Automatic bed leveling has become a standard feature in the last 2 years & has standardized on hall effect sensor pin testers. Hall effect sensors can measure distance down to the .1mm precision required.
The lion kingdom got a cheaper 3dtouch instead of the standard bltouch.
https://www.amazon.com/BZ-3D-Leveling-Printers-Precision/dp/B07ZCZP15F
Tearing it down is a destructive operation, so the only teardown of a sensor is:
There's a solenoid which raises & lowers the pin in order to change the XY position. Then, the hall effect sensor detects when the Z position hits a fixed height & emulates the Z stop switch. There's no analog height output. The user sets a difference between nozzle & probe height.
The mane problems are mounting the probe, recompiling the firmware & reconfiguring the gcode. The lion kingdom made a custom mount since all the online ones were junk.
https://github.com/heroineworshiper/utils/blob/master/3dtouch.FCStd
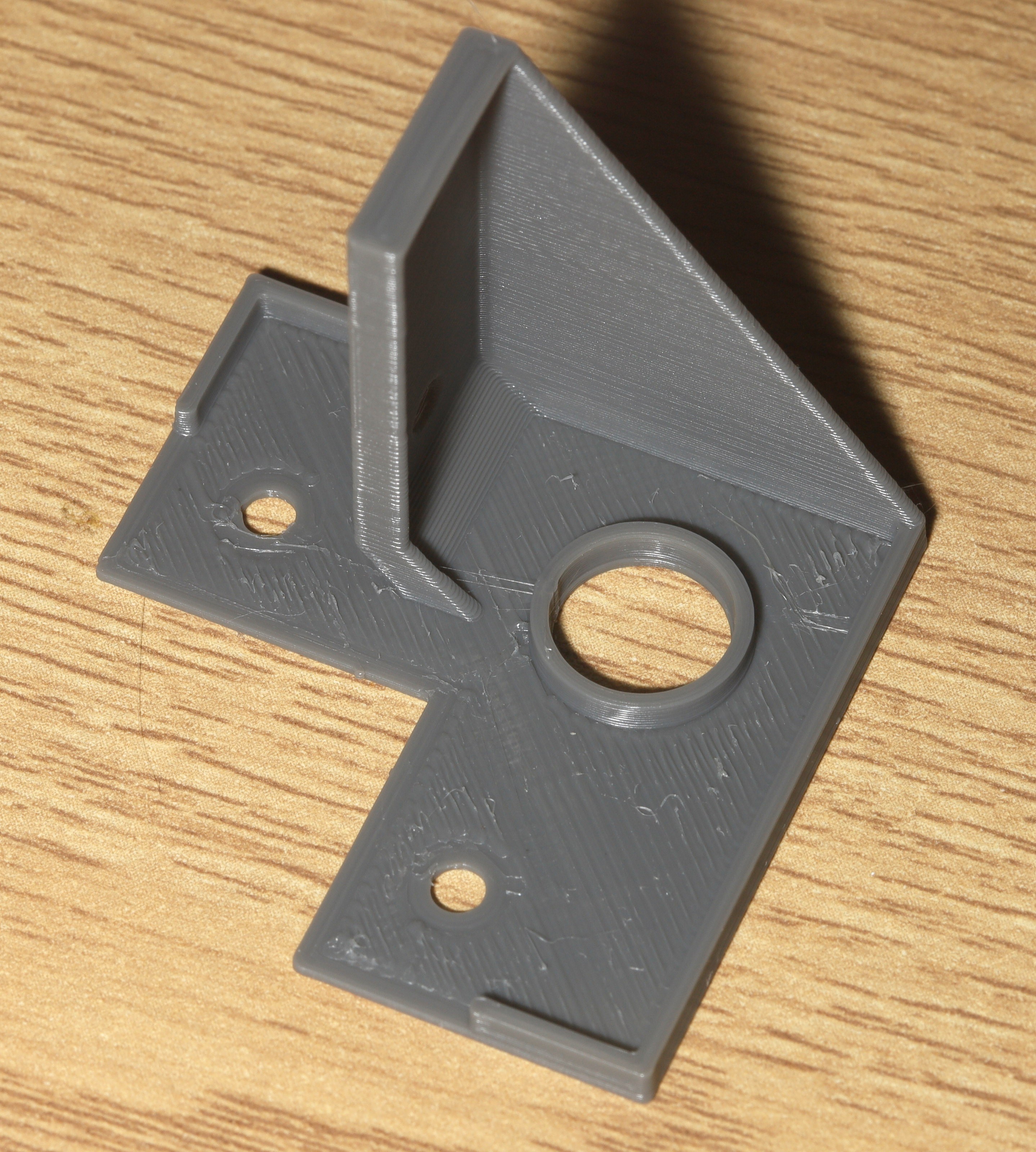
While this happened, the lion kingdom also ripped off the cooling fan.
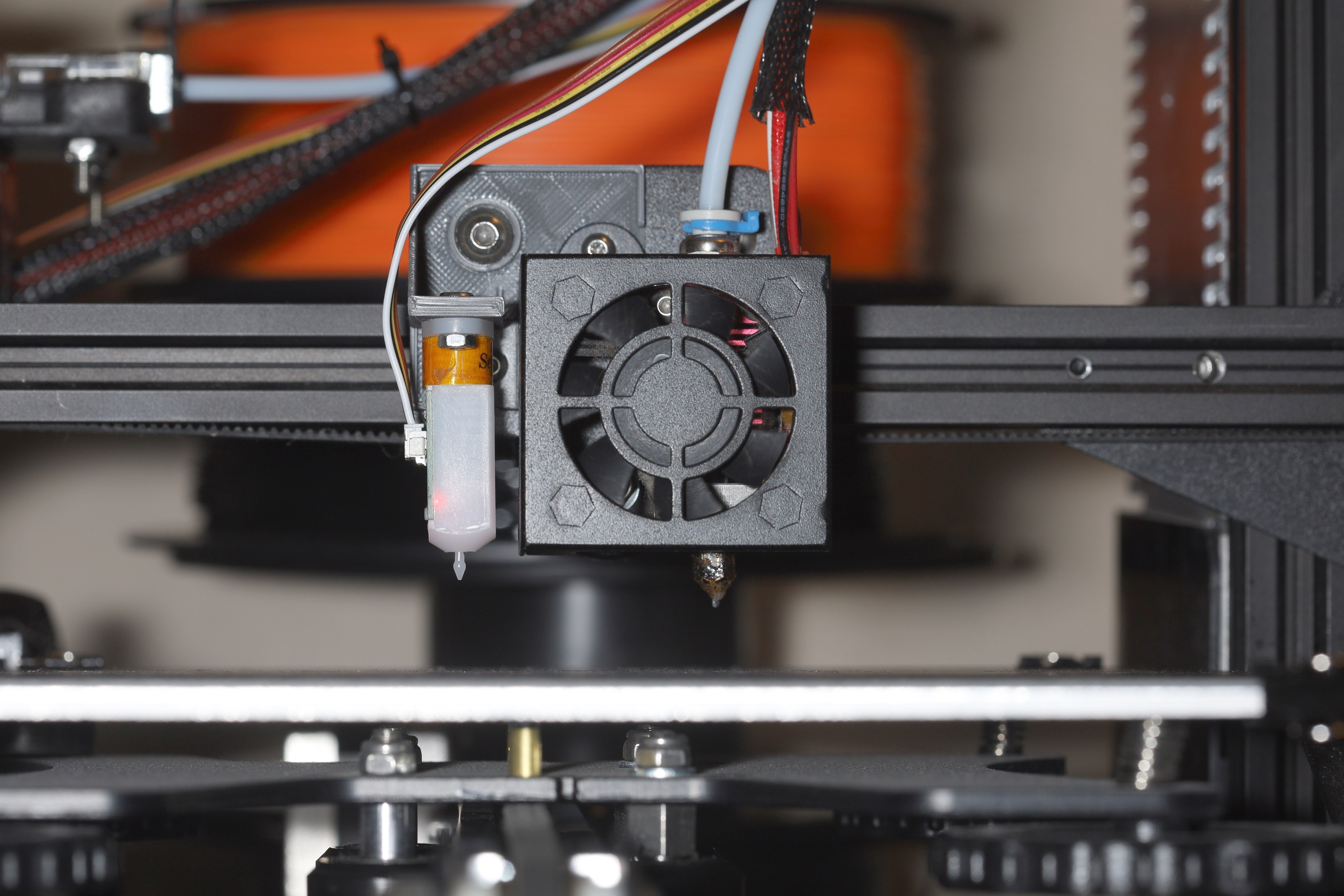
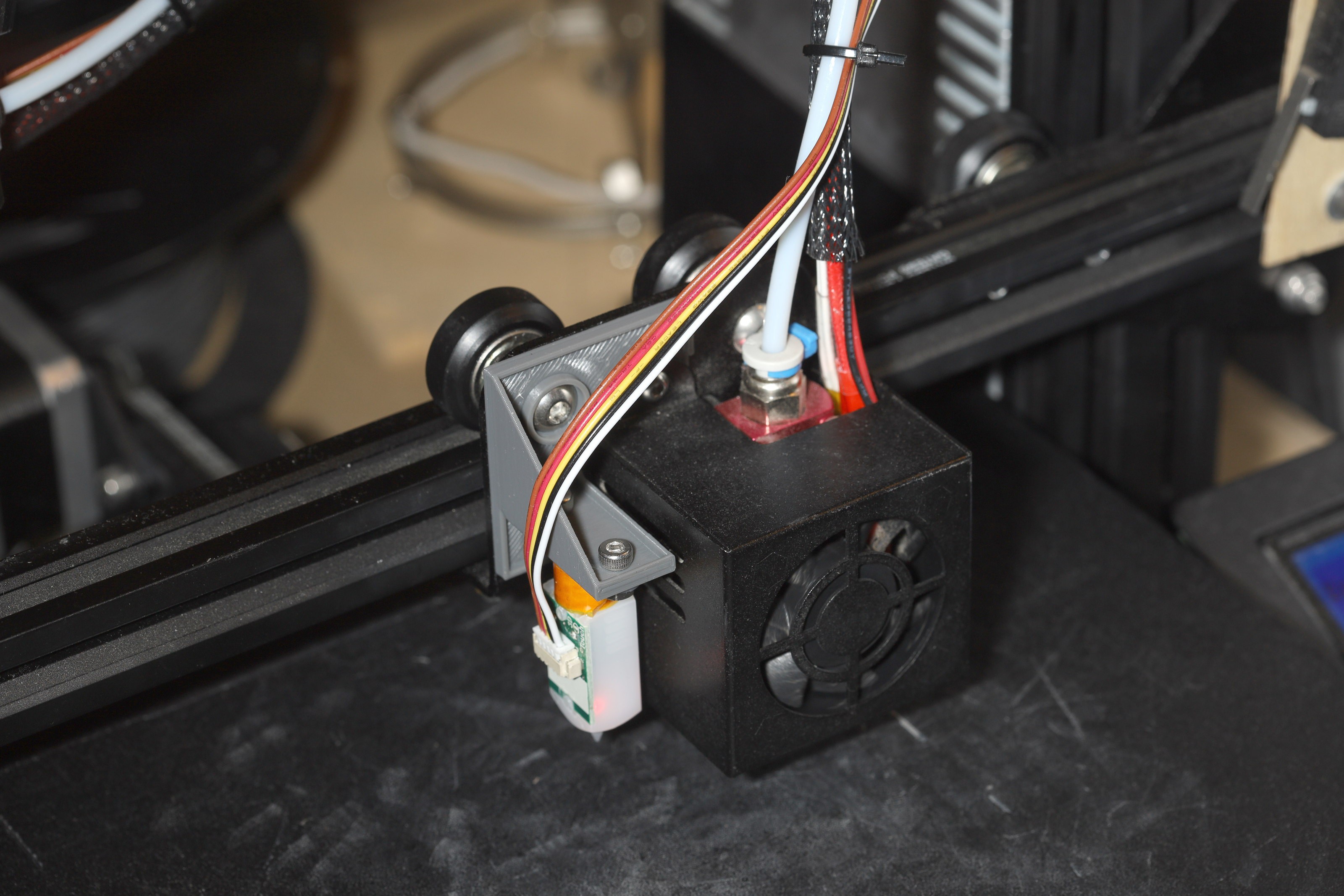
The only useful starting point came from:
https://all3dp.com/2/ender-3-with-marlin-how-to-install-marlin-firmware-on-your-ender-3/
The firmware has to be Marlin 1.1.x for the Ender 3, not marlin 2.0.x.
https://github.com/MarlinFirmware/Marlin/tree/1.1.x
The board has to be set to Sanguino & the processor has to be ATMEGA1284.
The best firmware notes were in:
The lion kindom used "PIN29" instead of "PIN27" for servo0 & kept the speaker alive, because you need the speaker to save the settings.
PIN 29 is actually pin 35 on the ATMega 1284, but the internet calls it PIN 29. We find PIN 29 being translated to PORTA2 in
~/.arduino15/packages/Sanguino/hardware/avr/1.0.3/variants/sanguino/pins_arduino.h
Then PORTA2 is pin35 on the 1284. The arduino libraries use some archaic pin numbering which has nothing to do with the datasheet. Pin29 emerges next to a capacitor.
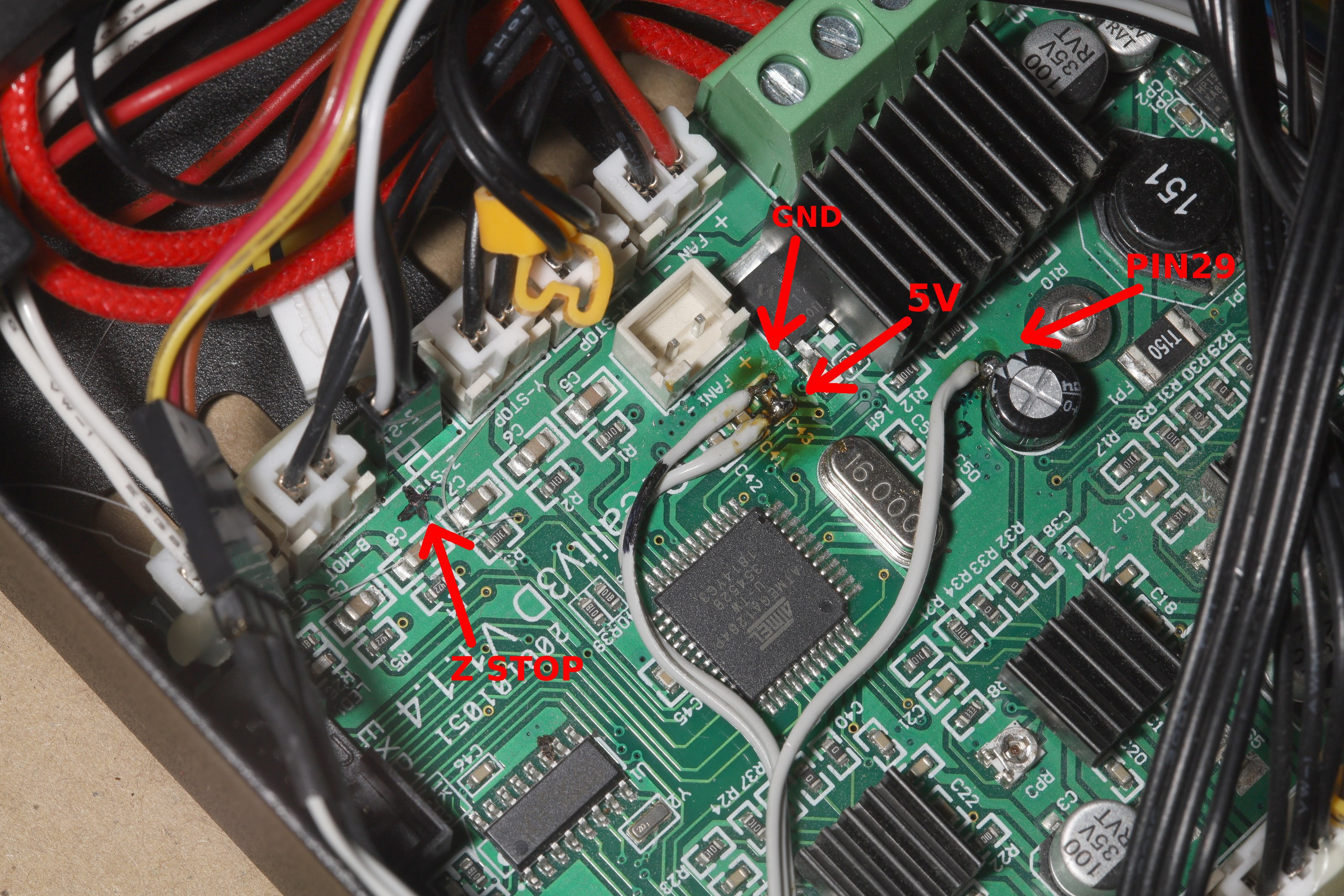
Programming the Ender 3 bootloader required writing the ArduinoISP sketch on an uno, then setting "Arduino as ISP" as the programmer to write the bootloader on the sanguino. Then, the Marlin firmware could be written to /dev/ttyUSB*. Sadly, the arduino bootloader on this board is crap. 1 problem is Marlin & the bootloader compete for the serial port.
The decision was made to scrap the bootloader & always use ICSP. It didn't free up a meaningful amount of memory, it was real slow, but it worked.
The trick with ICSP mode is you have to take the SD card out. The SD card shares the SPI pins with the programming pins & runs on 3.3V, so it'll get destroyed if you try programming with a 5V arduino.
You need to set the BAUDRATE & SPI_CLOCK in ArduinoISP.ino to 115200 & 200000 to speed up ICSP programming, then write the new ArduinoISP to an Arduino.
The avrdude command required to flash Marlin is given in an attempt to upload the sketch. All the Show verbose output check boxes must be enabled in preferences.
/root/arduino-1.8.15/hardware/tools/avr/bin/avrdude -C/root/arduino-1.8.15/hardware/tools/avr/etc/avrdude.conf -v -patmega1284p -cstk500v1 -P/dev/ttyACM0 -b115200 -Uflash:w:/tmp/arduino_build_951059/Marlin.ino.hex:i
In this case, the baud rate was increased to use the hacked ARduinoISP.
Notes about configuring gcode to level the bed are in
The mane point is it doesn't level the bed unless the gcode contains G29 after the bed is preheated & it gives a G28.
G29 makes it probe & applies the mesh, but requires a preceeding G28 to home the nozzle or it'll crash.
The lion kingdom updated its fixcura.py script to add bed leveling gcode.
https://github.com/heroineworshiper/utils/blob/master/fixcura.py
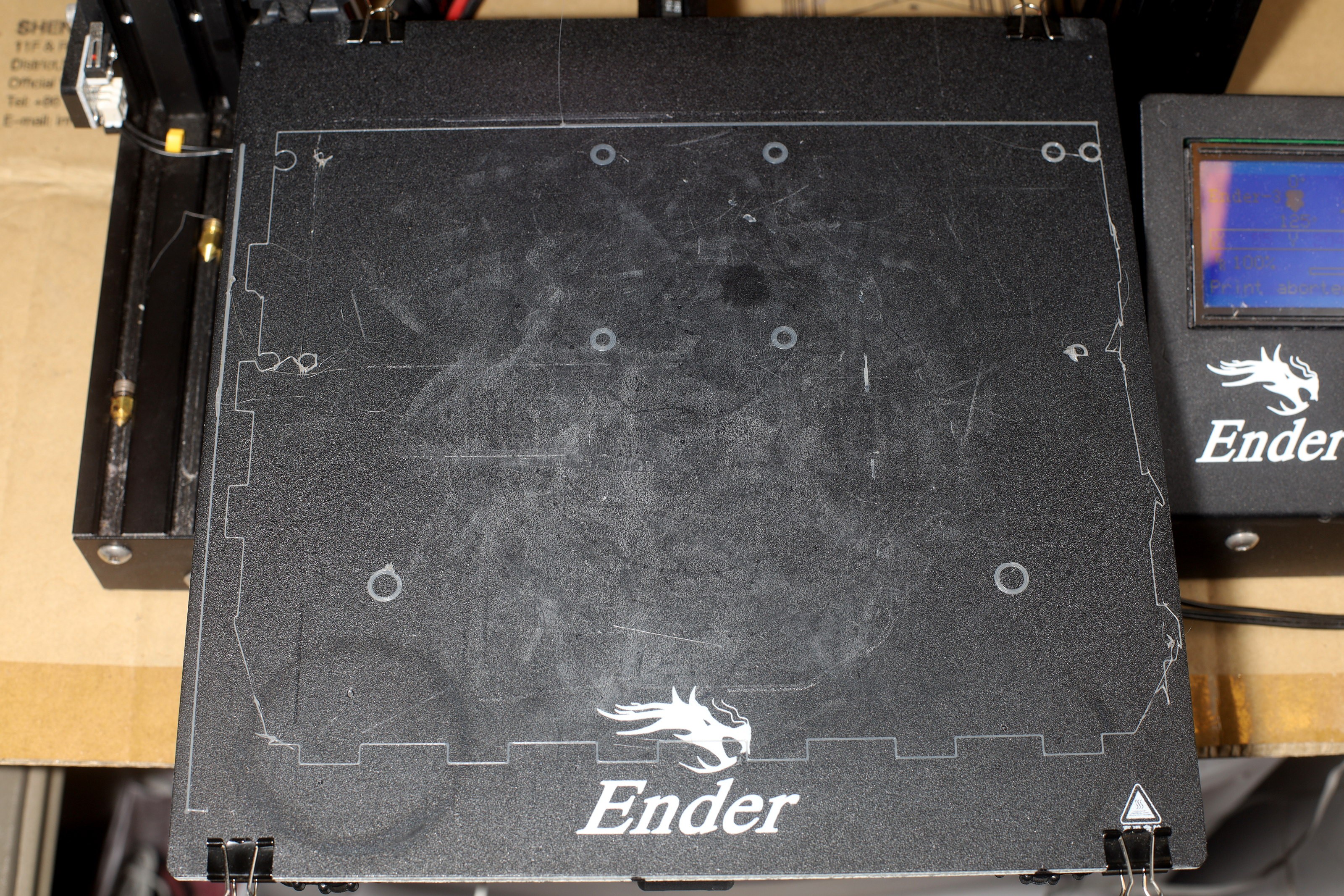
The default auto bed leveling firmware failed to access the very edges of the bed. It did incrementally improve the quality of smaller parts.
After giving up on accessing the very edges of the bed, the lion kingdom printed a part which previously worked without auto bed leveling. It was easier to print & slightly more even, but the 2nd layer was under extruded.
The lion kingdom had to set Z_PROBE_LOW_POINT to -5 for it to actually perform bed leveling. The Z axis movement is invisible to the naked eye. Reach in & feel the Z corkscrew to know if it's doing anything.
Probing closer to the edges or in places which best represent the height of the area might help. It can't probe the very right side because the nozzle runs out of room. Even the crazy auzzie bloke showed it not reaching the very right side. The lion kingdom set X_BED_SIZE to 250 to get closer to the right edge.
The mane problem was eventually narrowed down the Z axis not compensating enough. The probing seemed consistent but the nozzle didn't go down enough where it was low & it didn't go up enough where it was high. A simple hack doubling the probing matrix actually improved it enough to print the full width of the bed. It's as if they deliberately divided the probing matrix to make it more conservative.
Marlin_main.cpp: 5586 before print_bilinear_leveling_grid is where you can tweek the matrix.
#if ENABLED(AUTO_BED_LEVELING_BILINEAR)
if (!dryrun) extrapolate_unprobed_bed_level();
// HACK
for(int i = 0; i < GRID_MAX_POINTS_Y; i++)
{
for(int j = 0; j < GRID_MAX_POINTS_X; j++)
{
z_values[i][j] *= 2;
}
}
print_bilinear_leveling_grid();
refresh_bed_level();
Using a magnetic bed, the nozzle was always printing closer in the front than the rear. No amount of Z offset, wheel dialing, or rotation of the bed made any difference. The 3D touch was always detecting a higher bed in back than in front. Newer versions of marlin support tweeking the probe points in the GUI, but the best option for the Ender 3 was to hack the Marlin_main.cpp function.
// HACK
for(int i = 0; i < GRID_MAX_POINTS_Y; i++)
{
for(int j = 0; j < GRID_MAX_POINTS_X; j++)
{
z_values[i][j] *= 2;
}
}
// move right rear away from nozzle
// z_values[GRID_MAX_POINTS_Y - 1][GRID_MAX_POINTS_X - 1] += 0.1;
// move left front away from nozzle
z_values[0][0] += 0.1;
// move mid front away from nozzle
z_values[0][1] += 0.1;
// move right front away from nozzle
z_values[0][2] += 0.1;
This shows the relationship between the array subscripts & the positions of a 3x3 probing grid. Ideally, there would be gcode commands to tweek the probe points. Months of tweeking the Z offset gave a good enough idea of the required offsets to hard code it.
Another item which might help is shifting the paperclips closer to the center, so the edges aren't as eccentric.
Another problem afflicting bed leveling is the bed compressing from the pressure of filament extruding on it. The Ender 3 bed has an artifact where the adhesive bonding the buildak surface to the fiberglass expands & compresses. The lion kingdom desperately needs a more stable bed.
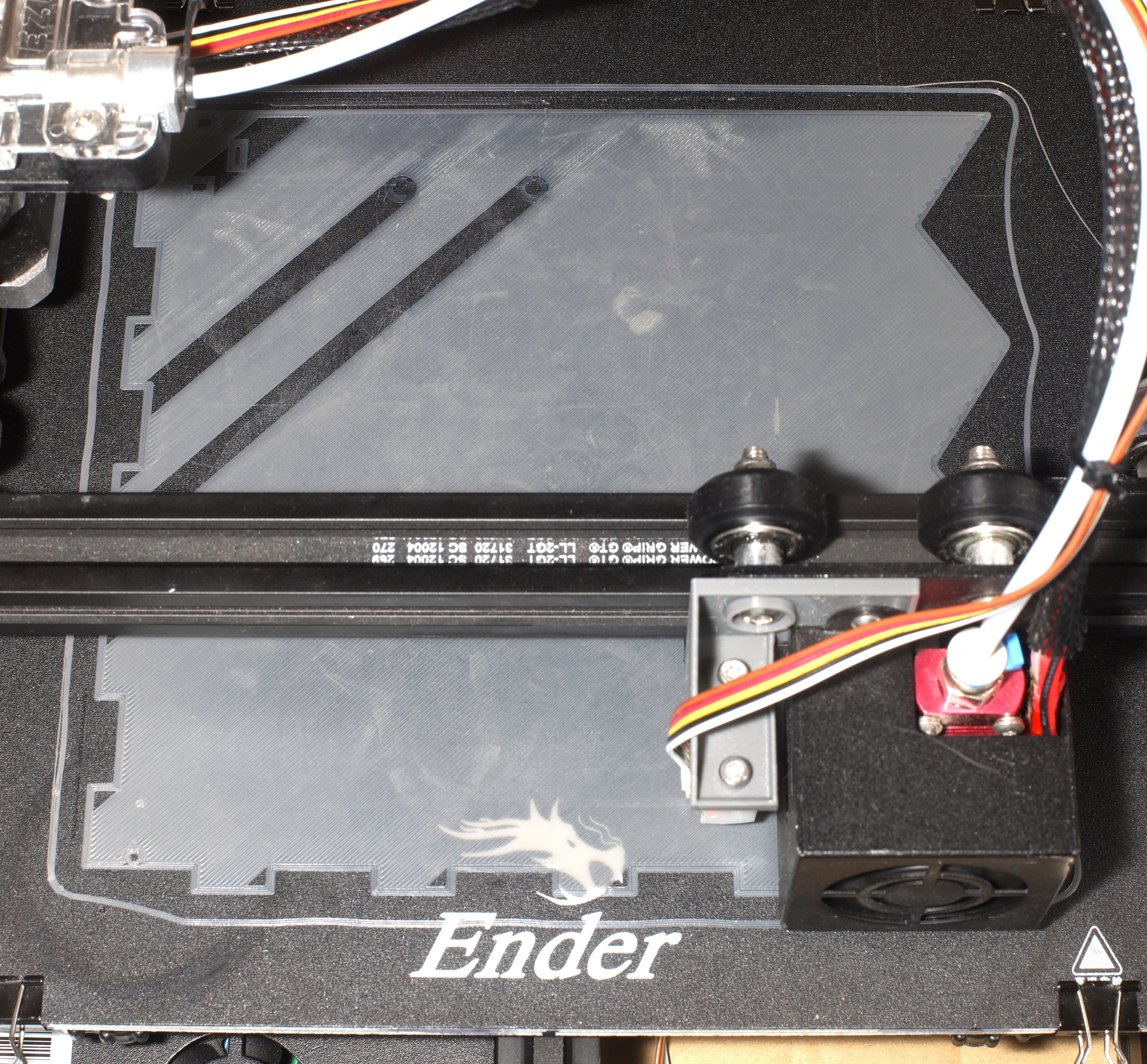
The bed in this layer was higher when it printed the outlines. Then, it got squished lower when it printed the crosshatching.
Your biggest ally in automatic bed leveling has proven to be prepare -> bed leveling -> PROBE Z OFFSET
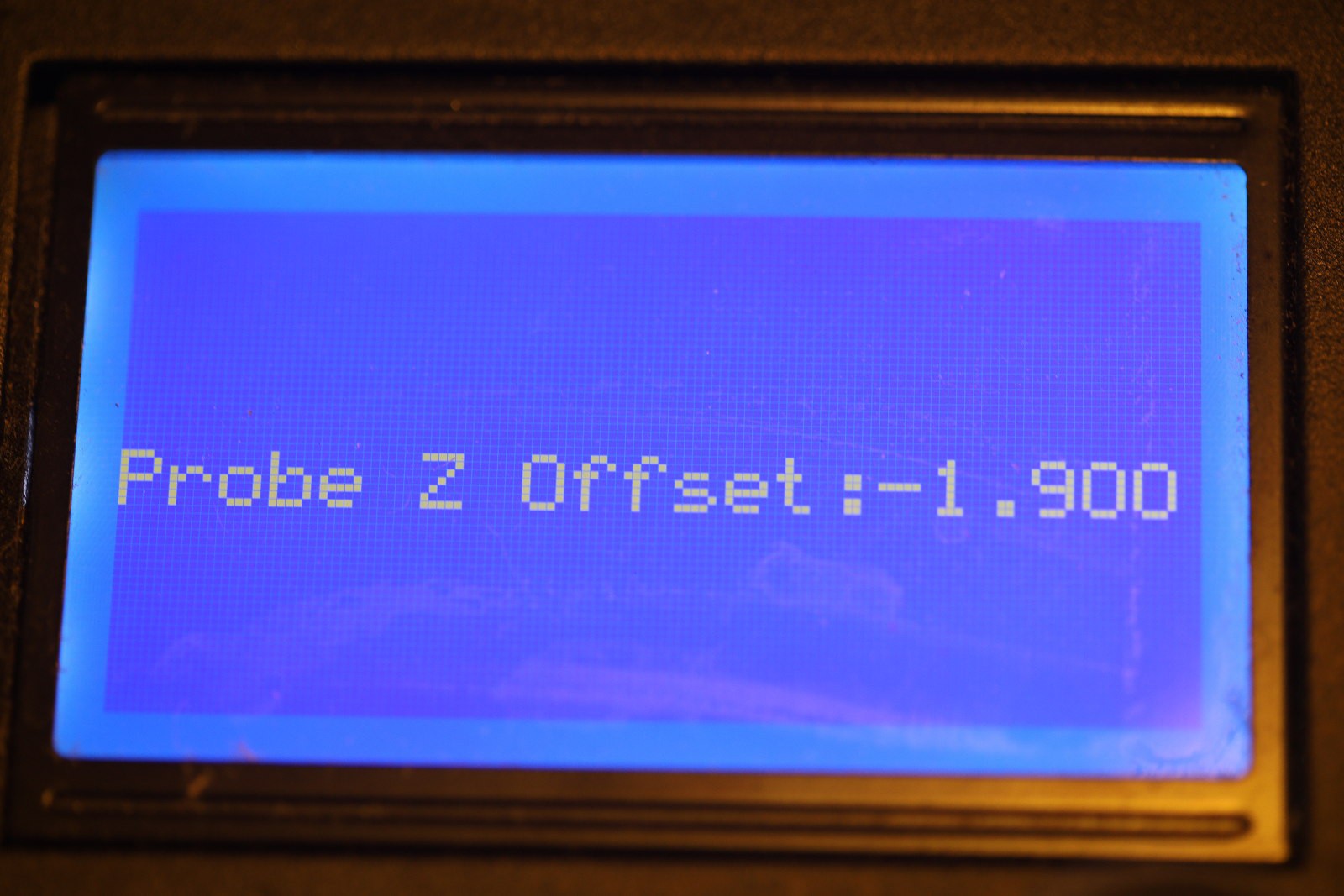
That's the difference between the probe & nozzle height. It has to be tweeked every time you change nozzles, then saved. Between prints, it seems to vary by .1mm. It can be tweeked while it's printing under tune -> probe Z offset but it can't be saved.
Printing a skirt & tweeking the Z offset is still essential, whenever possible. If there isn't enough room for a skirt, you can try modeling test areas & making sure the slicer prints the test areas 1st.
One thing which doesn't work is adjusting the knobs while printing. That always screws it up when auto bed leveling is active, where before auto bed leveling, it could work around errors.
The Ender 3 USB port
During this process, the lion kingdom discovered the Ender 3 USB port is a serial port with debugging output. It takes G code as input. G28; G29; levels the bed & prints the matrix.
0 1 2 3 4
0 -0.155 -0.040 -0.010 +0.030 +0.088
1 -0.195 -0.043 +0.005 -0.030 -0.030
2 -0.052 +0.035 +0.075 +0.067 +0.000
The matrix for a 5x3 probing grid has front left as 0,0 & back right as 4,2
Compare to the heated bed.
0 1 2 3 4
0 -0.375 -0.167 -0.160 -0.132 -0.107
1 -0.360 -0.070 +0.030 -0.057 -0.152
2 -0.223 -0.132 -0.073 -0.115 -0.210
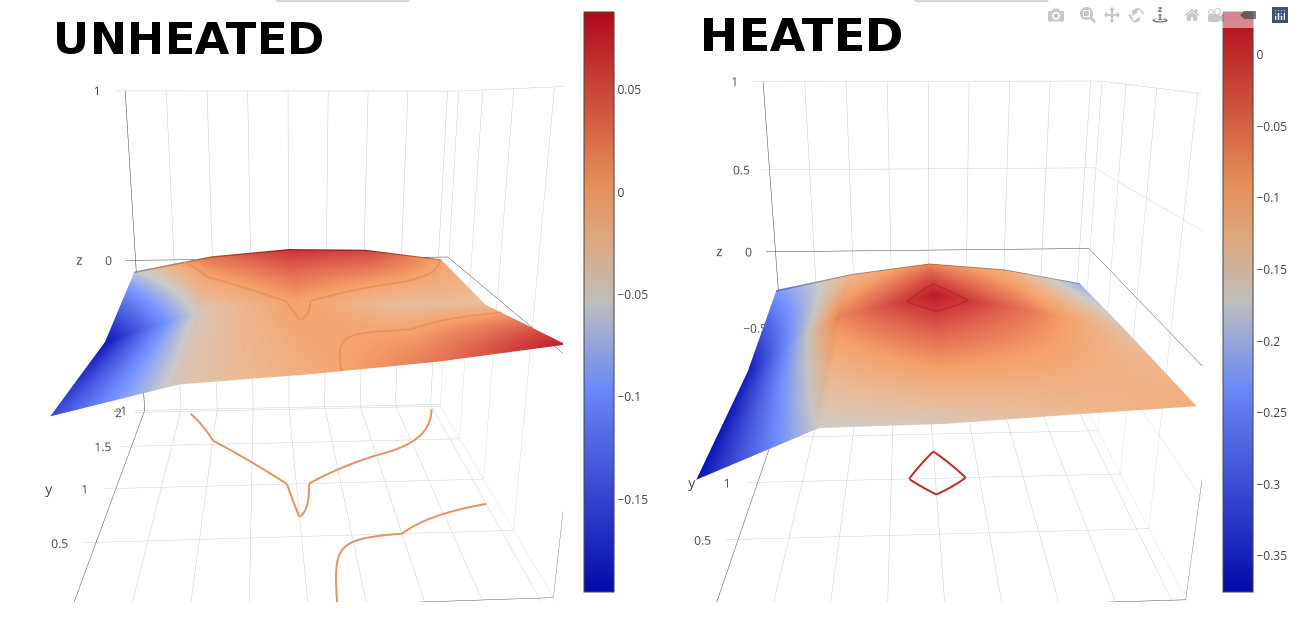
You could make a joystick control the print head with an HID to serial program.
The catch is opening the USB serial port resets the atmega, destroying any print in progress. The way around this is to remove C32 from the board.
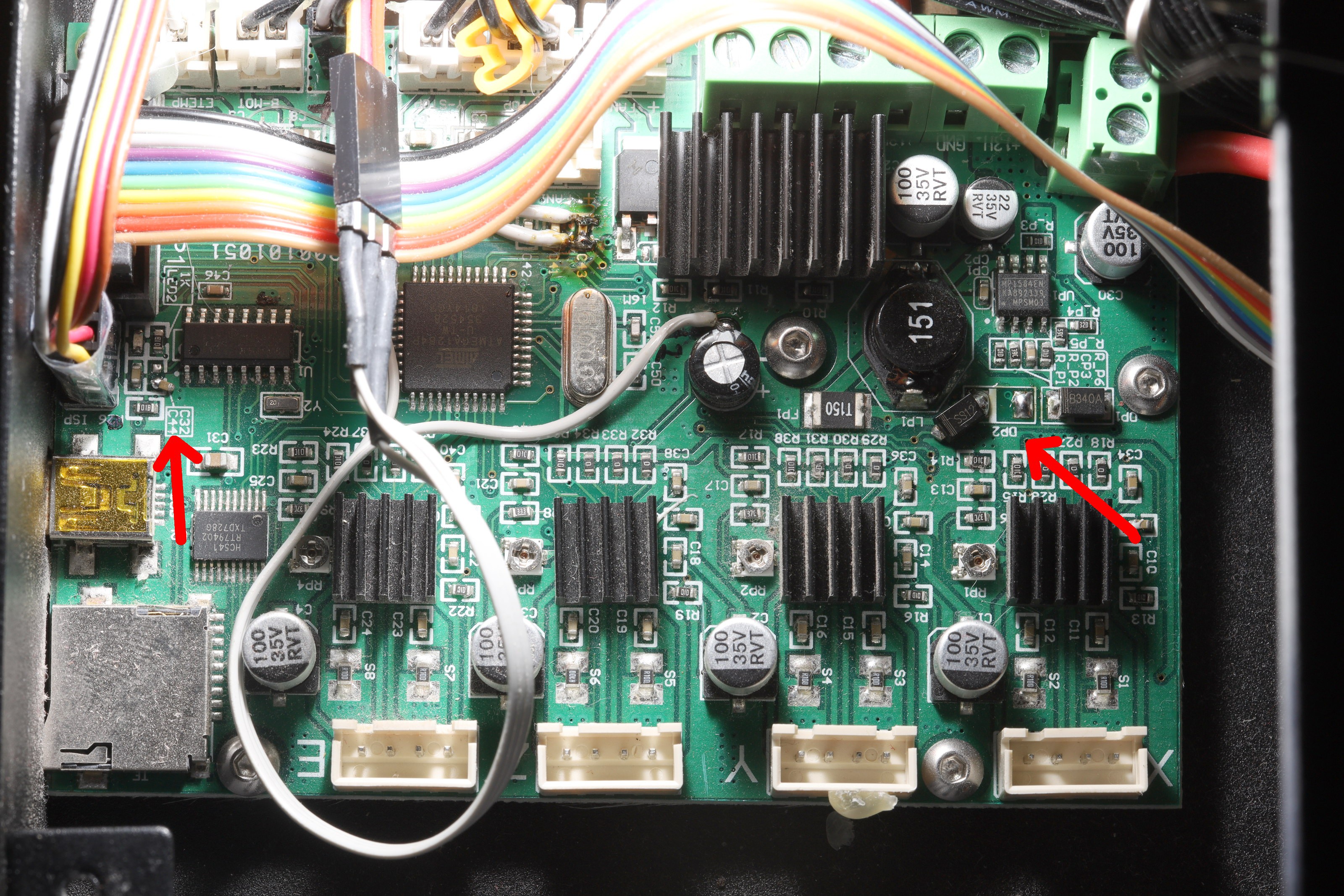
The other essential change is to unplug USB power from the mane board by removing DP2. Helas, the FTDI chip is powered by the mane board, not USB. These design flaws were undoubtedly kept from the board's Sanguino days.
Large prints
The lion kingdom has only 1 part which truly requires the full bed width & automatic bed leveling. Other narrower parts benefit from bed leveling but otherwise used to be printable with marginal quality.
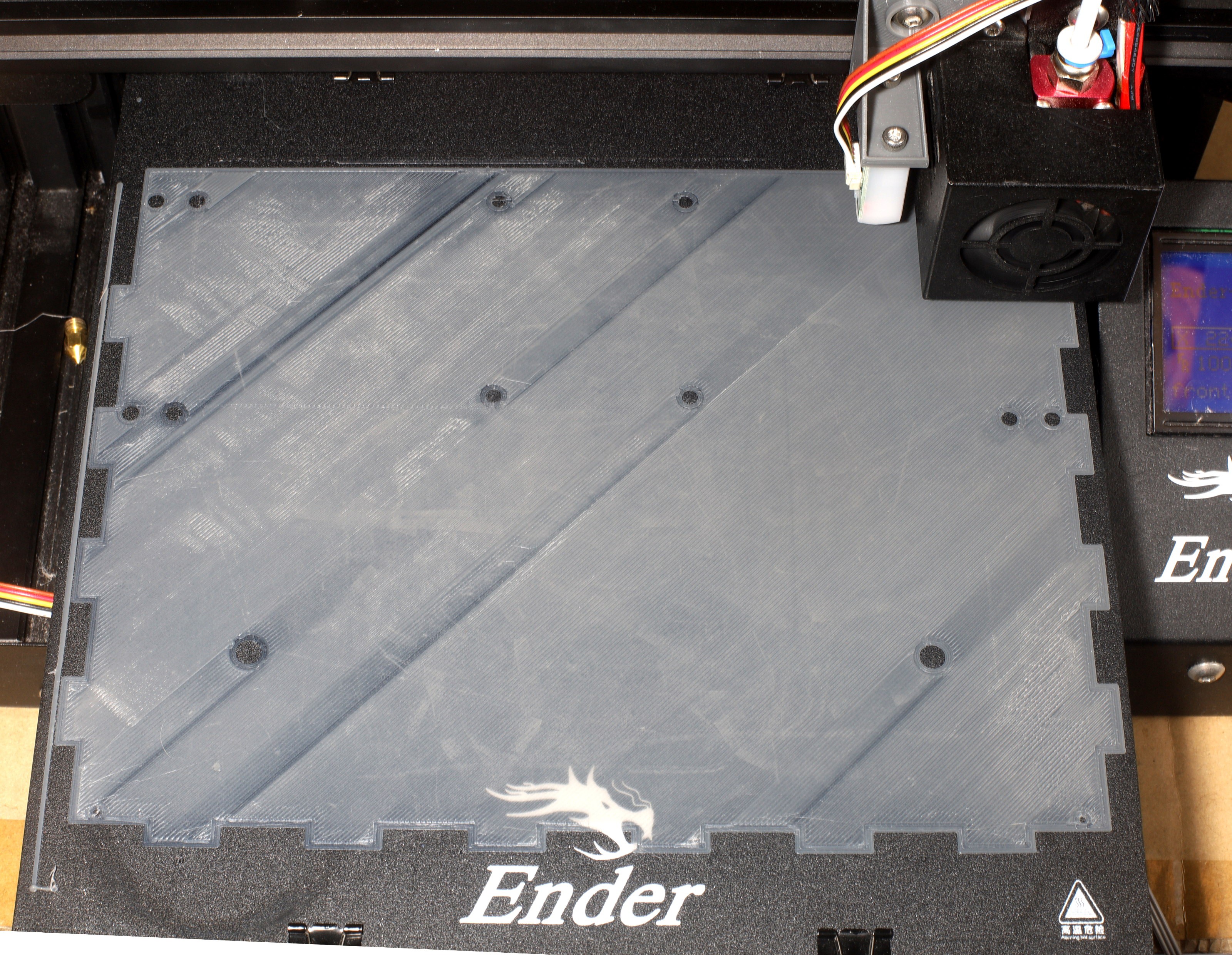
With wide parts & automatic bed leveling, the heating becomes the limiting factor. They have to be as far left as possible. It can't print the right edge because of the lack of heating. Getting this wide required 65C for the 1st layer.
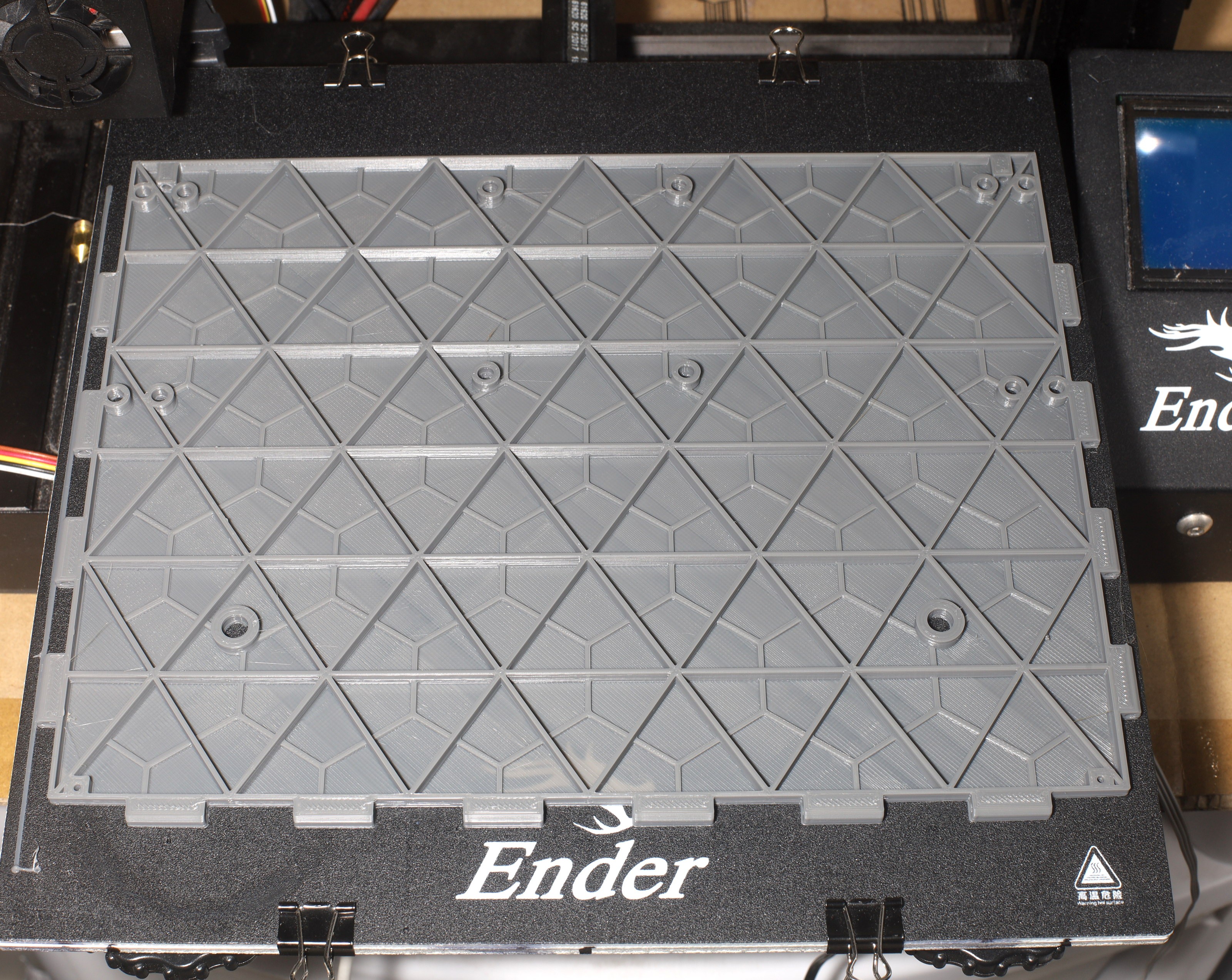
This part wasn't modeled based on the bed size, but it managed to fit by luck. 228mm is the practical limit of the 235mm bed width. It's not bad, considering the Ender 3 was marketed with a 220mm usable width.
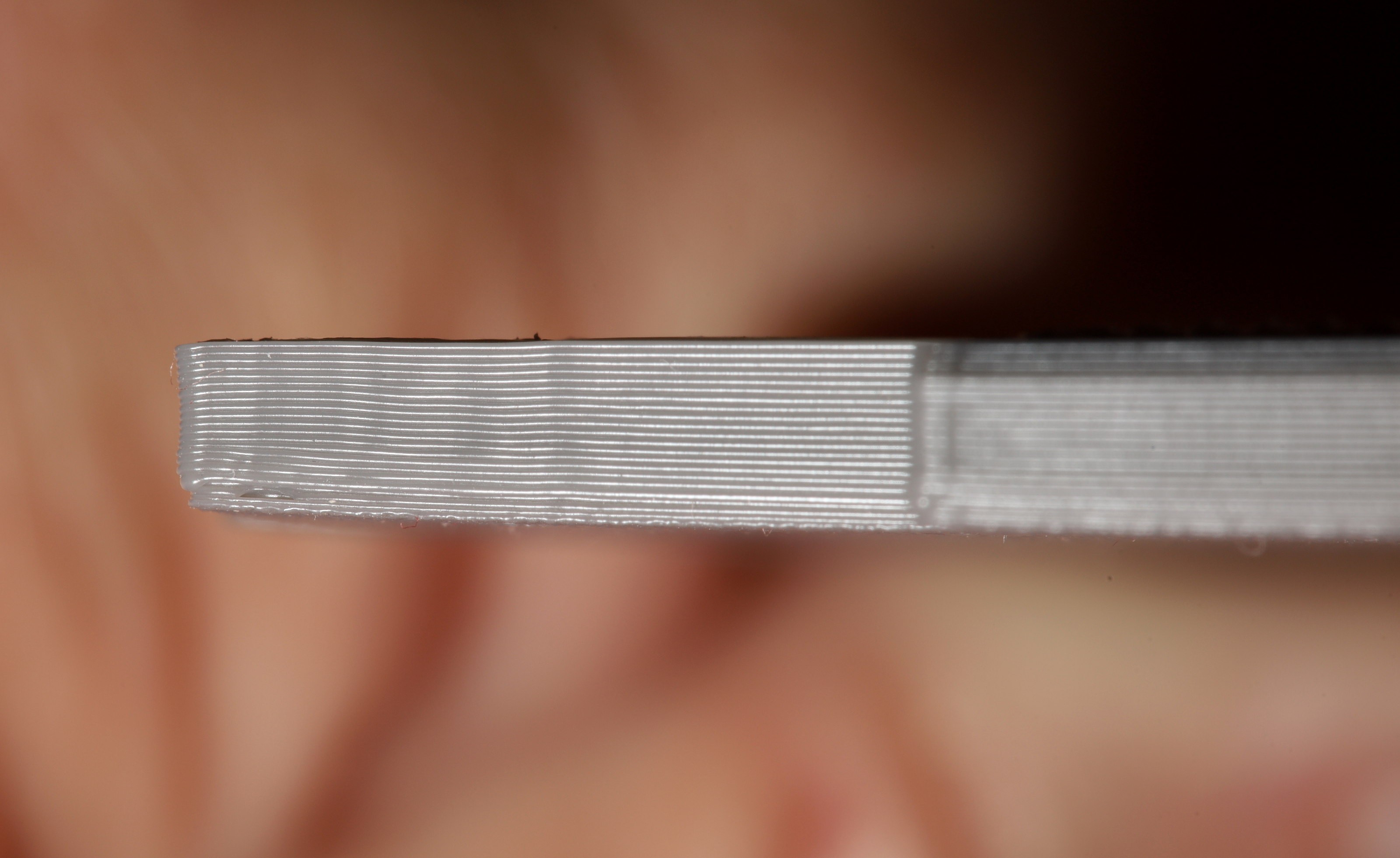
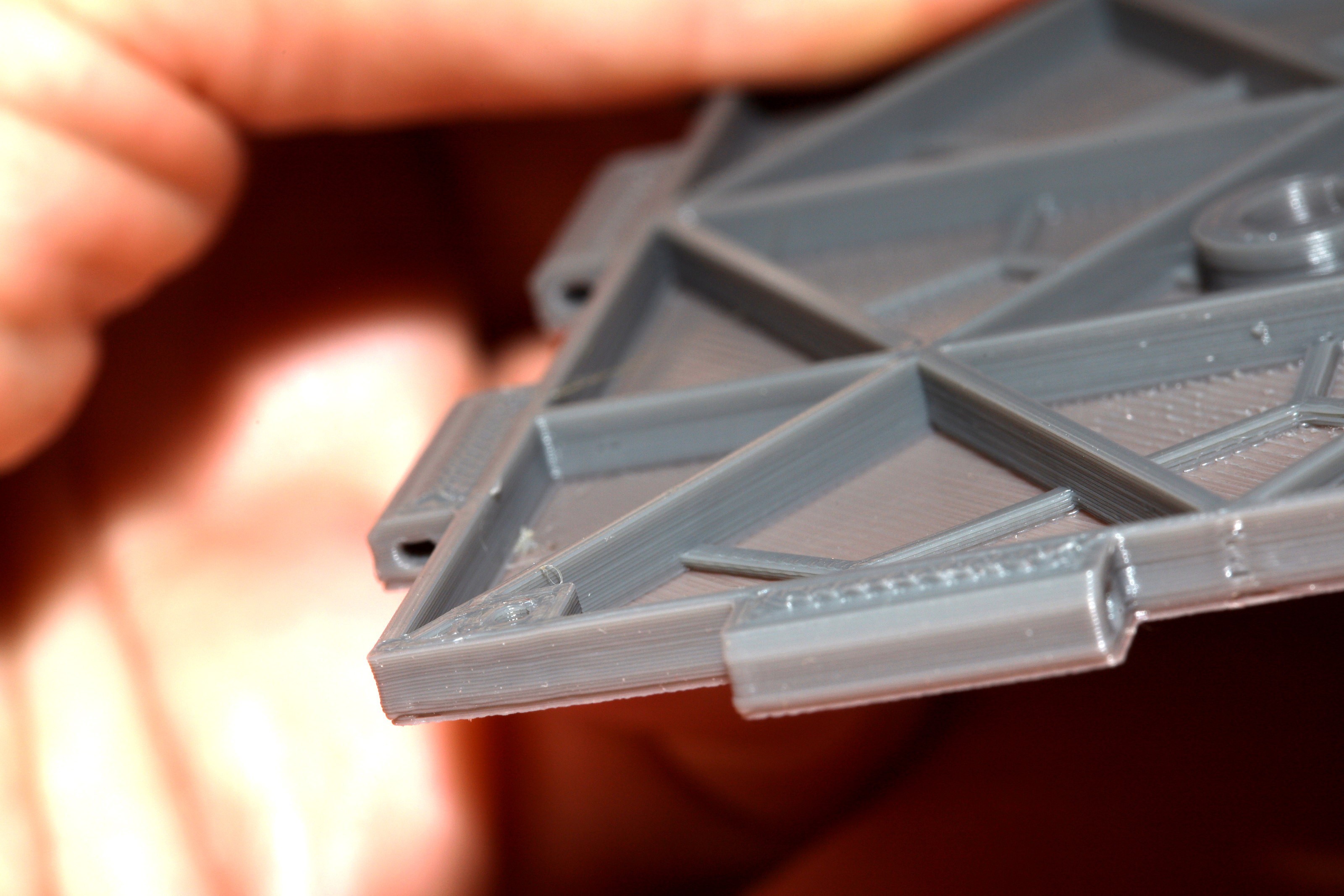
Unfortunately, with wide parts you can't cool down the bed after the 1st layer. The shrinking of PLA becomes important. This part had its lower layers shrink & warp because the bed was cooled. You might get away with 65C for the bottom layer & 60C for the top layers.
Discussions
Become a Hackaday.io Member
Create an account to leave a comment. Already have an account? Log In.