Roughly 6 possible designs have been made for returning the fingers back into an open position. There are a few others that have been used in previous prototypes but they were created more specific to the design requirements of those prototypes. So far, most of the prototypes have used an elastic cord on the back of the fingers to return them back into their open position. Elastic cords are fairly easy to obtain and assemble into the design, so it had been quite extensively. Main issues with elastic cords (dependant on material) is the long term durability in physical wear and loosing elasticity over time.
Roughly 6 designs were printed to test a number of different elastics and methods of opening fingers. 3 of the designs are elastic based, 2 are torsion bar based and 1 is a torsion spring based joint.
- 1mm elastic cord -
Used as a reference to compare with. - Rubber bands -
Functions well, however, finding a source for a specific sized elastic band can be difficult. Finger design doesn't have enough space to easily allow for a choice of different sized rubber bands. - Printed elastic -
Requires a bit more force to actuate. Easy to assembly as length is printed. Not suitable for stretching for long periods as it results in the material stretching. - Torsion TPU -
Fairly easy to print and assemble with the torsion bar printed in TPU. Actuation force is similar to the elastic cord design and returns to position when released. Joints are rather flexible and can be forced beyond its intended position which can result in the actuation cords being pulled further than intended. If there isn't slack in the system, the cords being pulled may result in damage. As the finger joints aren't particularly completely constrained, the load bearing capabilities aren't as high which results in greater actuation force. - Torsion nylon -
Doesn't require printing of the torsion bar but performs very similarly to the torsion bar printed in TPU with similar issues and effects. - Torsion spring -
Uses 0.4mm steel spring wire wrapped with 2 coils around the 3mm axle and inserted between the joints. Functions with similar actuation force as the rest of the test designs. Design would be fairly reliable if compared with longevity of the elastic designs. Main issue with torsion springs is the difficulty in sourcing and making through DIY methods. The cavity used also adds to print complexity which can make it hard to print.
Overall comparing the designs, I decided to settle on the elastic cord design as it provides the easiest design to source parts and assemble.
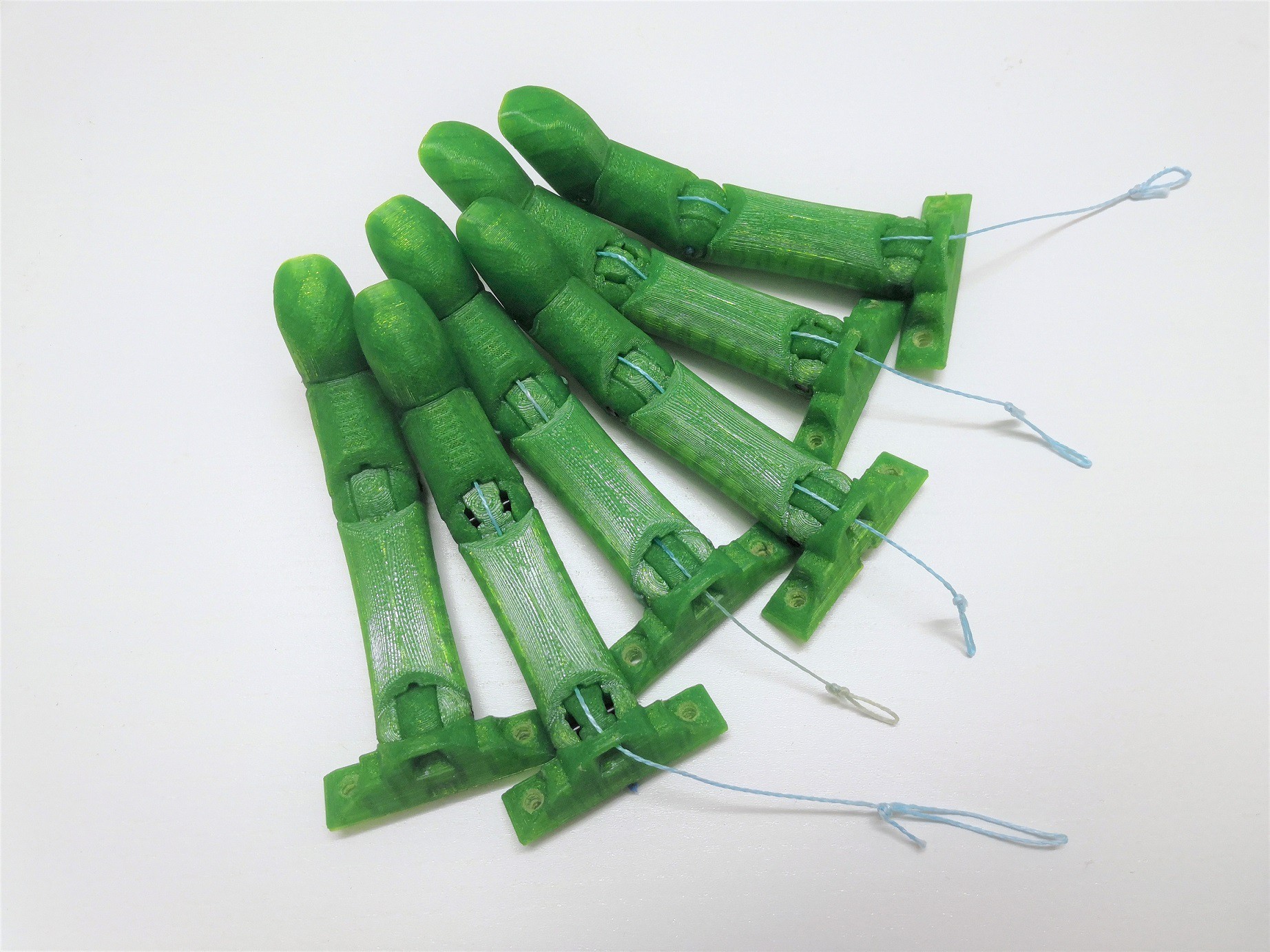
Discussions
Become a Hackaday.io Member
Create an account to leave a comment. Already have an account? Log In.