Challenge
If you use a laptop you may have found that using the touchpad involves placing your right hand, arm and shoulder in a different angle than your left. After some time this can lead to pain and even numbness due to nerve compression. An alternative is to use an external mouse but this also involves placing your right hand far from the keyboard and carries the same problems.
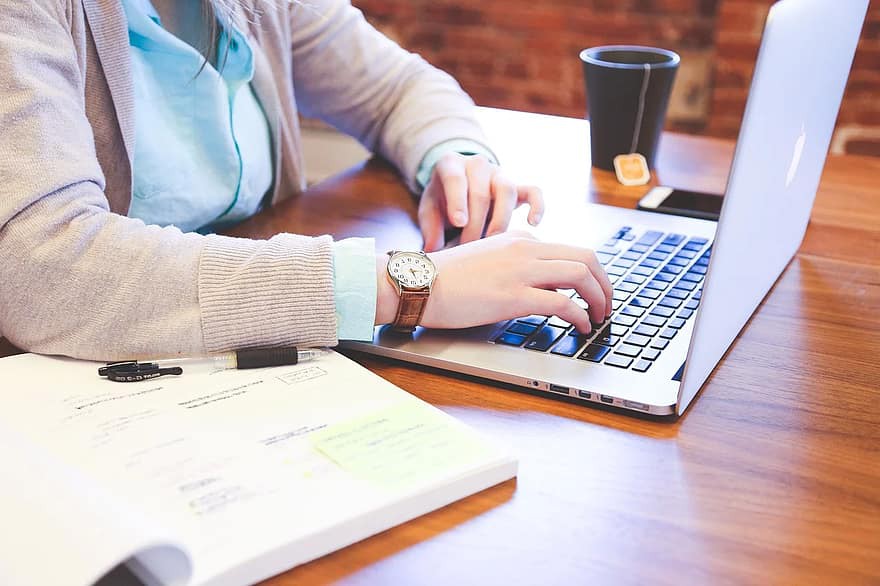
The main problem behind this, is that using your hand for pointer control gets in the way of maintaining a neutral and symmetric position on your keyboard, such as when you have your index fingers resting on the nubs of F and J keys.
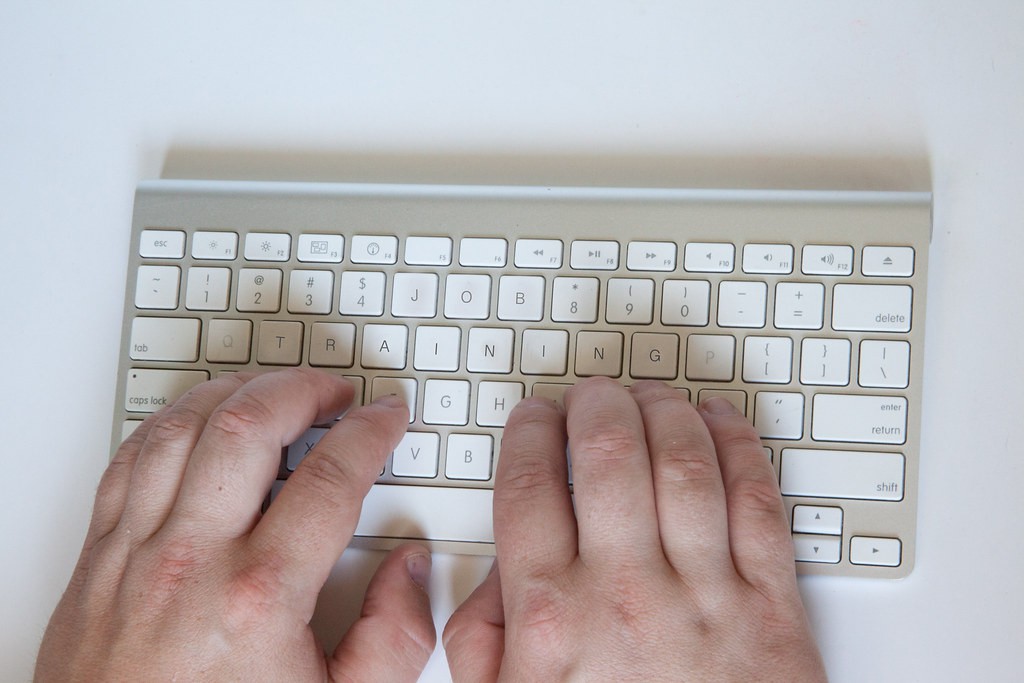
Besides the ergonomic aspect of this problem, a hand-controlled pointer wastes the extra dexterity available on your fingers: precise motion with a finger is easier than with your whole hand/arm.
In terms of accessibility, there are also limitations to current solutions: a universal mouse for left and right handed people implies either two different device models or ignoring the different grip from a left and right hand (mice are typically curved one way or the other).
Finally, there is an undeniable aspect related to individuals with limited mobility or dexterity, in case where full arm/hand use is not possible but thumb and index use is possible. While I have not addressed the problems of a particular ailment (this requires careful thought and consideration of a given disability and carries great responsibility to avoid false expectations), I believe it is possible to design a device that can be easily modified to conform to particular needs.
Proposed Solution
thumbMouse is designed around the BlackBerry trackpad family of sensors. These work exactly like the sensor found on optical mice, where images of the surface are analyzed directly in hardware to produce and estimation of planar motion based on the displacement of pixels on the image (this is usually called "optical flow"). The sensor simply reports an increment in X and Y coordinates. For the case of the BlackBerry trackpad, instead of sensing motion of the surface where you place your mouse it recognizes the motion of the finger over the sensor.
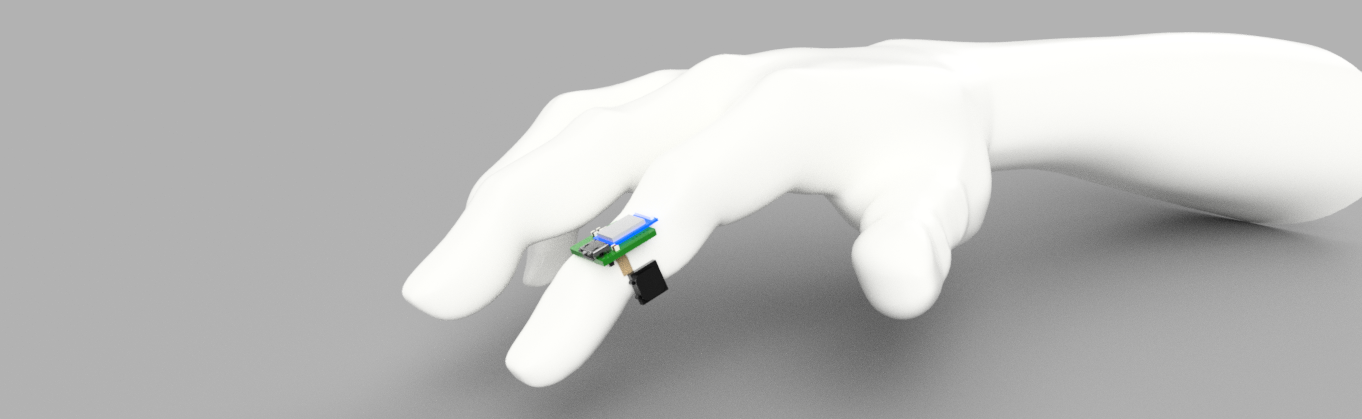
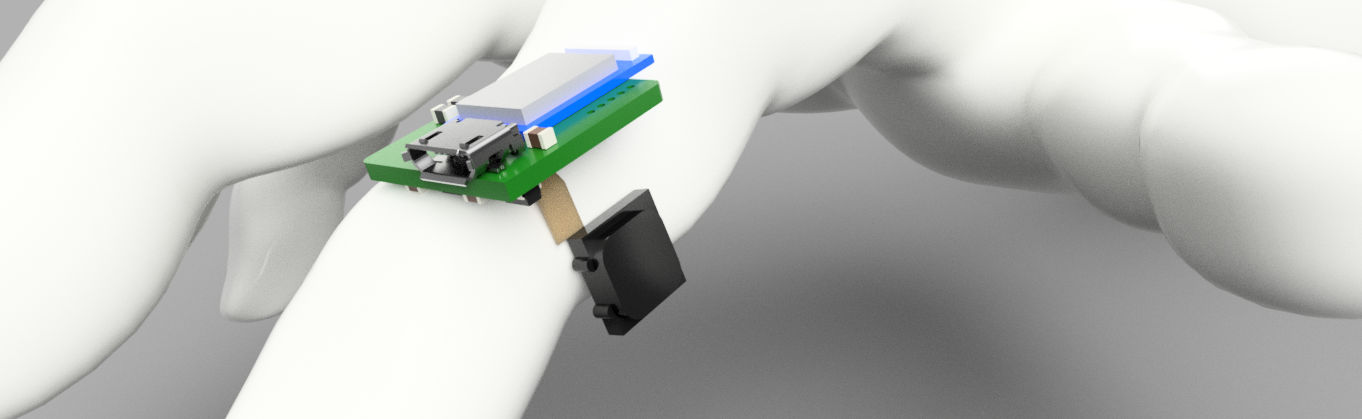
To provide a wireless solution using low-power approach, thumbMouse uses Bluetooth Low Energy (BLE) communication. The device itself acts as a Human Interface Device (HID) which is the standard protocol for mice and most input devices. This protocol is universally recognized not only by computers but also smartphones, regardless of its Operating System. To provide such a low-power and low-size solution, the nRF52832 chip (using a pre-existing module with chip antenna) is used.
As a wireless device requires its own power, thumbMouse also includes a battery and a USB based charging circuit.
To complete the device as a general purpose pointer, there's is support (via explicitly exposed PCB pads) for up to four I/O, as well as exposed 3.3V power and ground connections. As the trackpad itself embeds a push button in its back (you can press it and it will register the click), these extra I/O lines will mainly be used for adding other buttons found in mice such as left, right and middle click. However, given the ability of nRF chips to multiplex almost every pin to almost every peripheral, these inputs could be used to interface to analog sensors (including capacitive touch) or even I2C/SPI devices. This opens the possibility of extending the device in new ways, such as including an IMU.
The way to use thumbMouse is to wear it on your middle phalanx of your index finger and employ your thumb to operate the trackpad and thus control pointer motion. As the sensor has sufficient resolution, you can control it precisely. At the same time, by using pointer acceleration, a single swipe can make the pointer move across the entire screen with little effort.
Left/right/middle buttons can also be operated using your thumb or fingers from the other hand (for drag operations, for example). This operation allows...
Read more »
Hello, I came across this project searching for a adaptive equipment for people with disabilities looking for alternative input devices for a desktop computer. Is there a way I can contact you about this through email?