Today I tested the more powerful leg.
The original leg--using 20 kg-cm servos--could exert 1250 grams of "push" on a scale. The new leg--using 40 kg-cm servos--measured 3300 grams of "push" before the upper plywood test jig lifted. In other words, I'm getting nearly three times the lift with the new motors. The original leg used three $18. motors while the new leg uses one $18. motor and two $38. motors; so my cost per leg just went up $40.
The extra torque was too much for the upper axle piece and it sheared at the connection where it holds the leg.
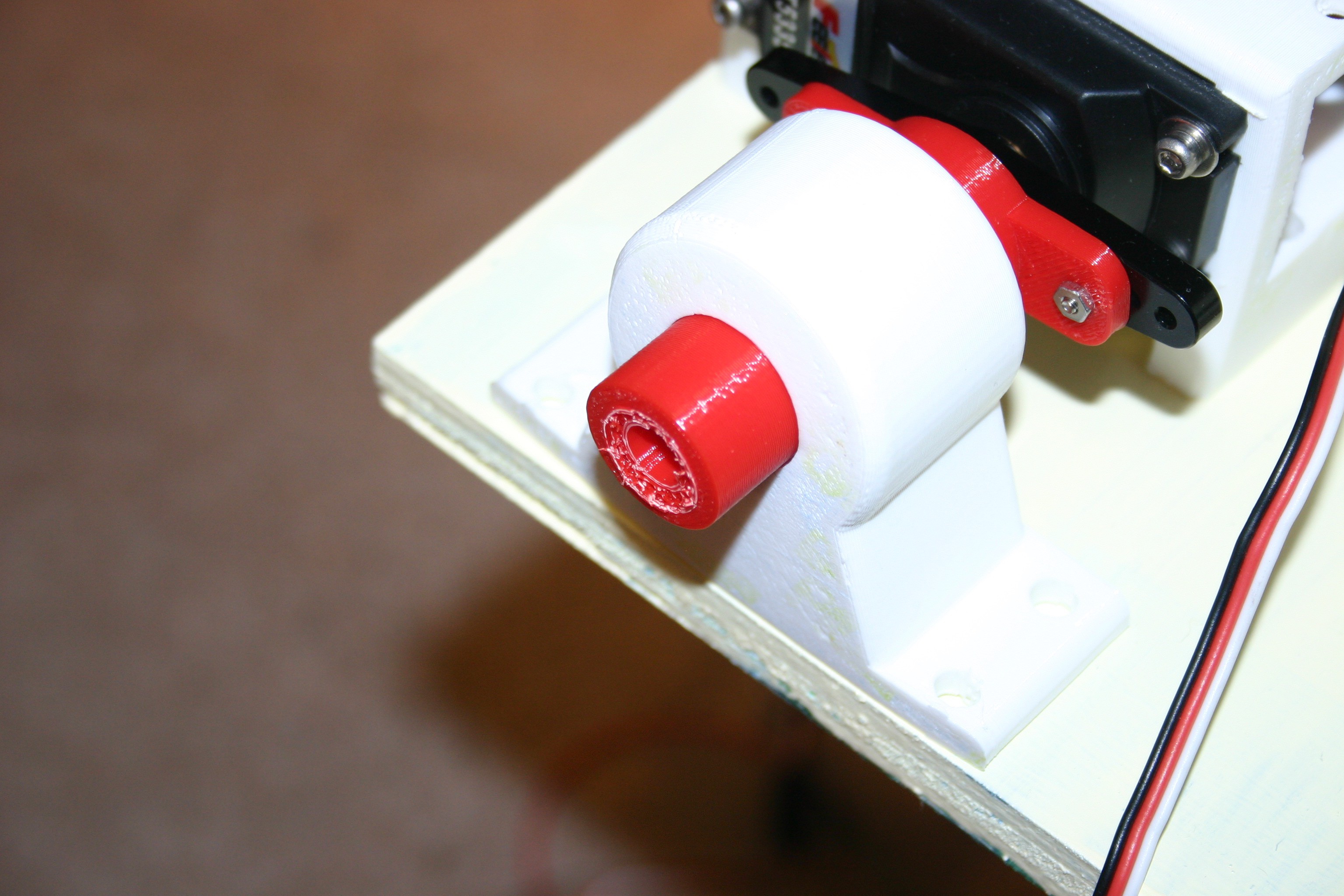
I reprinted the axle at 100% fill and it is now holding for test purposes. I'm in the process of redesigning the connection for more strength.
An unexpected benefit of the new motors involves a stiff gear train that resists external movement. If I raise the leg in the air and remove power to the servo motors, the leg stays in place.
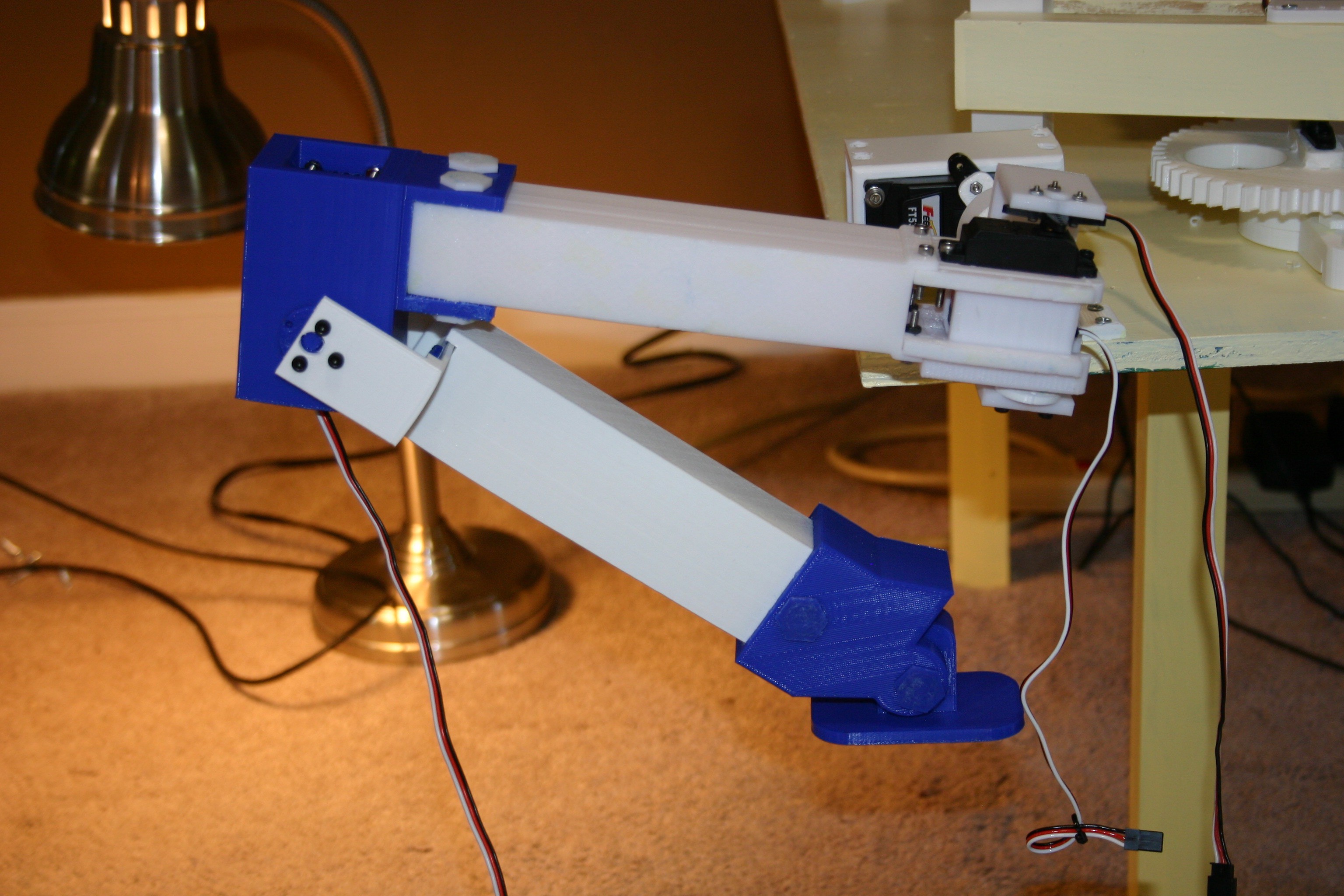
This is a major benefit in that the motors draw virtually no current (thus no wasted heat and battery energy) unless they are moving.
I'm working on stronger connections and I've ordered enough parts to complete four legs.
Discussions
Become a Hackaday.io Member
Create an account to leave a comment. Already have an account? Log In.