This gripper is based on the Yale OpenHand research, and used a method of fabrication known as "hybrid deposition manufacturing" to produce a multi-material part which allows for superior grasping characteristics. The assembly consists of two fingers that are individually driven with 20kg servo motors. Each finger has two degrees of freedom, and is controlled by a single motor, making the device an underactuated system. Underactuated robotic hands show adaptive behavior that is allows for a wide range of objects to grasped.
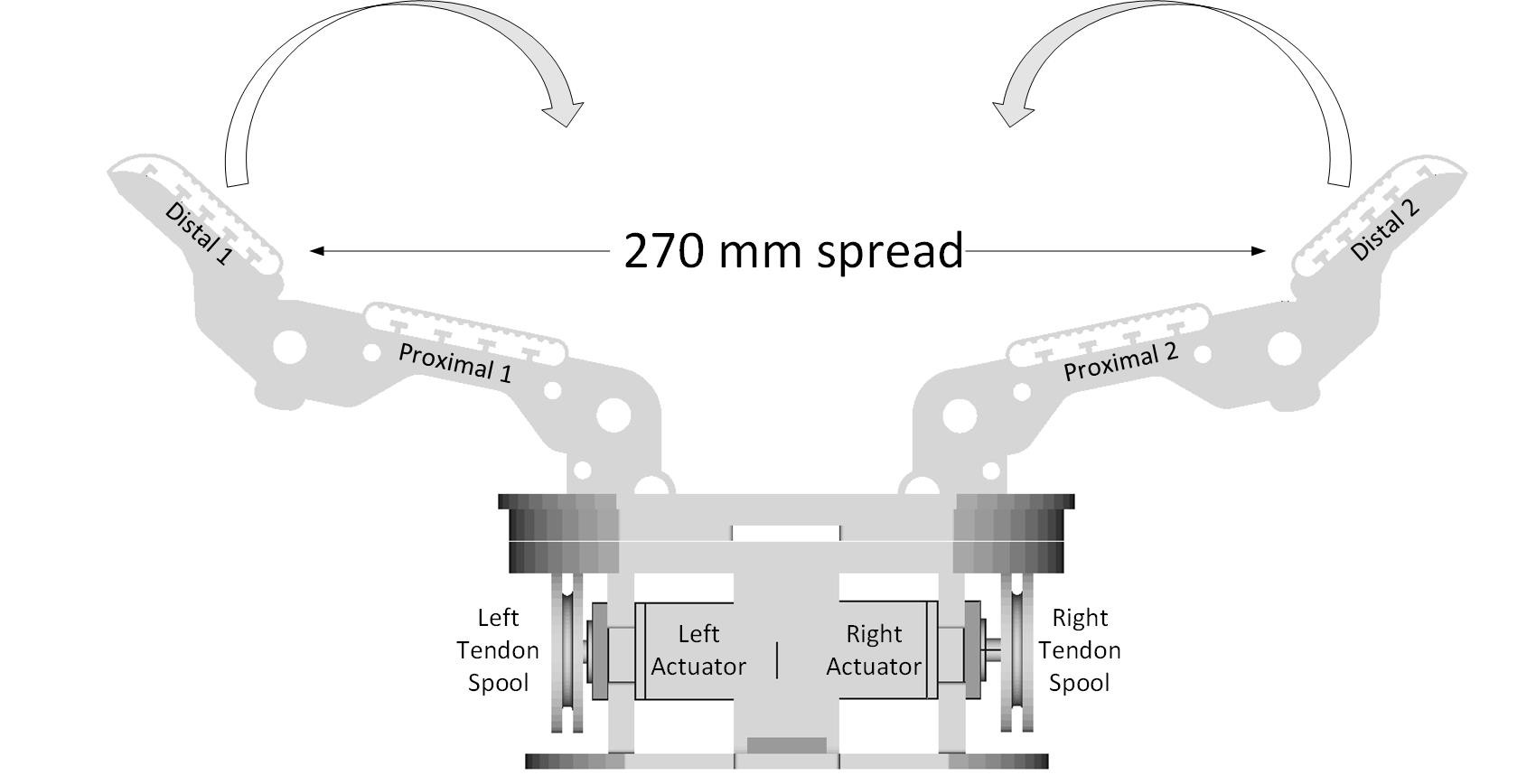
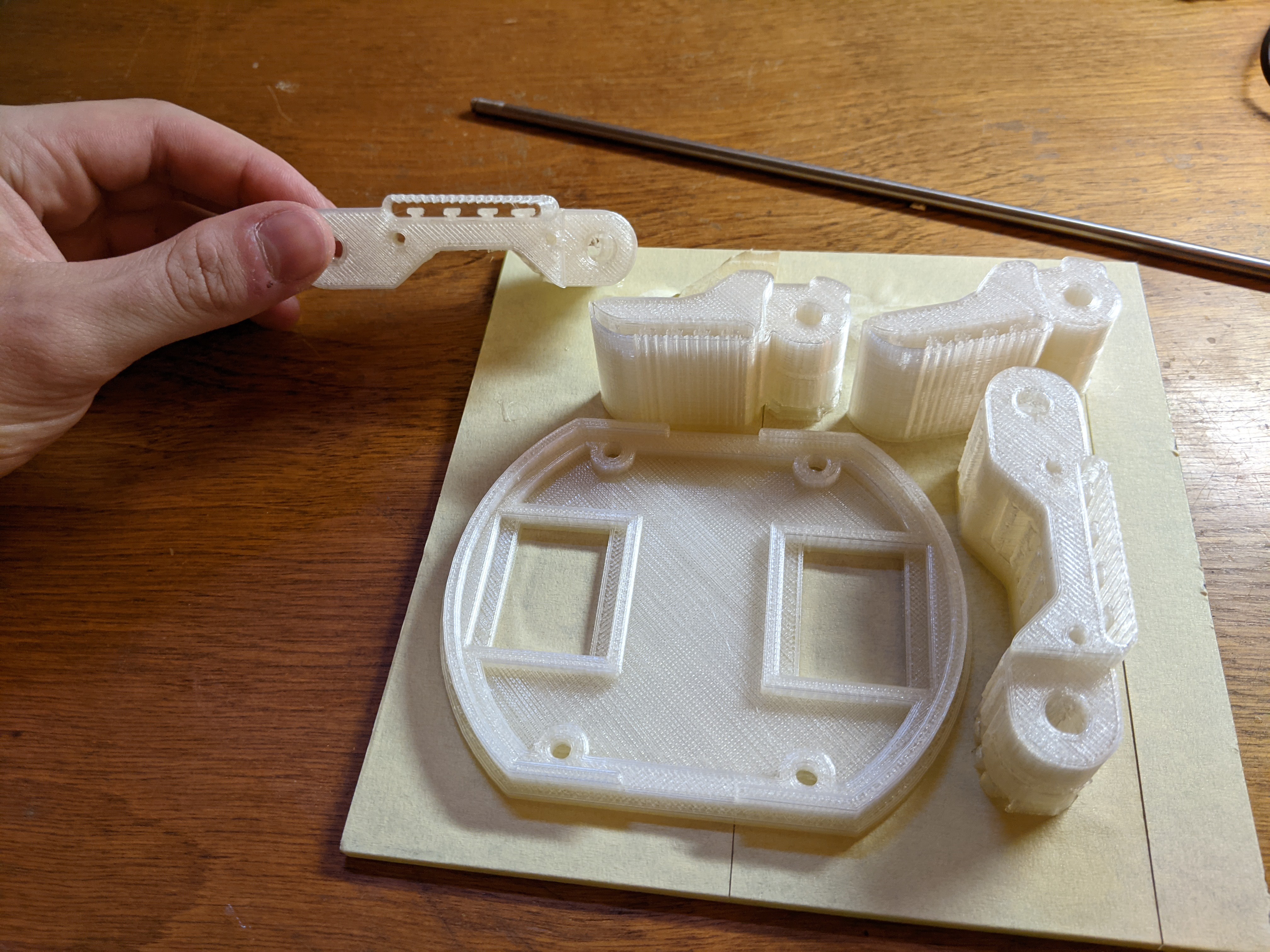
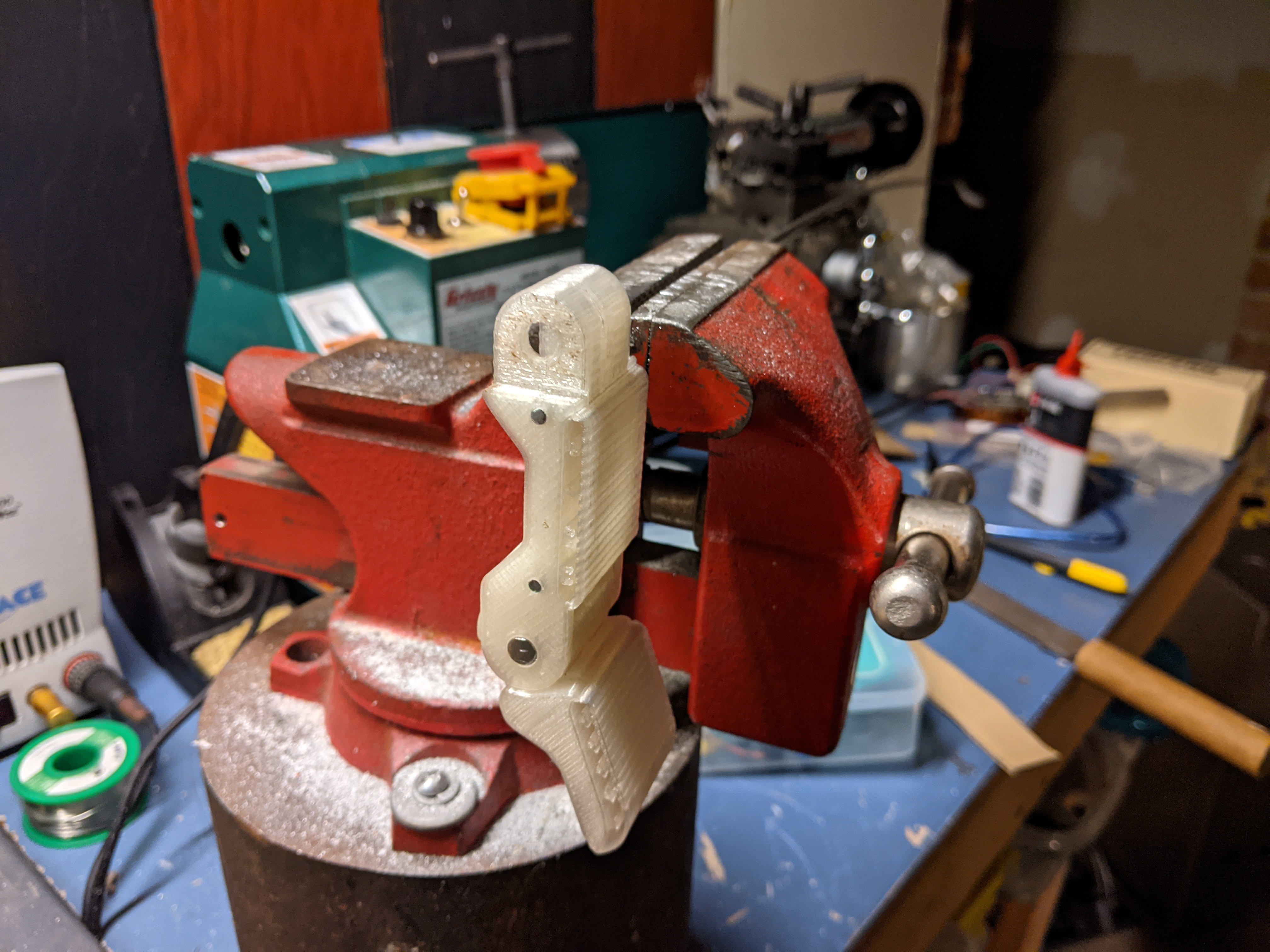
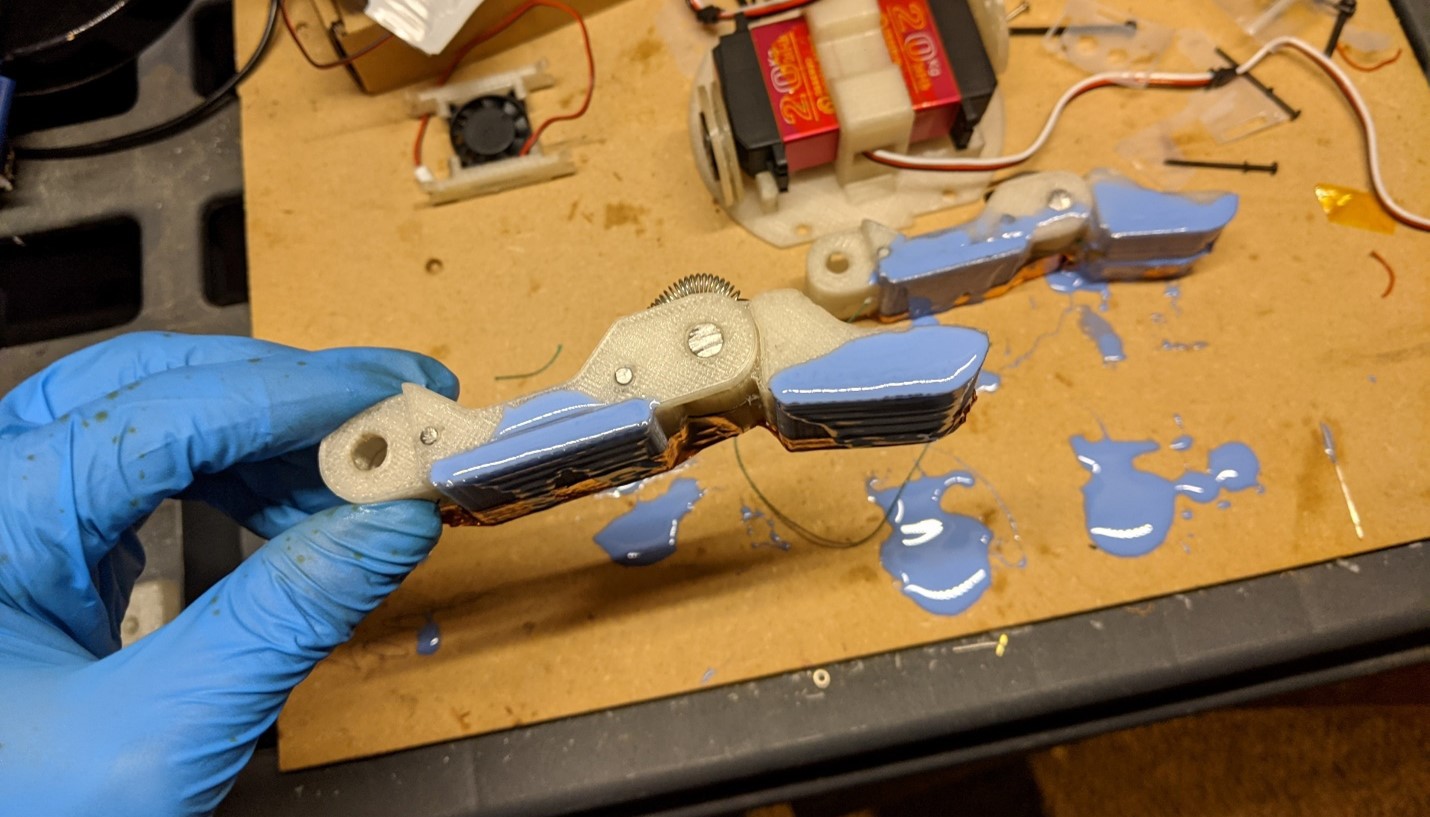
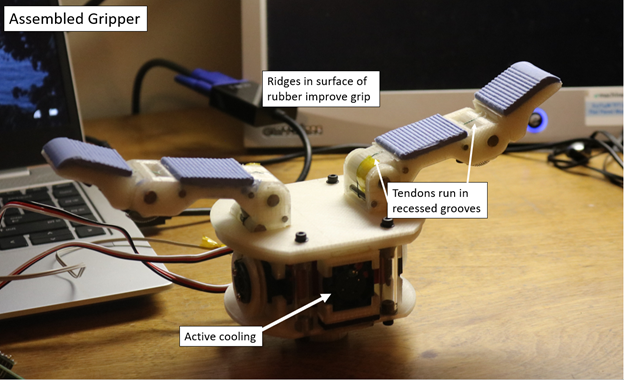
Discussions
Become a Hackaday.io Member
Create an account to leave a comment. Already have an account? Log In.