In preparation for next week when we'll be working with custom boards, Sean and I improved our soldering skills. Who says a programmer and an MBA student can't solder like champs?
As it turns out, my issues in the past have been twofold:
1. an assumption that the electronics parts can't take sustained heat has led me to solder FAST and at low heat. This week, we've cranked the dial up to 750 F, and taken our time to pre-heat the pads as well as the electronic components,
and
2. using rosin-core solder incorrectly. How? By not clipping it off a few inches at a time. I've always unraveled the solder wire right from the spool, and after a few connections, it seemed to get harder and harder. As I've learned this week, it gets more difficult because the rosin is melting well into the spooled wire. Solution: clip a few inches off at a time.
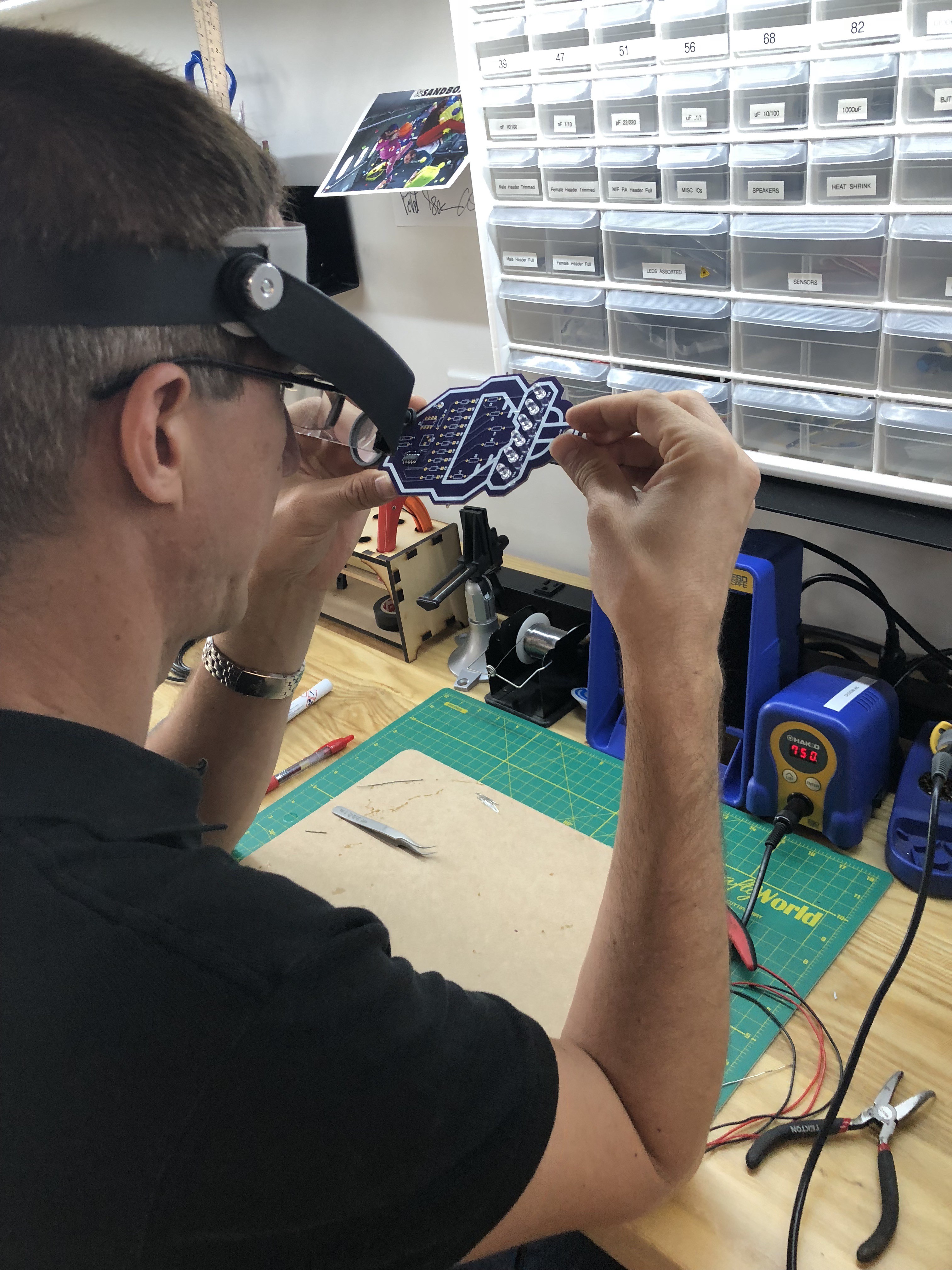
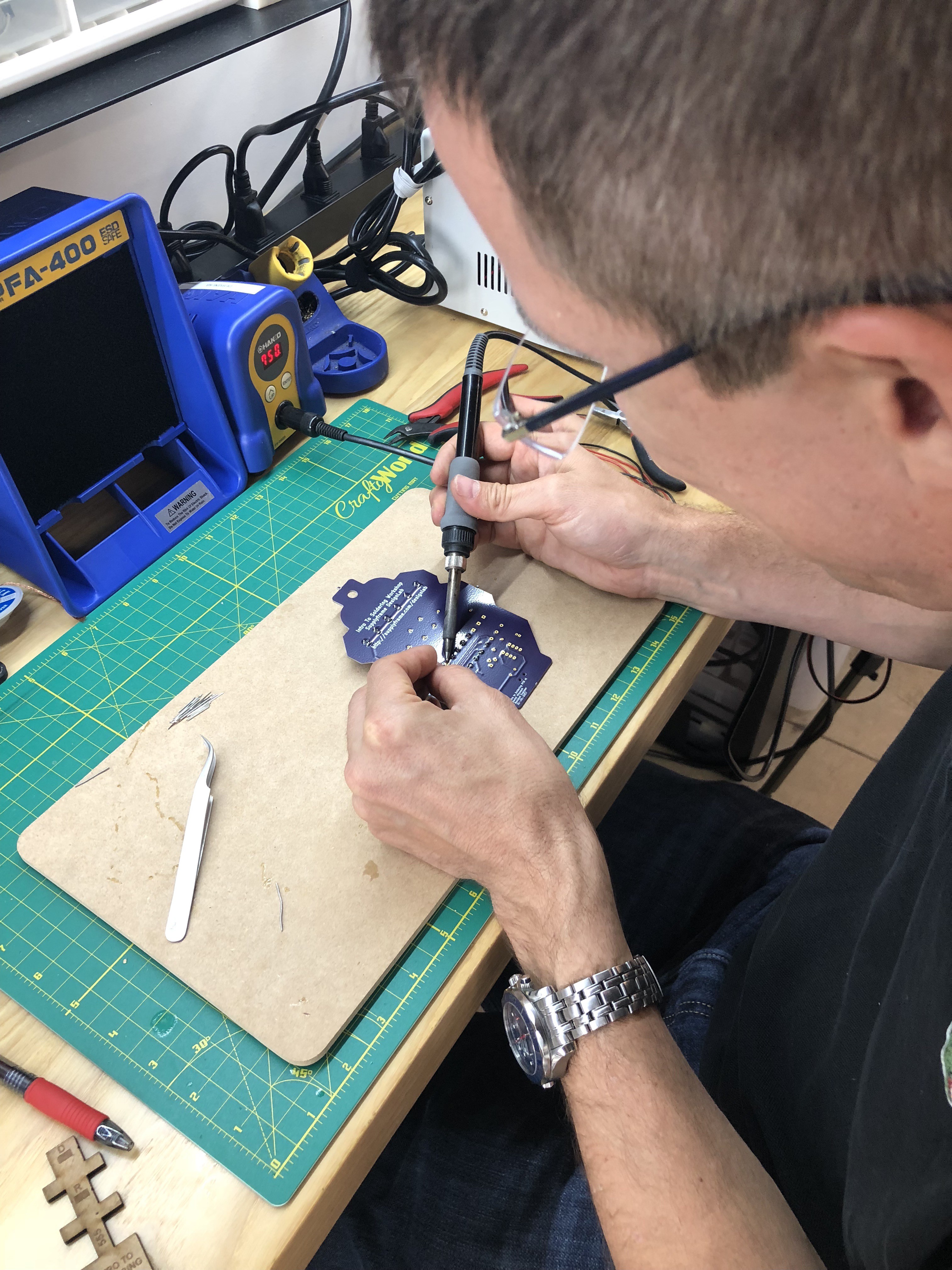
Discussions
Become a Hackaday.io Member
Create an account to leave a comment. Already have an account? Log In.
good to know the timing window, thanks!
Are you sure? yes | no
FYI: I usually set my iron at 500F(260C) for leaded solder and may be 550F(287C) for RoHS. Setting the iron too hot have a few issues: tip oxidation, FR4 degradation/delamination, pads/traces peeling off.
For leaded parts, you should be able to solder at 3-5 seconds per joint. (use thermal relief for pads to planes in your layout)
Are you sure? yes | no