The first iteration of this project didn't use planetary gears. Instead it used a combination of 2 : 1 and 5 : 1 straight gears on three independent shafts, plus a bevel gear to mount the stepper motor perpendicular to the axis (axes) of rotation.
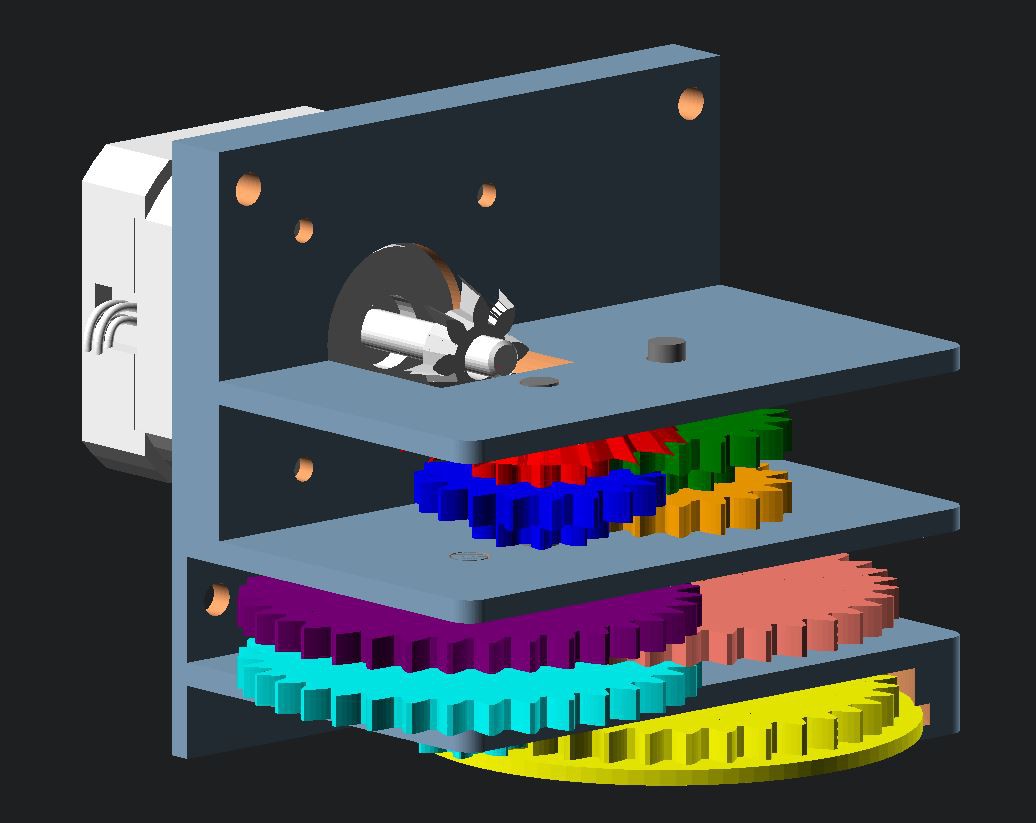
It was complicated and it never worked very well. The gears were tightly constrained in the walls but without much margin for error because of the multiple axes. They had a tendency to bind and there was a lot of lash, especially in the last 5 : 1 gear which was supposed to hold the camera. Inconsistent movement and non-axial motion are not good in an application where precision timing is key.
I don't remember what made me start thinking about planetary gears but once I had the thought it stuck and so far it's working out far better. There are more moving parts - 30 moving gears plus the planetary carriers feeding each successive stage, versus only nine moving gears in the original - but all those parts are much more tightly constrained in their range of motion.
Planetary gears are harder to reason about and calculate parameters for than coaxial meshed gears. The following resources helped a lot:
- Planetary Gear Simulator - simulates a parametric set of planetary gears in your browser. To simulate a fixed-ring gear set like in this project, set the "Ring Speed" slider to zero.
- Epicyclic Gearing on Wikipedia - the equations necessary to calculate important things like gear ratio from teeth count.
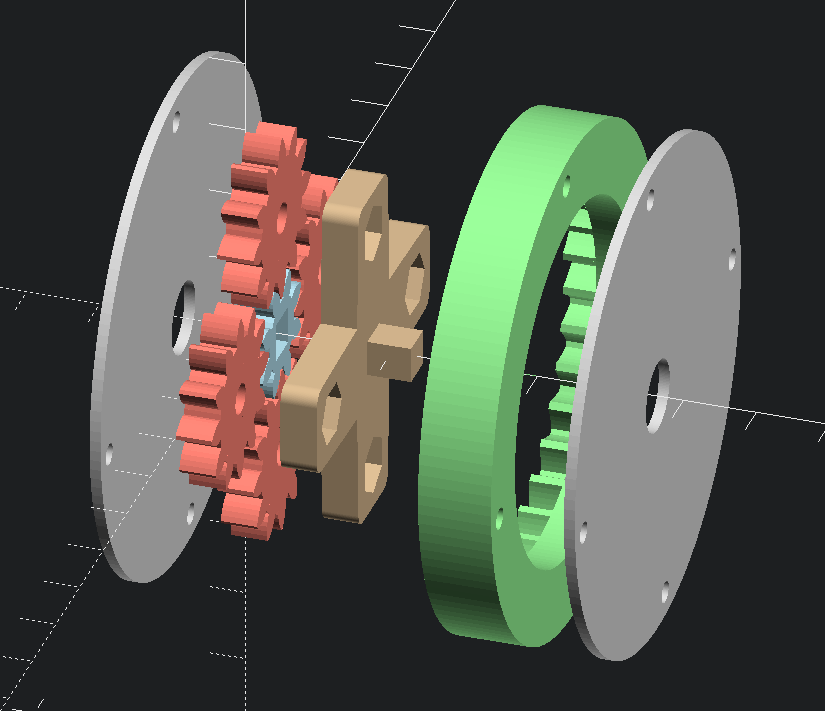
Discussions
Become a Hackaday.io Member
Create an account to leave a comment. Already have an account? Log In.