Cheaper Load Cells
So I was watching this teardown video of scales because Detail is considering them for one of his projects and I was wondering if I should chance the 300g load cells for more precision or stick with the planned 750g. I thought "If I could get the same precision as those 500g scales, I'd be fine with it."
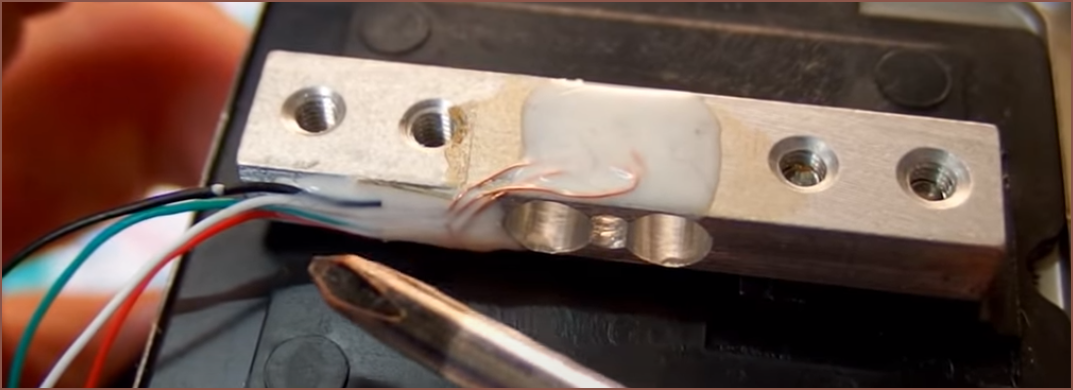
Of course it is. It's the 750g load cell I'm planning to use right now. It seems they're typically installed into 500g pocket precision scales, which makes sense considering they'd usually also have to hold a plate.
Well I go onto AliExpress to see their prices and they're low -- low enough that there was a possibility I could find an entire pocket scale cheaper than buying the load cells alone.
This is the price to beat:

And this is the cheapest scale + shipping I could find after an hour of searching manually (aka no AliTools):

I got AliTools into this to deepen my search, and I found this image:

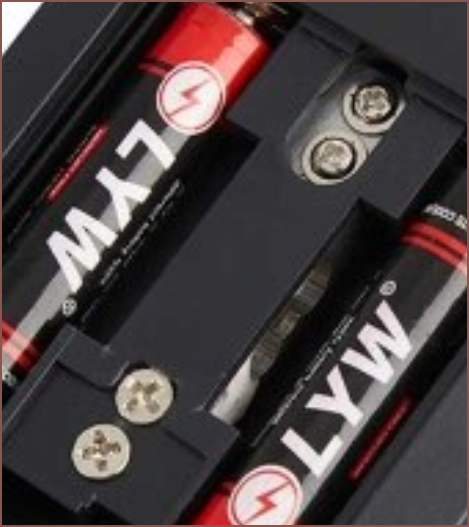
Yeahhhh! This has totally got to be the load cell I'm after. This is great news. The specs of the load cell recommend 10V, but the guy in the video measured only 2.48V going to the load cell. There are loads of pocket scales claiming 0.1 and 0.01g of precision with only 3V from the batteries! I can only imagine that the 0.01g scales just have better electronics or a different LCD. Reviews seem positive for the precision of these bargain-bin scales.
I did see a video on the listing and the (similar looking, but ultimately different) scale took like 1000ms to go from 0->100, which implies that whatever cheap circuity is used for pocket scales (likely the very popular HX711) does not obtain enough samples per second to be usable for this application. Remember that I need to be able to get a reading fast enough to generate the haptic feedback of a finger going through multiple actuation-force levels.
Another good thing to note is that the cell is able to get such precision even while mounted to cheap -- and somewhat thin looking -- plastic.
I have noticed that it's possible to get the 200g scales slightly cheaper than the 500g ones, which is probably perfectly fine for data-entry use cases. The max overload should be approx 900g anyway. I'll just play it safe with the 500g scales.
Cheaper chips
I put the new load cell source in the BOM spreadsheet and now the ADC sticks out as the most expensive single component. I found the same ADC on AliExpress from a new store (they only have 3 folowers) that sells a variety of chips:


And that's about it. So total savings are just under £28. That's an entire Tetrinsic with change right there.
Motor shortlist
I'm going to hold off buying all the motors as I still don't yet know if the one I've got is strong enough for the job. In the case that it's not strong enough (or I just want to save some BOM money), these are the motors I've found:
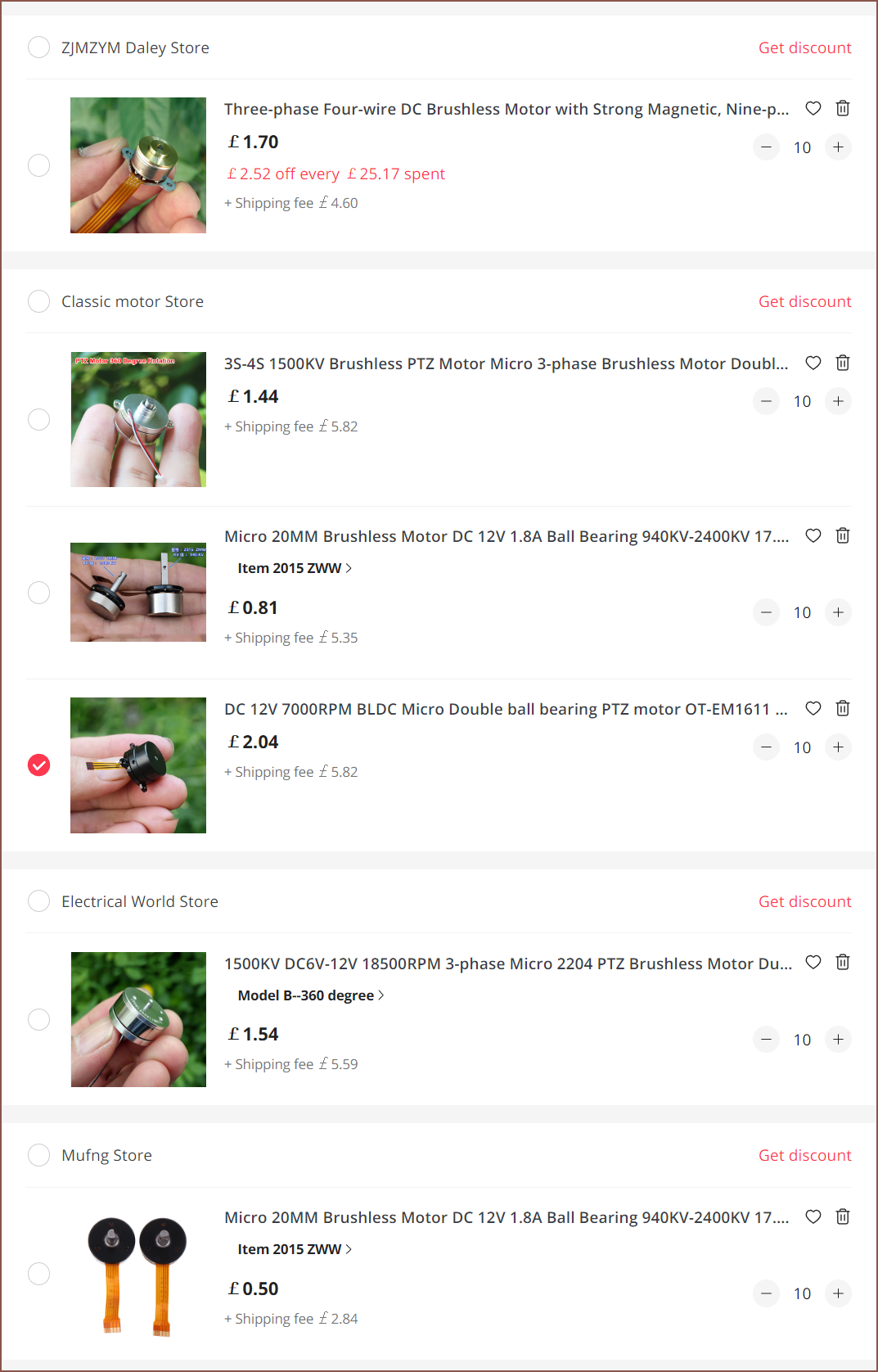
Wait...
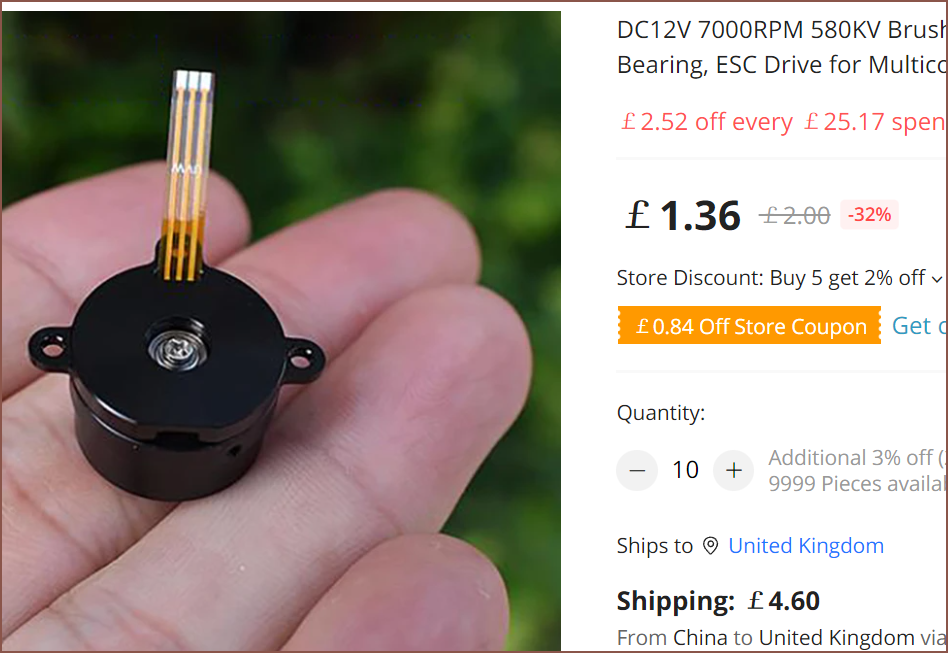
Anyway, as I was saying. The £1.70 one is the smallest and has an approx 1500KV. Then there's the 2010 and 2015 motors. These are the only one's I've found so far with torque data:
It's quite suprising that the motor that's 5mm shorter has 1/9th the torque. The larger one has a 940KV. The 50p listing is kind of suspicious because the title and listing all describe the 2015 model, yet all the product images are the 2010 model.
Those readings are concerning.
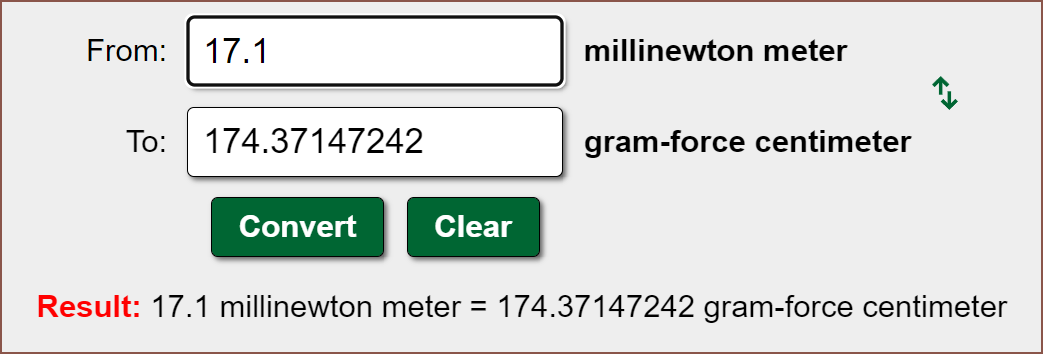
I think stator size should be a good indication of how strong a motor is. The 2015 motor has a 16.6mm diameter, 7mm thick stator. The 580KV I've just opened now is 13.1mm by 7mm. This site says "stator volume is a factor of motor torque assuming all other variables being equal" and "narrower stator width, [resulting] in a smaller rotational inertia that allows for faster RPM changes". That leads me to believe:
350 * (13.1/16.6)^2 = 218.0g
218g should be decent enough for science, right?
gets scale out and mounts it vertically
ehh... my fingers are actually hovering around that 220g-and-up ballpark. 240 seems to be the average.
Maybe I should go back to my OG strat of dual axis strain guages. Having to create some 2-axis resultant vector just doesn't sound like the greatest idea though, even if the current Tetent layout is already designed to always go back to the E column. Nah, cancel that idea; traditional gaming wouldn't be possible. I'm trying a fixed chain and it doesn't feel that great either.
I'm looking at the datasheets of "high dedent force encoders" and they're 210 +/- 70gf, so the 580KV motor might be good enough for science.
Conclusion
The idea of being able to tweak actuation forces down to a tenth of a gram is just not something your standard input device is able to do. Exciting! Someone could have a <10g or >100g "switch" and be able to effortlessly switch between them. The only real questions I've got is "will the BLDC motor be able to create the haptic responses I want?" and "Is the BLDC even strong enough for decent finger resistance?"
Lastly, I've noticed that the proposed chain path and PCB is awfully similar to what I was planning for Tetrinsic 2.0, so I'm renaming Tetrinsic Concept4 to Tetrinsic Gen 2X2. 2 x 2 = 4 anyway.
Solution mining... ends, in 15 days.
Discussions
Become a Hackaday.io Member
Create an account to leave a comment. Already have an account? Log In.