This project implements the function of a Dungeons and Dragons dice tower and dice using a retro digital multimeter with nixie tube display. The user selects a number of dice using the two digit thumb-wheel switches, then selects the dice type (2 sided, 4 sided, 6 sided, 8 sided, 10 sided, 12 sided, 20 sided, or 100 sided) using a rotary switch, and finally presses the roll button to get a result. The device applies the GNU AVR lib C pseudo random rand() function, calculates the result, and displays it on the nixie tube display. The user can then re-roll by pressing the roll button again, or change the count and/or dice and roll a different set of die. It's that simple to use.
This is a revision of the previous 1978 "Heathkit" D&D Digital Dice Tower project. In this revision, I'll attempt to simplify the build process, add some features, and subsequently update the list of components and source code.
The content I'll be adding here assumes you're at least familiar with the previous project. So if you haven't already, check out the link in the paragraph above.
Just like the original project, this is based on a 1975 Bell & Howell Digital Mulitmeter.
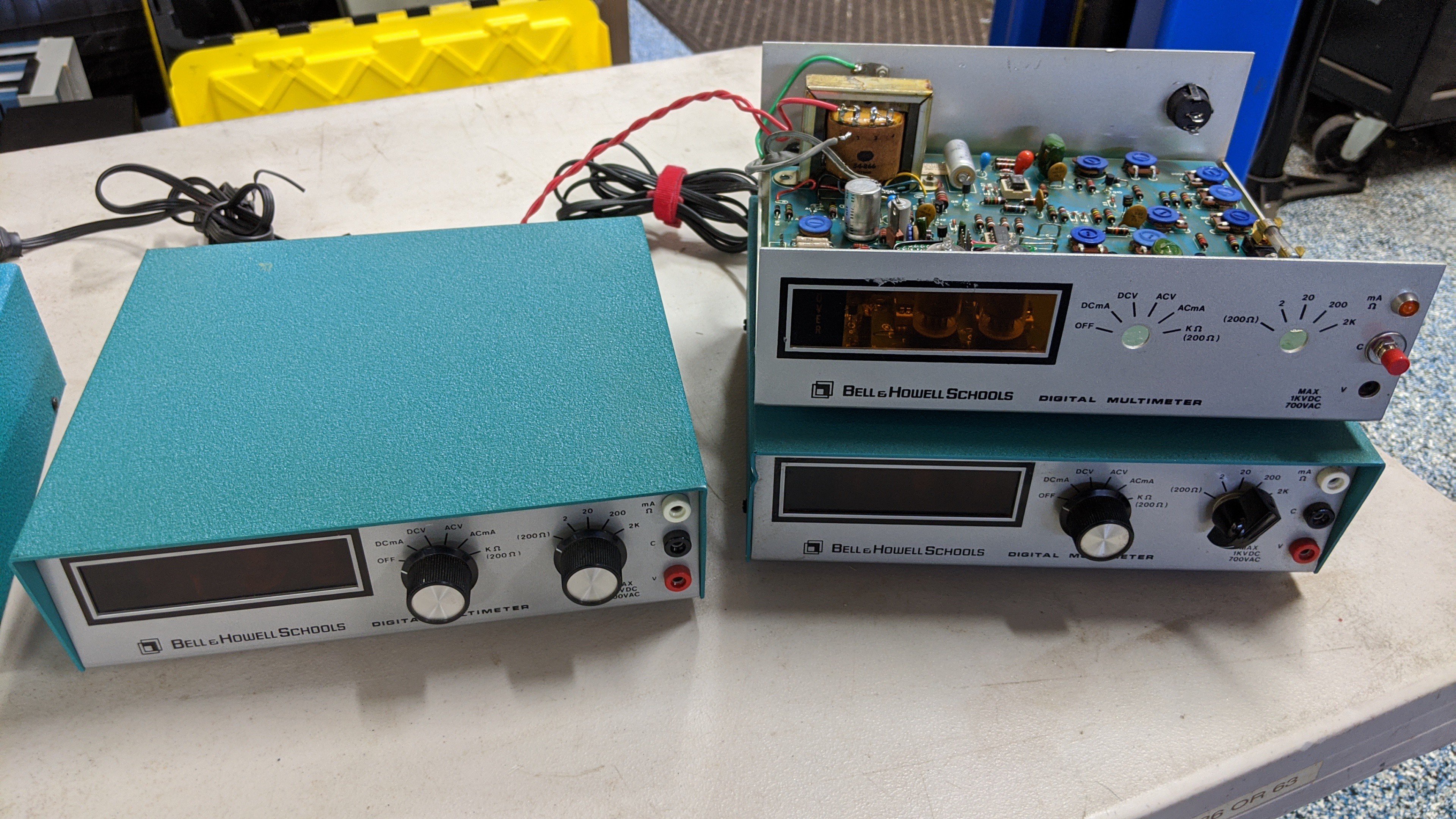
When I was thinking up the concept for the original project, several of my friends expressed interest. So as I often do when purchasing parts for a project I bought extras of everything so I would have plenty of spares and a couple extra to build for friends. Given the year it took to find time to work on this project, I've managed to collect enough parts to build 9-10 of these. So, I am motivated to figure out how to make these easier to build, add new features, and keep the original period look and feel. Besides if I am gonna build 5-10 of these, I'm definitely going to riff on this a little with each build. I'm not a machine that would happily stamp out 10 of these exactly like the original one.
So what are these new features you speak of?
- Simplified Case Modifications - I'm ditching the riveted faceplate for the new switches and button and reusing the existing holes and cutting/grinding the square hole for the thumbwheel switch directly in the case. The three holes for the banana jacks will be re-purposed for a panel mount LED, the roll button, and an access point to let the glorious new sounds out of the case. This will save a couple steps in the build process.
- New Controller Board Layout - The controller board will be soldered up to a breadboard style protoboard and connected to the original PCB through a separate board connected by a 10 pin IDC flat cable.
- New Thumbwheel Switch w/Stops - I'm trying a new 2 digit thumbwheel switch that has stops so I can configure a reasonable range of dice count the user can select.
- Sound and possibly voice - Adding a speaker, PCM sound functionality to the software, and possibly voice.
- New Microcontroller with more Flash memory - Need somewhere to store those PCM sound images.
- Result Status LED - This LED will light solid when the displayed value on the nixies is the result of the current dice count and type settings. If the settings are changed, the LED will pulse until a new roll is initiated.
- Additional I/O Board - The new status LED and speaker will need a board to serve as a mount point. I'll need to figure out how to mount this to the faceplate.
- Different Faceplate Graphics - I'm wanting to play with different types of faceplate graphics. I don't want two of these dice towers to look exactly the same. For this next iteration, I'm going with classic plastic embossed labels to give it that 70's home built look. In another iteration, I'd like to try a toner transfer process. I've had poor luck with that in past and I like to figure out how to make that work better. Going to try an acetone soak with pressure for the transfer.
With that, it's time to get started on this new spin. Look for updates soon.
That chevron rotary knob, white paint in the groove, fastening screw at the end, is absolutely of that past era. Brings back memories.