<< 13/06/2024 >>
First of all – ORDERS ARE OPEN! You can now order a complete set of parts to build your Inova SLS printer. Two batches of 15 sets are currently open. One for delivery inSeptember ’24, the other in October ’24. Check out ourstore for all the details.
Secondly – Inova is becoming open source as promised. We’ve started with the hardware, which means that:
- full BOMs
- schematics for the GATE1 and ZERO1 expansion boards
- the complete Live! as well as a downloadable 3D model of the Inova printer
are now available in the members section.
We have also done most of the FW and SW pre-publishing activities. So, the SLS4All Compact software package will also be released very soon.
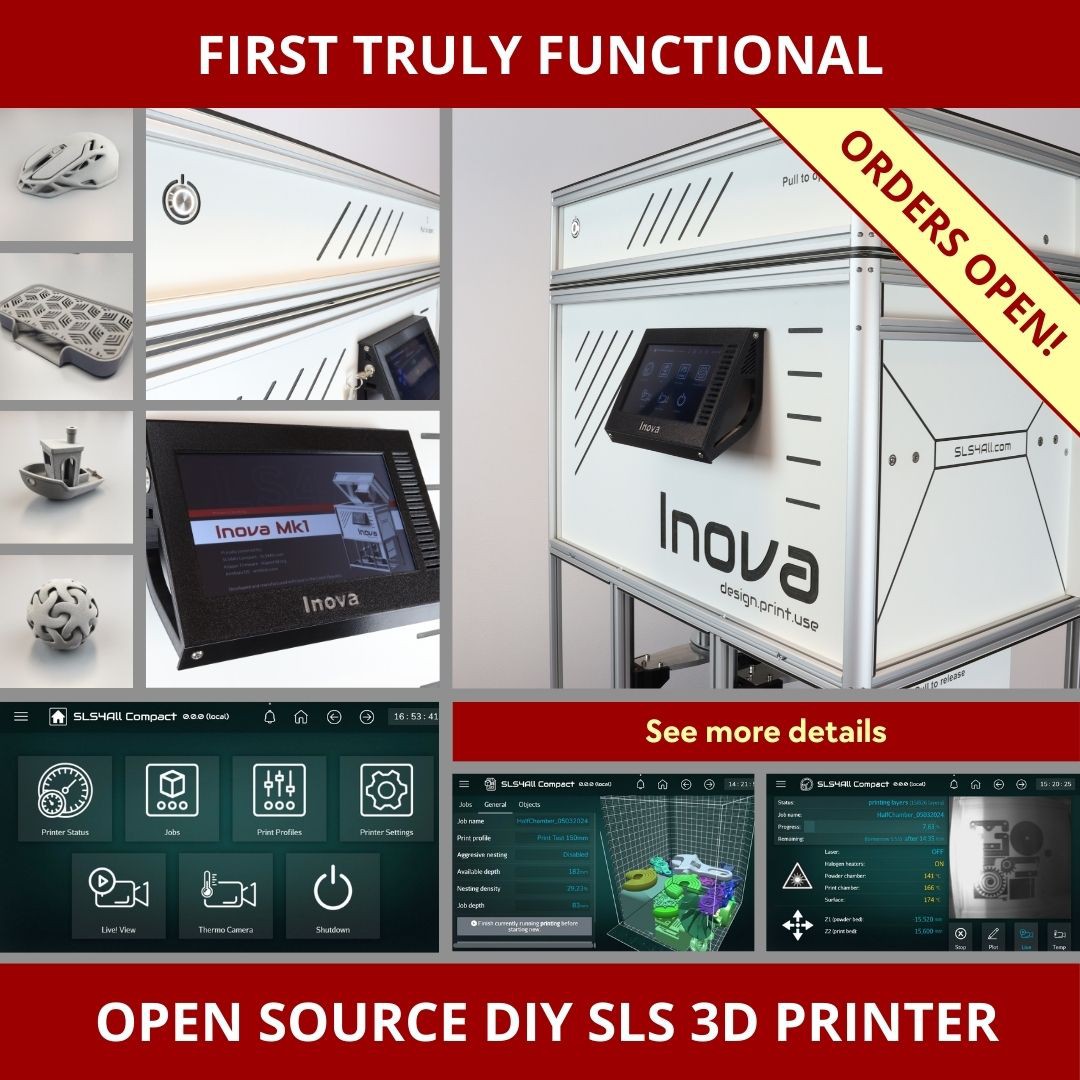
<< 23/03/2024 >>
It took me almost 3.5 years, but I finally achieved the print quality I dreamed of when I started this project. I'm really happy that the printer is working reliably and its release time is fast approaching. Below is a small sample of recen print outputs.
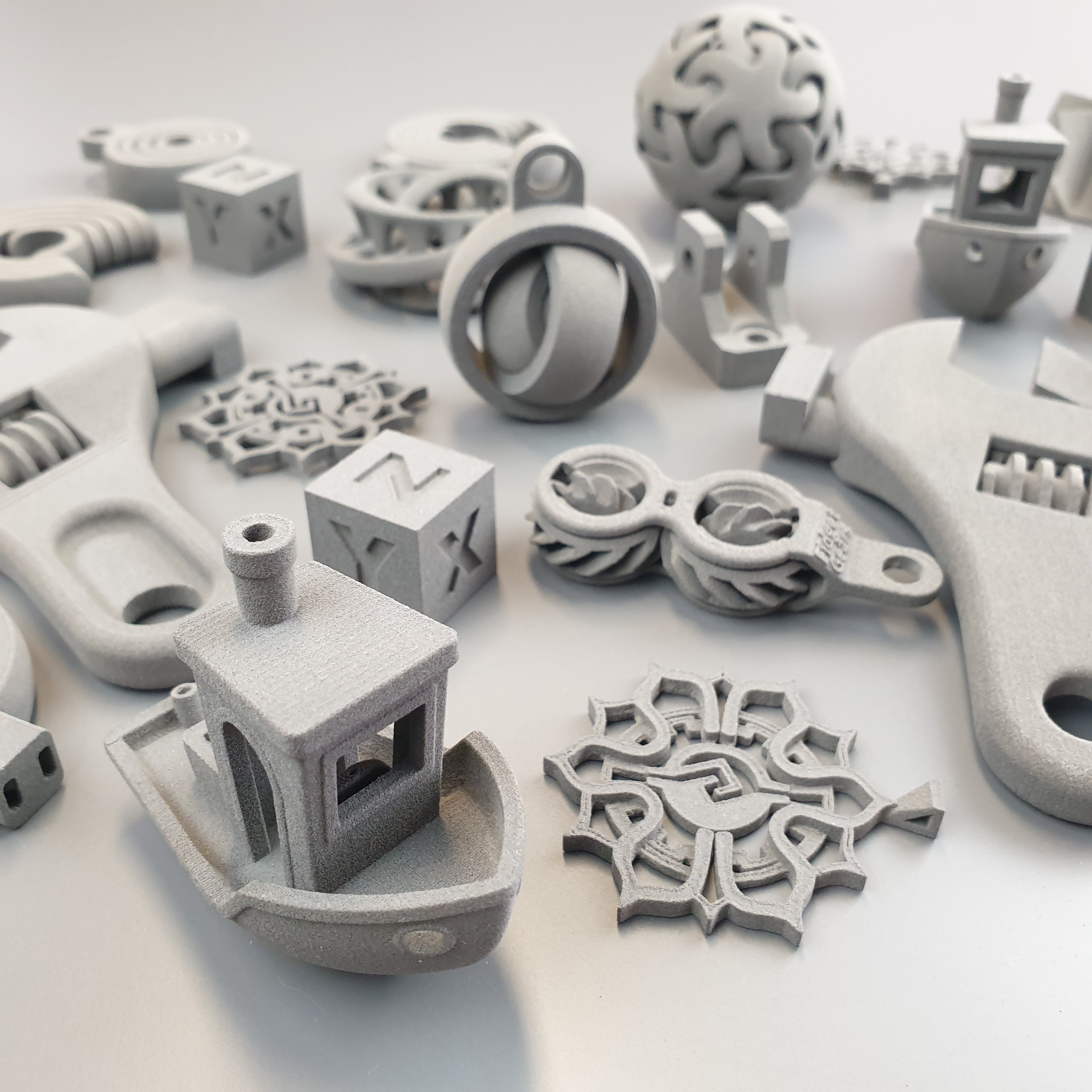
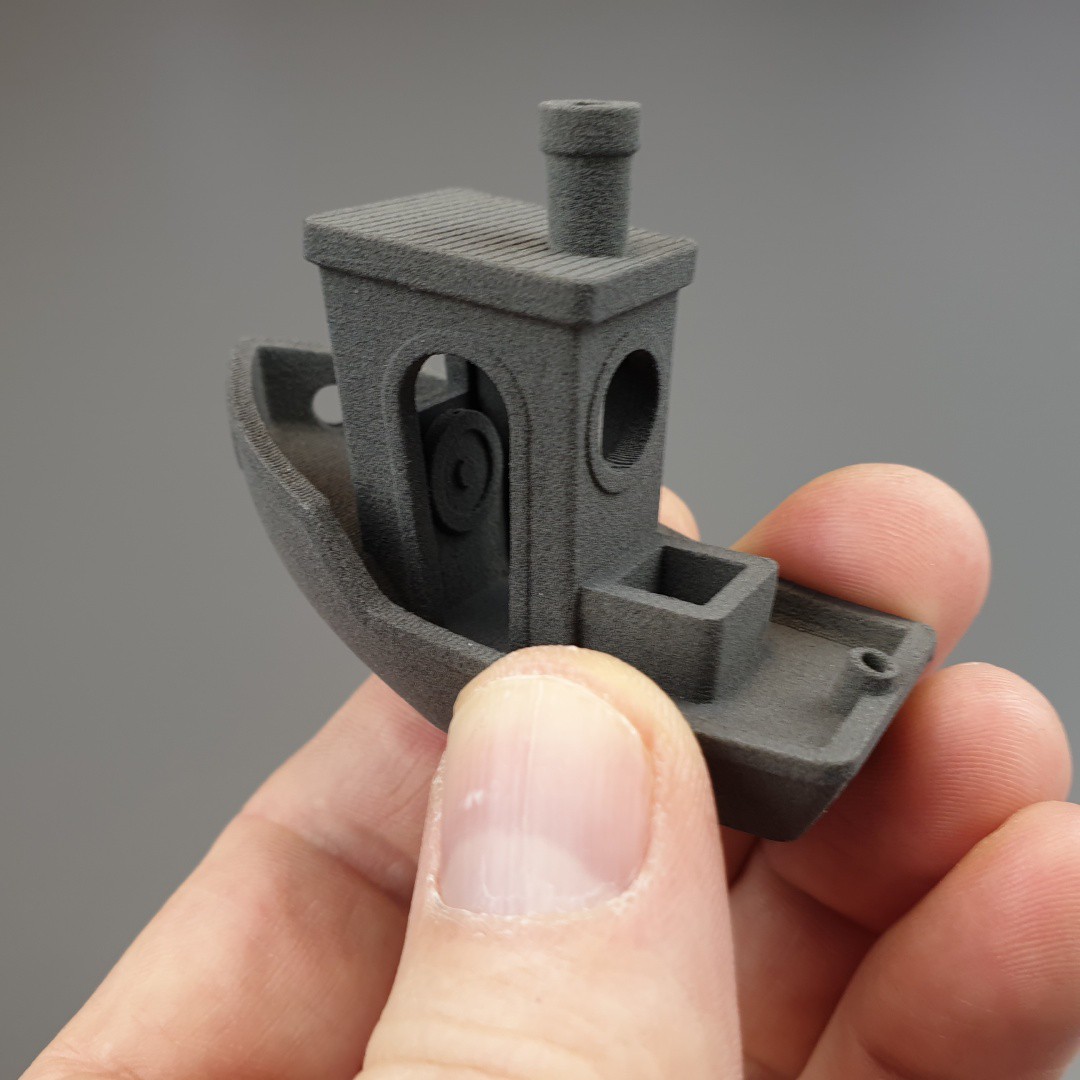
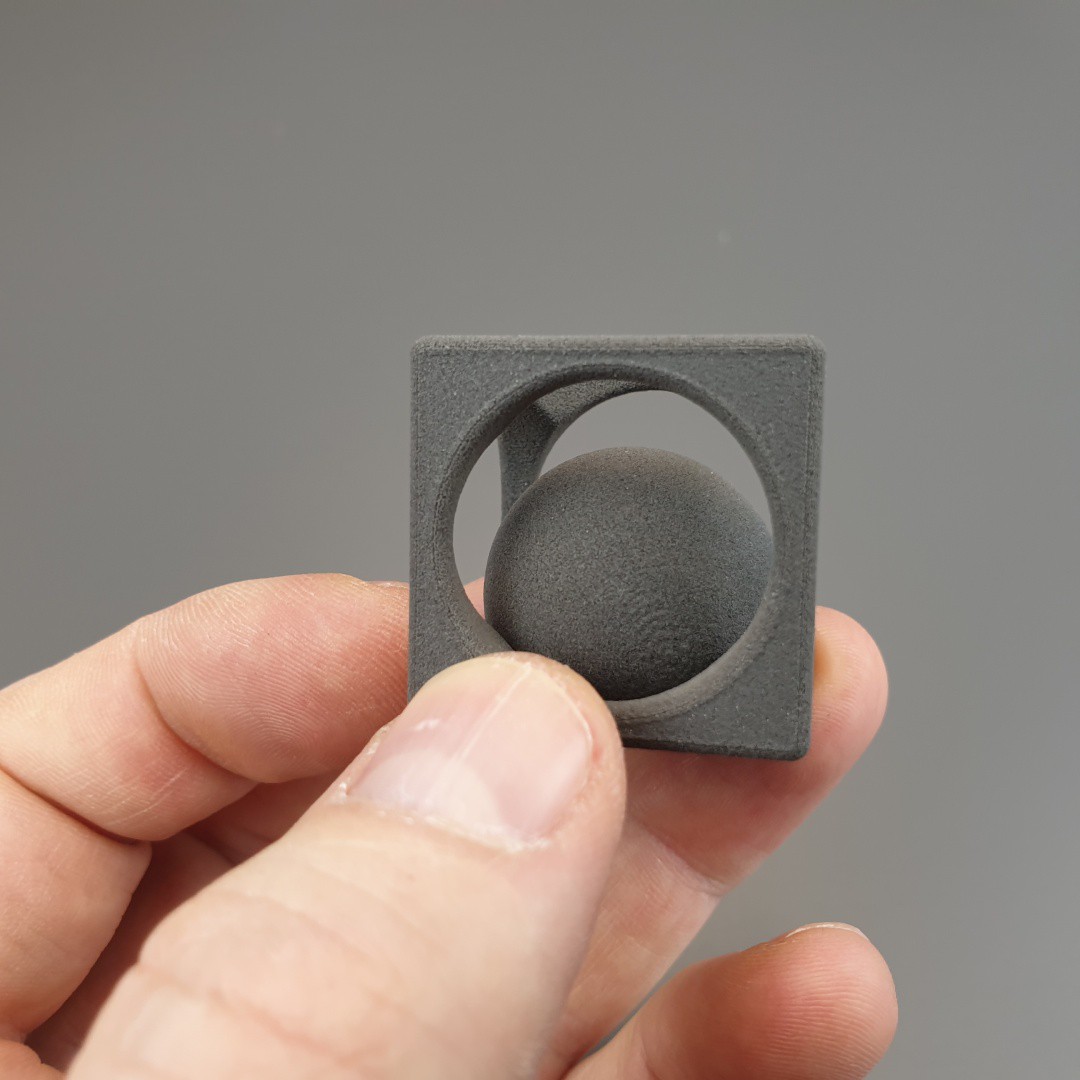
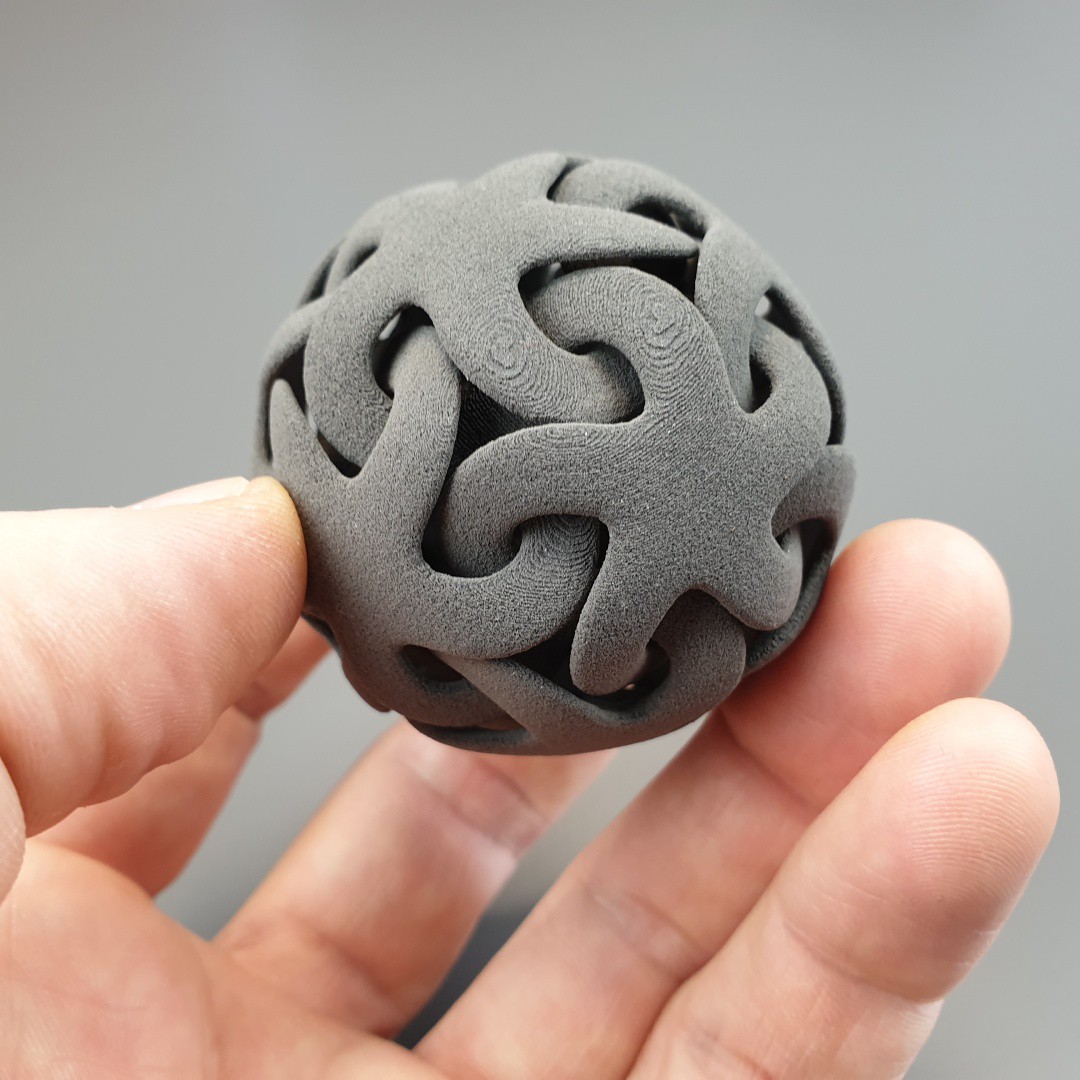
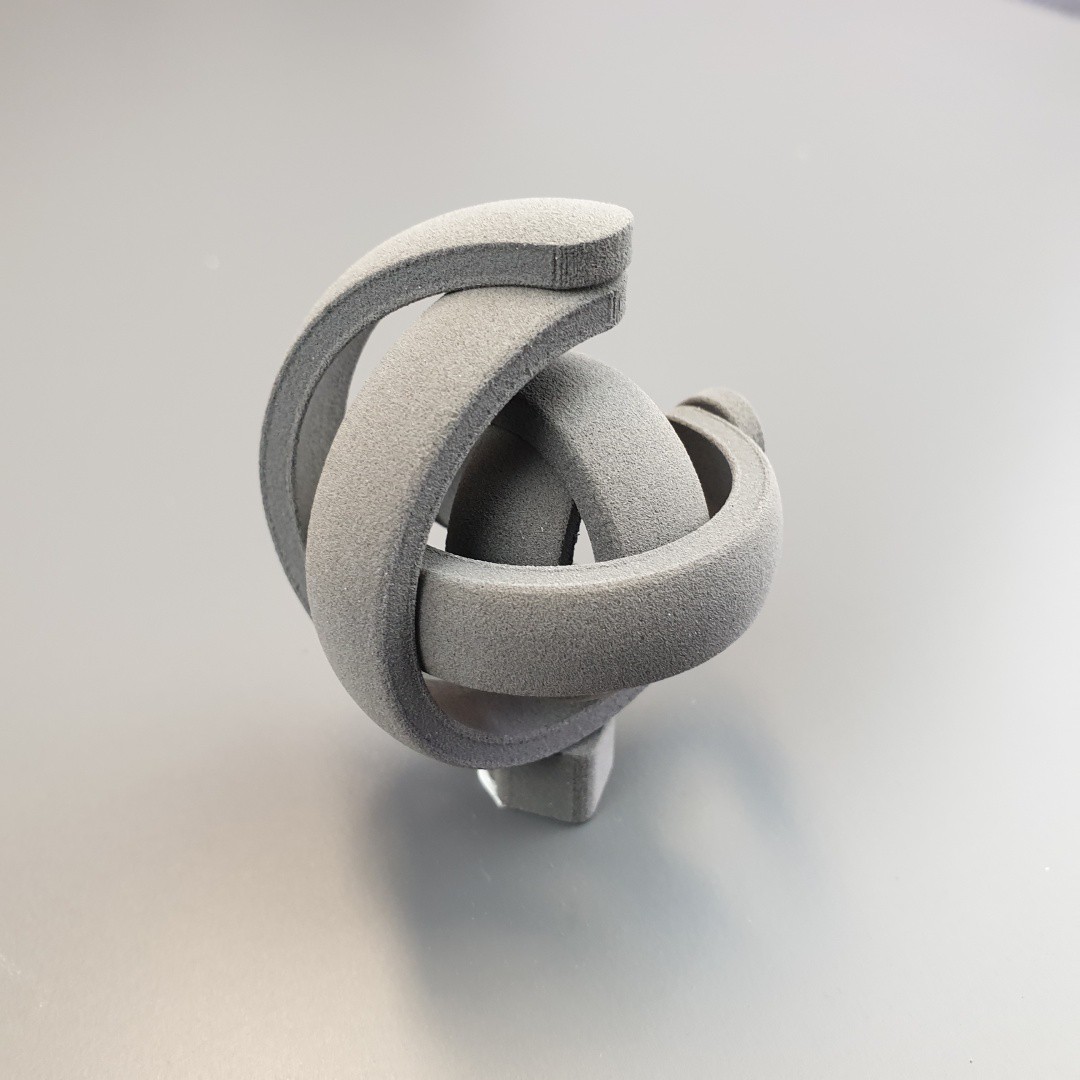
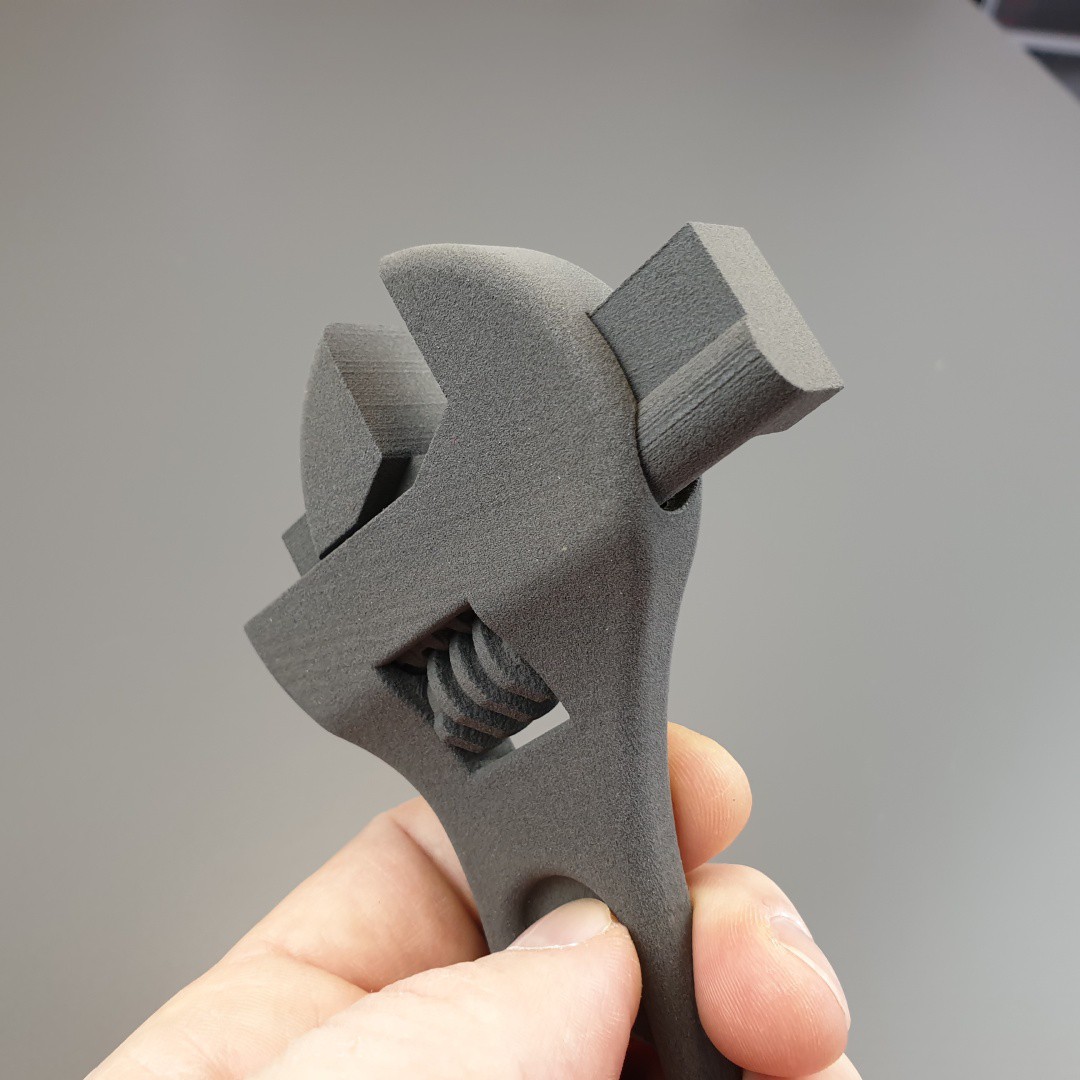
<< 28/11/2023 >>
Testing and tuning of the realease candidate version of my DIY SLS 3D printer is in full swing.
Here is one of really early prints:
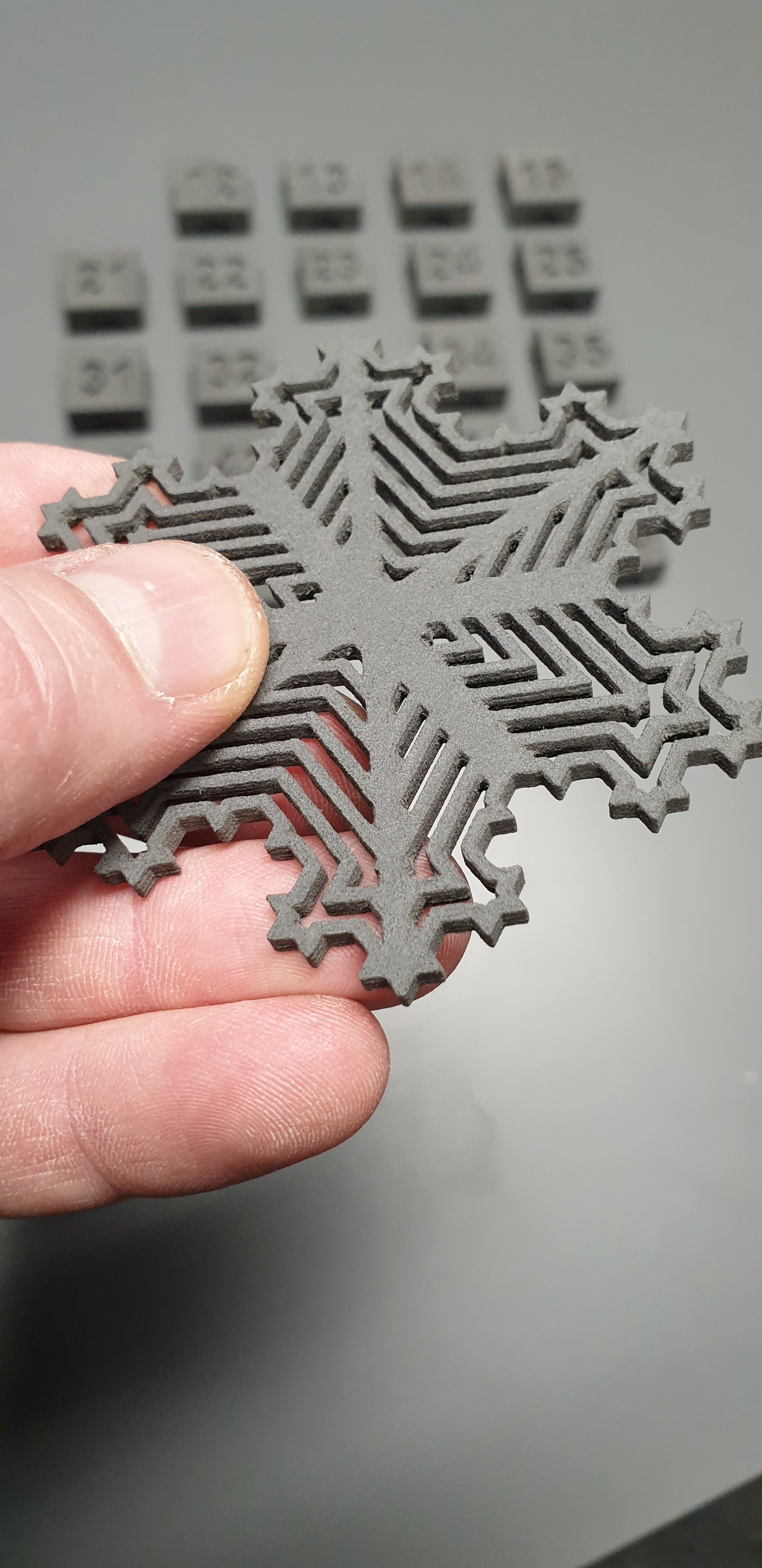
<< 24/07/2023 >>
If you're wondering what are the differences between the first prototype and the second evolution of my printer, this video is for you.
<<Current Build Status Of The Updated Printer Version: 09/03/2023>>
Check out the project homepage or join Discord for more information.
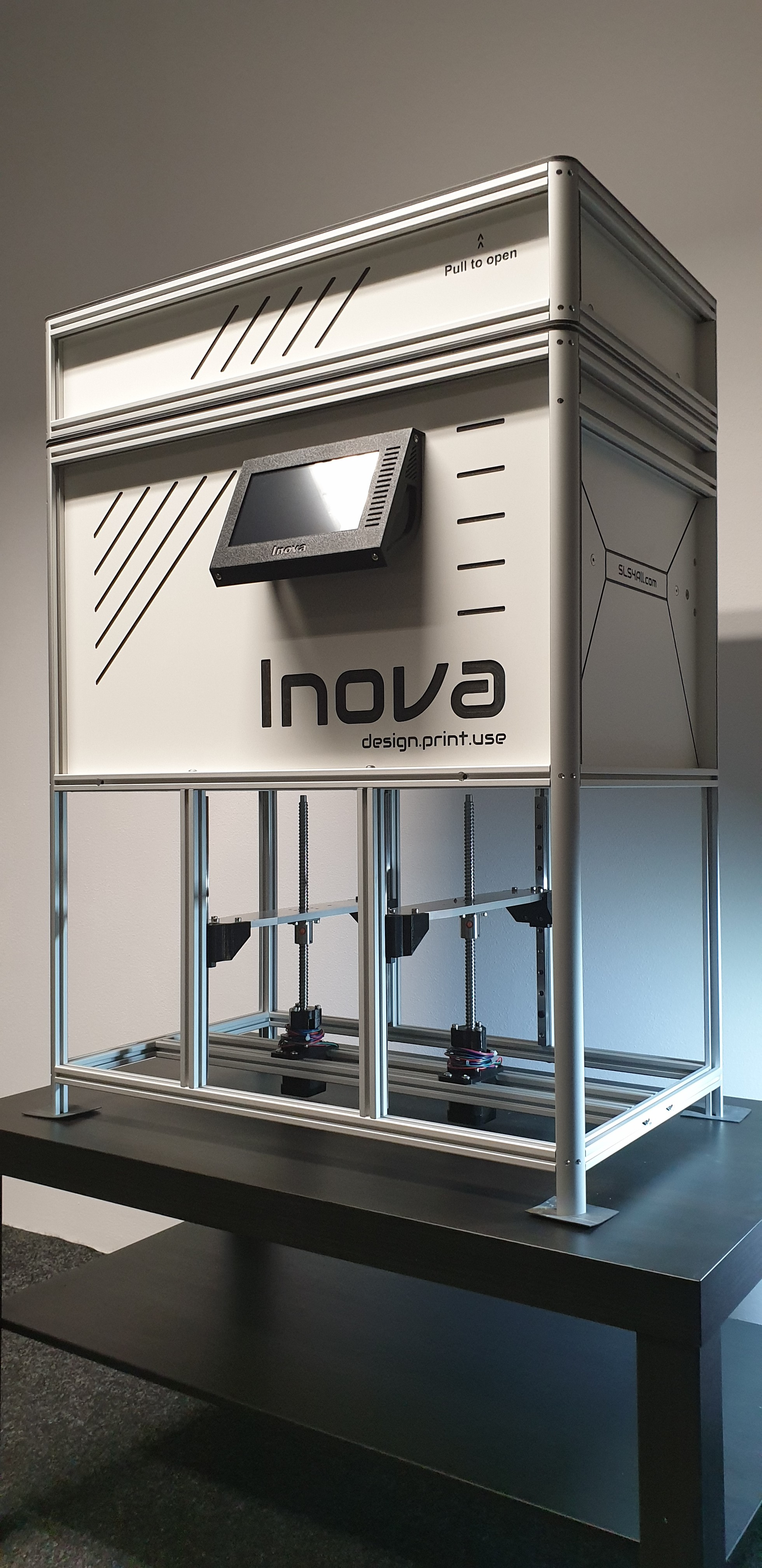
<< First Parts of The Updated Printer Version Are Here: 08/12/2022 >>
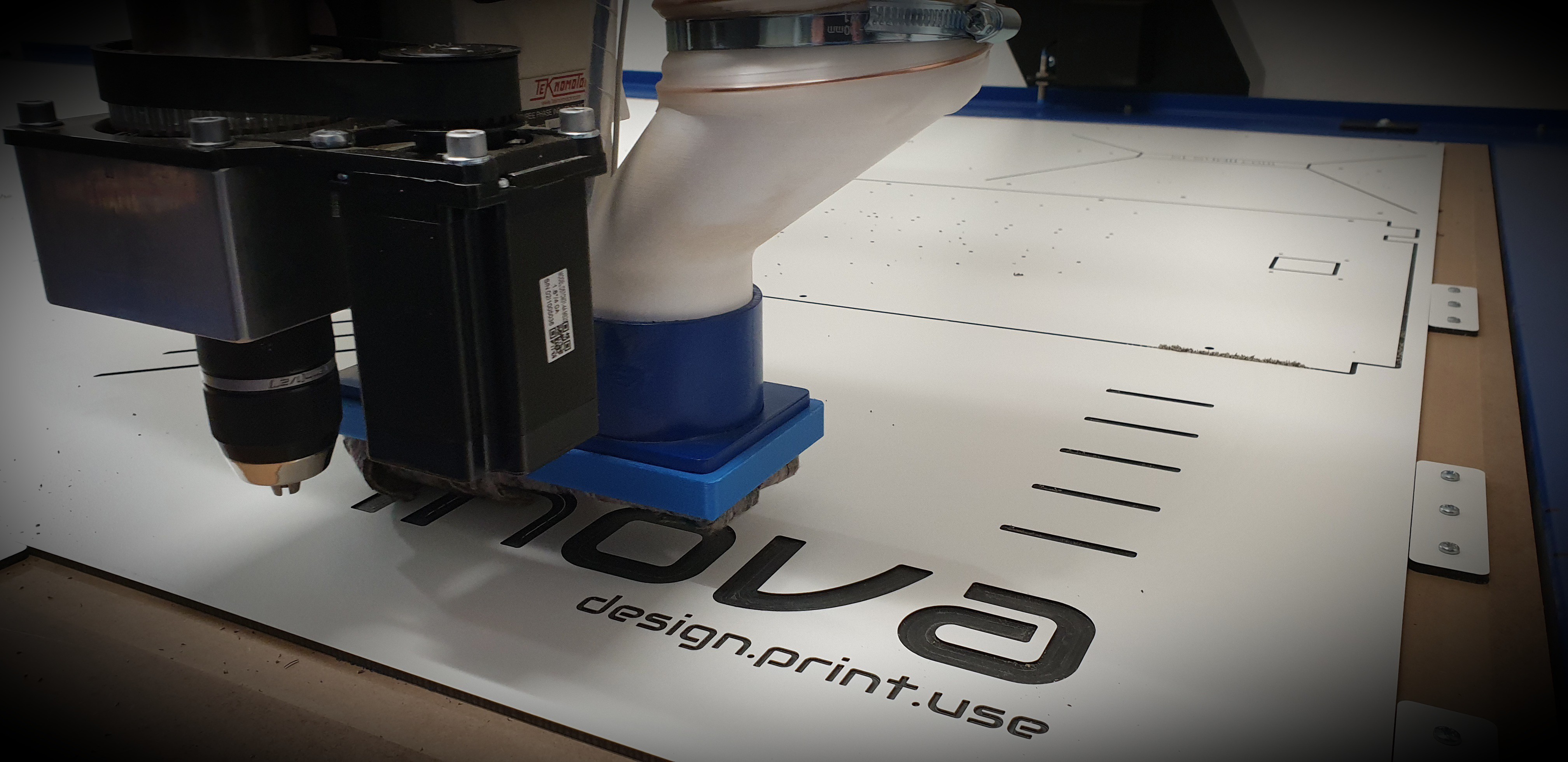
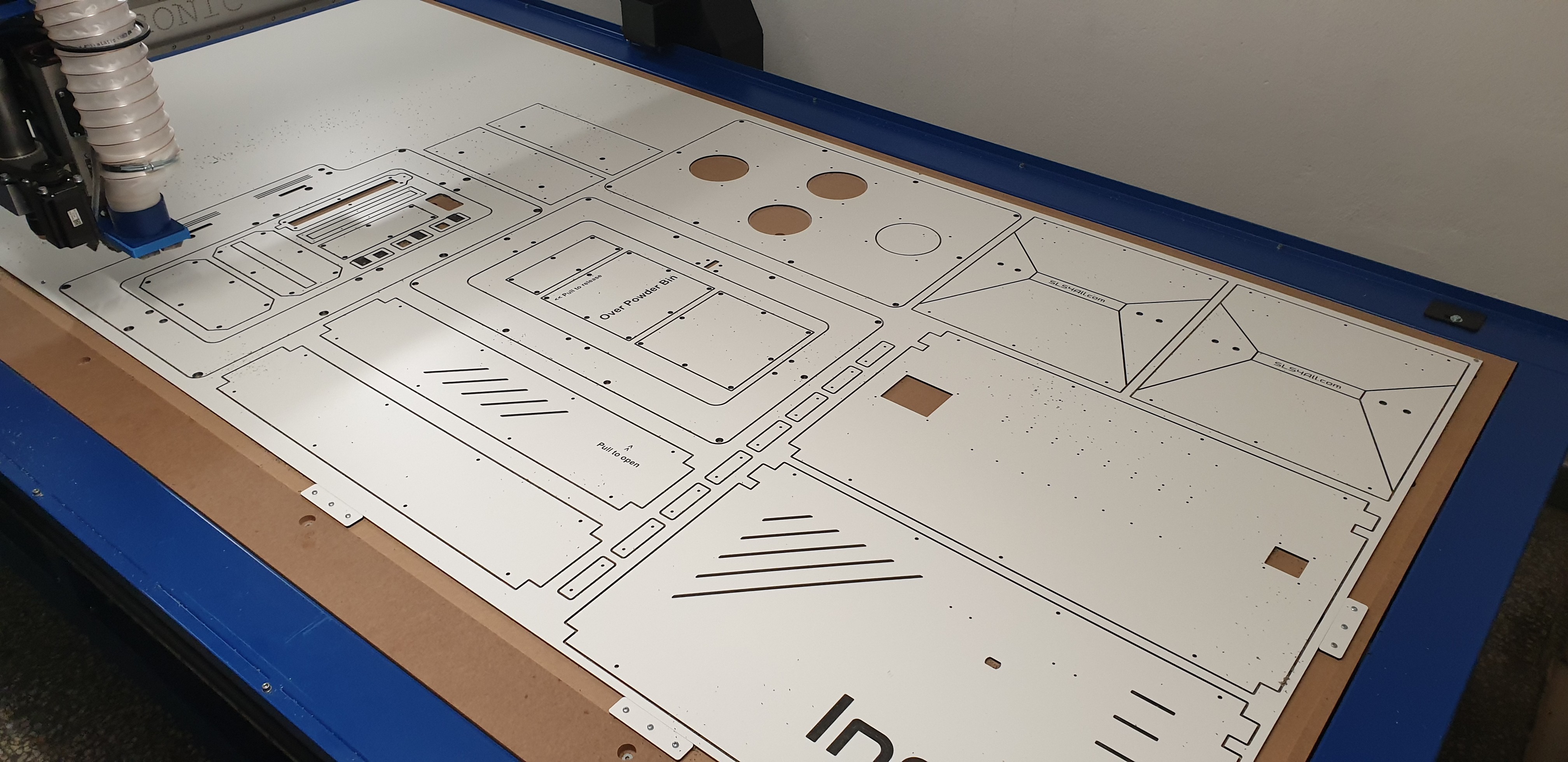
<< Design of Updated Version: 15/09/2022 >>
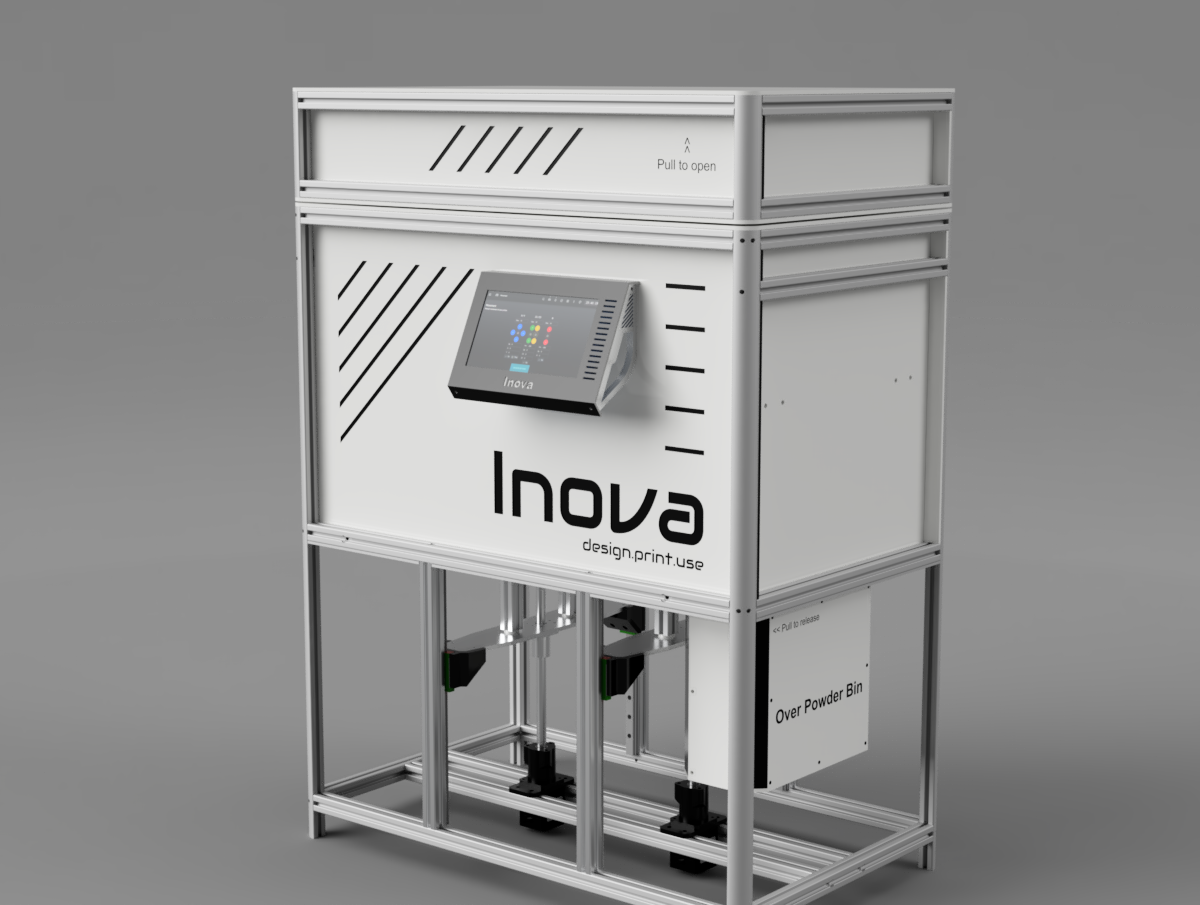
<< Printer Testing: 13/08/2022 >>
<< Recoater after redesign: 05/05/2022 >>
<< Current Status: 04/2022 >>
<< Project Details >>
I decided to use the ordinary arrangement of the SLS printers. It means to have two chambers with the moving beds. One as the powder reservoir (powder chamber) and the second one for the printing outputs (print chamber). The printing material (PA12 powder) will be moved layer by layer from the powder to print chamber using wiping mechanism.
<< Frame >>
Frame construction is made from the so called 2020 extruded aluminum profiles (20x20mm). All the walls are from the 3mm thick aluminum plates.
Even though I designed the frame as two-skin I had some troubles with the heat in early stage. Therefore, Teflon (PTFE) is used at meaningful frame joints and the rock wool insulates the top skin form the inside heat.
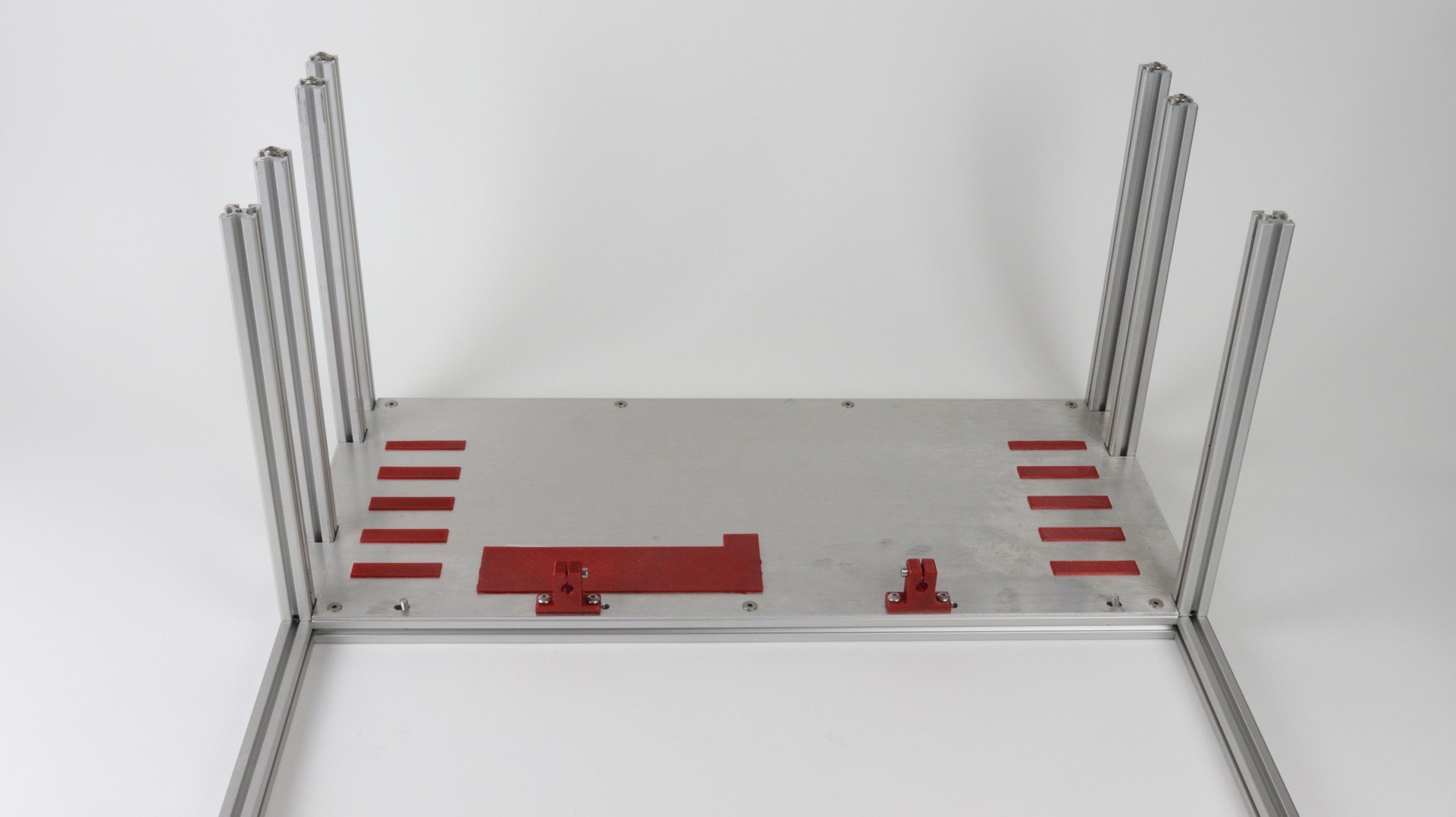
<< Chambers >>
The dimensions of the chambers are 220x175x200 mm for the powder reservoir and 175x175x200 mm for the print chamber. It should allow me to print the range form small to mid-sized parts. I would like to have the effective print volume somewhere around 150x150x180mm.
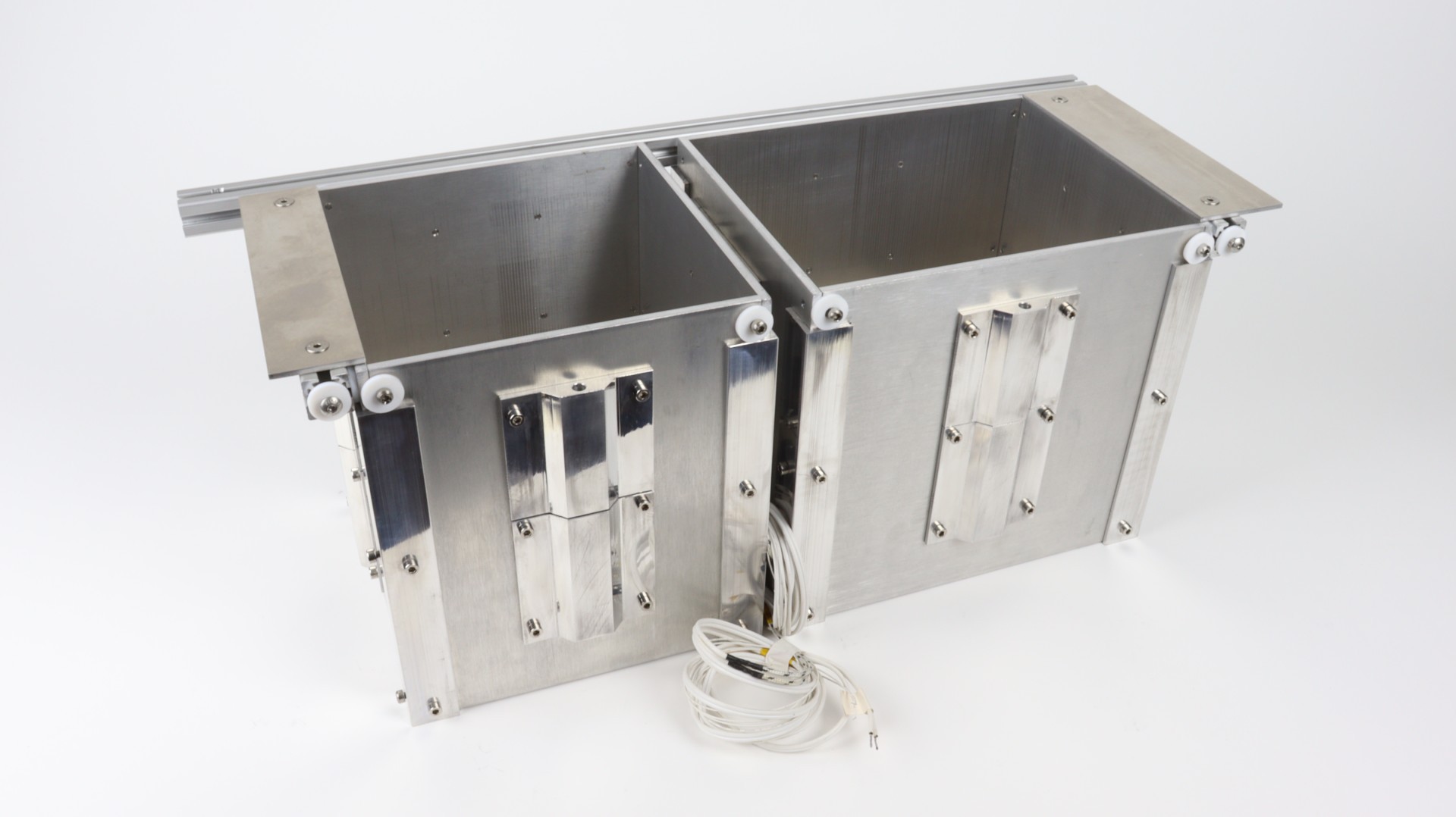
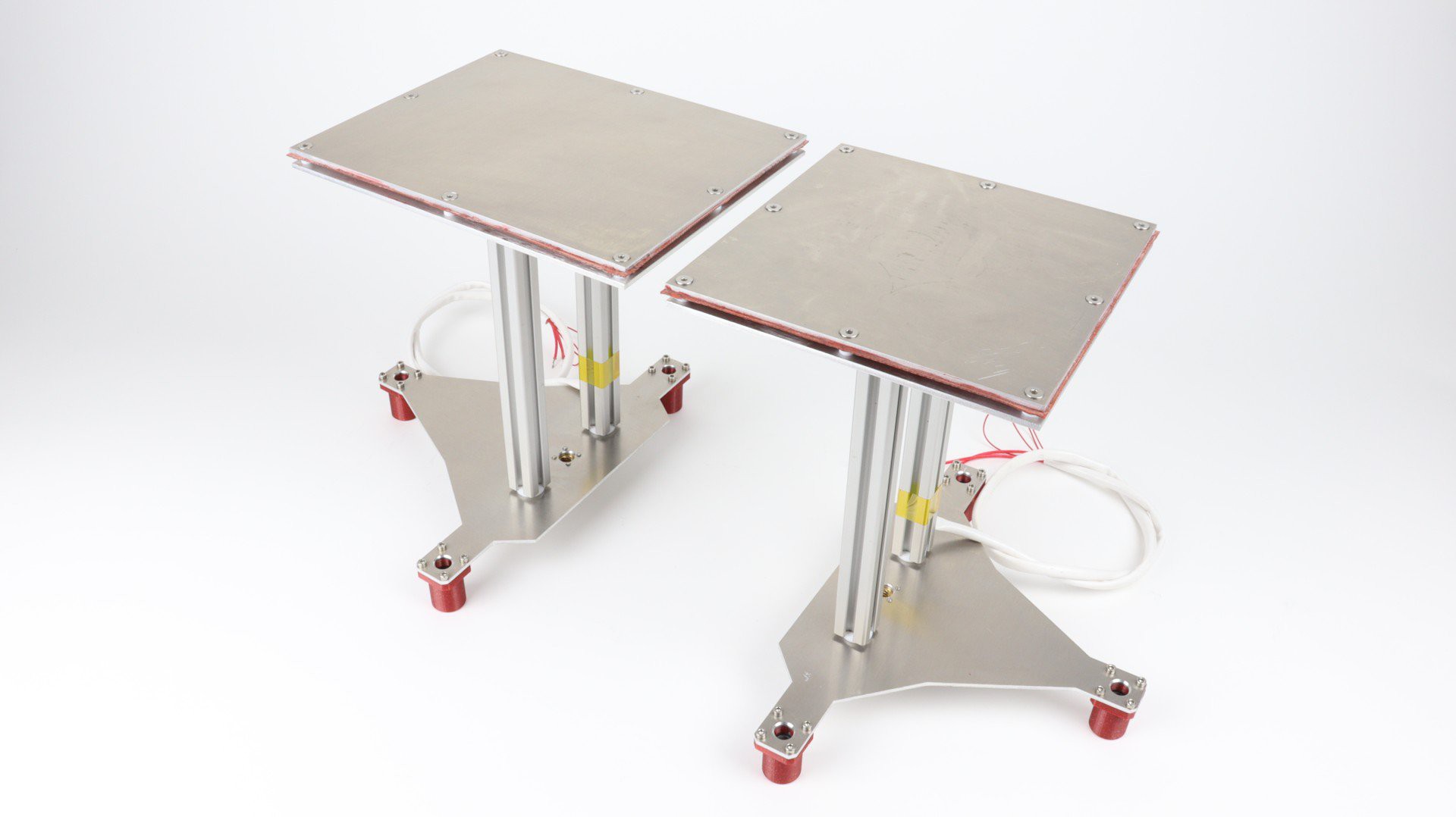
<< Recoater >>
I decided to go in the way of counter rolling mechanism instead of simple piece of aluminum plate. I choose this way because the quality of the layers is one of the parameters directly affecting printing quality.
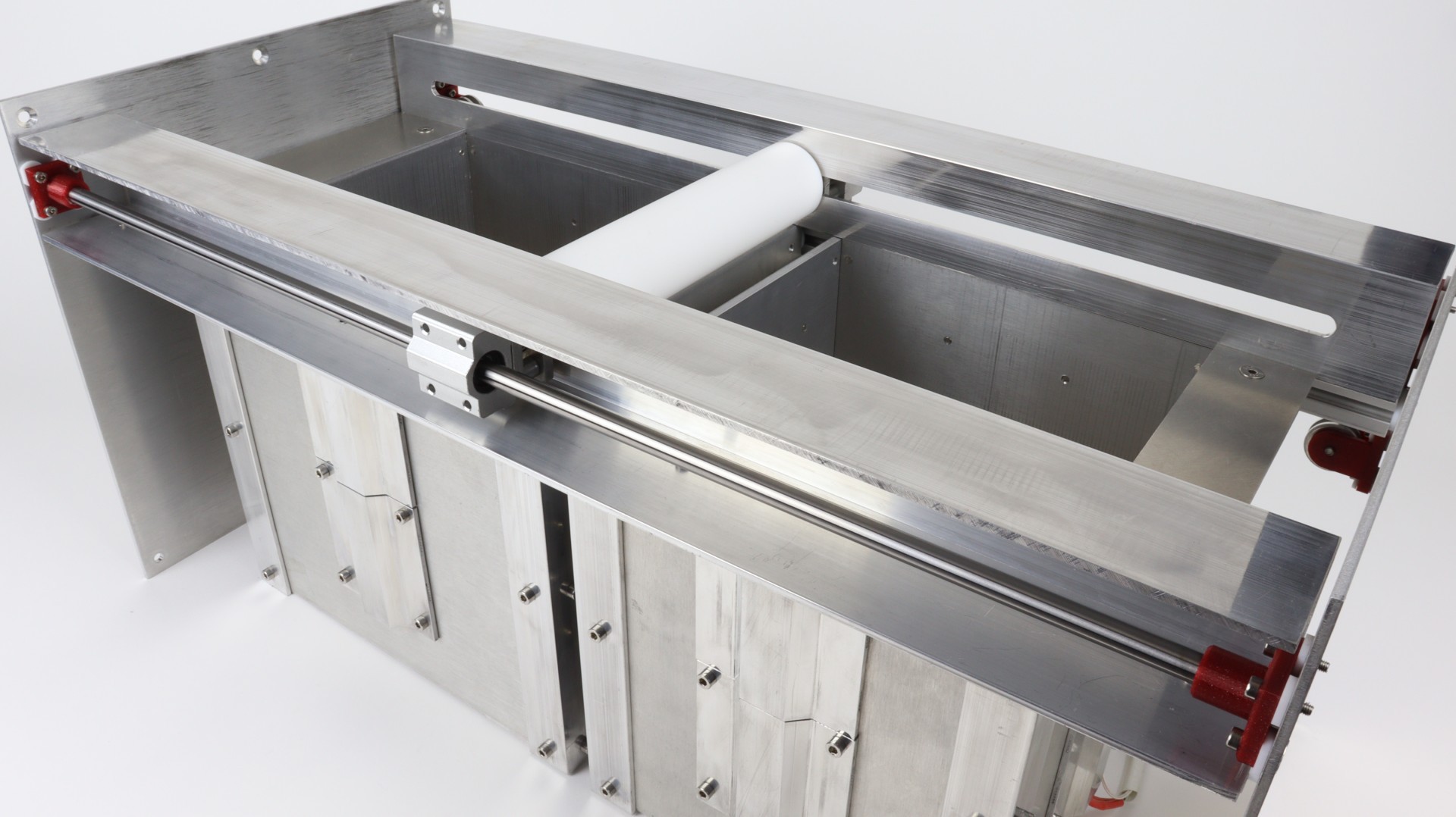
<< Heating >>
I proposed quite comprehensive heating system. It can be seen as an overkill, but hopefully, it will do what it should. I want to achieve maximal temperature uniformity possible across the material in both powder and print chamber. It means I want to have the temperature control on every single side of both chambers, including the beds. Another 4 independent halogen heaters will be used to heat the top layer surface.
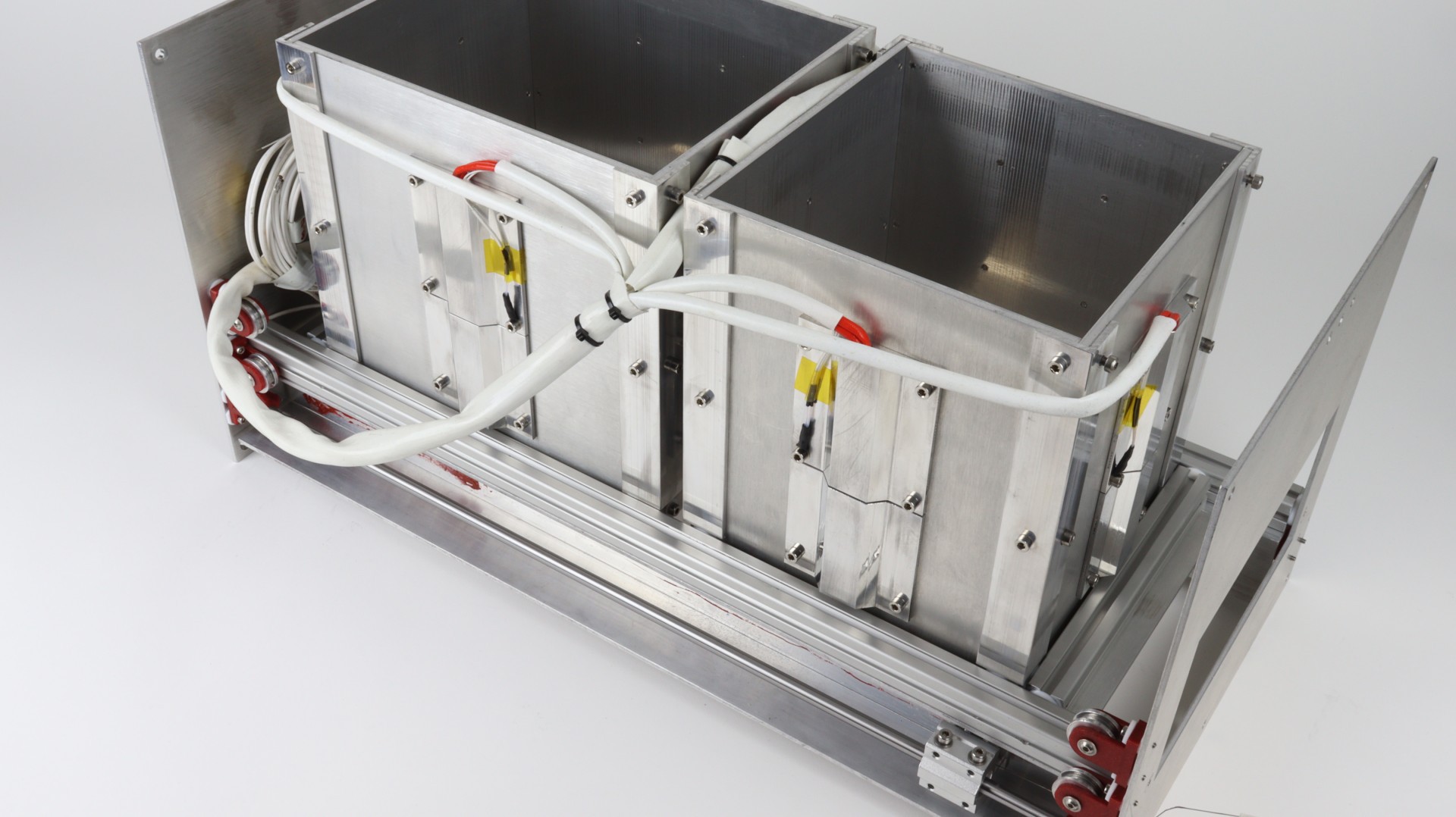
<< X & Y axis >>
I want my printer to be quicker that FDM ones. Therefore, I have to avoid common Cartesian X and Y axis layout. Why? Even if the X and Y moves would be at the same decent speeds as the FDM printers do, total print speed will be much slower because of layer preparation time overhead. Therefore, I decided to go in a way of galvanometers (galvos).
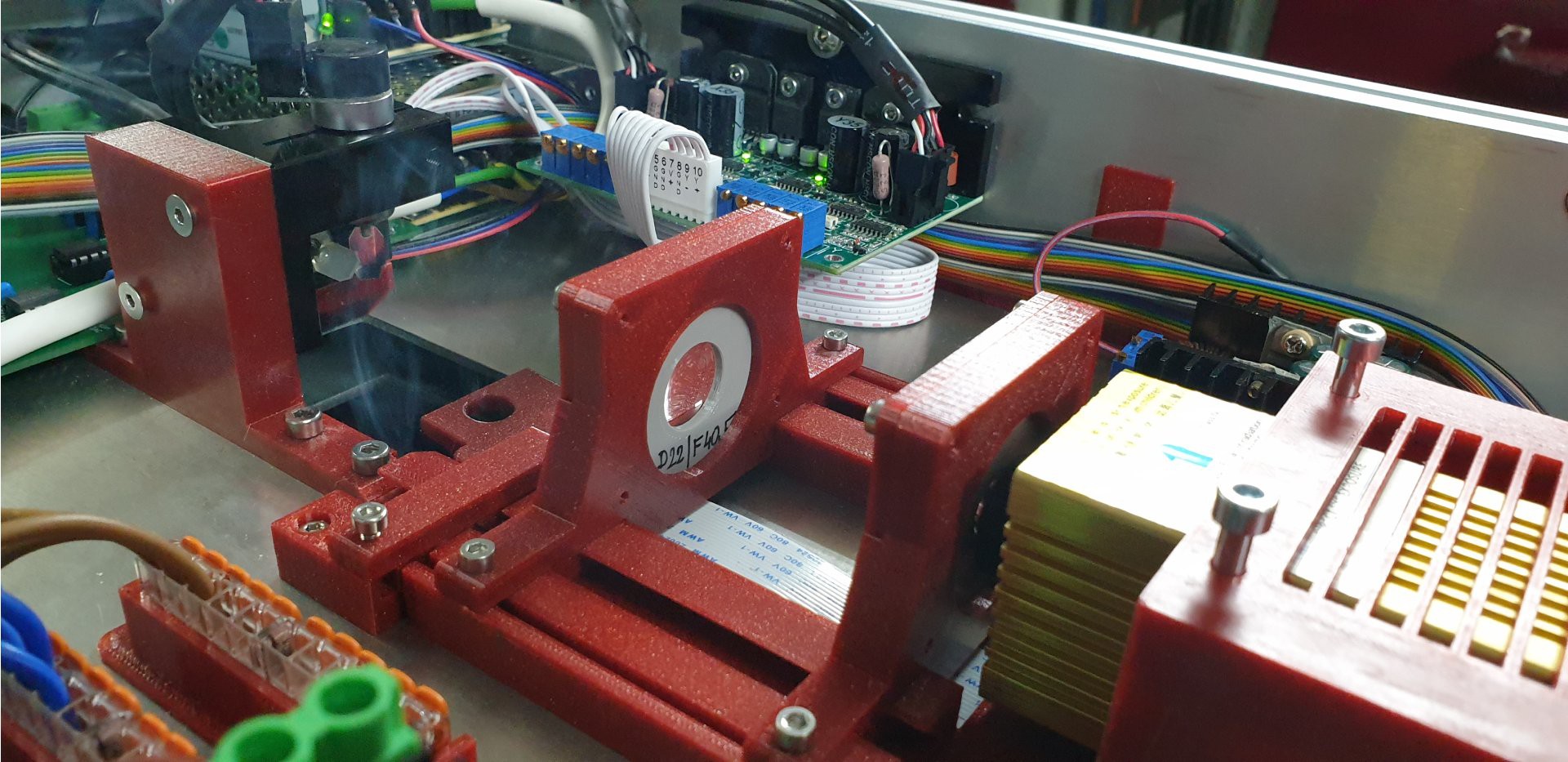
<< Laser source >>
Laser source will be the 5W blue laser diode (wavelength of 445 nm). It is the most cost-effective solution but as with anything, you...
Read more »
have a look at high speed sintering, a dark part profile on white powder is sintered by passing a halogen heater across the surface, leaving the white powder unsintered.
means having a printhead instead of a laser.