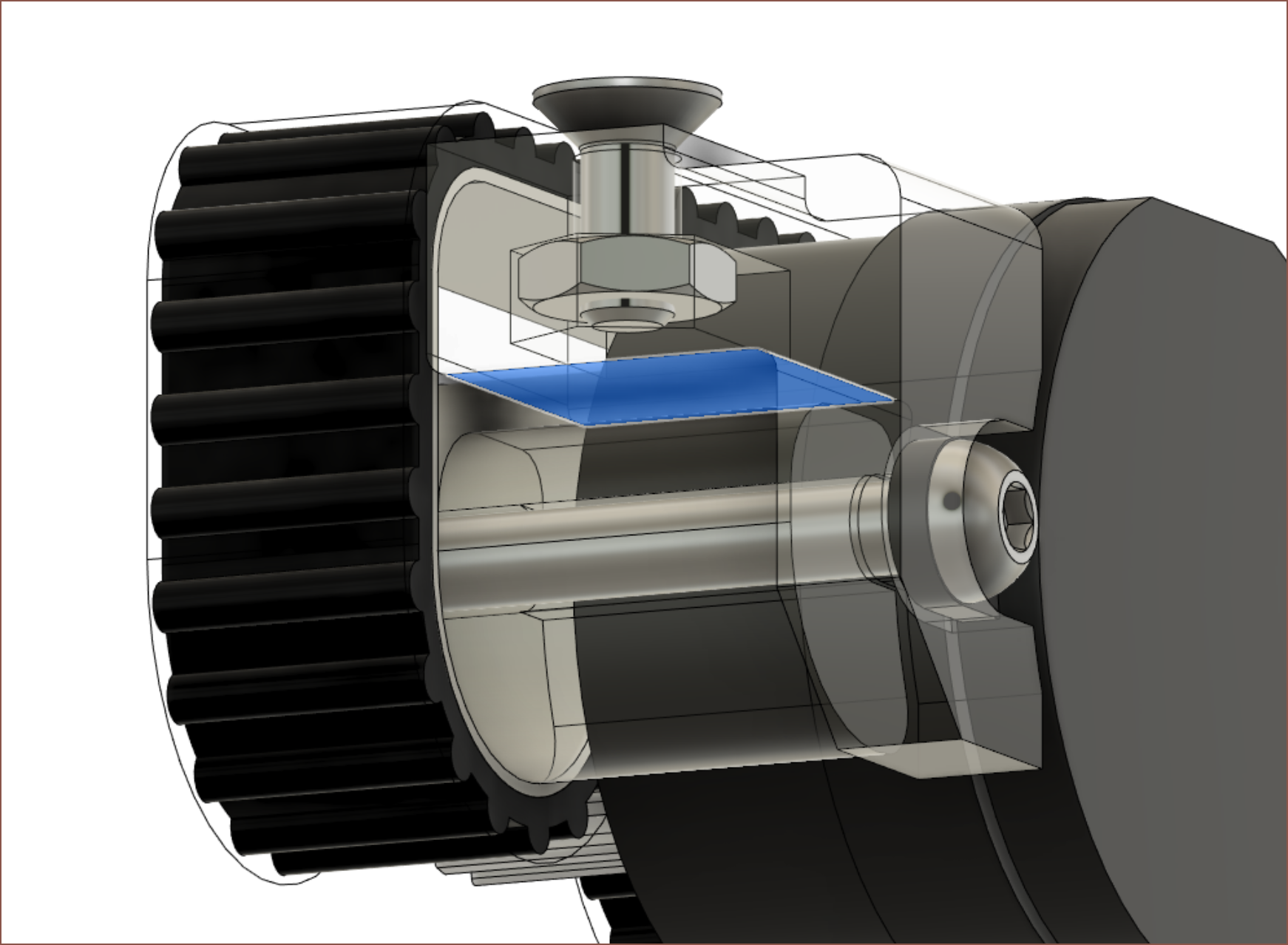
It's questionable if the part would even flex in a usable way, since I fear that the 3mm section will bend an unacceptable amount. Ideally, I want to sense up to 240g of force. Fusion360's simulation keeps giving me an unknown failure message so I can't get any data that way.
While small, it does seem to be perfectly FDM printable. I'm printing it out now.
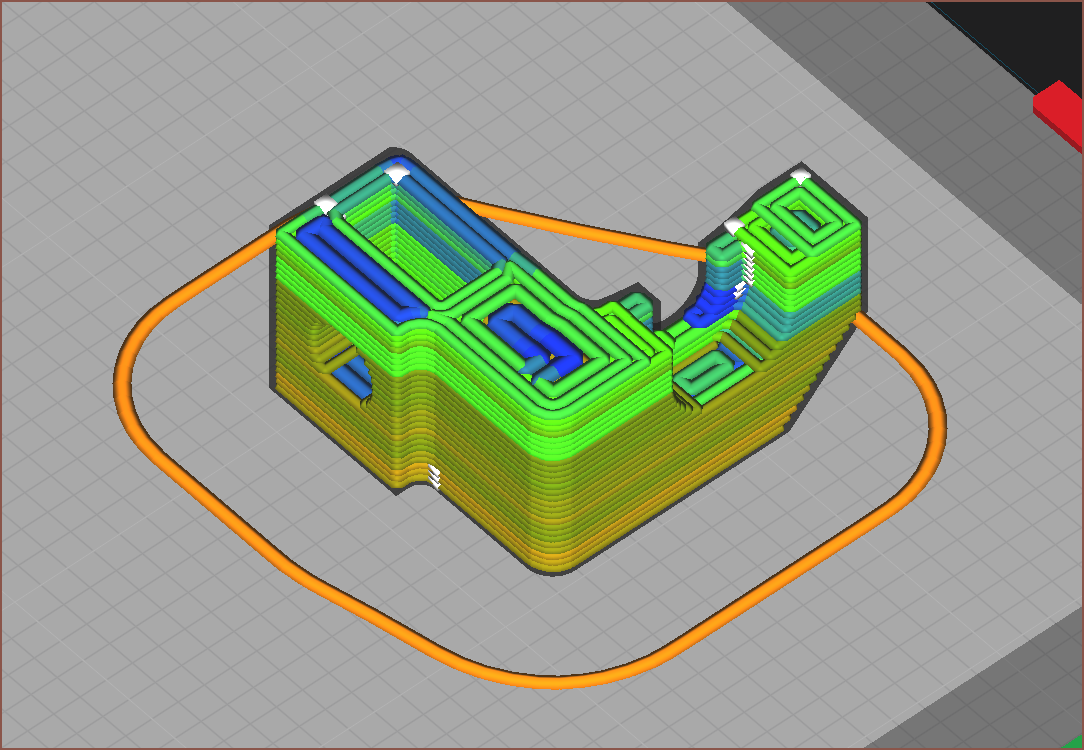
I might "mirror" this idea because the M2 countersunk screws are now right next to the belt:
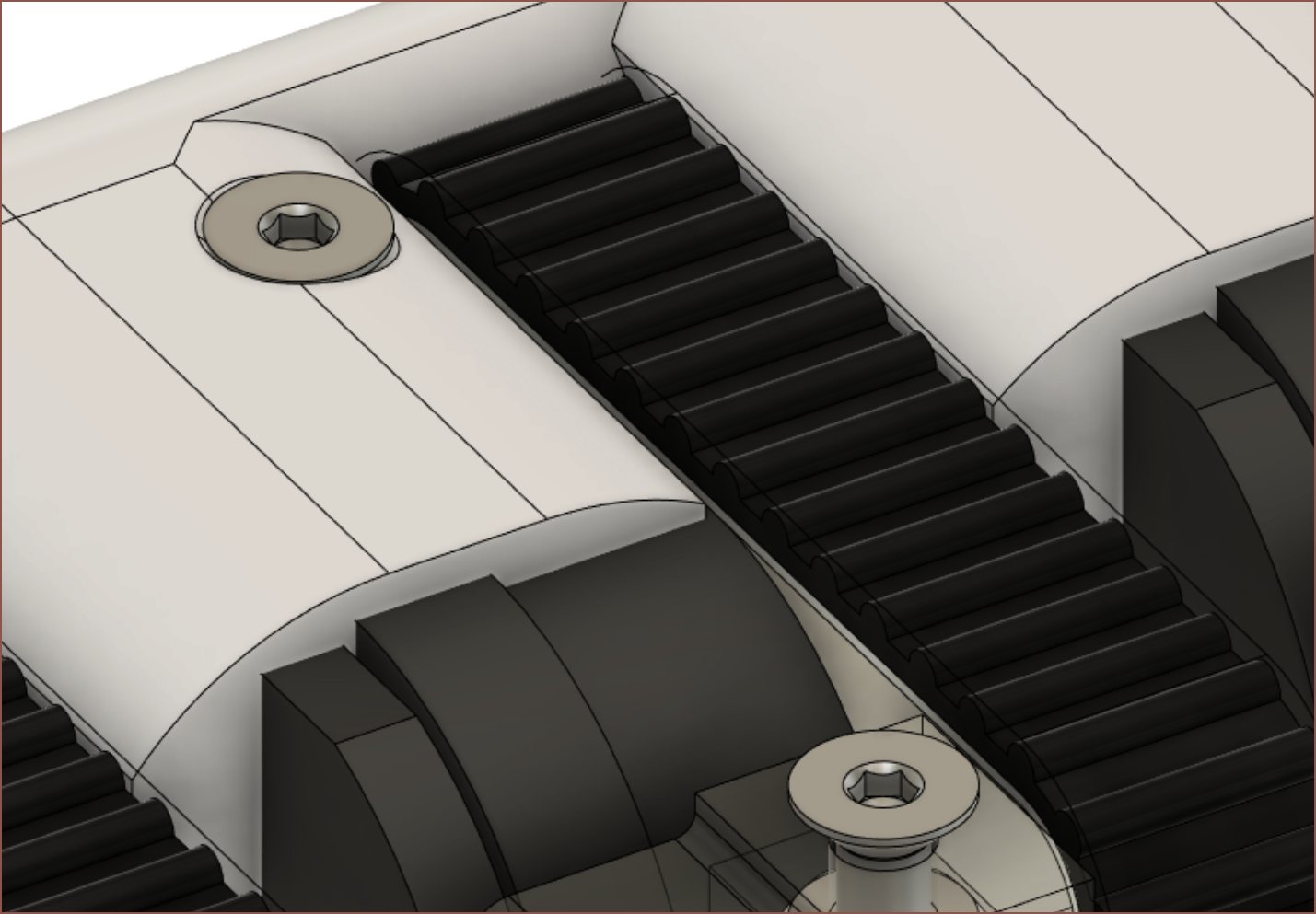
In other news, it looks like I'm going to have to abandon the idea of using 2 hall effect sensors instead of an absolute magnetic encoder due to this research I found.
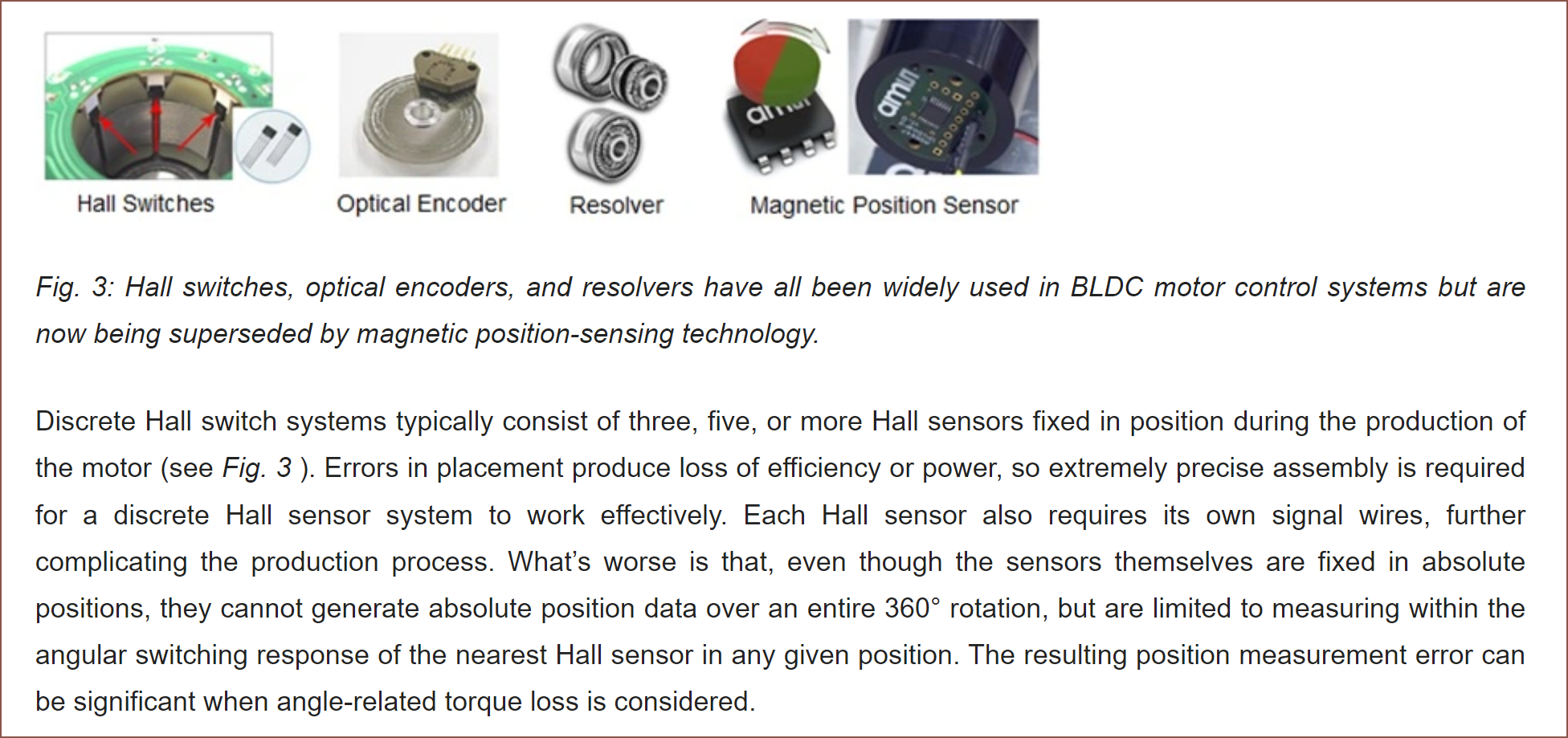
I've also been looking at my options instead of the TMC6300. The only reason why I started looking around was because of the tiny 3x3mm package, but it seems that I can just fry the board on a pan of sand:
Anyway, a more important reason to look for alternatives is because my human eye can only see Out Of Stock for the TMC6300-LA and the DRV8311 from Ti I also found. The STSPIN230 looks to be an option. While it's still in the same 3x3mm package, I can get it on alixpress for under £3 a chip.
Oh, nice the print is done.
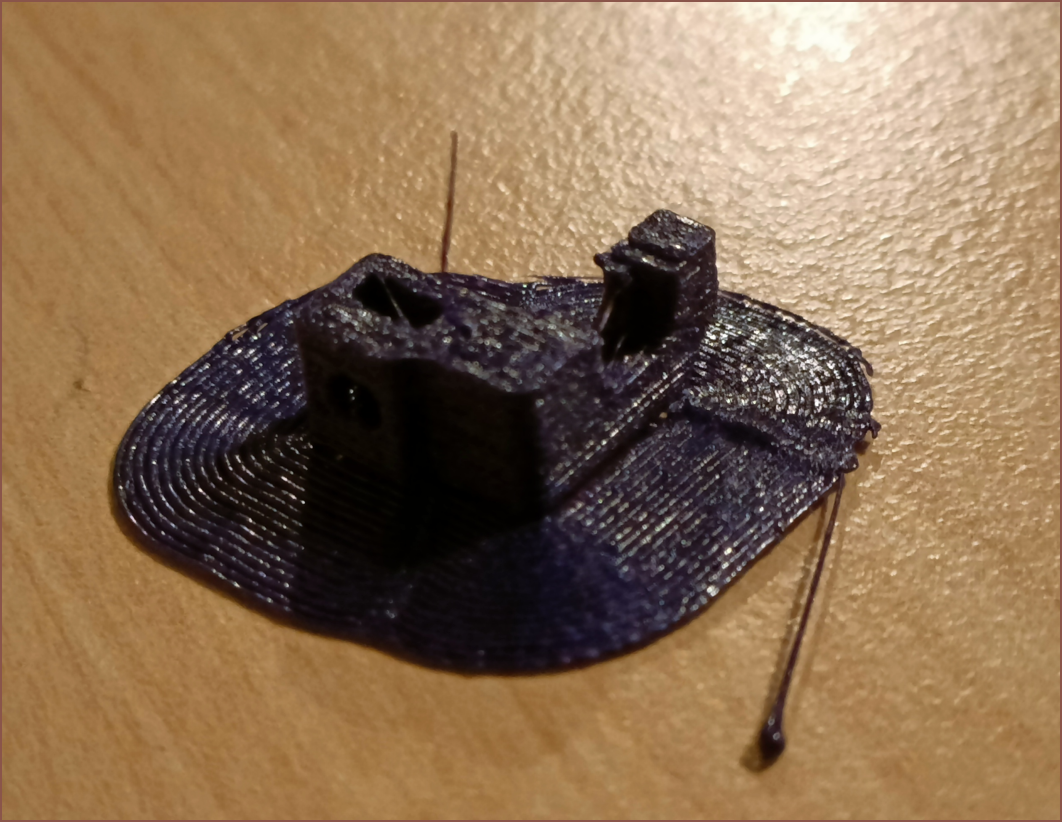
Hm... wait couldn't I just...
[some minutes later]
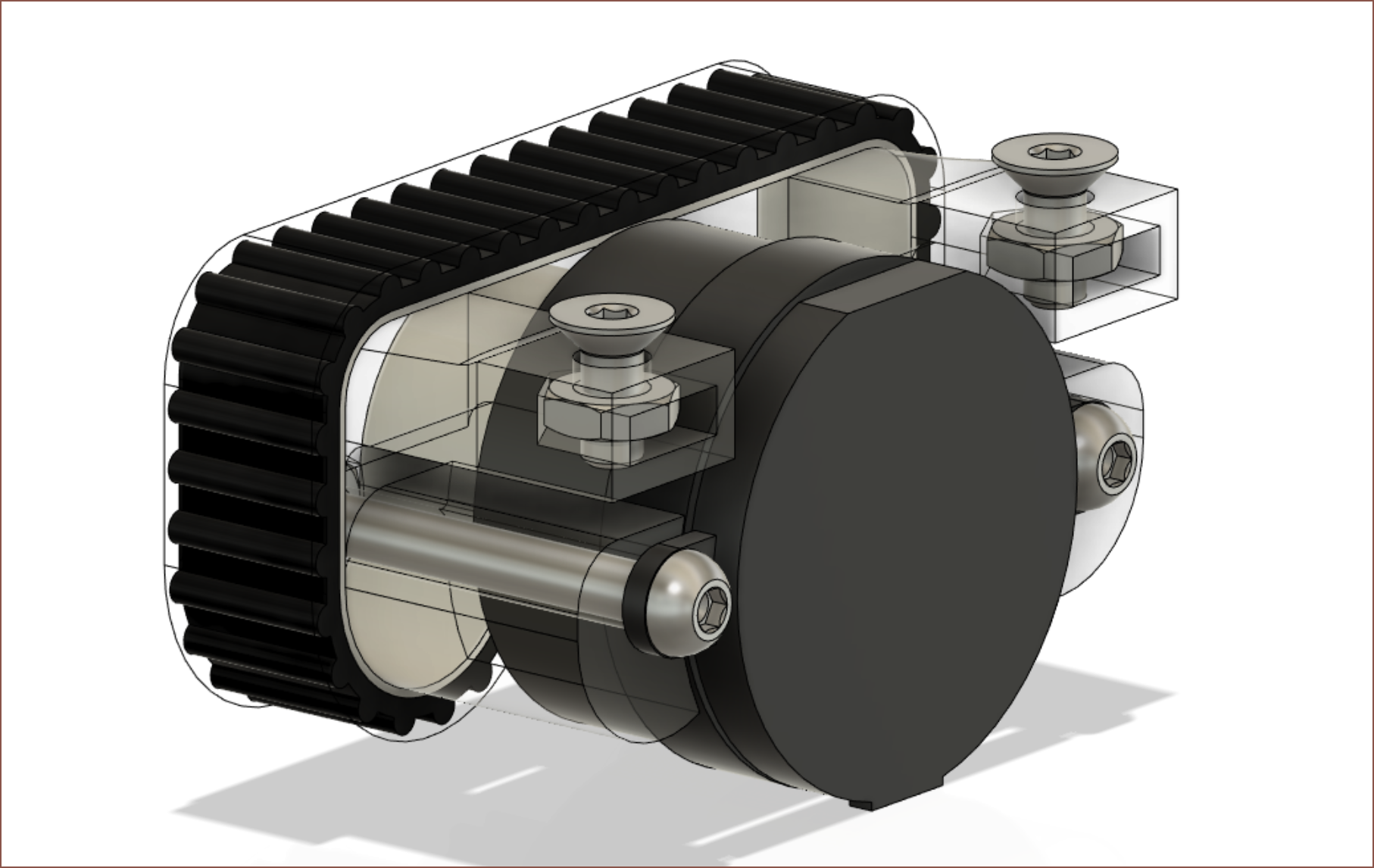
Yeah. Now everything's 1 piece not 3 and I've now got 6x10mm of area for the strain guages, which increases my options a bit. It seems that a 7mm wide area would be ideal though, which would require me to increase the overall key length to 34mm.
CheckingTool: - Length increased - Keycap_Flat length increased from 24 to 26mm. - File repaired - Belt length: 97.58mm - Recommendation: Reduce belt length to 96.5mm to use a 96mm belt. - Implemented changes to Tetent [gd0090] concept without conflicts. -- The new length (106mm) does not propose a conflict in Teti [gd0022]. - The changes can be implemented into Tetent Timespy [gd0136] without expected conflicts. - The increased length of the Tetrinsic Switch [gd0041] is expected to increase ergonomics for larger hands.
Ok everything checks out it seems.
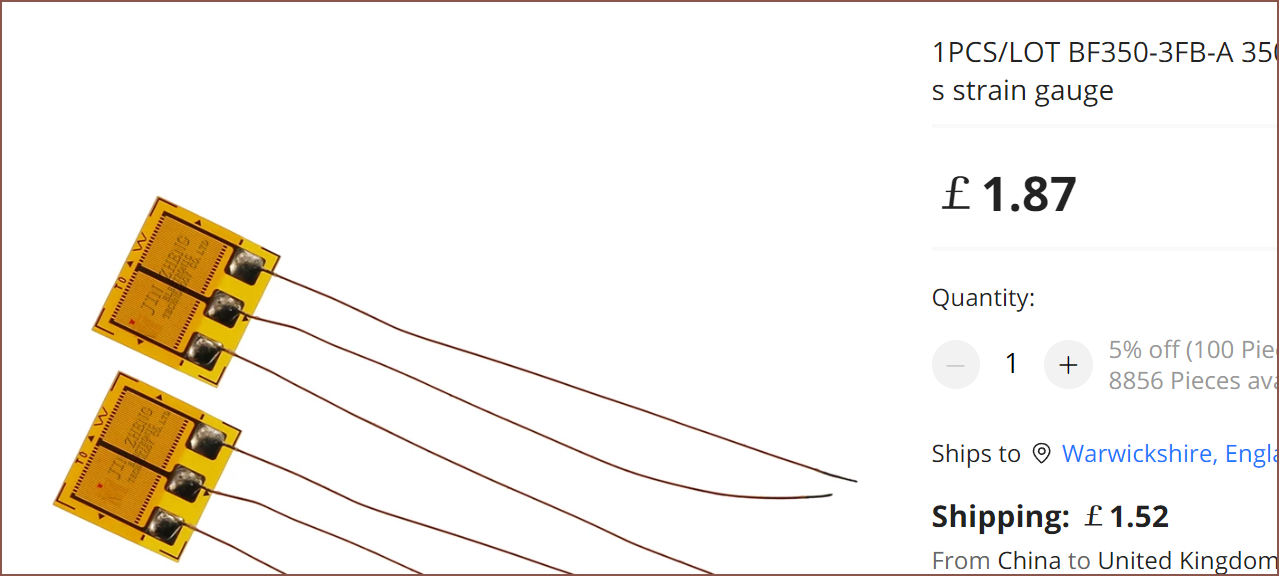
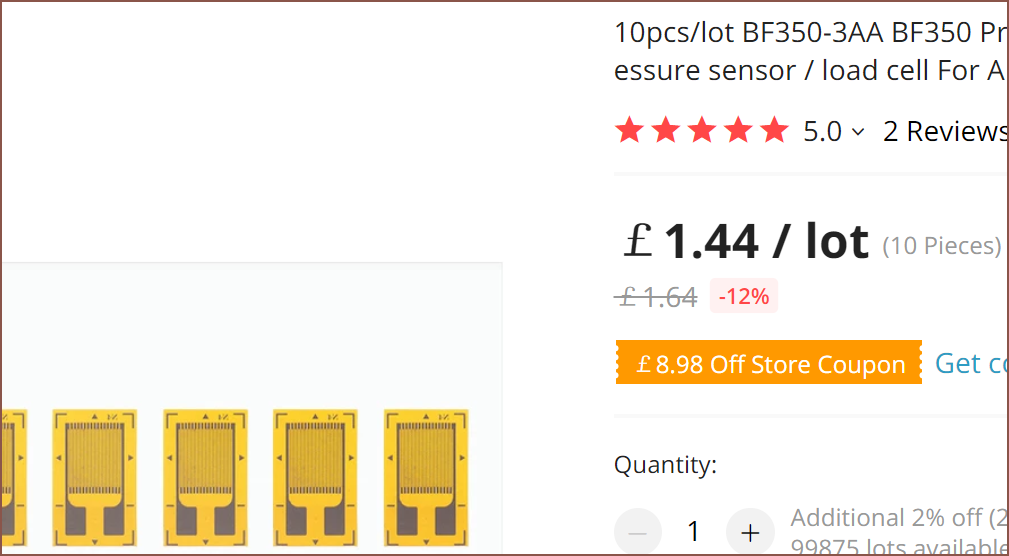
[Some research later]
Ok I've read https://www.allaboutcircuits.com/textbook/direct-current/chpt-9/strain-gauges/ and, with the way I'm straining the key, I only need 2 mounted in the area. The other two need to be nearby to account for temperature differences. Ideally, I'd have whatever sensor's in this:
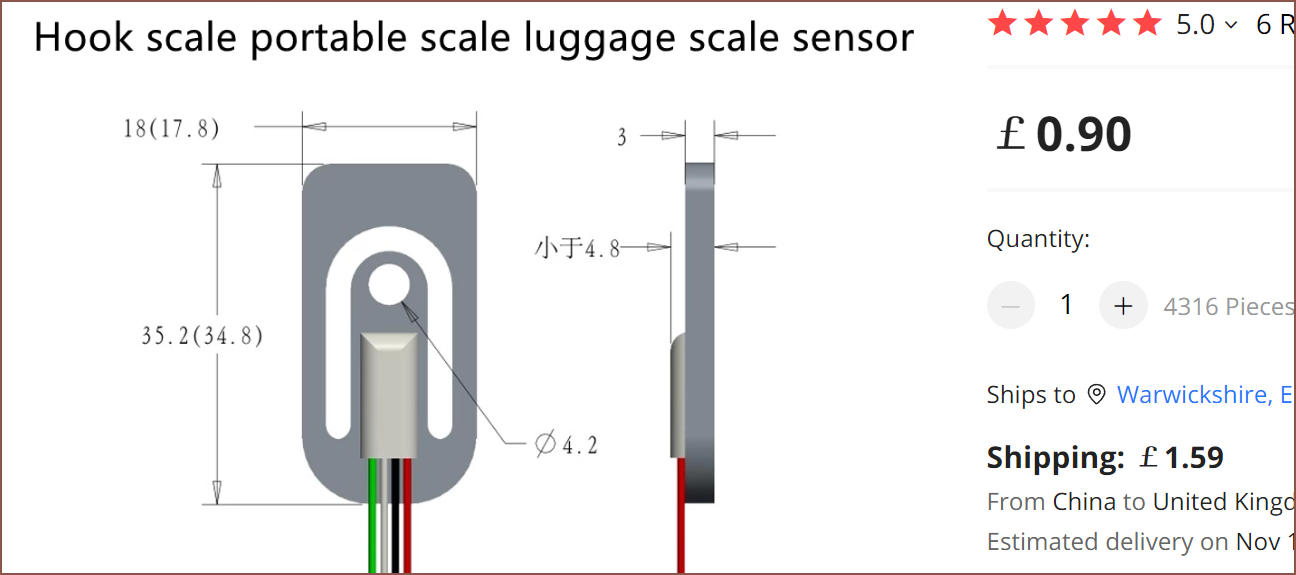

[some more research later]
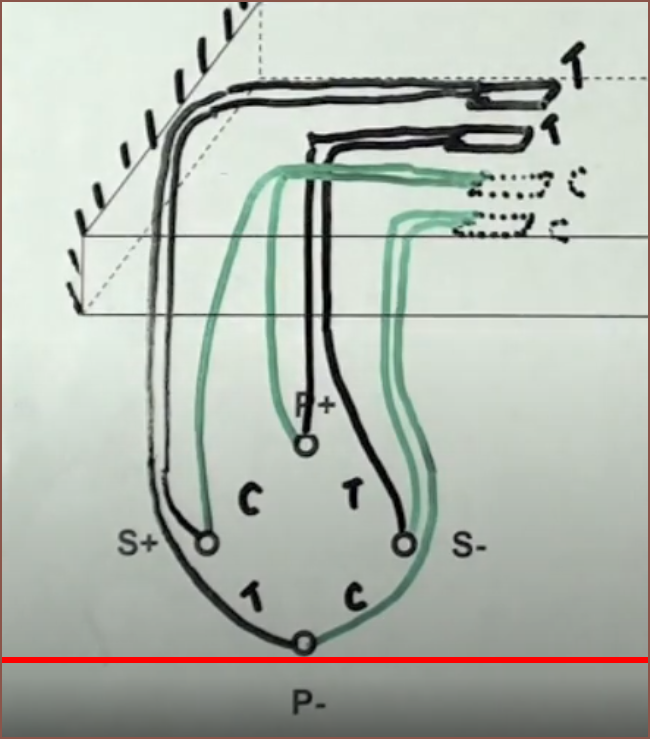
Right... I could stick the green strain guages to each of the two beams and have the other two somewhere else that doesn't flex.
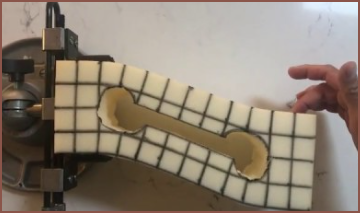
Second print
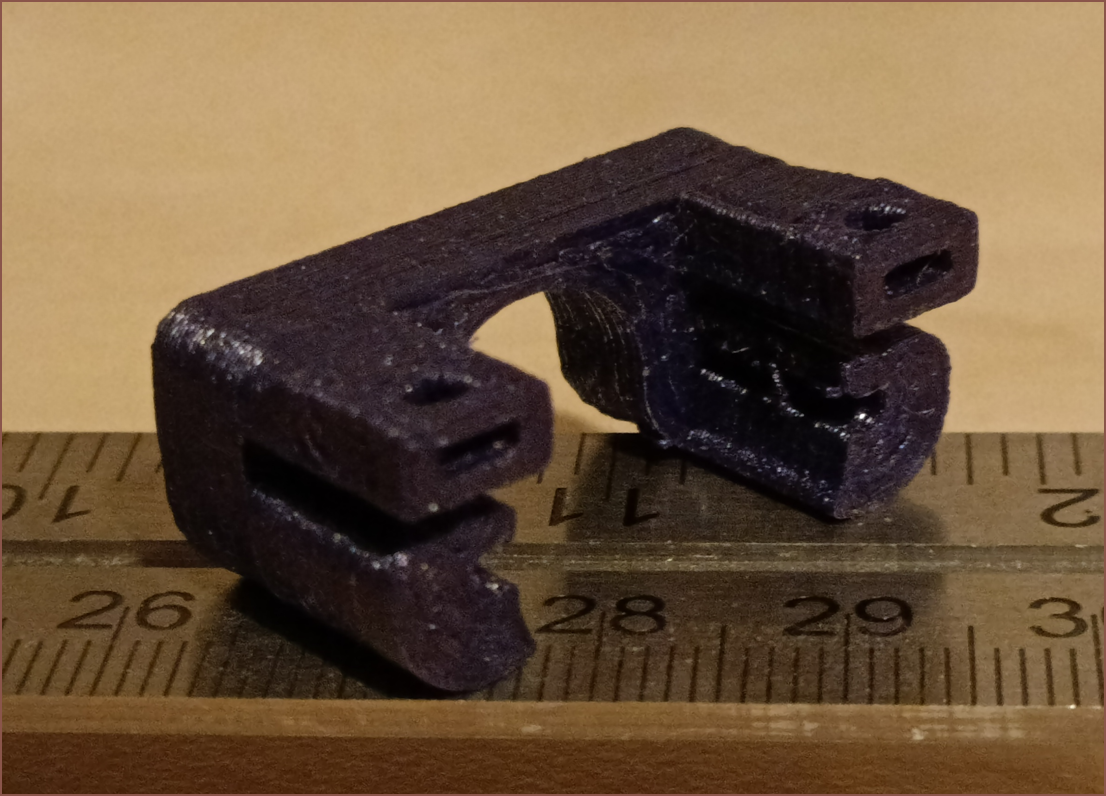
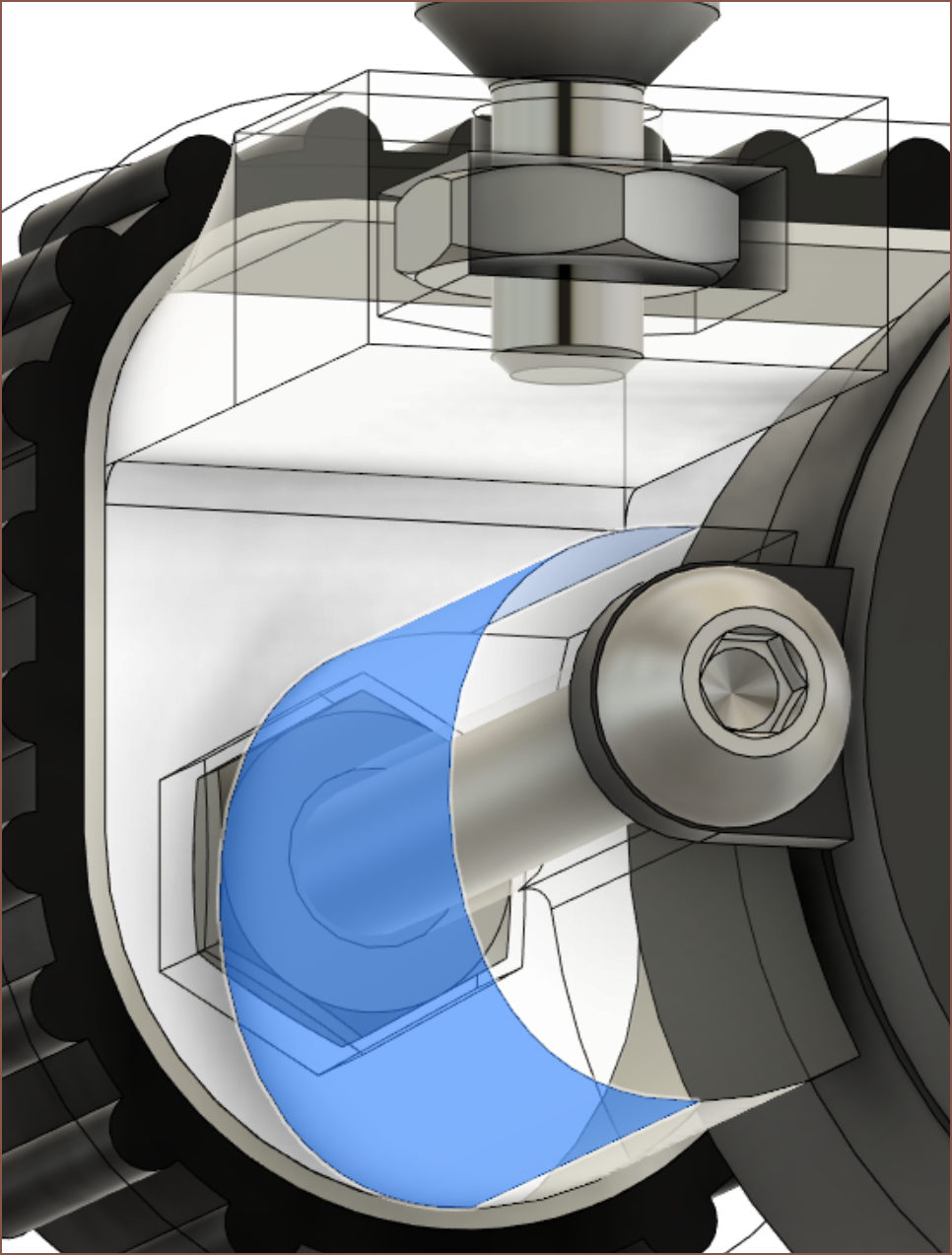
[after more research]
The absolute encoder situation is looking a lot less favourable. With a 1.2mm PCB, the length is worryingly close to the 20mm limit. I was hoping that I was going to get under 19mm for the #Tetent Timespy [gd0136].
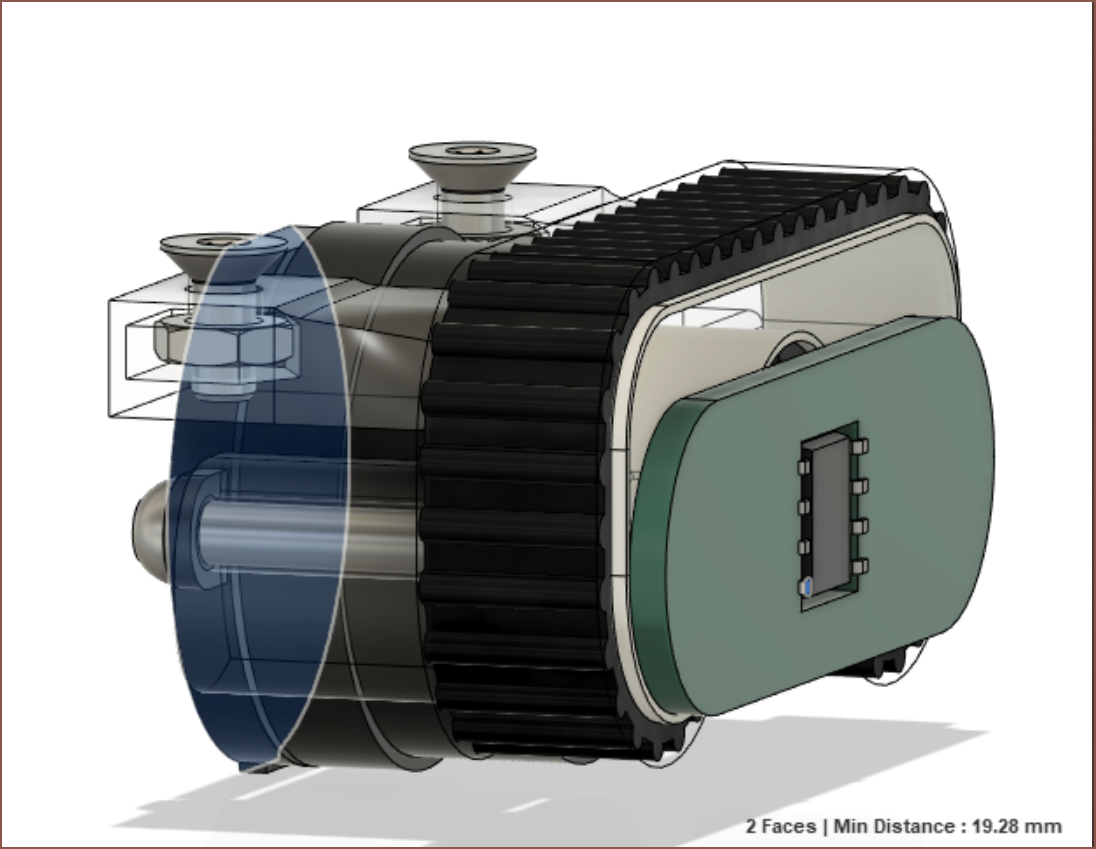
Anyway, I started writing this project log at 16:00 and it's currently 23:00 so I think I should stop here.
Discussions
Become a Hackaday.io Member
Create an account to leave a comment. Already have an account? Log In.
Wow. To think that Me In The Past knew about the DRV8311 but I couldn't go for it at the time because it was out of stock...
Are you sure? yes | no