I found a way of making a consistent gap between the contacts of a relay. Rather than have printed slots to hold relay contacts in place, instead I first position them close to the pole, held apart from it by a 0.4mm thickness of card, then glue them in place using quick set epoxy. In the photo below you can see the cardboard arches that fit over the pole nail while the glue is drying to keep the contacts at a fixed separation. The small blocks that the contacts sit on are located under the centre of gravity of the 20mm contact nails, so that the nails don't fall off before the glue dries.
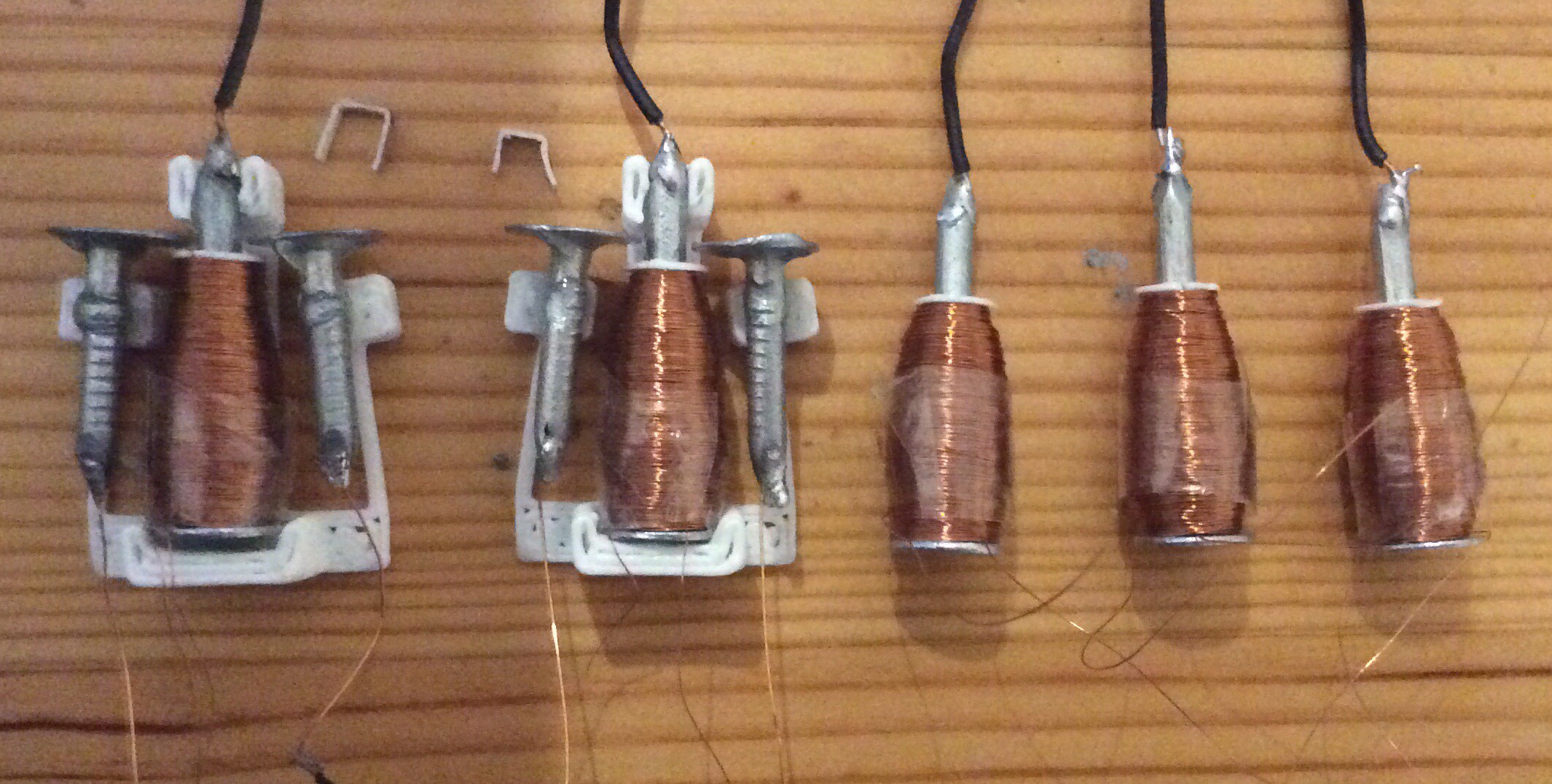
Both of these relays have a pull-in voltage of about 5 volts (one was 4.6 V, one was 5.3 V) and a drop-out voltage of about 1.5 volts (1.6 V and 1.3 V). Because the contacts are so close to the pole (compared with my previous similar relays) the force that pulls the contacts closed is greater, so I can use thicker flexible struts, which makes the relays less fragile.
It occurred to me recently that the zinc coating on these galvanised nails might be playing a role in keeping the dropout voltage higher than it would be otherwise. In armature relays, there is a thin non-magnetic separator between the armature and the core to prevent the relay staying on - if the armature and core are in direct contact then only a very small voltage is needed to keep the relay on, and it may remain on when it should be off. (In this note it is called a residual stud). I don't have one of these, but perhaps the thin layer of zinc helps? If so then the relay should become more prone to sticking on over time, if the zinc coating wears off with repeated closing and opening. It should be possible to test this hypothesis by looking for a galvanized and a non-galvanized nail of the same shape in the hardware shop.
Discussions
Become a Hackaday.io Member
Create an account to leave a comment. Already have an account? Log In.