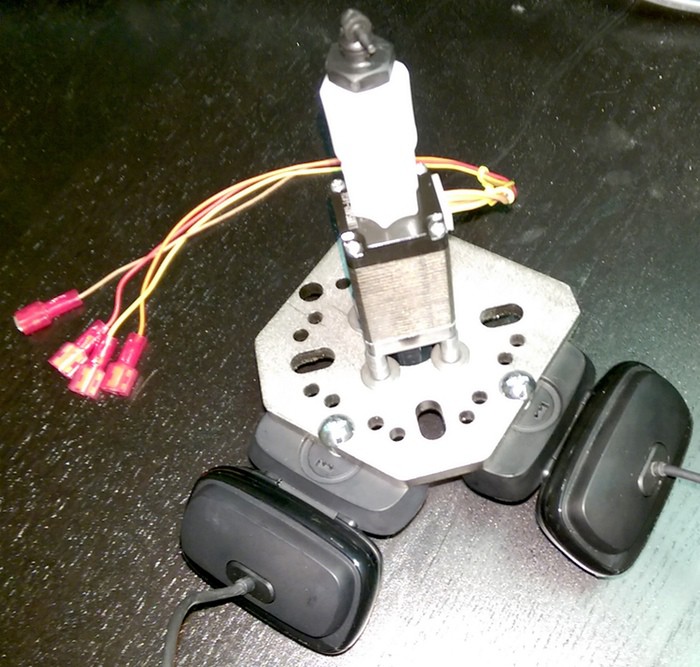
This new head design will eliminate all of the backlash that we currently have. It also brings rigidly mounted cameras that will allow us to move faster. Previously, we had to run slower than top speed just so our cameras wouldn't move off target due to rapid accelerations and decelerations.
Right now we have to waste a bunch of time over the upward looking camera while we confirm that our rotational correction has been applied. This is because of the backlash in the system. The computer vision tells us that we have to rotate, say 5 degrees, to have the part properly aligned, however when we tell the motor to turn by 5 degrees it really doesn't turn 5 degrees because our belt system has slack in it. Some of the motor's movement is just to take up the slack in the belt instead of actually rotating the part. We end up needing to use the computer vision to confirm that the part was actually rotated correctly and this means having to hang out over the upward camera until the part is actually fully rotated to the proper orientation.
The new head will eliminate all of this wasted time. The new design has no belt, so we'll be able to take an image of the part, and then immediately start flying to the place location. On our way there we should get the feedback from the computer vision saying what the angular offset is, and we can correct it on the fly. This is the first major step to getting us to over 1000 cph (components per hour).
The new head has been mounted on our prototype, but we need a bracket to mount a limit switch to so that we know when we make contact with the pick-up tip. We have time scheduled late tomorrow with the laser cutter, so we should be able to start running trials with the new head design on Thursday.
We're also trying a NEMA 23 motor on the z-axis to see if there's any speed difference versus the old NEMA 17.
The last change we applied today was a new feeder divider that will allow us to reconfigure the incoming feeders for the various types of SMT reels out there from 8mm to 44mm.
Discussions
Become a Hackaday.io Member
Create an account to leave a comment. Already have an account? Log In.