consumption, but can wake up if there is a need.
So it is not just margin for the 5V voltage converter we need, but also general energy consumption saving.
We have quite a lot of tasks in front of us. But I feel we have a good team willing to contribute and will end up with a great project.
Keith
Are you sure? yes | no
Hi Keith! What you think about that:
edit: 10W is 10V, my mistake
Are you sure? yes | no
Thanks Petar,
A couple of things,
I think the bottom end of D2 needs to be connected to the +5V rail, not ground. Please check.
I understand that the input "PWM" is the Arduino signal on pin D9. Is that correct? Will this work OK over the full range of PWM ratios we are likely to use, from very high to very low? Is there any chance we will exceed the current rating of the Arduino output, without a current limiting resistor?
How much current can this circuit supply? How did you size the capacitors?
Thanks again
Keith
Are you sure? yes | no
Hi!
PWM signal can be from arduino or timer 555. Arduino GPIO can delivery 40mA on 5V which is 0.2W. In this case we have 0.2W and 5V whis is 20mA in the ideal case without losses in semiconductors. I suggest to insert timer 555 with fixed frequency.
C1 should be much smaller than C2 (lower C1 gives lower ripple, but lower curtent capacity and slower voltage ramp-up), and critically diodes should have lowest possible Vf. Also C1 and PWM frequency should be calculated for 10V.
Are you sure? yes | no
Don't forget your "40mA" coming off the AVR is listed under "Absolute Maximum Rating". When doing a design, you should always use the recommended max values in the regular section of the electrical specs under IOH/IOL which are only 20mA.
Note the voltage drops (typ value not guarantees) under that section as well as the graphs under "35.7 Pin Driver Strength". Voltage drops are probably 0.7-0.8V at 20mA (I think that needed to be counted twice - one for charging the cap, again for "lifting" the cap) and not factoring in additional drops across 2 series connected diodes in a charge pump. i.e. you are no where near 10V either. Ditto for the 555 datasheets very carefully and disregard the numbers that are not from the right sections of a datasheet. Take a look at the graphs for typical performance before drawing your own conclusions about the real current you can draw.
There are Charge Pump chips if you are going down this path...
Are you sure? yes | no
Hi Lee!
I did not understand your disapproval for 555. What do you think for common collector transistor?
Regards!
Are you sure? yes | no
Did you read the datasheet correctly? Read the voltage drops curves at all? Do that before asking that question.
Are you sure? yes | no
Obviously you're in a bad mood. Sorry about that. :)
While looking for datasheet I found this:
http://www.instructables.com/id/555-Voltage-Doubler/
http://www.elprocus.com/voltage-doubler-circuit-with-working/
Regards!
Are you sure? yes | no
Why do you avoid read the datasheet and go by unreliable 3rd party info? That's what I have issues with. Learn to read datasheets correctly and think/analyse for yourself.
On TI's LM555, the voltage drop on VOH is somewhere between 1.3V to 1.6V for current between 1mA to 100mA for VCC=5V while VOL is somewhere between 0.01V and 1V depending on the current.
Let's be generous and use 1mA for drops to see the highest voltage you'll get from this. You can use LTSpice to look at more realistic numbers.
So you are charging the cap when 555 output is low via diode with 5V - 0V - 0.5V = 4.5V
When the 555 pin goes high, the cap is lifted up by 5V - 1.3V = 3.7V i.e. 3.7V + 4.5V = 8.2V get dumped via another diode into output cap. So cap has 8.2V - 0.5V = 7.7V. <-- This is the peak value. Average is lower as the cap discharges in the cycle.
Are you sure? yes | no
Ok Lee, I don't think that this voltage drop is a problem. With 555 PWM with 3.7Vpp we can drive transisto and we will have 5V PWM.
I still think that the common collector transistor scheme is best for our purpose.
Regards!
Are you sure? yes | no
Other simple voltage linear regulator:
Vin - from battery or PV
Vout = Uz-Ube = 12 - 1 = 11V
Ube is usually about 0.7 V for a silicon transistor. BD139 has Ube = 1V.
R4 = Vrmin / (IDmin+ILmax/(hFE+1))
Where:
- Vrmin is the minimum voltage to be maintained across Rv
- IDmin is the minimum current to be maintained through the zener diode
- ILmax is the maximum design load current
- hFE is the forward current gain of the transistor, ICollector / IBase
In my opinion this is the best option
Are you sure? yes | no
Hi Petar,
P-channel MOSFETs are easier to drive but have a higher RDSon value than most N-channel MOSFETs. Just something to consider.
Are you sure? yes | no
What you need to do is modify the design and algorithm to use the stable voltage for testing, and determining optimum power transfer. Existing method is exact, appears limited by design of a Buck converter.
I suggest using the present method to determine optimum power transfer, then base your switching of the raw, unconditioned solar input to approximate the transfer as if it were through a Buck converter. Testing after each period of raw switching that bypasses the Buck converter would be made to adjust the raw switching.
This might approach the optimal MPPT performance, and allow you to get around limitations (and costs,) of a 5KW Buck converter.
Are you sure? yes | no
Charles, I am having trouble understanding what you are suggesting. Is it just to do with how we can test our controller design? Or is it to do with a need to change the MPP tracking algorithm? I would be happy to understand your suggestions, if you can clarify please.
Thank you,
Keith
Are you sure? yes | no
Scan of existing product spec reveals the Buck converter as limiting. Eighty AMPS is allot of current switched through two critical components: the switch, and magnetic inductance. As efficiency will be high, you may be able to pull it off somehow. Products appear to have determined forty amps as the upper limit for viability, and are testing the market. A synchronous converter may be interesting, allowing scaled levels in increments. Look in LTSPICE, and for custom computer generated designs using the Linear Technology SCAD program to determine switch, and magnetic currents in Buck topology. Then decide how you want to go about switching a hundred-fifty amps into the magnetic at fifty-percent duty cycle. There is a problem here for marketing a safe, reliable, and producible product.
Are you sure? yes | no
Charles, Current project (V3) handles only 50 W. New Version 4 aspires to 40 Amps,, which with a 48 V batter translates to 2 kW. I think this is sufficiently ambitious for the current project. There are commercial products on the market with higher capacity, so it obviously can be done. But at this stage, I think 40 amps will address a big segment of the user requirements. Do you have a different view?
Keith
Are you sure? yes | no
Thanks Petar, if we go with a 60 V rating in this converter we would need to remove the capability to handle a 48 V battery. If there are no integrated circuits that will handle 80 V then we might be down to the last option, of making the converter from discrete components. Or maybe there is a way of protecting a 60 V converter from the 80 V level when it occurs. Could we put a linear regulator in front of the 60 V switchmode regulator?
I think it is a bit early to give up on our aspiration for a 48 V battery at this stage.
Thanks for your input.
Keith
Are you sure? yes | no
Can I know why we shouldn't not go for 48V battery system ? Little bit puzzled.
As per my knowledge the buck converter input voltage should be matched with battery to be charged. As we are taping power from the battery.
If 48V is nominal battery Voltage,it can goes up to 56 - 58 V or maximum 60V when fully charged. What petar is recommend may fulfill our requirements.
If I am wrong please clarify .
I checked the LM2576 module on eBay its cost is 2.99 USD.These are the specification
1. Input voltage range: 5V-60V (rated Suggestions below 50V reliable)
2. Output voltage range: 1.25V-26V
3. Output current: 3A(MAX)-need to add heat sink
4. Continuous working current: 1.2A (total power output within 20W)
5. Conversion efficiency: Up to 92% (output voltage higher, the higher the efficiency)
6. Switching Frequency: 150KHz
7. Rectifier: Non-Synchronous Rectification
8. Module Properties: Non-isolated step-down module (buck)
9. Short circuit protection: current limiting, since the recovery
10.Operating temperature: Industrial grade (-40? to +85?) (output power 10W or less)
11.Full load temperature rise: 40?
12.Load regulation: ±0.5%
13.Voltage regulation: ±0.5%
14.Dynamic response speed: 5% 200uS
15.Mode of connection:welding
16.Size:4.3(L)*3.0(W)*1.2(H)cm
If we do not use ready made module , We can use the 4 leg converter on our final PCB.
Are you sure? yes | no
Hi. I think we should cater for as many situations as we reasonably can. I have the following data from various references.
For charging Lead Acid batteries, voltages range up to 2.48 V/cell (Wikipedia); 2.45 volts/cell (Battery University); 2.76 volts/cell (PowerStream). This last case is an extreme one for very low temperatures. These translate to 59.5, 58.8 and 66.24 volts in a nominal 48 V battery.
For charging NiFe batteries, the charging voltage goes up to 1.8 volts/cell, so for a 40 cell battery (nominally 48 volts) the highest charging voltage would be 72 volts.
For Lithium Iron Phosphate batteries, they have a nominal cell voltage of 3.2 volts/cell, so a nominal 48 volt battery would have 16 cells. which gives 51.2 volts. Wikipedia gives a maximum charging voltage of 3.65 volts/cell which equates to 58.4 volts in a nominal 48 V battery.
If we are to use a component with a 60 V maximum rating, then as a matter of good practice (aiming for a reliable system) I don't think we should subject it to more than about 50 volts. This margin will be a matter of opinion. Anyway we are in a very marginal situation with a 60 V rating. I specified 80 V in order to give us a good safety margin. I agree it may be a bit higher than is truly necessary - but I do not think a 60 V rating, for a conservative 50 V limit, is enough.
I am now thinking about a 60 V regulator (hopefully package) sitting at 50 V below a linear regulator that takes the top 30 V (usually less) off the voltage exposure. The current drain at 50 V will be quite small (like, around 100 ma) so the power loss in a linear regulator will be modest.
Regards, Keith
Are you sure? yes | no
Hi!
We need LM2576 or similar just to power Arduino and other peripherals. The total power consumption is less than 1A. But input voltage can be more than 60V.
Regards!
Are you sure? yes | no
Thanks keith for making me clear.You are right 80V or near to it is good choice. I skipped the NiFe battery.
So we need a higher rated converter. 60V is not sufficient.
Petar, the power consumption is less than 1A excluding the USB port. If we power USB from the same converter then current rating should be higher. Their may be another option for using a separate converter for USB port.
Are you sure? yes | no
Yes, 1A excluding the USB port but serious controllers have no USB for charging. This controller is similar to our requirements: http://www.victronenergy.com/solar-charge-controllers/bluesolar-mppt-150-35
and this: http://www.ebay.co.uk/itm/LCD-Display-40A-Solar-Charge-Controller-100V-Solar-Panel-True-IP30-MPPT-Function-/400674514052?pt=LH_DefaultDomain_3&hash=item5d4a0fe484
Are you sure? yes | no
LM5116:
Vinmin = 6V
Vinmax = 100V
Ioutmax = 20A
But the price is big.
Are you sure? yes | no
Thank you Debasish and Petar for quick and useful inputs. BlueSolar controller does 48 V as well as 12 and 24 V, so it is closer to our target. The Tracer charger on EBay only does 12 and 24 V. I have a later model of this controller in my off grid system. It works well but has its limitations.
Can you give us an idea of the price of the LM5116? The spec looks like overkill (re current) which might make it seriously expensive. So the price could be a big problem.
So now I looked on EBay. The bare chip is available for $5 - $8. Integrated into a development board it is more like $75.
So we might look at putting the relevant components around it ourselves. It may still be expensive compared to a complete buck converter package for less than $3. I am still looking at how to use the cheaper unit.
And I looked again on Ebay for LM2576. Bare chip is around $0.50. Integrated into a package the cheapest I saw was $1.80, but mostly around $5 to $7.
Are you sure? yes | no
Hi! I am not shopping much on ebay because of a long wait for delivery. For that reason I looking here: http://bg.farnell.com/texas-instruments/lm5116mh/ic-sync-control-buck-1mhz-htssop/dp/1342345?ost=LM5116&categoryId=700000004337
Here the price is 6 Euro.
Are you sure? yes | no
Can we make 80V to 5V in two stages ?
Are you sure? yes | no
Hi. I have been studying the 2 stage solution. I have a design almost ready to share with the team. It uses a buck converter, either package or based on a converter chip like LM2576 and associated discrete components. I have assumed the buck converter generates 5 V out and takes in anything from 6 v to 60 V (as per our earlier messages). Then I have an interface to the Vb rail. The interface uses 4 transistors, 2 zener diodes, and a handful of resistors. It may need a capacitor as well, I have not worked that out yet. I think the cost of the components for this option is going to be pretty similar to the cost of a LM5116, although I have not done that arithmetic yet. I will update status in a little while.
Are you sure? yes | no
LM5007: 80V switching regulator, LM5008:100V switching regulator Both are around $2.5 QTY 1. http://www.findchips.com/search/lm5008
As for 60V-80V... Telecom uses 48V batteries, so there are lots of parts designed for that market.
Also warning about ebay DC/DC converter boards using parts that are sanded and laser engraved to look like higher rating ones.
Are you sure? yes | no
K.C. Lee, thanks for sharing the informations on LM5008.
It may work for us. I go through eBay its cost around 4.5USD and have following specifications.
Input Voltage Min:6V
Input Voltage Max:95V
Output Voltage:75VPrimary Input Voltage:95V
No. of Pins:8
Output Current:350mA
Output Voltage Min:2.5V
Output Voltage Max:75V
Switching Frequency:1.1MHz
Temperature Max:125°C
Packaging:Cut TapeMSL:MSL 1 - Unlimited
Operating Temperature Min:-40°COperating Temperature Range:-40°C to +125°C
http://www.ebay.com/itm/IC-STEP-DOWN-REGULATOR-VSSOP-8-MPN-LM5008AMM-NOPB-TEXAS-INSTRUMENTS-/271558052235?pt=LH_DefaultDomain_3&hash=item3f3a1f098b
Are you sure? yes | no
Hey DD
It appears LM5007/LM5008 is a good solution, but it's output current rating is limited for your multitasking circuits. I would recommend to have a stable 12V 2A source in your circuit from the HV 48V Battery pack. Getting any desire voltage from 12V source is much more easy and cost effective. So I think you can go for 2 stage conversion e.g 80V to 12V, then 12V to 5V or 3.3V(if you want to use WiFI chips).
You can also consider 90-60VDC input 12V output CC LED driver IC, mostly used inside LED Lights. They are reliable, dedicated to for this specific CC 12V supplies. I dont have the exact part no with me now, will update here soon.
Are you sure? yes | no
Thanks for the suggestion.
Power consumption data in my v-3 controller ( rough estimation ) :
1. WiFi Module - 215mA maximum
ESP8266 operates at 3.3V ,if we calculate current at 5.0V level,it should be less.But for the time being take the maximum value.
2. LCD - 40.8mA ( with back light on) and 5.6mA ( back light off) I have tested in my v-3 controller
3. LED ( maximum 15 mA, if we use SMT LED it should be less)
4. Arduino Board - maximum 100mA
5.USB port - 2.1A
If we discard USB port,the total power requirement is
215 + 40.8 + 15 + 100 = 370.8mA
LM5007/LM5008 have 700mA output . So I think it have enough margin to power all the auxiliaries.
Are you sure? yes | no
Thanks K.C.Lee. I think that means we can just go with an off-the-shelf package, which is great for both design time and implementation cost. I will cease work on the 2 stage solution.
Are you sure? yes | no
No problems.
Are you sure? yes | no
We need a converter to output +5V to power the Arduino and all the other peripheral devices in this controller. Version 3 uses a packaged buck converter from D-SUN, but I believe its voltage rating is not sufficient for Version 4. So we need to find a suitable converter. My suggested steps are:
1. we need to assess the 5 V current requirement. We have a partial listing of all the devices in our design spreadsheet, so we just need a column to show the expected current draw by each one. I hope one of our contributors will do that.
2. we need a converter with the following capabilities: a) sufficient capacity for all the devices, plus some margin for future additions; b) input voltage as low as 9 volts and up to 80 volts c) efficient design so it has minimal impact on the overall efficiency of our controller.
I think the preferred solution will be an off-the-shelf buck converter; but if we cannot find one then the next choice would be a buck converter we assemble as part of this project using a buck converter chip and some discrete components. Last choice would be a converter we assemble ourselves from discrete components. I hope one of our contributors will look into this.
Posted 11 June 2015 by Keith.
Are you sure? yes | no
Hi!
I can suggest these:
LM2575HVT-5.0 > Vinmin=4V; Vinmax=60V; Ioutmax=1A
LM2576HVT-ADJ > Vinmin=4V; Vinmax=60V; Ioutmax=3A
Voutmax is not up to 80V but it is very hard to find such converter.
Regards!
Are you sure? yes | no