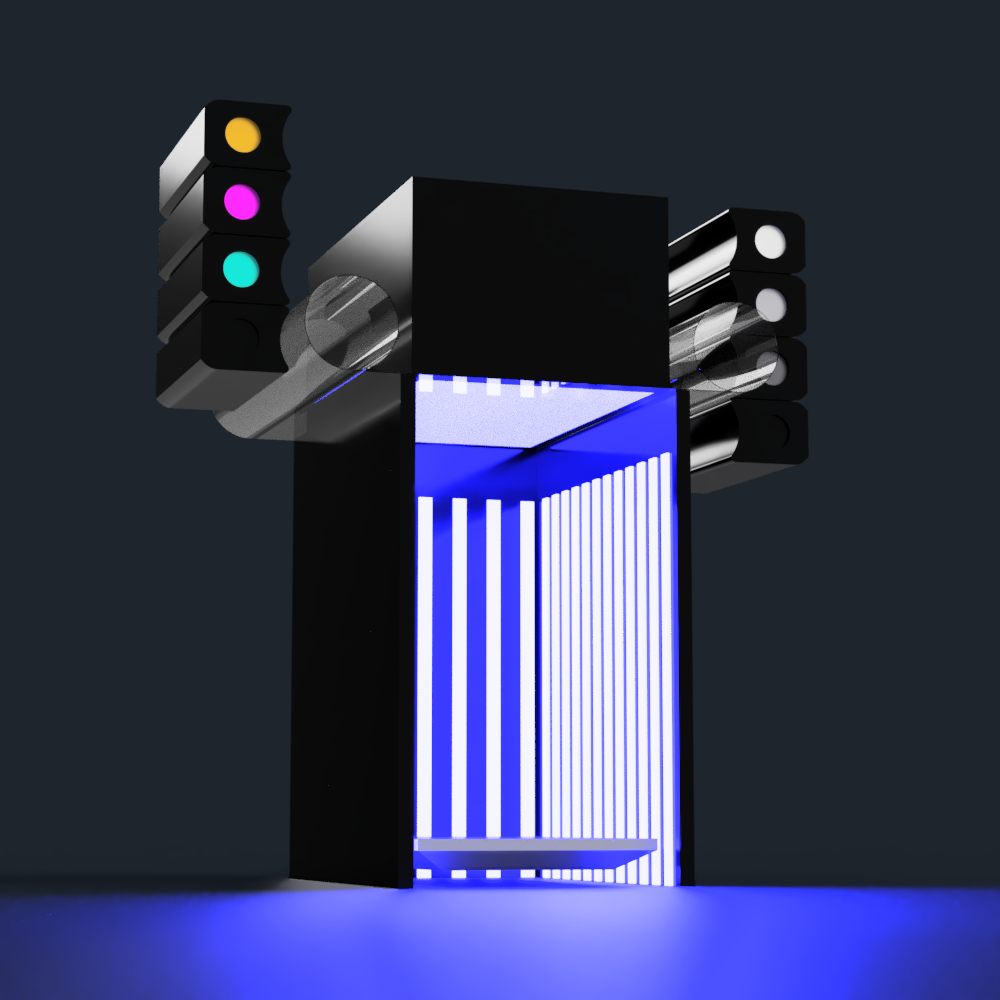
I've just made a minimum viable 3D model to better explain my previous project log.
- I intend for the printer to also have a built in wash and cure station.
- Ideally, I'd like to be able to cure from the top without the use of the LCD panel to increase longevity.
- With the screen oriented this way, I can install more LEDs on the walls
- This also means that the film's unsupported span is shorter than if it were oriented the same way as the vast majority of MSLA printers.
- The same LED pattern will be on the front window, but more sparse to increase visibility
- A drawback is that the hardware responsible for resin application will have to be longer
- The same LED pattern will be on the front window, but more sparse to increase visibility
- The whole print area will be as "watertight" as needed so that the part can be washed
- Ideally, the print will be washed as it prints.
- this might need some kind of sensor to know if any liquids may have splashed onto the resin-covered screen
- the print likely has to be washed when the material is switched
- Ideally, the print will be washed as it prints.
- The resin is held inside modules which also have the hardware that applies and retrieves resin from the rollers
- The modules are on a gantry that will move away from the roller and then move up or down to switch to a new one before pressing against the roller again.
- An RGB LED is an idea for the coloured dot; the benefit is that it can be dynamically changed easily. However, it would need a power source when the module is stored away. Maybe a 3V coin cell is enough for this. Alternatively, there could be a window/cutout so that the inserted bottle of resin is visible.
- For the render, I've installed CMYK on the left and White, Transparent, Support, Black on the right
- The washing fluid will be at the base of the printer, under the max Z location.
- A current design concern is that the washing system and/or the curing LEDs might not be able to get to every part of the print.
- A circular bed instead of a rectangular one could fix this.
- It might be beneficial to see how dishwashers clean their contents.
Also, I'm computing a mental simulation and I come to the conclusion VLM technology removes the need to have drainage holes (assuming that the layer height is thin enough for the screen to fully cure the resin), further getting towards the convenience of FDM. It might be required to first print the layer, wash the layer and then cure the inside offset of the layer so that any trace amounts of resin that would be in the part will be cured.
Other than the resin applicators, this solution doesn't seem that much more complex than a toner printer + dishwasher. Additionally, I haven't done extensive research but I'd like to believe that a hobbyist (chemist) would have a much easier time creating the resin blend (especially since viscosity is less of a constraint) and just being able to use it in the printer, rather than creating polymer pellets and then presicely extruding it through a filament extruder for use in an FDM printer, opening up the possiblility of a maker both designing a custom part and custom material to make it out of.
Discussions
Become a Hackaday.io Member
Create an account to leave a comment. Already have an account? Log In.