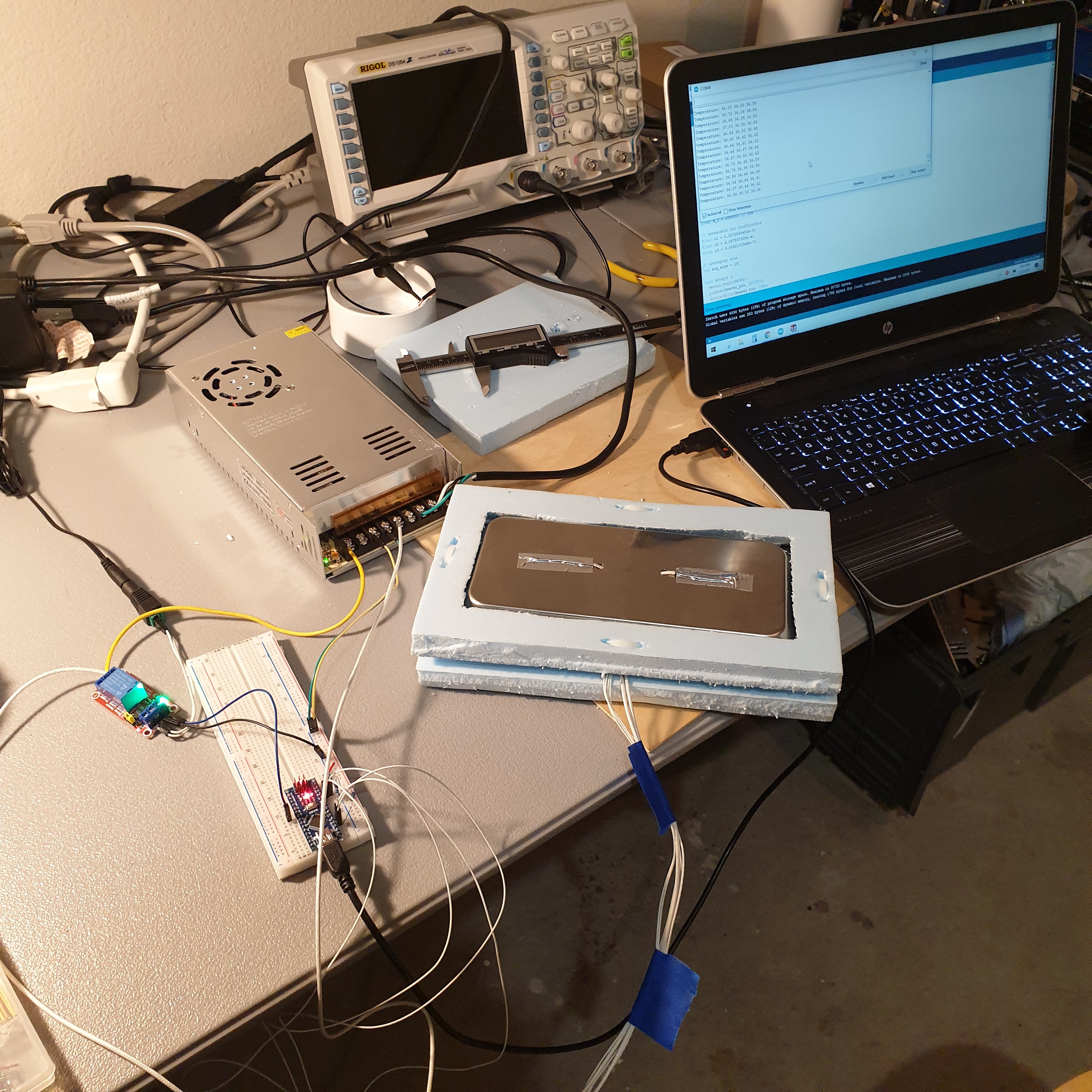
The test setup depicted in the image is representative of one of the hot plates of the two hot plate IV fluid warmer design that is being evaluated. A 100W heater silicone pad is sandwiched between a layer of polystyrene insulation foam and a stainless steel medical tray. Two 100kOhm thermistors are fed through holes in the stainless steel tray and mounted to the side of the tray opposite the heater with aluminum tape. As part of the two hot plate IV fluid warmer design, the IV tubing will be in direct contact with the hot plate on the same side as the thermistors.
The 100W silicone heater pad and two 100kOhm thermistors are operating successfully with a bang-bang feedback controller. The controller is programmed to turn on the heater if the device is below 36degC and turn it off when the device reaches 36.25degC. Cooling is achieved by natural convection for this test setup. Because the heater and thermistors are on opposite sides of the stainless steel medical tray, the thermistors detect a temperature change about four seconds after the heater has been turned on. After the heater shuts off at 36.25degC, it continues to transfer heat to the hot plate. The hot plate starts to cool down after reaching a maximum temperature near 38degC. Since the heater and stainless steel tray are sandwiched between two layers of polystyrene, the lowest thermal resistance path is through the stainless steel plate out to ambient air.
It was not my original intention to implement a bang-bang controller, but I am now considering it based on the potential cost savings and simplicity. Up until this point, I have been expecting to implement a PID control algorithm with a 3D printer heater, power FET module. In total, the power FET modules are about $4 USD (5% of total material cost) more expensive than the relay modules needed for bang-bang control. It wasn't until I realized that the power FET modules I had bought require a minimum input signal of around 7.5V (Arduino only outputs a 5V PWM signal) that I considered bang-bang control just to get something working. Bang-bang control has the disadvantage of always drawing max current of around 16.6A combined for both 100W, 12V heaters. Even so, I am looking forward to testing bang-bang control with the two heater plate prototype.
The next step is to complete the two heater plate proof-of-concept prototype and test it with the fluid temperature rise test setup that I described in the last project log. All materials have arrived and the majority of the fabrication is already done. It will take about two to three more evenings to get everything setup and the first set of performance data collected.
Discussions
Become a Hackaday.io Member
Create an account to leave a comment. Already have an account? Log In.