The engraved Hylite technology
Hylite composite was originally developed to lighten body sheet metal in the automotive industry. Its ability to produce hinges, because of its polypropylene core, is cited by the manufacturer, but had not given rise to significant developments.
PP is very suitable for forming strong and durable live hinges, as shown by the millions of moulded boxes with integrated lids that are used everywhere. With the Hylite composite, such live hinges can be made in any complex geometry, by CNC engraving. By acting on the engraving profile, the mechanical characteristics of the hinge can be adjusted, for example the precision according to the bending stroke.
Moreover, the composite itself is very rigid, so that the deformable engraved areas are, by contrast, very precisely located. The articulated mechanisms thus created are thus precise, and without geometric uncertainty.
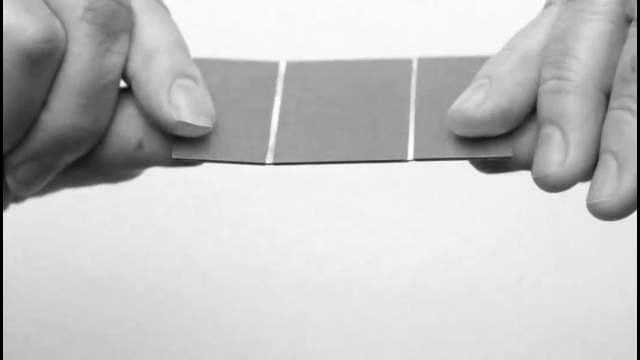
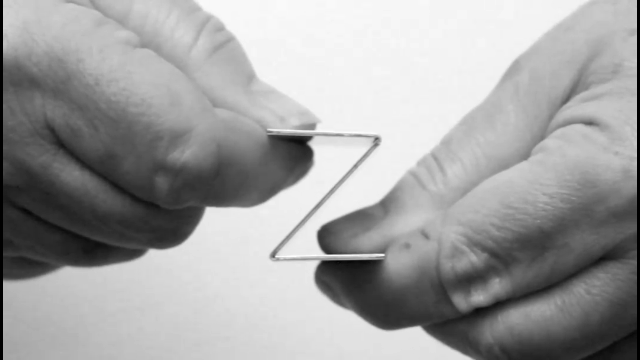
I have done some research, and many prototypes, to constitute a catalogue of engraving profiles adapted to different uses as stiffening folds, recesses, robust hinges capable of turning at 180°, or very precise hinges for limited strokes, etc.

It is this work that allows me to talk about a new technology, the engraved Hylite.
Durability of the engraved live hinges
I have performed extensive tests to ensure the durability of the live hinges, over more than 14 million bending cycles, without them being altered in any way. One of my prototypes has been running as a 3D printer for over two years with exactly the same mechanical precision. It's very reliable, and very strong! The tests are reported here:
A convincing application : Zatsit
The delta robot Zatsit is a first example entirely made up in this way. The technique of engraved Hylite makes it possible to obtain the totality of a very light delta mechanism, and geometrically very exact, starting from a simple sheet of Hylite. The result is extremely efficient, in terms of precision and repeatability of movements, resistance to vibrations, durability and ease of building.
Zatsit is just one example. This technique, consisting in engraving Hylite by CNC, to constitute technical or aesthetic, complex and multi-functional objects, is applicable everywhere.
Zatsit as a generic delta robot
Zatsit was designed as a universal robotic platform, on a linear delta architecture. Its main qualities are low cost, ease of construction, and performance in speed, repeatability, and accuracy of movement.
The holder is hollow, to be able to install any tool smaller than a cylinder of Ø66mm. The fixing device consists of three M3 screws, arranged at 120° on a Ø70mm circle.
Adapting, or hacking, an existing tool, or a specific device, is therefore very easy. It is generally sufficient to make an adaptation board, either from a Hylite disc proposed for this purpose, or in 3D-printing an ad-hoc plate.
The lower the mass of the effector, the better the robot's performance. With lightweight effectors, such as Pick & Place manipulators, or 3D print heads, speed and acceleration can be spectacular.
With heavier tools, acceleration must be reduced. The articulated mechanism is robust, but due to its relative flexibility it is not suitable for high forces, as in the case of milling. On the other hand, engraving is possible with a light spindle.
The screw mounting system is completed by a three-magnet system, useful for mounting light accessories, e.g. cameras, air diffusers, sensors, etc., in addition to fixed tools.
As an example, a tool for engraving glass by vibration/percussion was adapted very simply, by 3D-printing an adaptation...
Read more »
An extremely smart solution! Bravo!