Using the 3Devo my university just happens to have, I was able to extrude some PBT. However there were voids and the thickness was unstable.
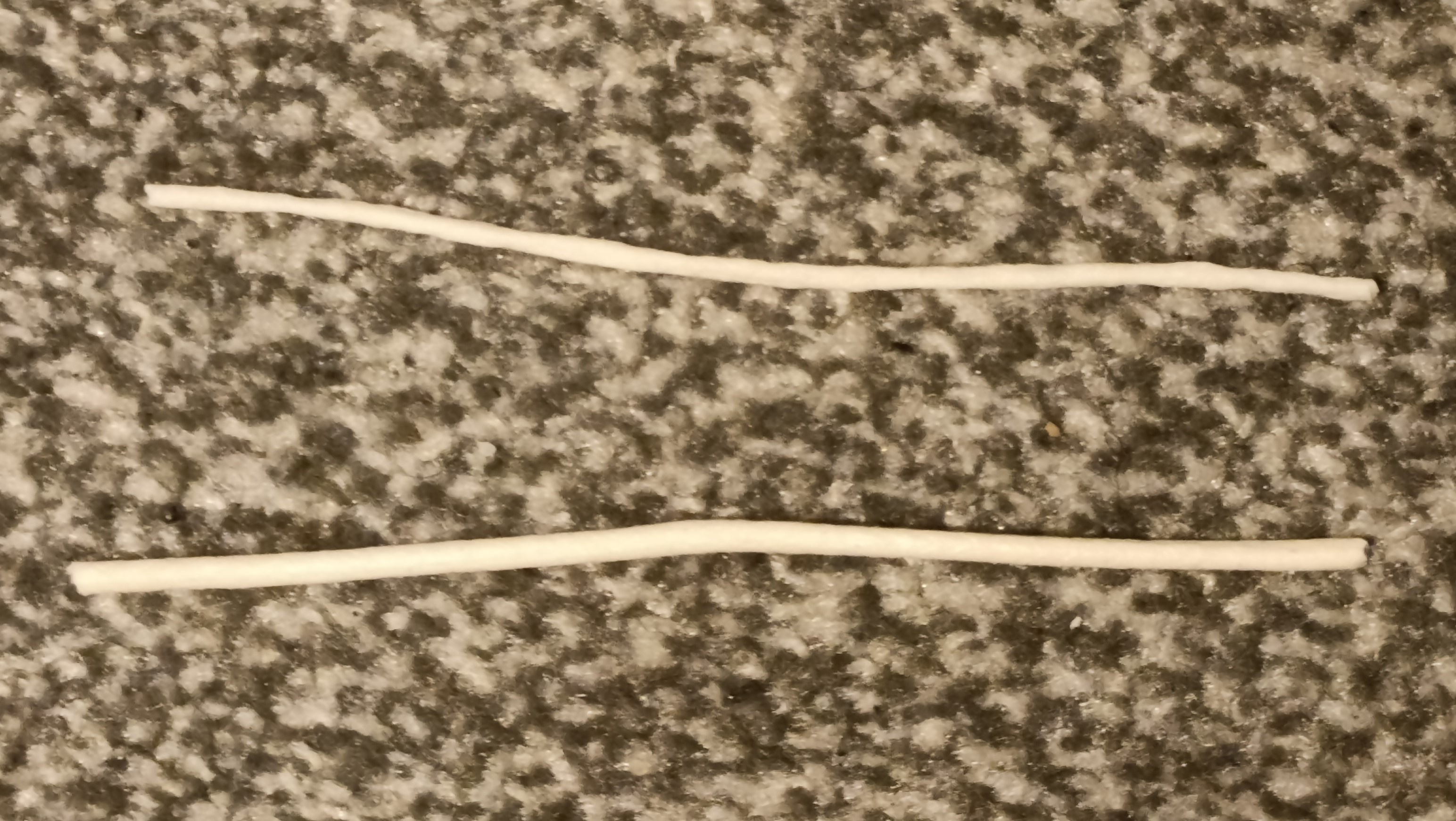
I tried again on another day, and after finding recommended temperatures of 260C, I got something a tad better but still not great (top is first attempt, bottom is second) or consistent.
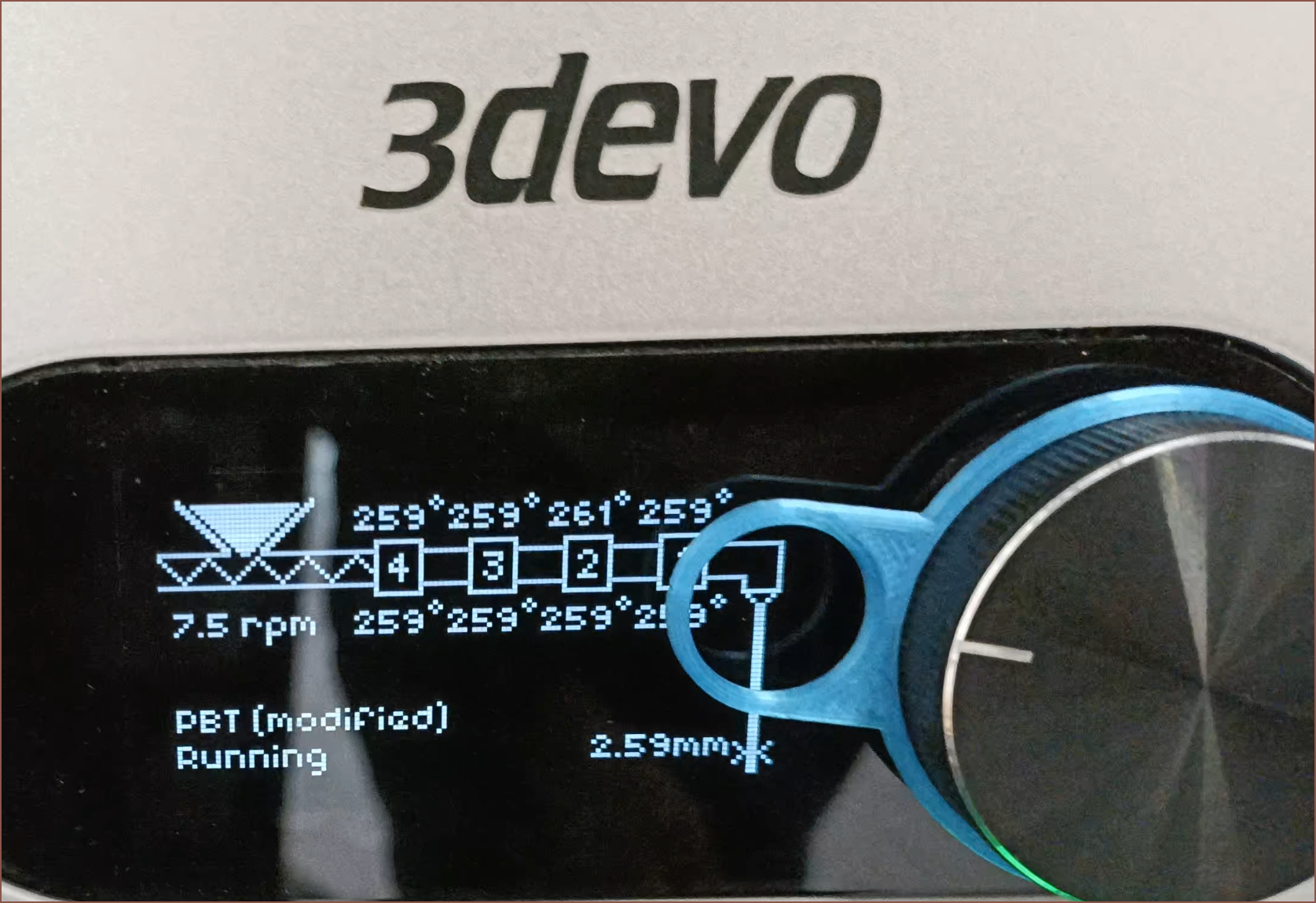
I thought to add some PET for processability, and was able to get something barely printer-usable after hours of extruding:
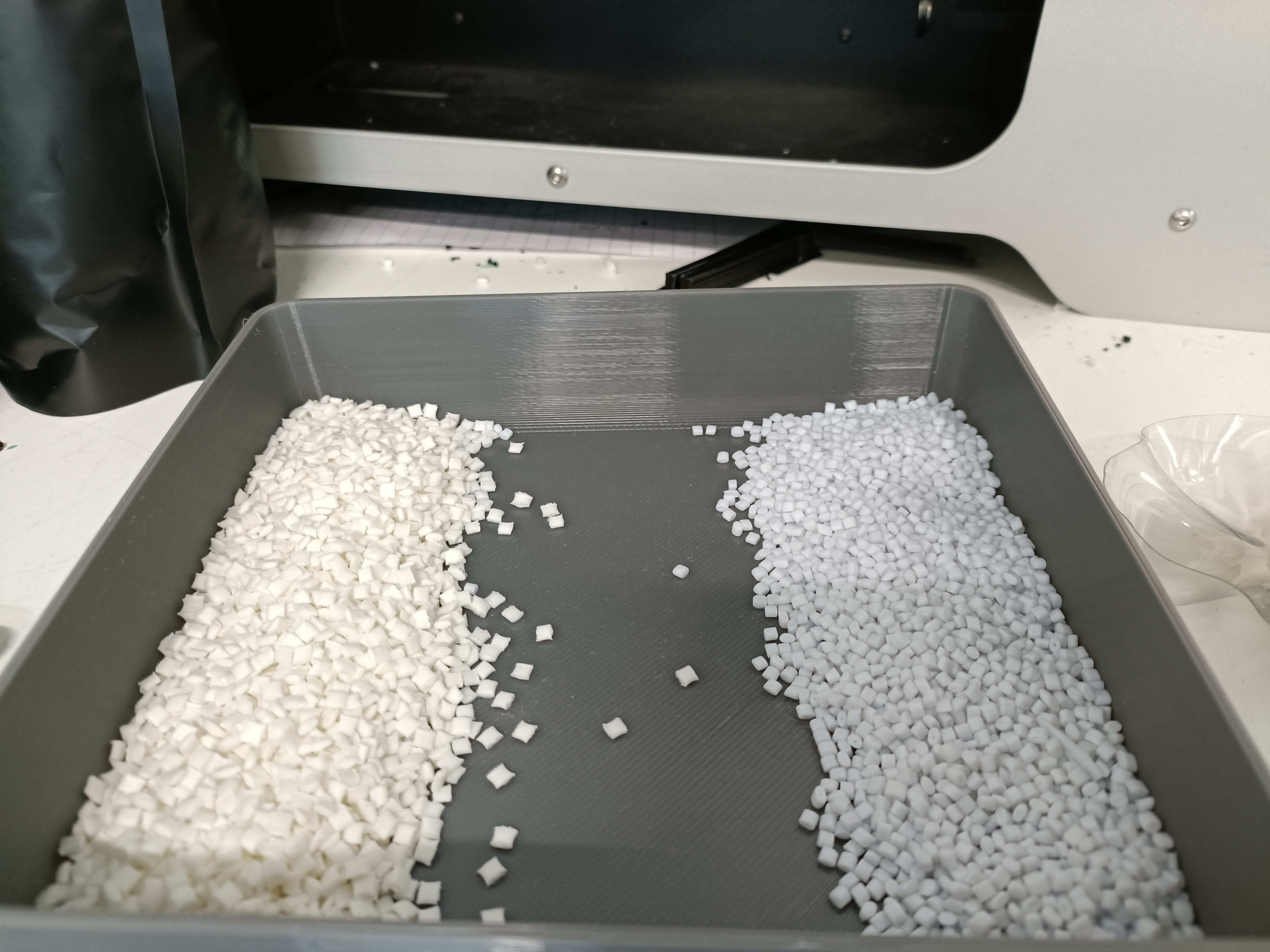
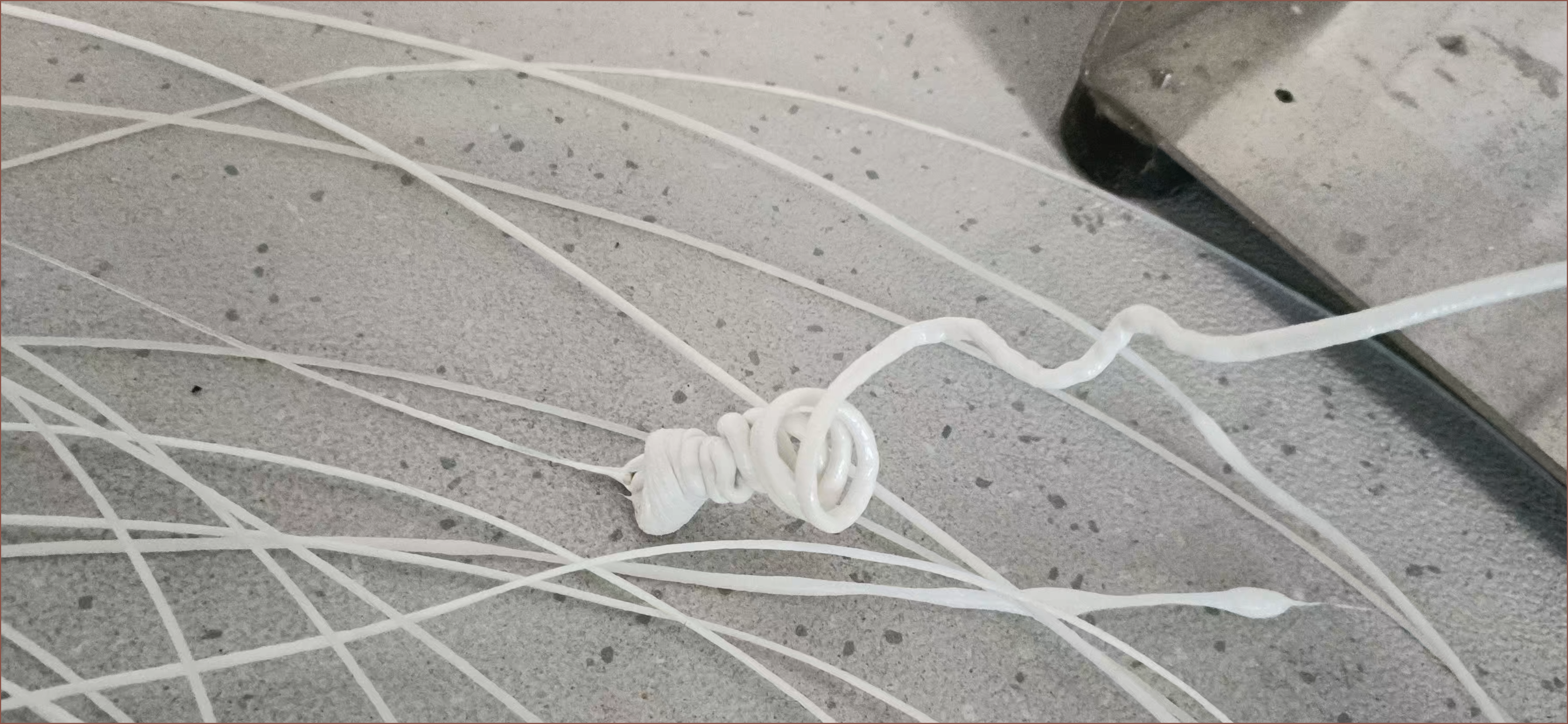
Some takeaways from the PBT / PET blend:
- 50% PET caused the output to be predominantly PET
- 0% PET brought back the PBT, but it was as volatile as before
- Somewhere inbetween has a nice flowability
- PET flows really nicely and opaque "grey" pellets became transparent.
- I believe the PBT re crystalizes but the PET doesn't.
- the "grey" looks blue tinted to me
- Pure PET is brittle
- It seems easier to work with if the PBT crystalizes as fast as possible
My hypothesis is that the 90 degree angle in the 3Devo is not playing nicely with the glass fibre reinforced pellets, meaning the PBT will clog like cholesterol in an artery and the PET would melt past it.
Takeaways from using the 3Devo:
- Heating takes ages.
- even more so if individual heaters are set to different temperatures
- Seeing if my changes had an effect takes ages.
- Sometimes it's not clear if the pellets are actually feeding into the extruder. It seems that, unlike a 3D printer, the motor will happily keep spining the auger even if no plastic is being extruded.
- Fans need to be strong enough to cool, but not strong enough to cause the filament to move around
Discussions
Become a Hackaday.io Member
Create an account to leave a comment. Already have an account? Log In.