Starting the grind at 14:30, I found out that you can drag the Fusion 360 tabs out to put them in new windows (see below). This helps loads because I could now view the schematic and PCB side by side.
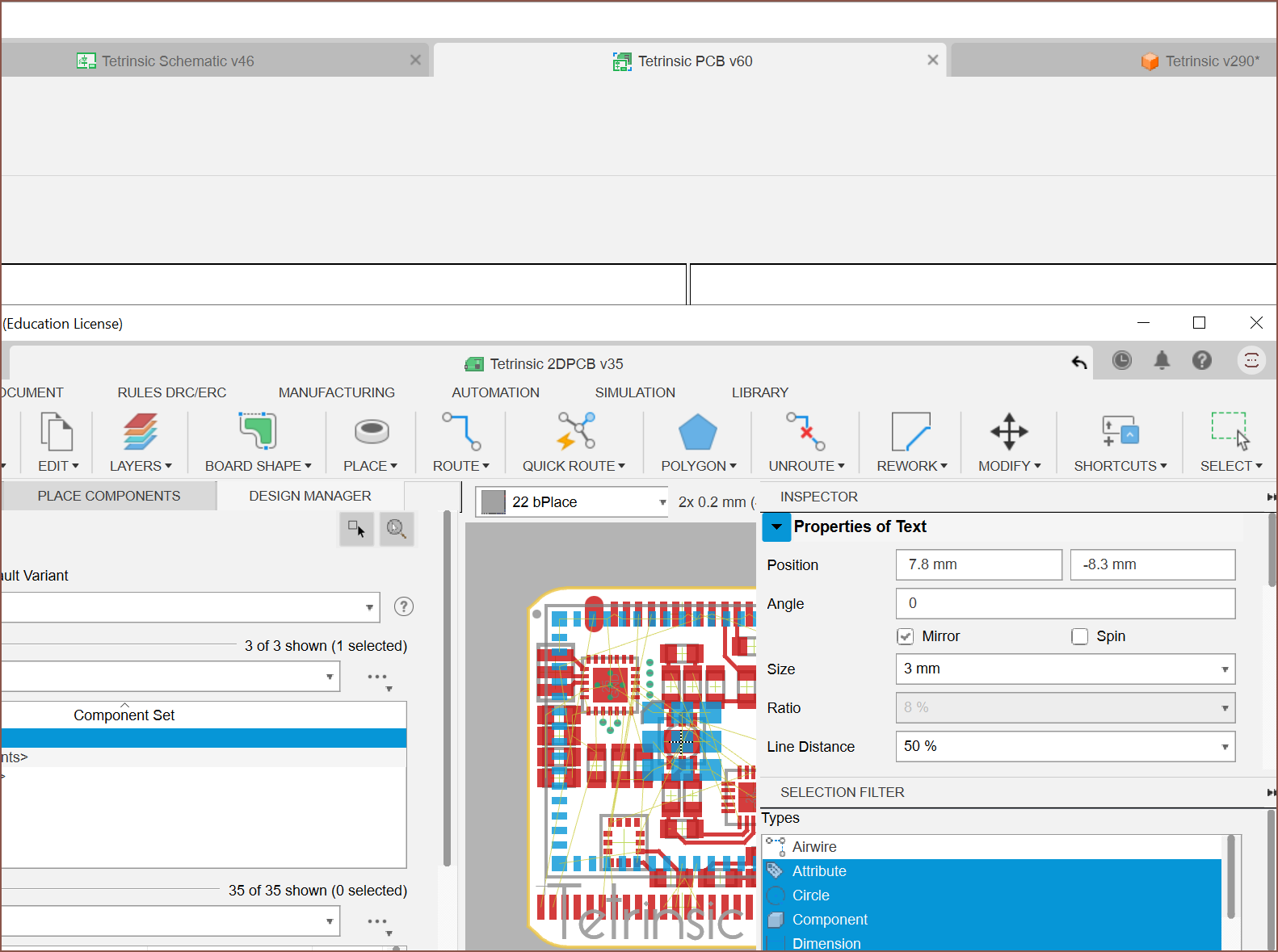
Then I found out how to change the colours of the layers and opted for ones that were more comfortable to my eyes. I also decided that I was going to have 1 interior signal layer and one GND copper pour. I put the pour under the Top layer to potentially help with heat dissipation from the BLDC controller.
By 16:30, I had gotten some connections onto the BLDC:
It was already starting to look like mounting the MINI-1U module on the back was a great idea. It would take much more space to route out if all components were on the same side. Unfortunately, I had to fint in a via so I had to do a select-and-move-surgery:
Oh, and I changed the EXPn index to start from 0.
What you see above was very nice to see. It's what happens when I join up an incomplete trace. It's now one long trace. In EasyEDA, they'd be seperate entities and so I'd have a lot of complete but segmented traces.
2 crashes later, it's now 20:30 and I've tweaked the masterpad order and have now fully connected the BLDC controller, the IMU and managed to get all but EXP0 (connected to IO0) on analog capable pins (which gives me the most flexibility for implementing features).
Then I remember about POSITION, which is on the right other side of this masterpad and it needs an analog-capable pin. I just used the last one. After looking at my options, I decided to move the MISO pin over and then have a long trace to POSITION:
After a 30 minute break staring at trees (and imagining they're actually all virtual like I'm wearing a futuristic VR headset), I come back rejuvinated with the goal in mind to make #Leti so that I can work on projects while I stand/walk outside.
At 21:30, I found out how the differental pair worked. While I didn't do this for the ADC inputs, the routes I neded up with seemed close enough to a differential pair anyway. Oh, and I watched this video that helped speed up my tracing workflow:
I thought it was a bit early, but I wanted to give the copper pour feature a go. I selected "Copper pour from outline", cliced the edge of the board and it actually worked. I had to click on the outline, not the pour, to get the inspector to activate, and then I changed the net to GND.
Here's what everything got connected to on the MINI-1U:
And here's the pinout of the masterpad:
The order of the I2S pins were chosen based on one of Adafruits boards:
Discussions
Become a Hackaday.io Member
Create an account to leave a comment. Already have an account? Log In.