Another $30 in the furnace & an assortment of welding alternatives arrived, along with some 10 mil steel. Actually thought it was tin & ate 12oz of cookies to obtain it, only to find out it was steel. The 2 farsteners of choice were pop rivets & staples. The staples looked horrendous while the pop rivets gave the aircraft look lions wanted.
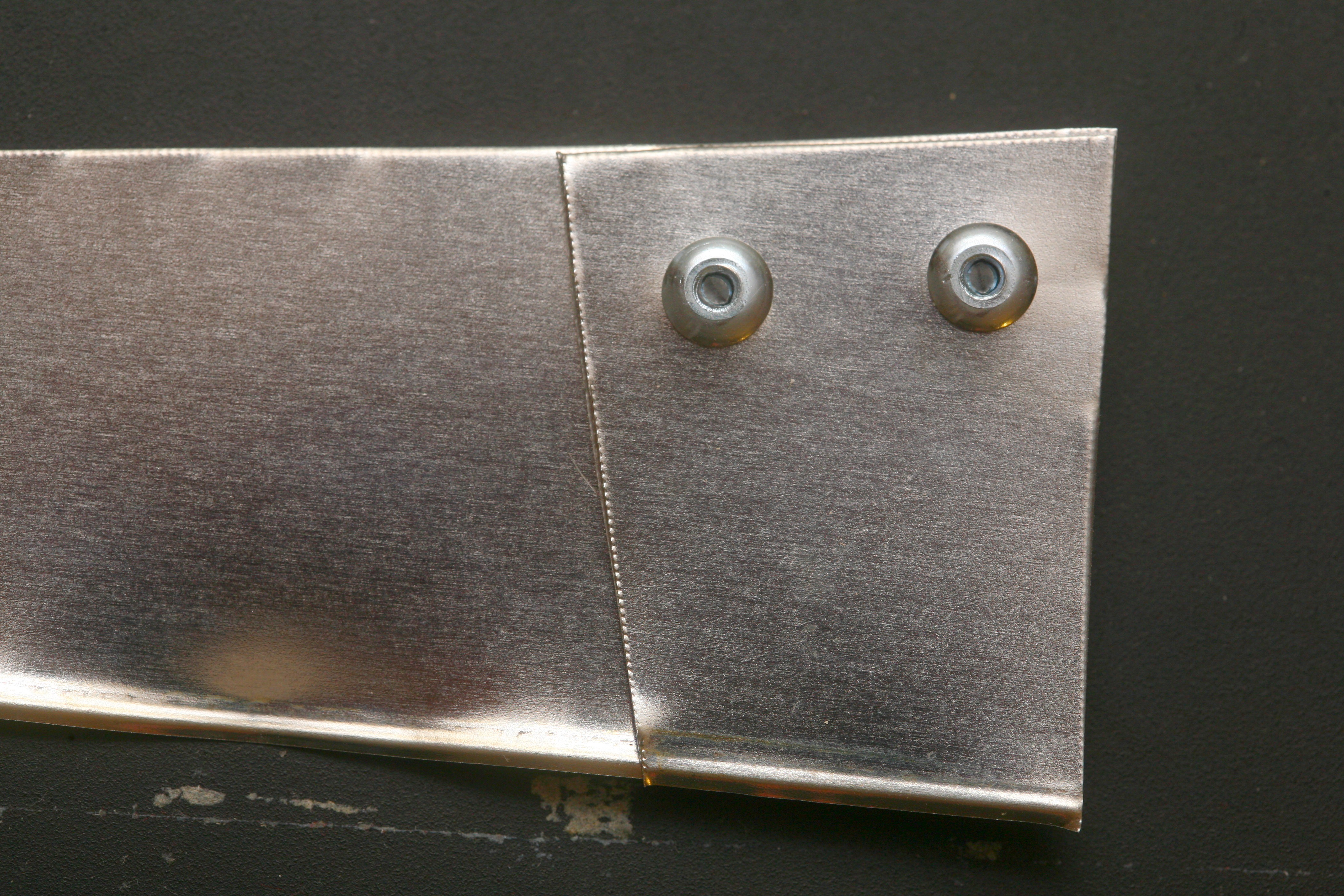
They just created horrendous plugs which had to be painstakingly machined down.
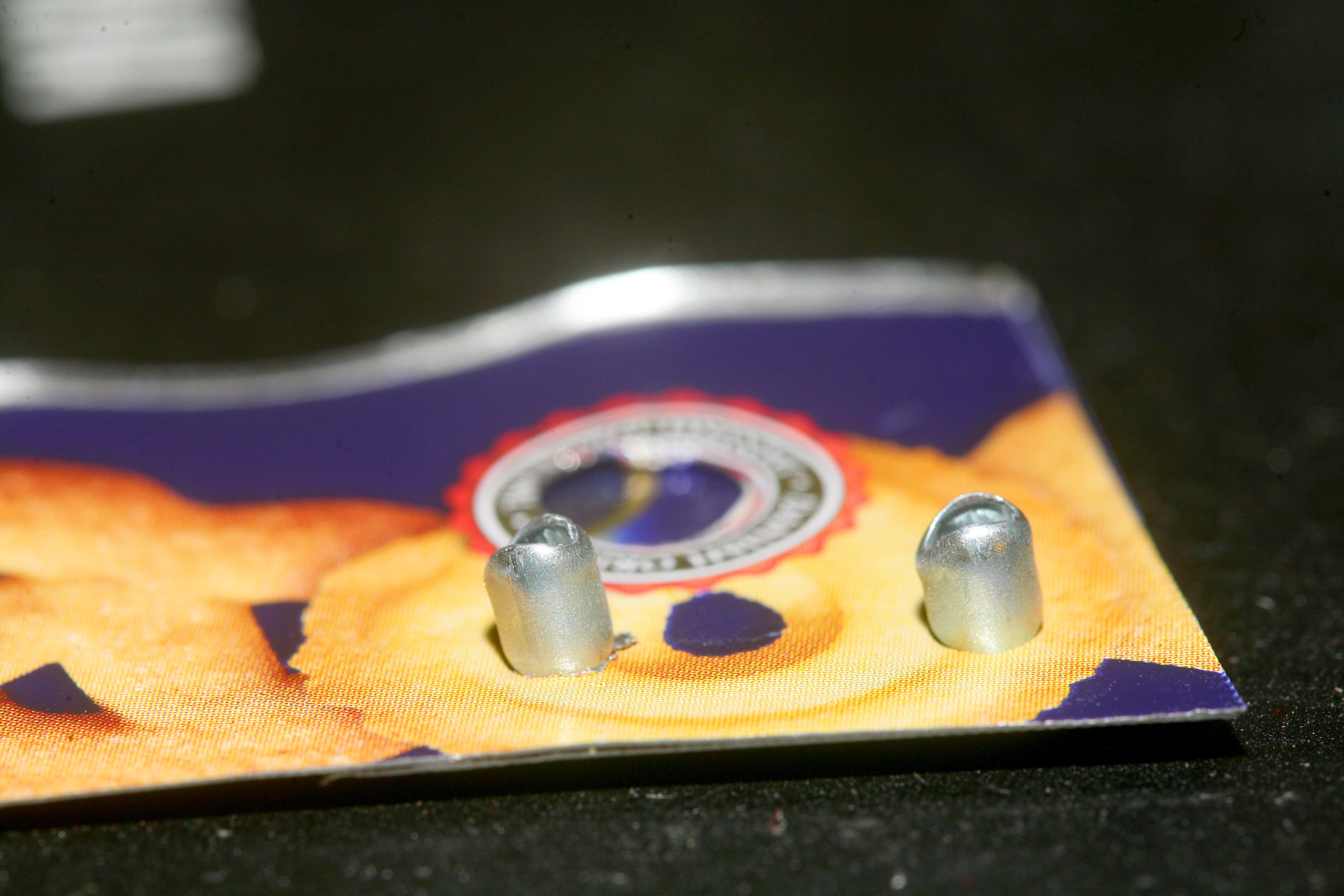
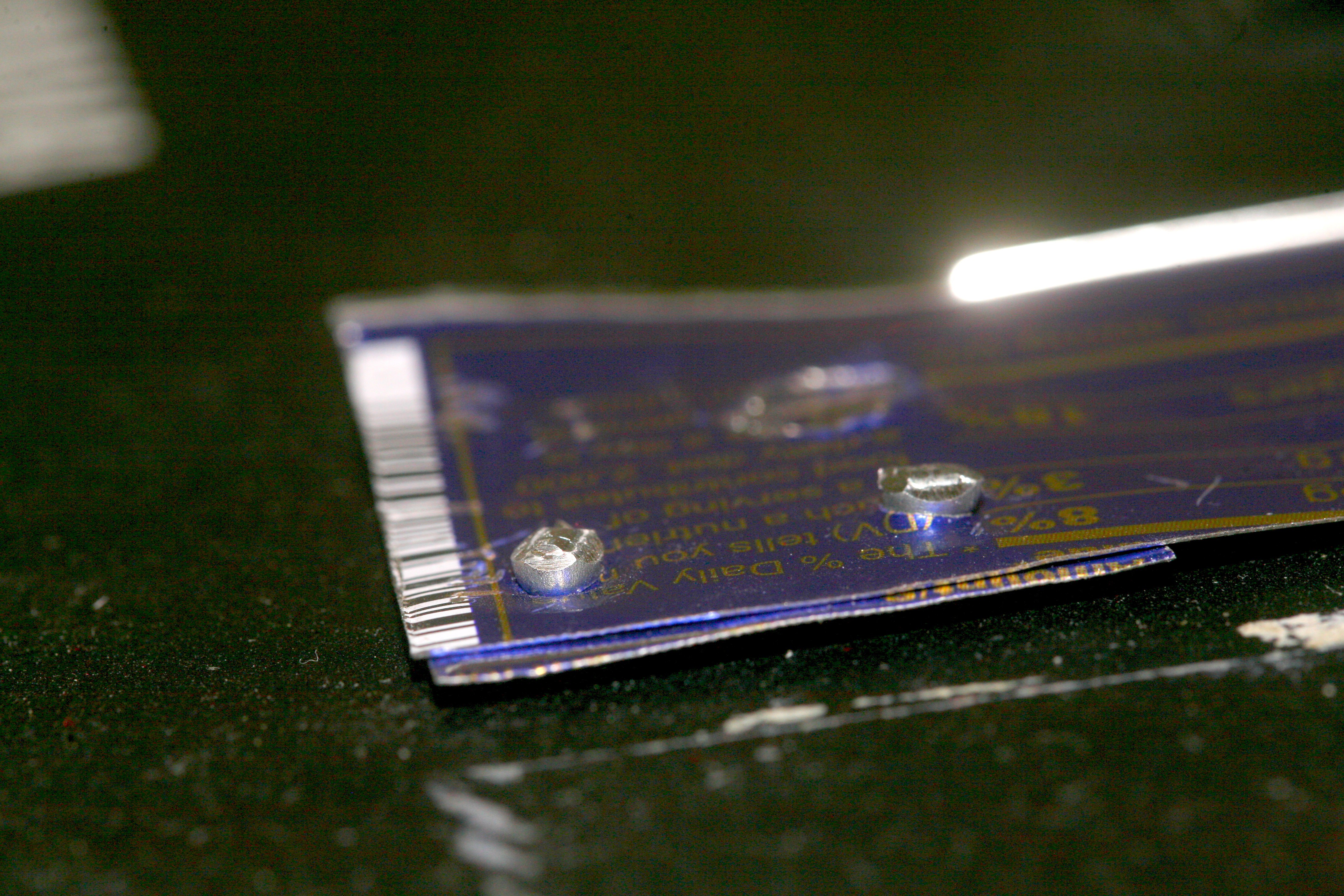
The staples were much easier to install & were flatter.
Drilling the 1/4" & 5/16" holes in 10mil steel also was problematic. They either need to be ground or thicker metal is needed.
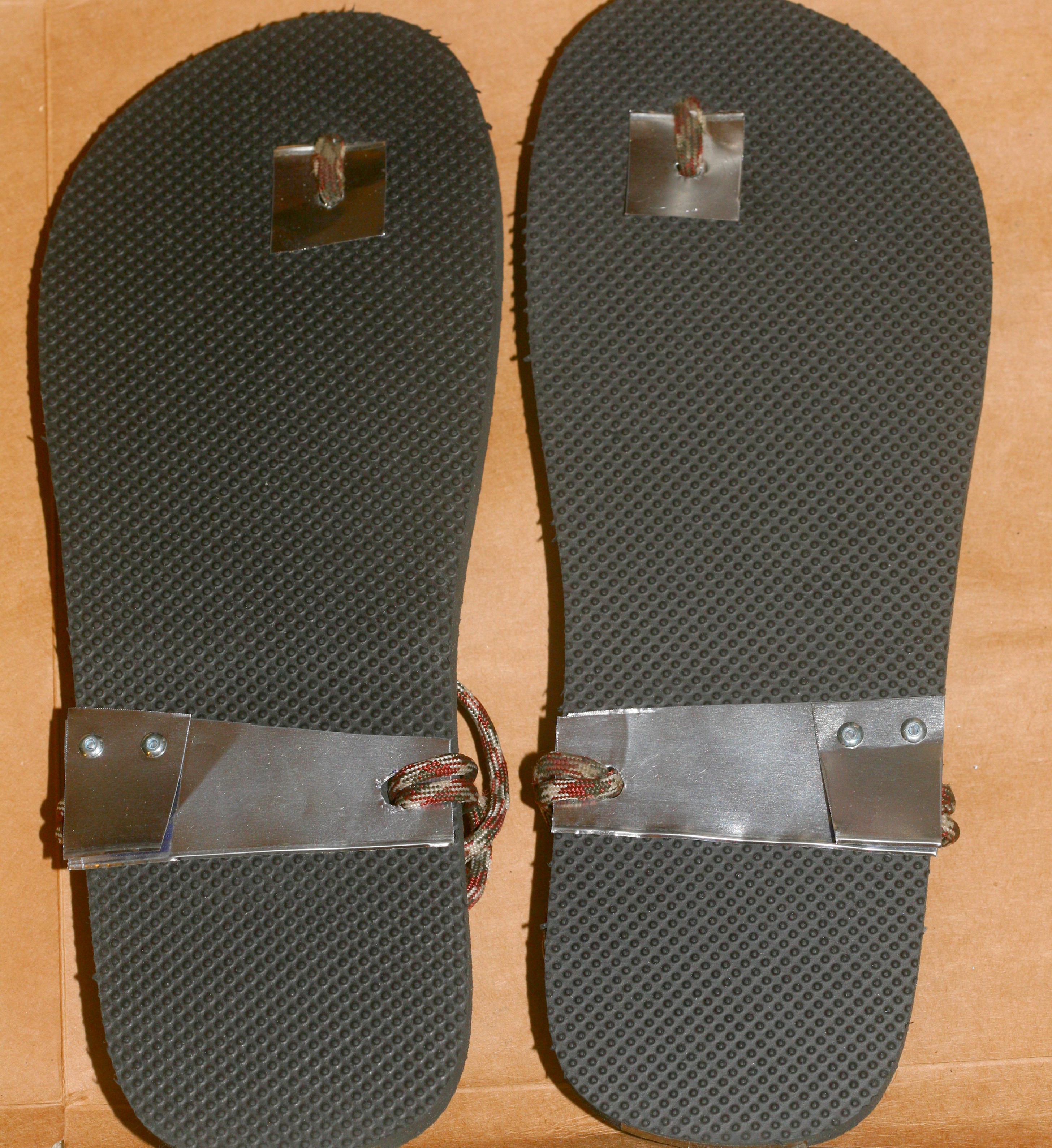
The final problem was the need for a spacer. The only reason the laces fit is because 10 mil steel can bend, while titanium can't. There's no way to adjust the laces, once they're installed. Thicker metal with rounded edges is a must. Metal may not be worth it. Teflon can go at least 50 miles.
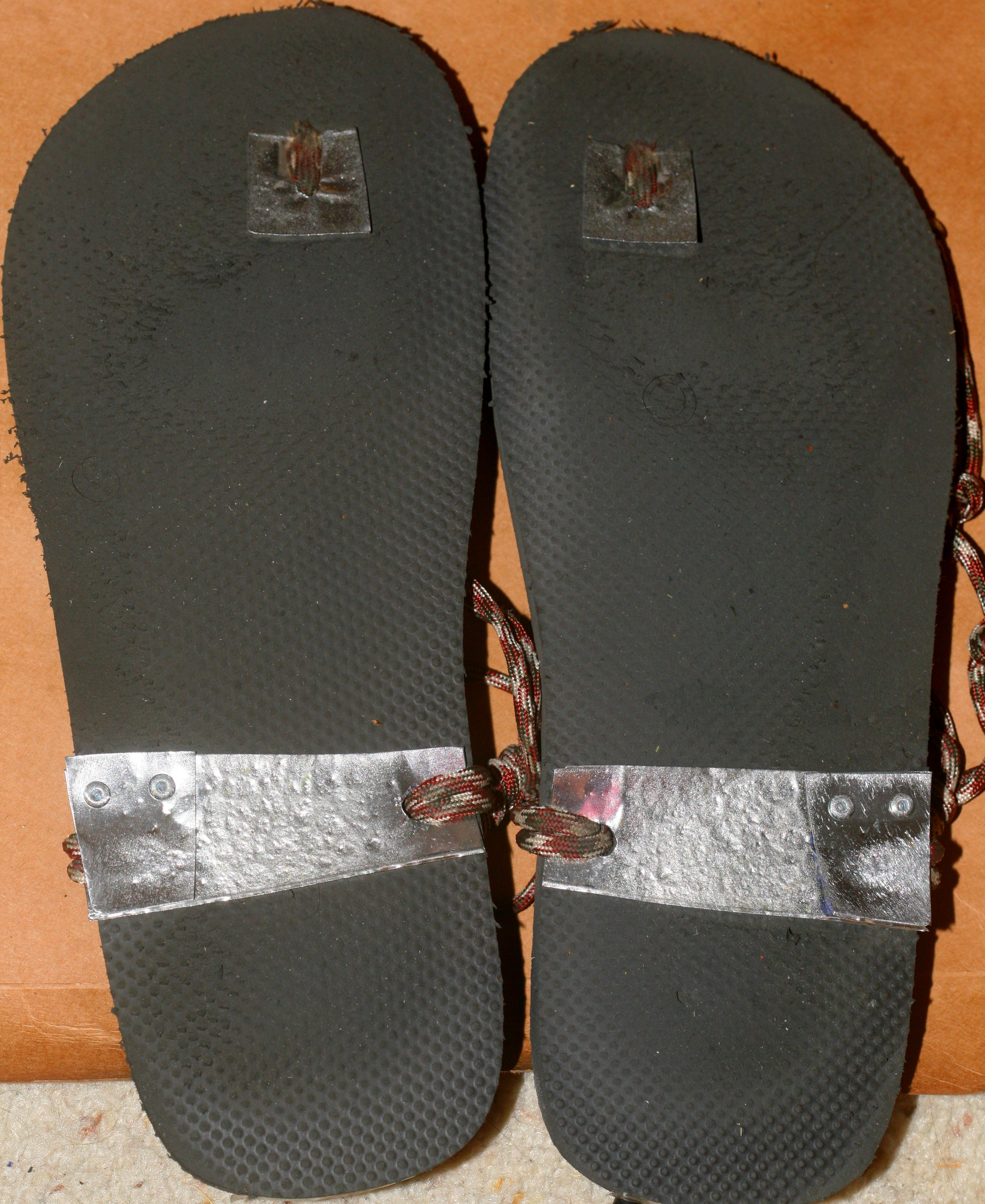
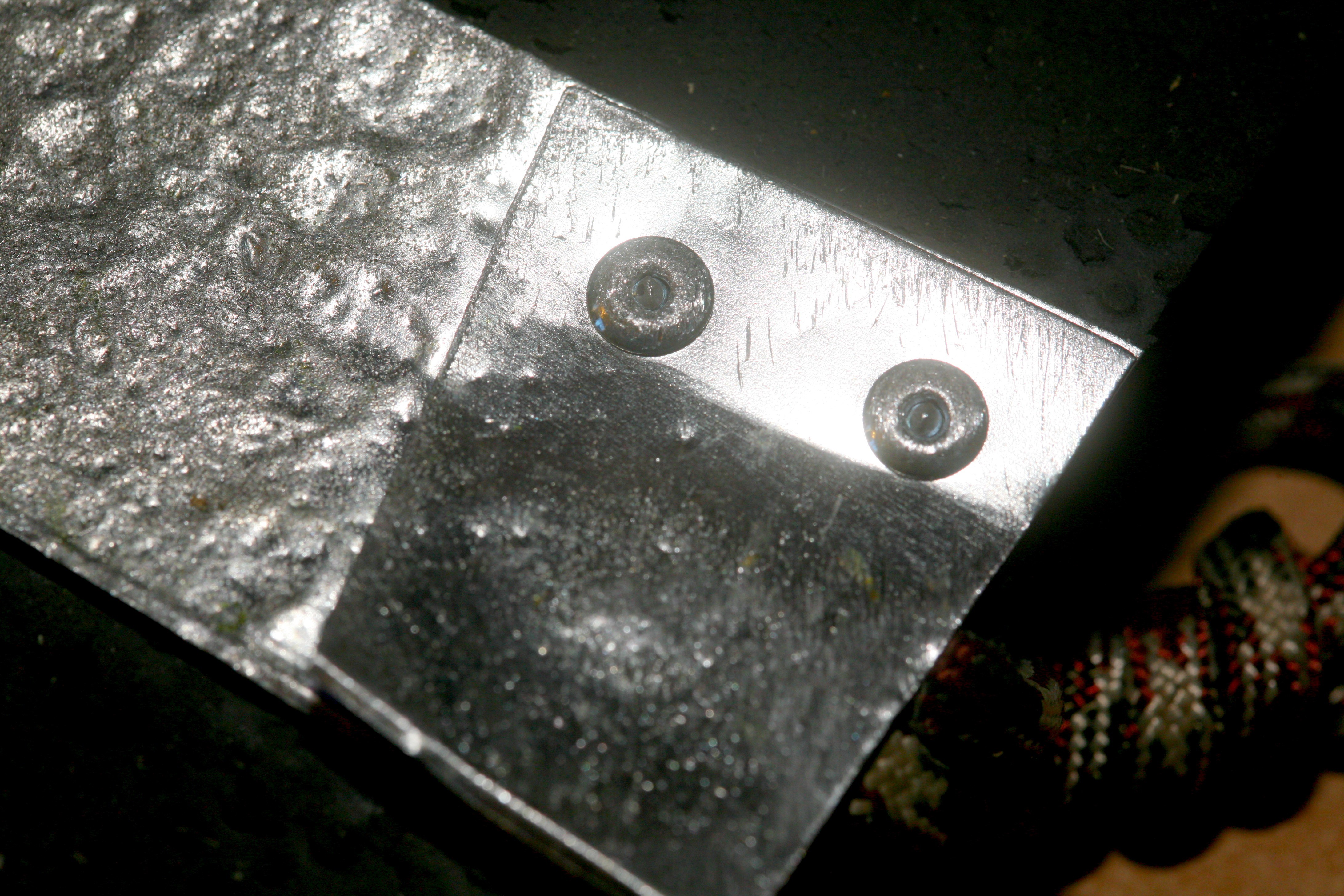
7 miles later, the steel looked worse than teflon after 50 miles & the rivets were also pretty chewed. It was a pretty convincing case for teflon & all its limitations.
Discussions
Become a Hackaday.io Member
Create an account to leave a comment. Already have an account? Log In.