The First Blended Wing Body Tailsitter
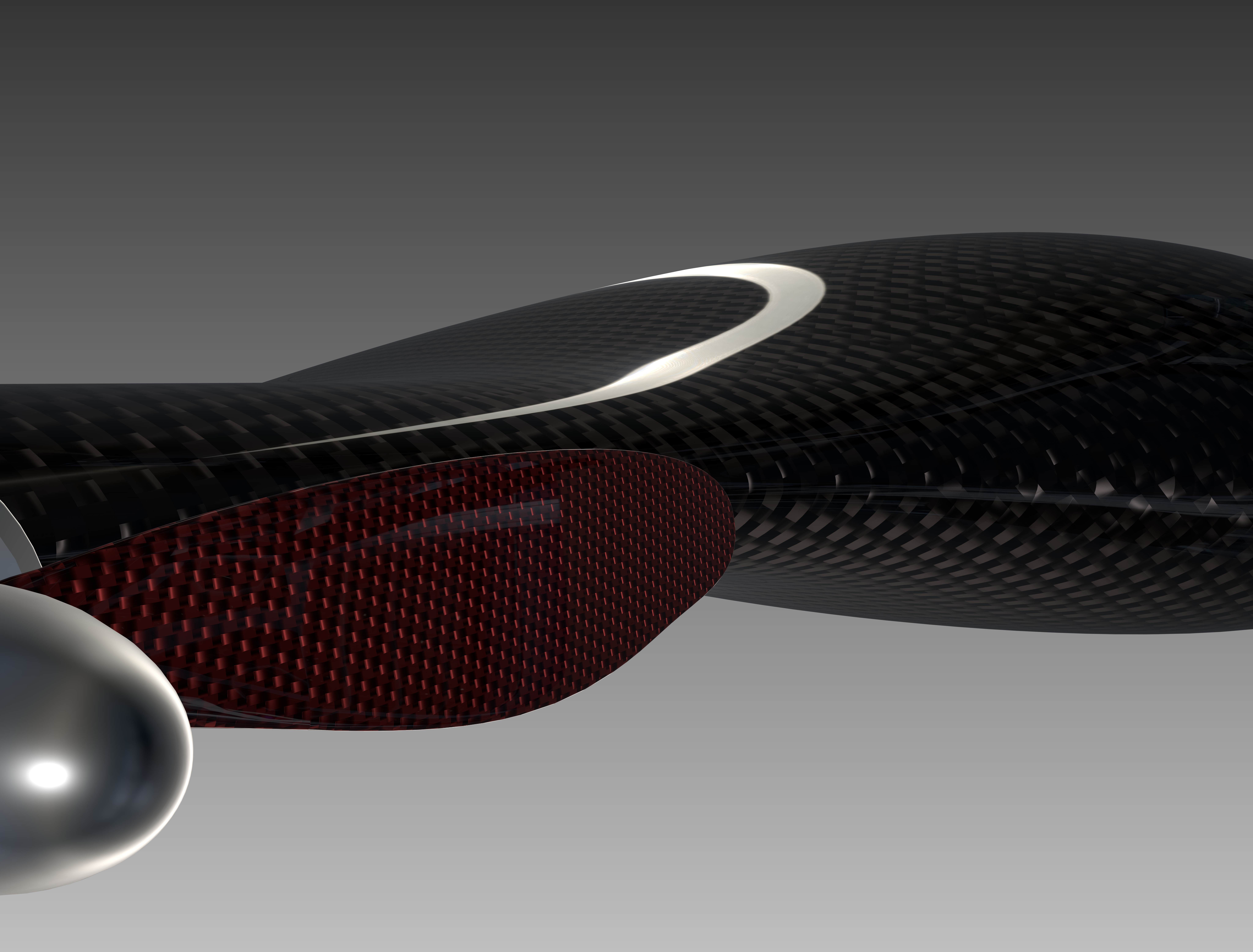
To effectively fullfill the unique flight requirements, our drone has to have a corresponding unique airframe. Combining modern concepts, we're bringing together the experimental Blended Wind Body (of which very little literature exists), and the Tailsitter (of which even less literature exists) into a Blended Wing Body Tailsitter (of which no aircraft exist, with our prototype being the first)
The Tailsitter
A lot of things have changed about this concept from its inception, however VTOL was always a necessity, as we needed to create a system that could takeoff directly from stores without any infrastructure or complex setup. Given the small size of our system (2kg compared with ~10kg for most delivery drones, with a projected area of 2.5 sq ft, compared to ~25 sq ft for other delivery drones), and the minimal moving parts (our drone has only 5 independent moving parts, with other drones ranging from 8 to 19), a tailsitter was a far more effective option, eliminating redundant parts or additional actuation surfaces for flight transition, simply using the existing elevons of a flying wing to switch between horizontal and vertical flight.
The Blended Wing Body
As with all aircraft, effiiency is paramount . For delivery operations, a higher efficiency allows us to have a greater range and carry a much larger payload. Since we'd need to have a flying wing configuration (due to the drone being a tailsitter), along with a relatively large fuselage to store the cargo (a 10*20*25cm box, as per requirements from hospitals), a blended wing configuration would allow us to have the fuselage additionally generate lift and therefore improve the efficiency of the aircraft greatly. This allows us to further reduce the size of the aircraft, as smaller wings can provide adequate lift, and create a more suitable lift distribution, reducing the forces on the airframe