Lions started etching boards in May 2009. Lions have always used single sided, photoresist coated copper boards, 1/32" thick, from MG Chemicals.
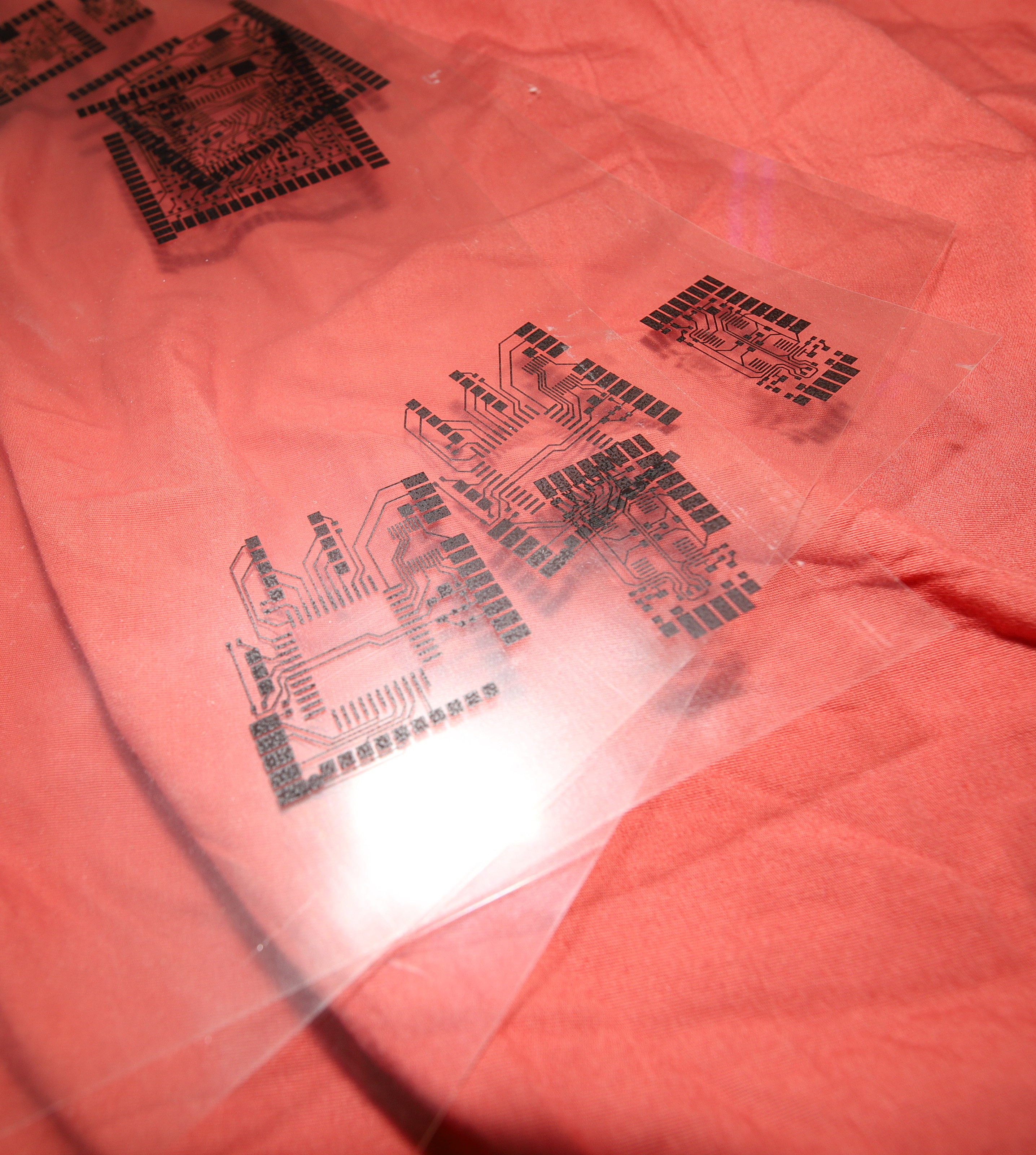
Note the general design of a board is a mane chip in the middle with pads around the edge of the board. The pads on the edge of the board are .2x.1" & extend off the edge of the board so no material is wasted when it could be used for solderable surface.
Flip the circuit horizontally in your paint program. Print 2 copies of the circuit on 2 transparencies, at least 1200 dpi. The 2 transparencies will be stacked to block enough light. Sadly, laser printers are more accurate in the horizontal direction than the vertical direction, so fine traces & critical alignments have to be aligned in the horizontal direction. Multiple copies of a board have to be placed horizontally.
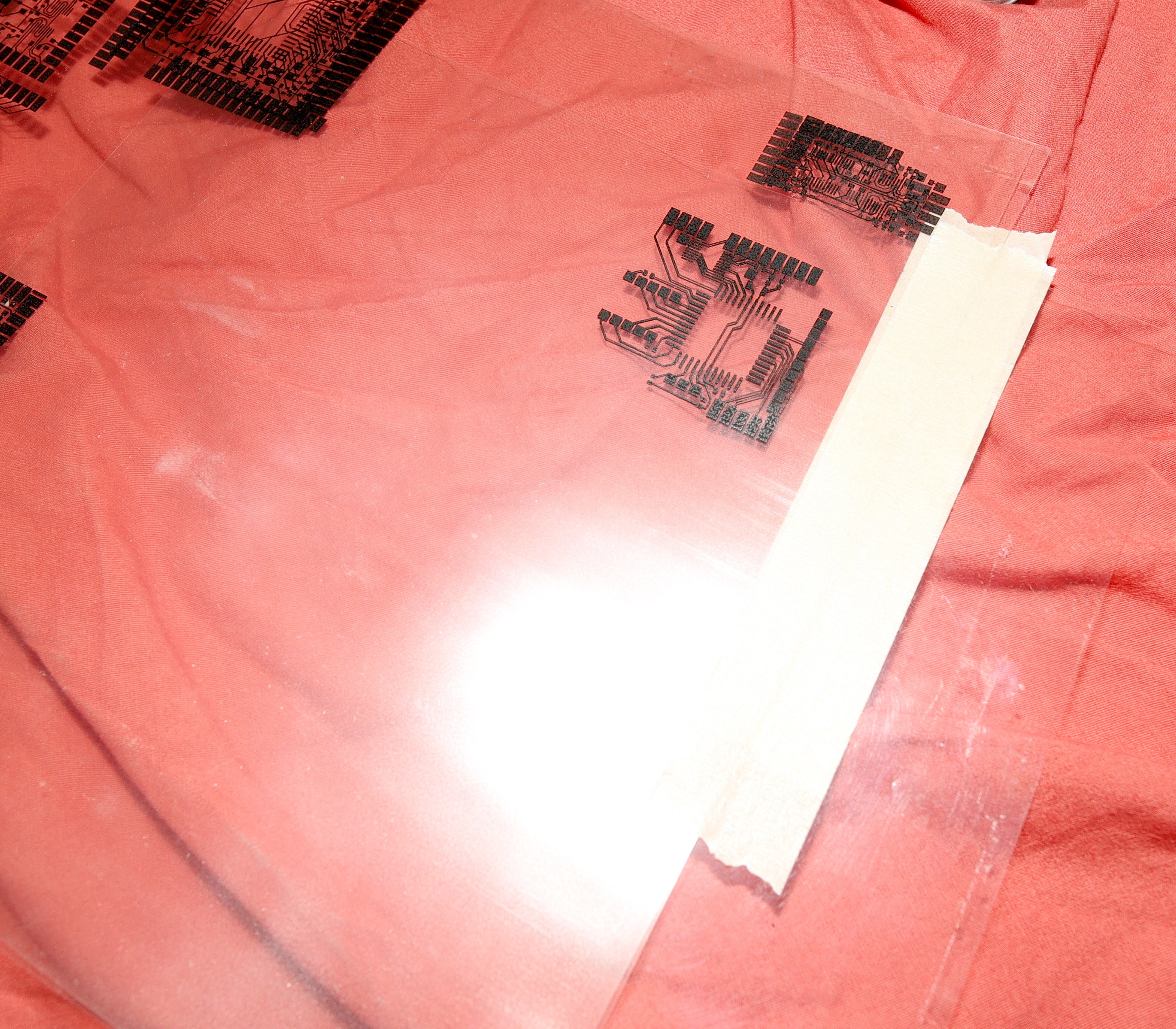
Align & tape them on top of a 3rd transparency with the toner facing up.
Cut out the required material with margin for grabbing it & making mistakes.
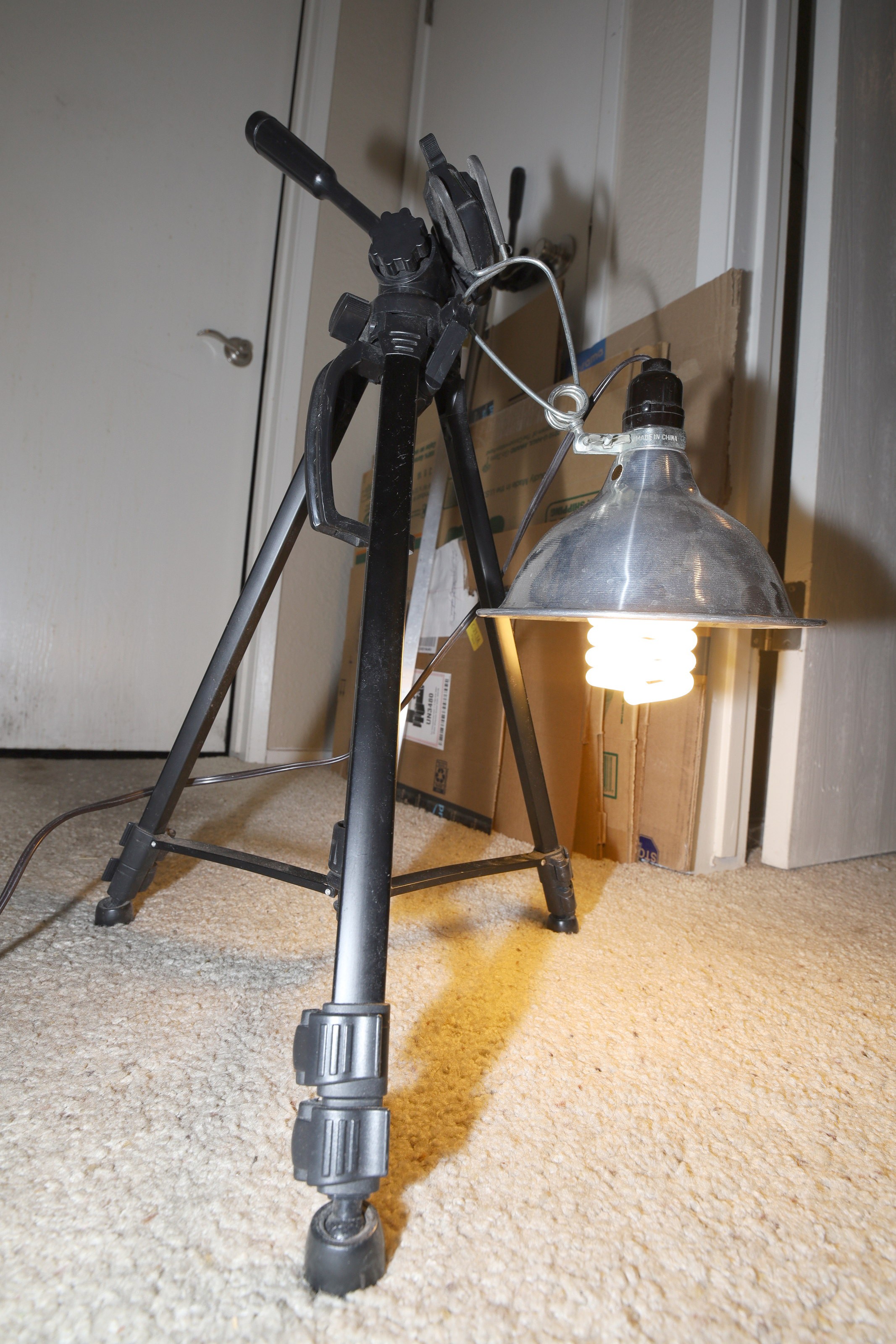
Assemble a minimum 23W fluorescent light 1 ft off the floor.
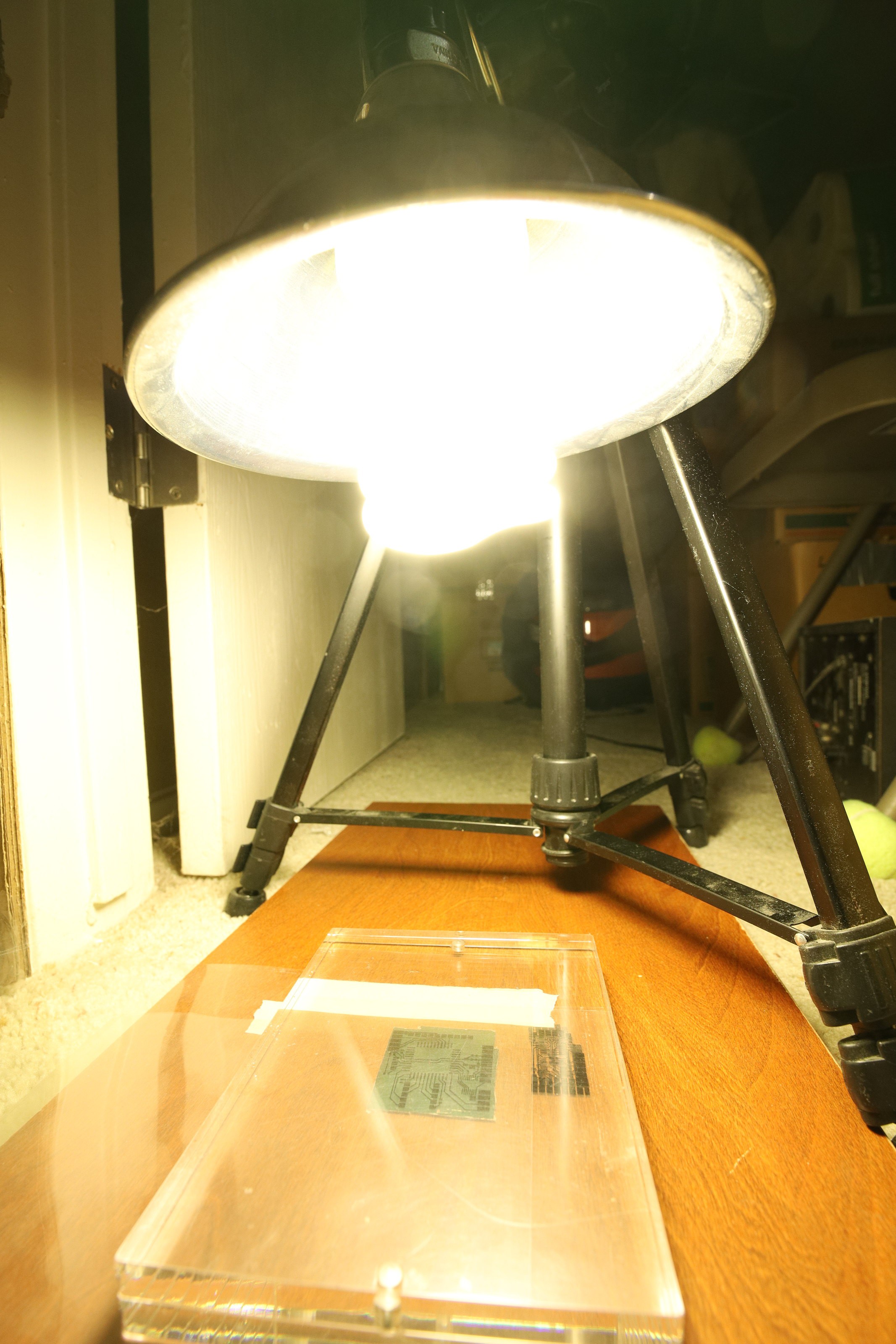
Stack the board under the transparencies & a weighted transparent cover. Expose to fluorescent light for 25 minutes. Over exposing is better than under exposing.
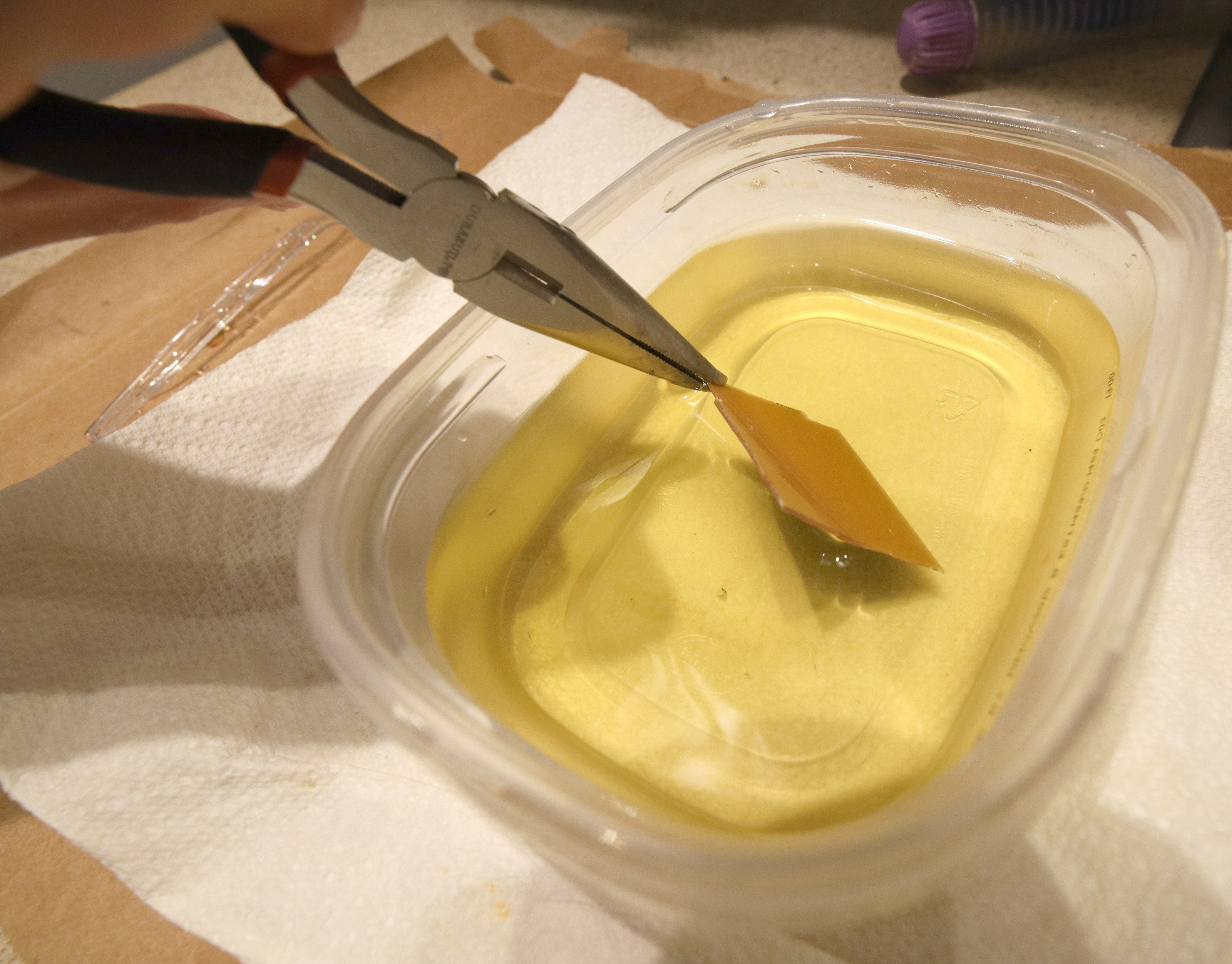
Put on your lab coat & old clothing. Use PC board pliers to stir the board in 10% hair clog remover until the exposed photoresist is gone. The board must be upside down as much as possible to avoid getting exposed. Take it out frequently to examine how much has been dissolved.
For better results, tilt the board so the photoresist faces the direction of motion. The NaOH should press against the photoresist, pushing away the dissolved material. Without the pressing motion, the dissolved photoresist will pool on top of the circuit, making it hard to judge how much has been dissolved.
Then rinse in water. Lions have obtained NaOH as hair clog remover. Draino formulations don't have enough NaOH to do the job.
The concentration of NaOH is a fiddly detail. Slightly too much & it'll instantly burn away all the photoresist. Slightly too little & it won't develop anything at all. Lions usually pour just enough NaOH to coat 1/2 the bottom of the tupperware & fill the tupperware 1" deep with water. If it doesn't develop, add small amounts of NaOH. It's very important to stir the NaOH.
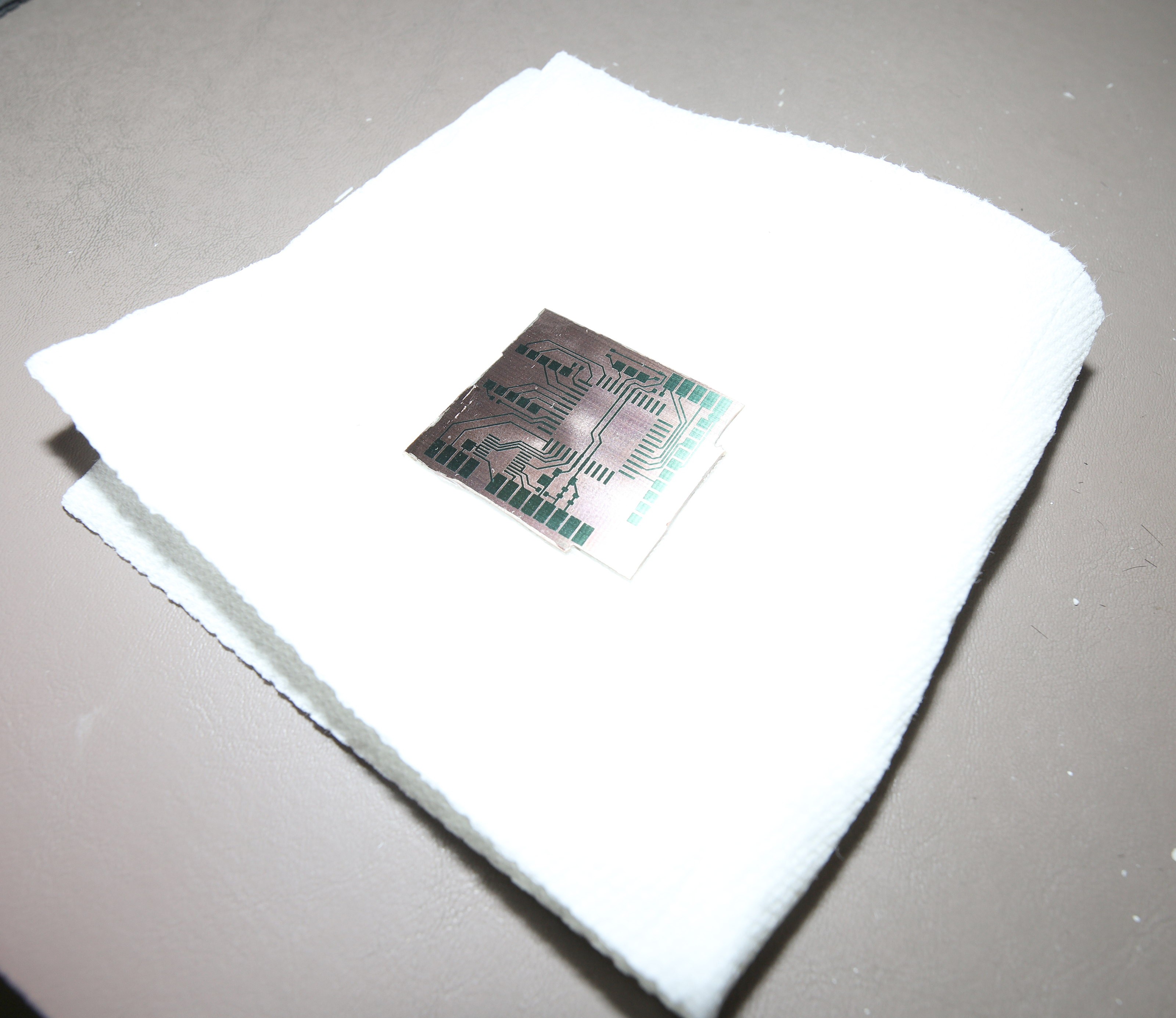
Dry out the board & fix errors with a sharpie. The board must be dry before etching.
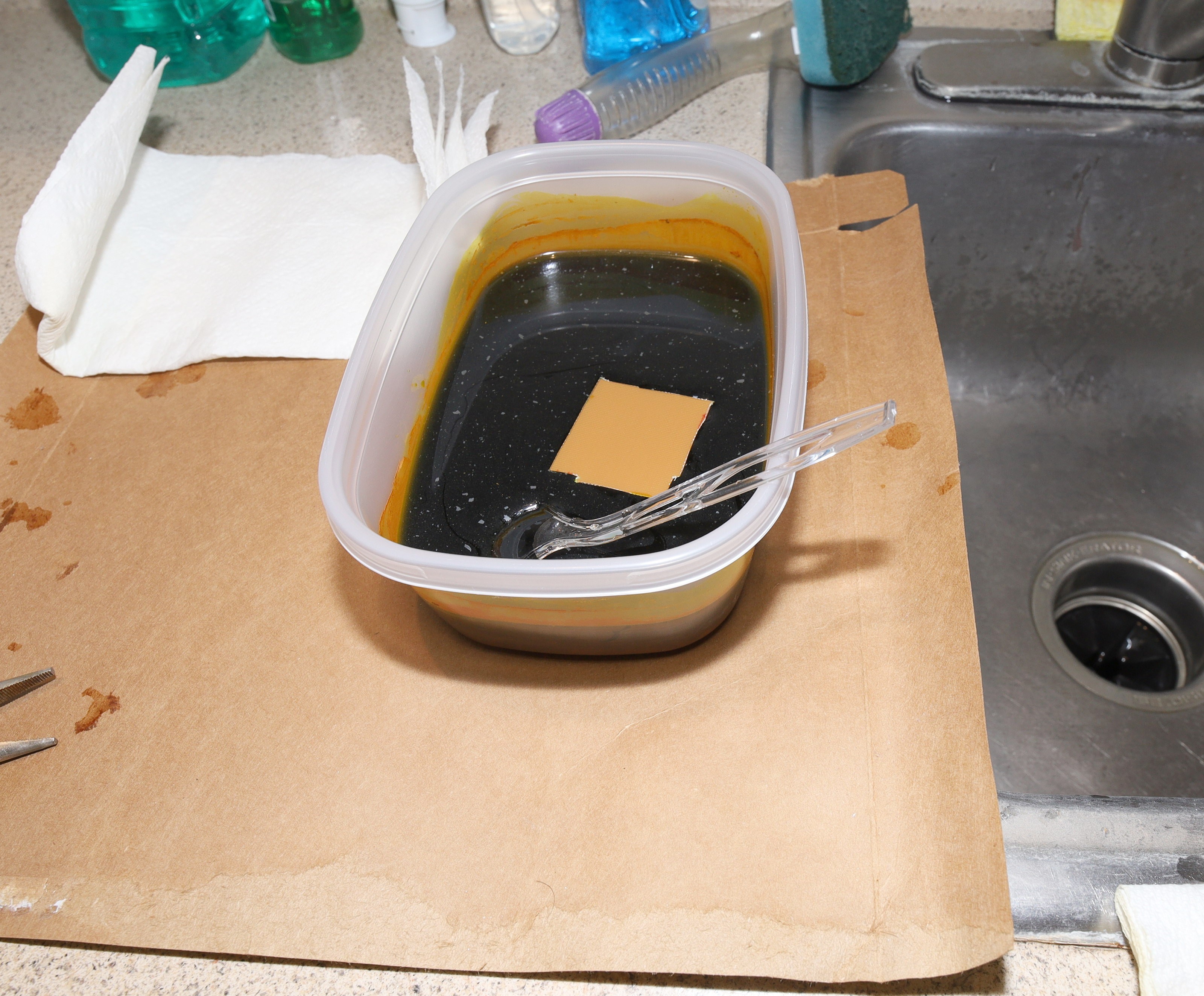
Drop it face down on the FeCl. Lions use fully concentrated FeCl straight from the bottle.
If it's under 2" x 2" or rectangular with a dimension under 2", it'll float upside down, allowing the copper to drop away. If it's wet, it won't float. If it's bigger than 2" x 2", it'll have to be held up with PC board pliers.
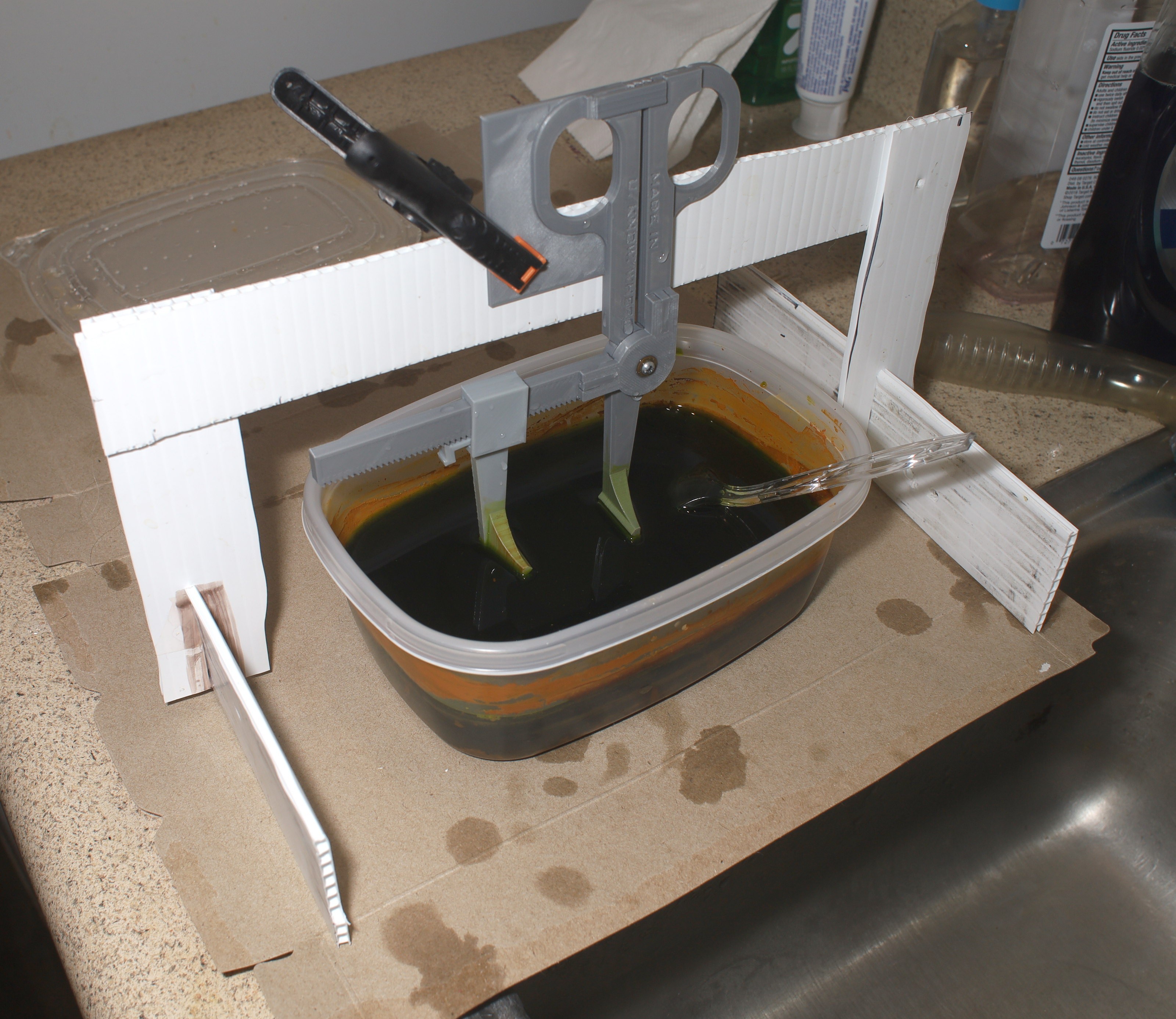
Slide it around a few times to disperse air bubbles. Some air bubbles require taking out the board & popping the bubbled. The PC board pliers are convenient way to shake off air bubbles. Determining the extent of the air bubbles requires waiting & seeing if everything is dissolving from above.
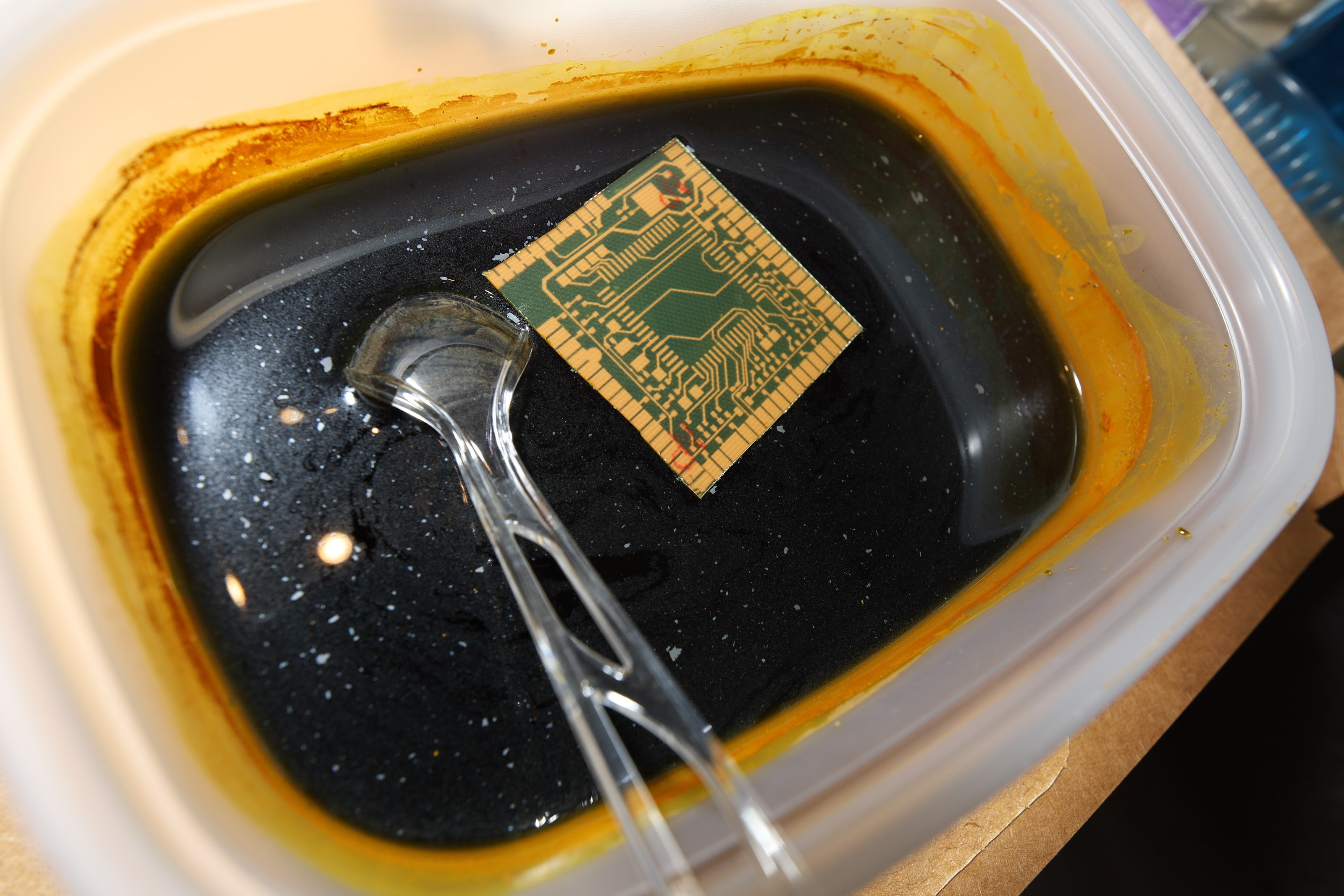
Note the air bubble on this board is visible from above, joining 2 pads which were unused anyway.
Etch it for 30-50 minutes, depending on temperature, monitoring it from the top to know when the copper has all dropped away. Lions prefer having the chemicals on a place setting overlapping the sink.
Rinse it off. Beware that any amount of rinsed FeCl stains stainless steel on contact. It has to be rinsed over the drain.
Grind down the edges of the board & drill out vias with a wire bit. The photoresist should be left on to prevent oxidation. Soldering burns it away. Lions originally dunked the finished board back in concentrated NaOH to erase all the photoresist, but this was expensive.
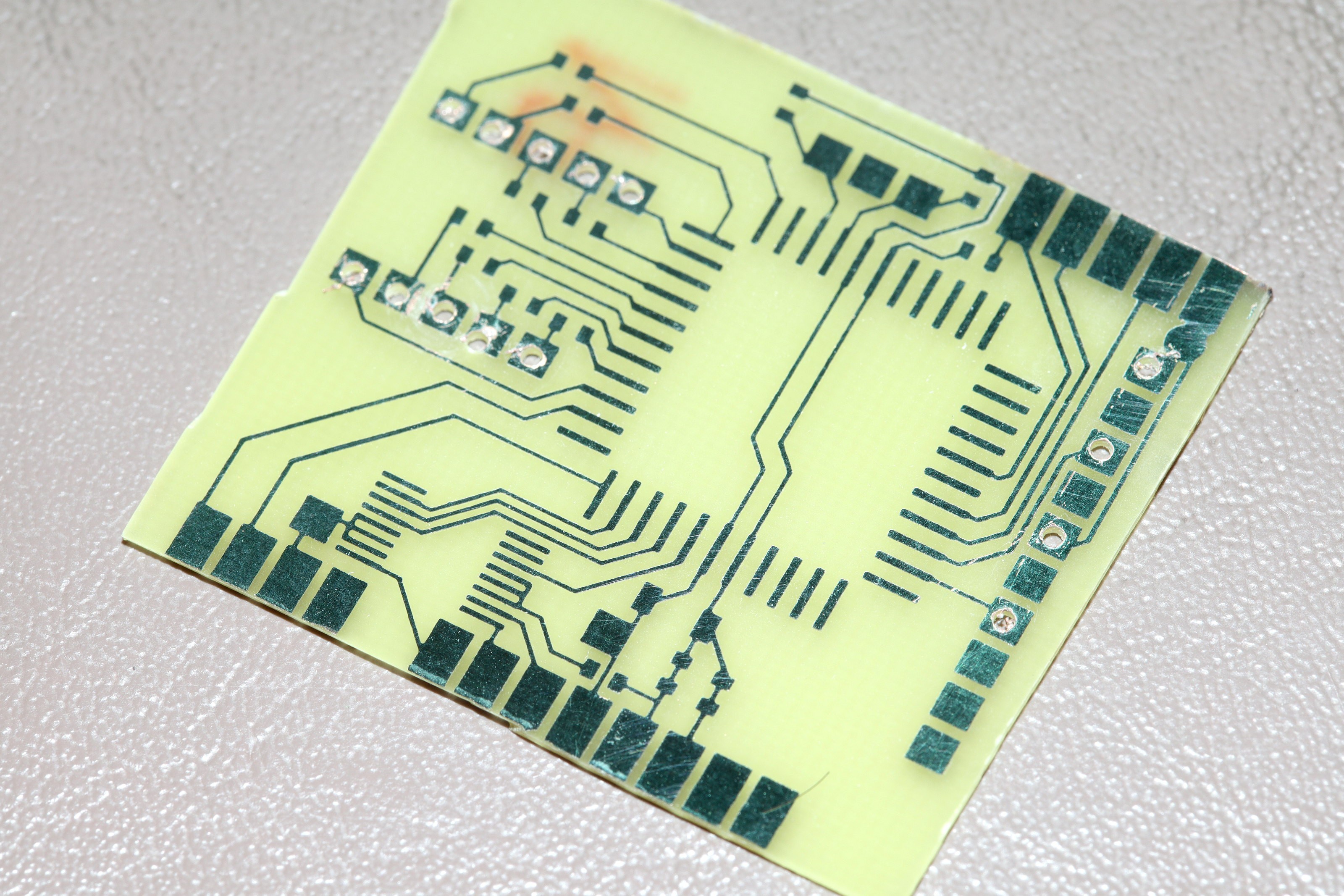
The mane causes...
Read more »
i think he gone........