@Steven.Carr has been happily milling out PC boards and laser cut experiments on his very nice equipment. I was growing envious as I sit here airwiring stuff.
Four years later, I finally got around to building the PCB milling attachment for #Arcus-3D-M2 - Mixed material filament printer . I always had a couple extra AL end effectors and 12 extra mag balls for exactly this purpose. Necessity is your mother.
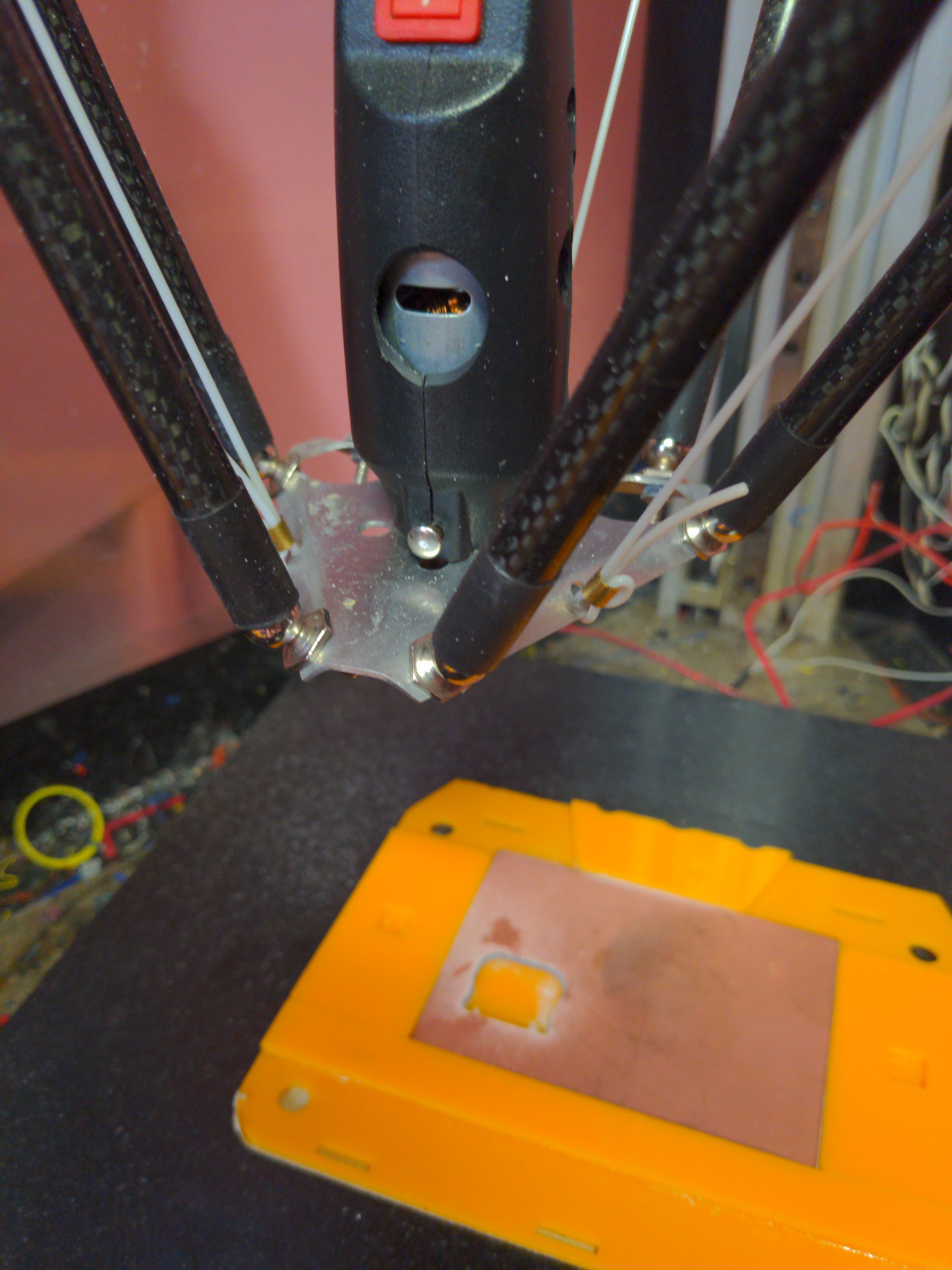
Took the HF Moto tool I had and machined a full depth collet for it to specifically fit the PCB milling bits I have been carrying around in my toolbox for the last 4 years. The normal collets for this tool when presented with any side loading wear out in about 5 minutes as they are relatively soft brass, and only hold the first 3mm of the bit.
I also drilled massive holes in the housing to try to cool the motor a little better so it doesn't melt its mounts when running continuously.
This little motor does actually have *one* nice bearing in it, and carbon block brushes. It may actually do okay for a while now.
Anyway... The results.
This part is the PCB that holds the two optical encoders we are using which allow us to turn DC motors (a Ford F150 wiper motor) into proper servos for about $4 in parts.
I don't know if it is intended to be offset like that or not. I assume so because I actually ran it twice as I got the depth wrong the first time.
I just took the gcode that @Steven.Carr ran on his Tormach (envy) and stripped out all those unnecessary things like tool changer commands and actual spindle speed speed control, and reduced the depth of the drill cycle to just give me the centers by relocating Z=0 with a G92 before it.
Then again using a Tormach to mill PCB's is akin to using a pulse jet engine to spray sanitizer. Yes, I am referencing you ACME Creation Labs.
And.. a video.
I was pretty conservative with my feedrates as I had no idea how this would do.
Steven ran this at F3.0. I turned that down to F1.0, but ended up running the trace etching at F3.0 via feed rate override, but then dropping it to F0.6 for the final pass cutting full depth on the cutout.
I also discovered my 3D printer UI does not properly handle running in G20. Imperial coordinate systems FTW. I am choosing not to fix that.
Discussions
Become a Hackaday.io Member
Create an account to leave a comment. Already have an account? Log In.