I both under-extruded and set values which were too large for backlash/clearance on my proof of concept.
The under-extrusion was mostly on purpose. I didn't need this to handle any kind of load, and under-extrusion of gears produces perfect profiles with far less thought.
However... the backlash/clearance values I used were from another project where I had also planned to intentionally over-extrude everything to ensure I had completely solid gears for my high-load application.
So the result is my gears don't mesh well and have massive clearance/backlash.
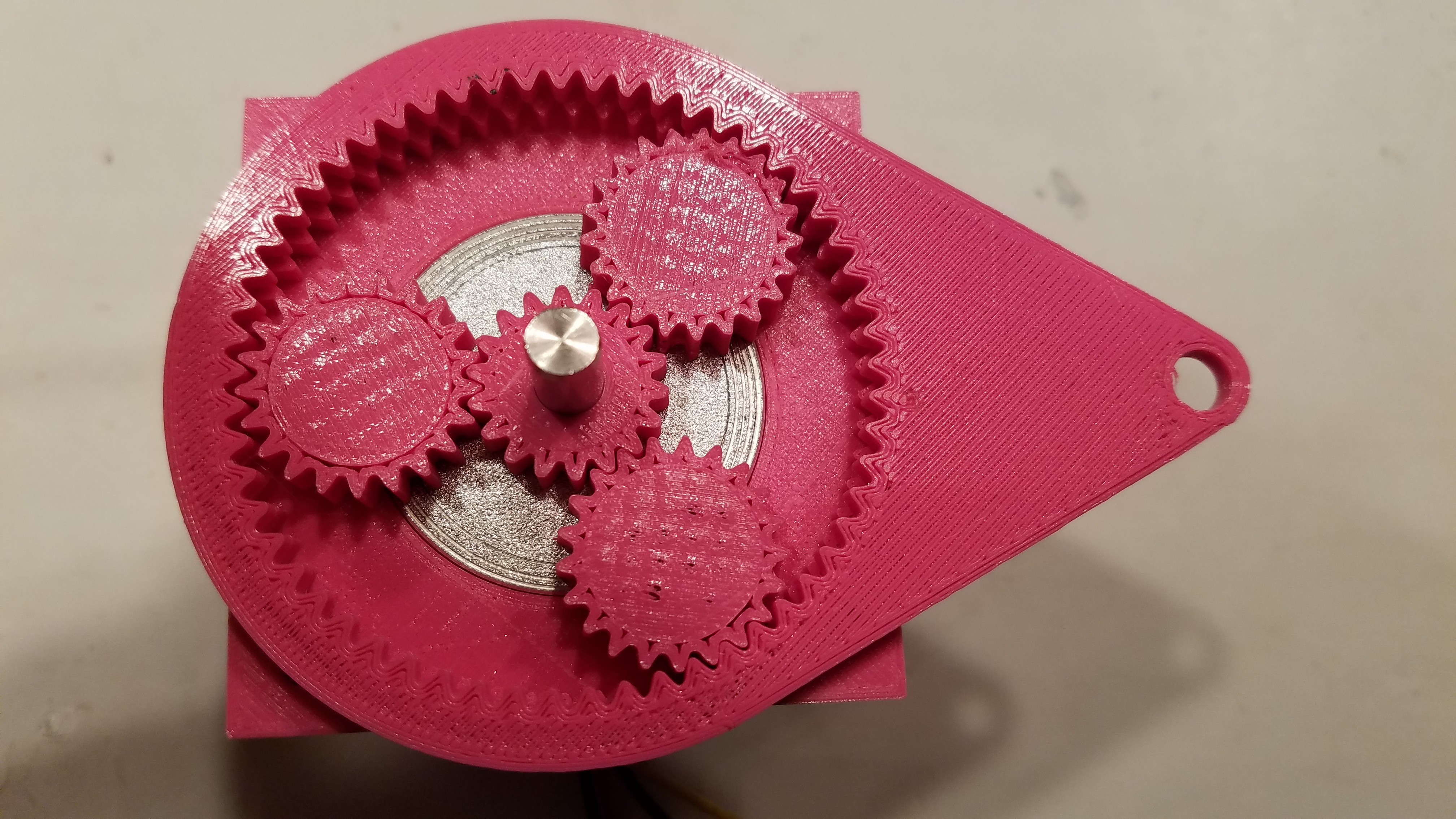
It does work though, but I won't do a video of it looking like this.
It probably didn't help that I also intentionally doubled the backlash value for the output gear to ensure it wouldn't bind as it will be running a less than perfect involute gear profile. I also increased the tooth pitch (which means smaller teeth) so I'm in uncharted territory for printing these. These teeth are smaller than I have ever printed at 0.4mm nozzle size.
So... 'doing the needful' as my co-workers of Indian descent like to say. :)
Discussions
Become a Hackaday.io Member
Create an account to leave a comment. Already have an account? Log In.