I have refined my idea in the last log about the string/yarn that will clean the roller.
This is the string I intend to use:
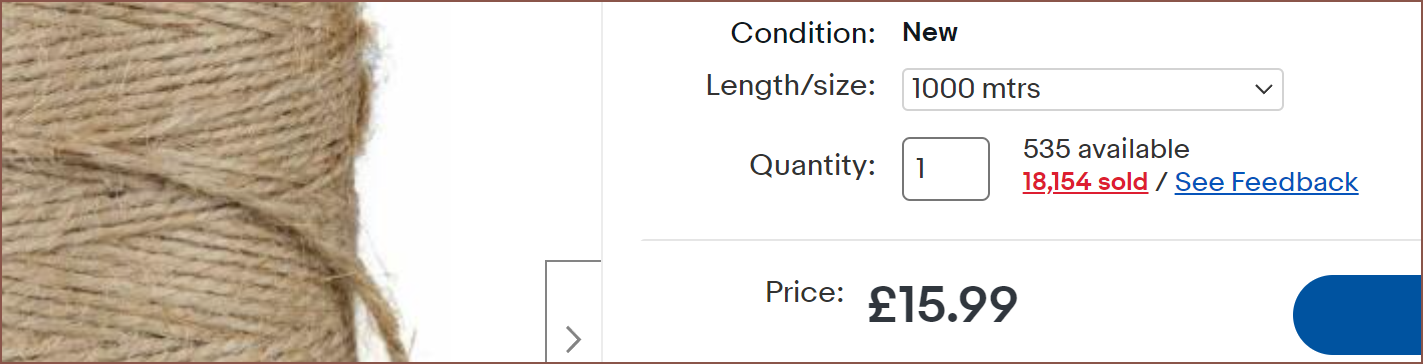
It's cheap and looks like it could really grab and hold onto the uncured resin from the roller. Instead of 2 strings on each side, a single string will be located at the top of the roller. This both means that resin can be cured to both sides of the exposed string, leading to less string used and less complexity, but the roller can be cleaned as it rolls over the print area. This reduces the limitations to extending the Y axis solely to the screen and UV lamp used, as well as reducing the time it takes to clean the roller for any additionall passes needed.
A smaller roller diameter can be used, claiming back valuable Z height. With the extra space around the roller now, I can probably add a second row of LEDs. The next aluminium angle size up is 15x15mm and the strips are 8mm each, so hopefully the 1mm overlap isn't a problem. More LEDs will allow a faster pass with the same final cure hardness or a higher cure hardness for the same default speed. Alternatively, a second roller could be added for a deeper clean on every pass.
I also wonder if the continuous fibre could be used. The roller is cleaned and the fibre is coated with UV resin for use with the fibre attachement.
Discussions
Become a Hackaday.io Member
Create an account to leave a comment. Already have an account? Log In.