[17 Jan] Right now, the tool steel bed costs around £60 and the honeycomb mesh would probably cost another £60 if I could find one in the size I need. I did some research on r/lasercutting and the reasons for the honeycomb is so that the air stream has somewhere to go and the laser beam doesn't reflect back onto the cut material, allegedly. I also looked at the typical beds for top-down SLA's and it does seem that resin prints can tolerate quite large holes.
I'm thinking that a sensor will be needed to detect if the bed was able to move down to the max; this would indicate if it was able to push the boltheads through the holes in the bed or if a part or fixture stopped it. It could be as simple as a second endstop or as detailed as a load cell force sensor.
Anyway, I found this video that shows that charring of the bottom side of the laser cut workpiece can be eliminated if the sheet is elevated. A commentor suggested ball bearings as a possible object too.
Due to having tofirst layer cleaning, moving bed mass, auto ejecting and preventing laser reflections, it really seems that a bed surface with a large air:material ratio is the ideal bed choice for my application. Additionally, I was wondering how I was going to mount traditional PCBs for any PnP operations, and the holes would allow for a straightforward solution.
Ideally, the hole spacing would be equal to the mounting holes of the MGN9 rail, allowing me to actually mount the rail directly to the bed underside. M3 bolts seem common enough, and their bolt heads can usually pass though a 6mm hole, so this measurement will be the minimum size. I feel like >=8mm would be ideal, allowing for some of the bolts to be misaligned.
Here are M8 threaded holes spaced 20mm apart in an 8mm plate. There are M3 bolts on the very bottom of the Z axis travel such that when the bed goes all the way down, the bolts stick up through the bed and push off whatever is ontop. I can already see that there's still loads of surface area, so a more extreme 10mm spacing could be used:

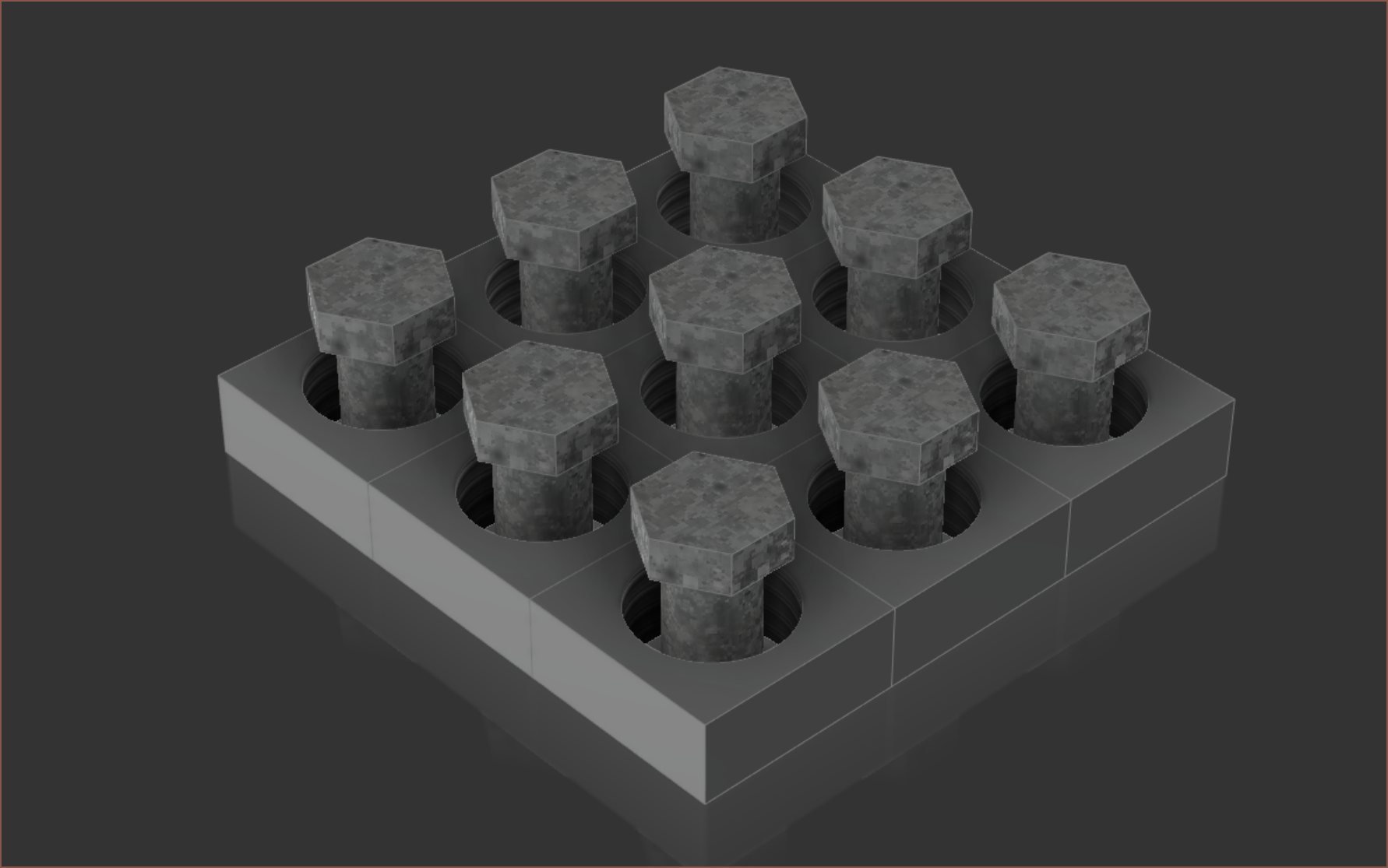

Anyway, that number could be even higher if I can't find some industrial printer somewhere that actually can get away with holes so large. I found this model which uses 5mm holes, so an 8mm hole is probably in the realm of possibility.
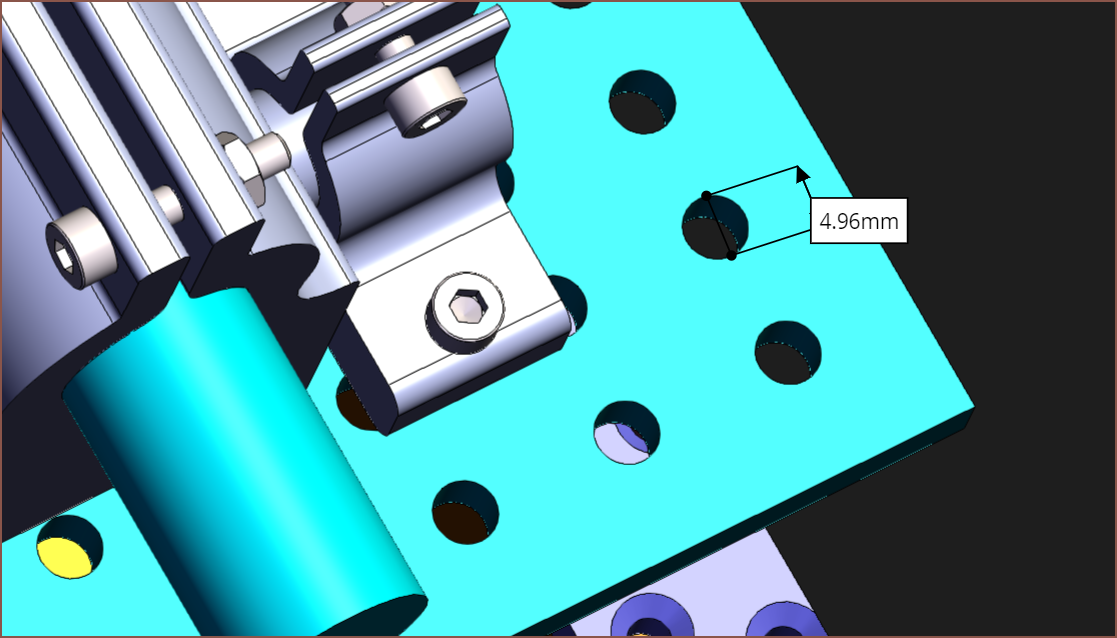
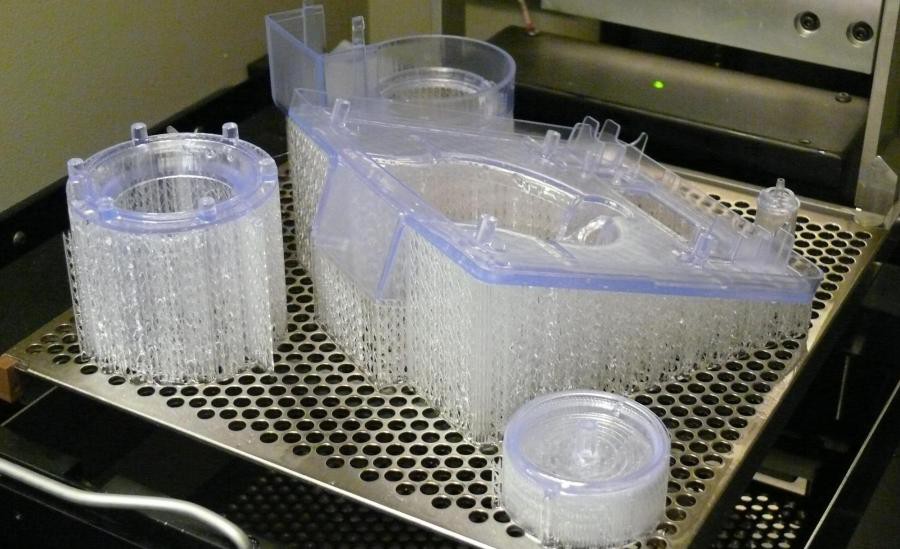
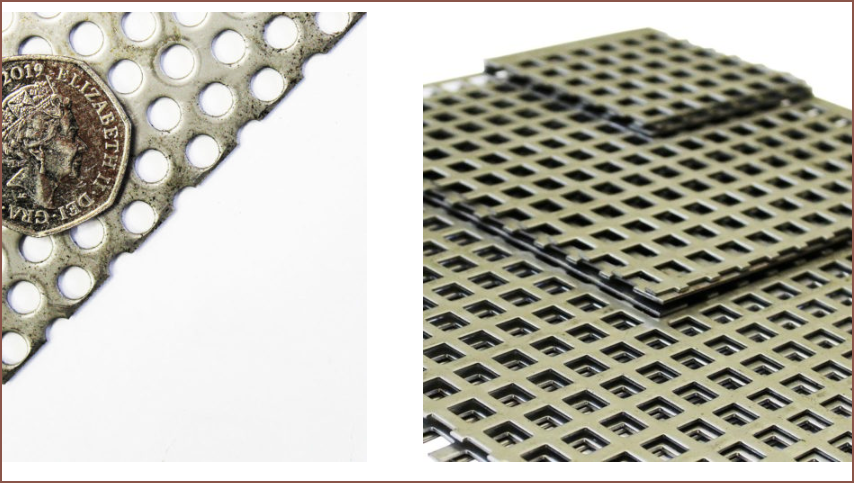
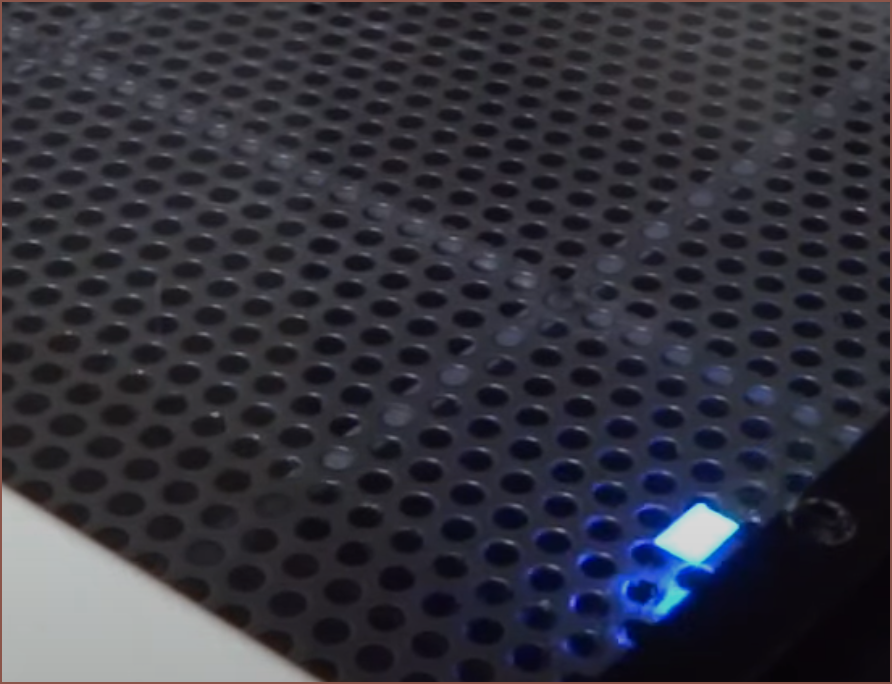
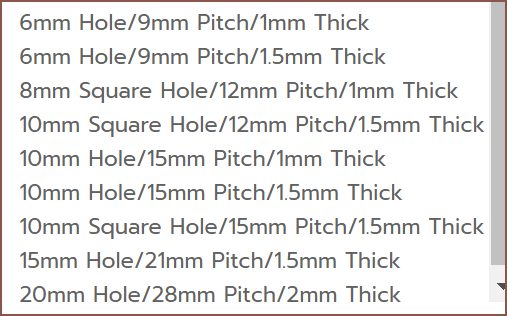
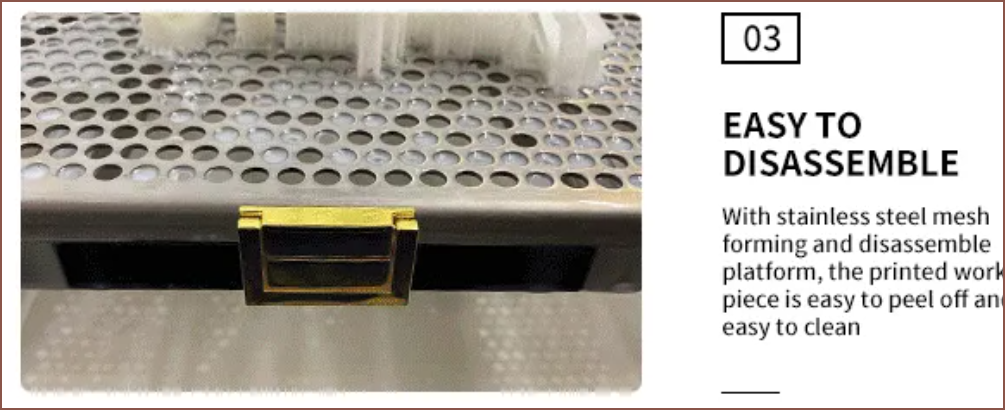
I can't seem to find anything against using this as a bed material for laser cutting. Only issue I can see so far is that it's only 2mm thick max (and the ones I like are 1.5mm). How am I supposed to thread that? The good news though is that stainless steel should be 3x as stiff as aluminium, so theoretically a 2mm perforated sheet should be as stiff as 6mm of aluminium, right?
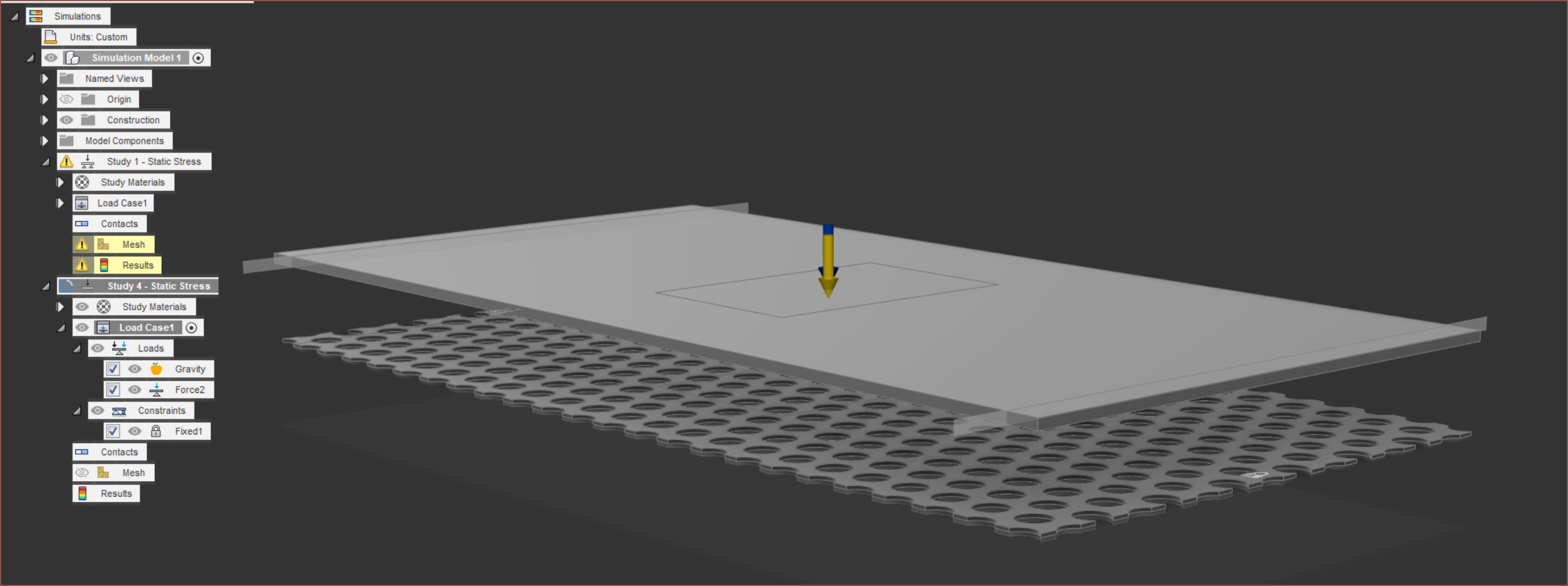
I have no idea if this is going to work, but it turns out that "simplify" applies to all studies so I can't just remove the unsimulated bed.
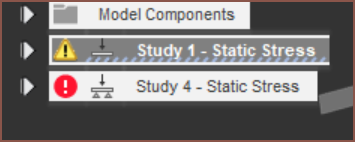
nope. Ok let's try "suppressing features" on the remove instances in the simplify
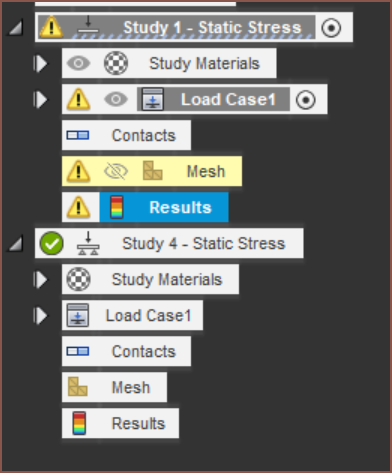
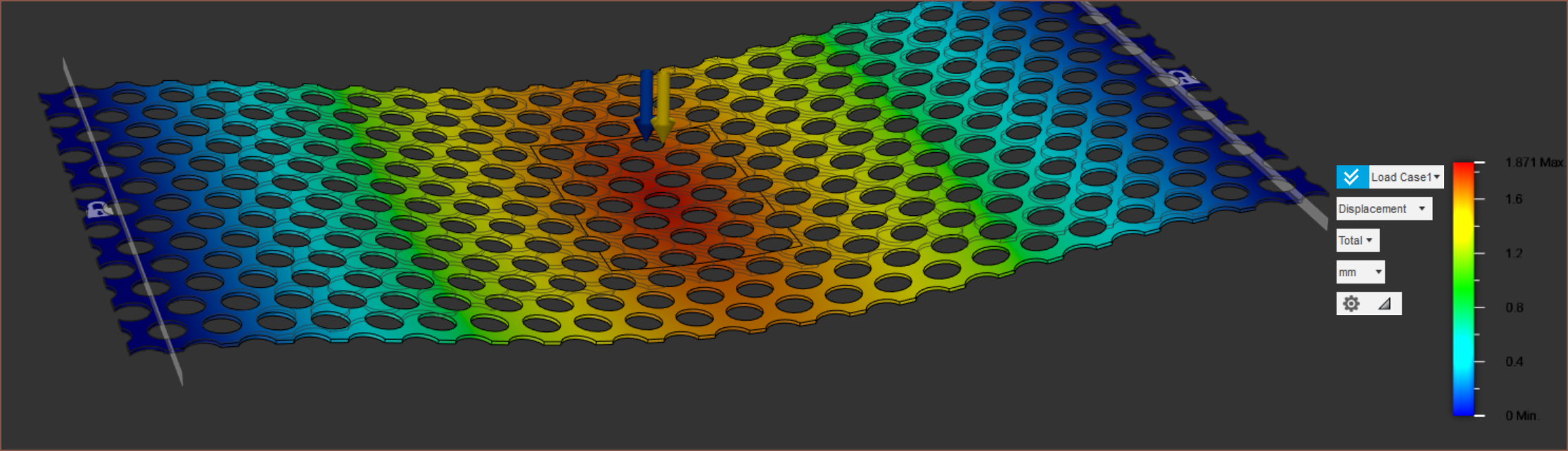
Perhaps the simulation only works if I send 1 to the cloud at a time.
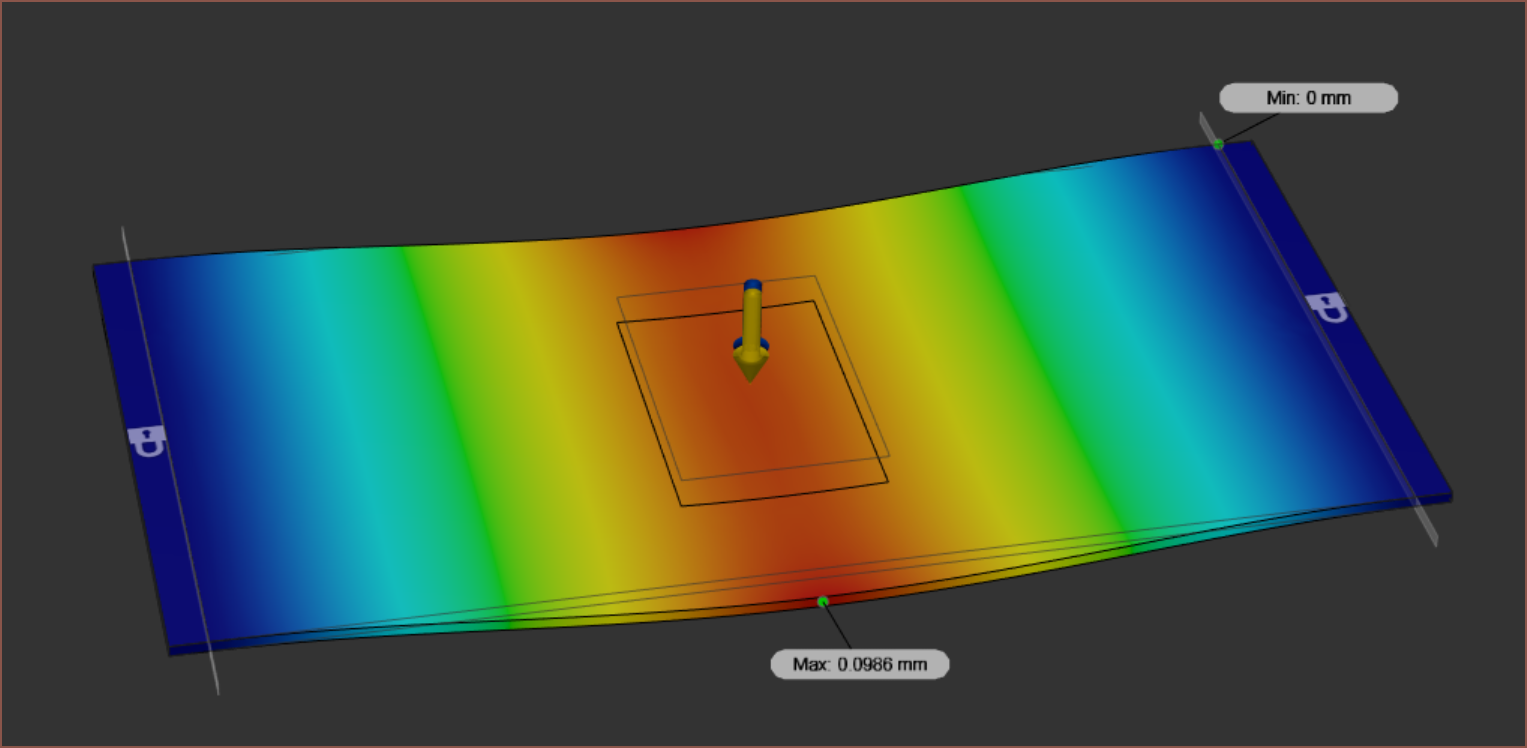
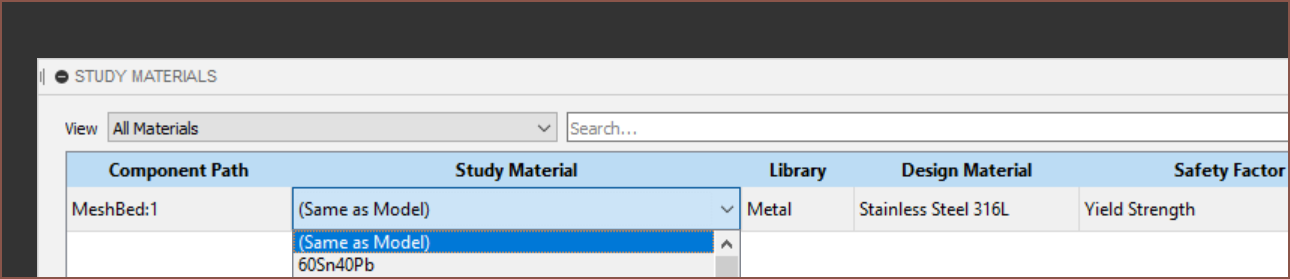
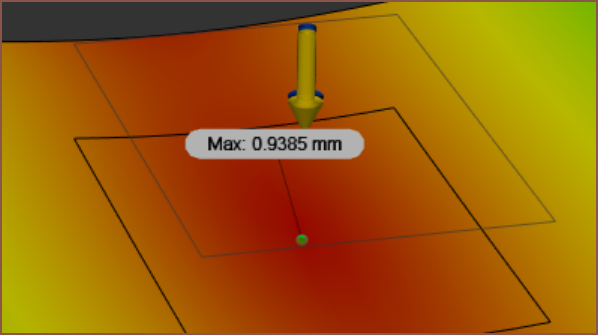
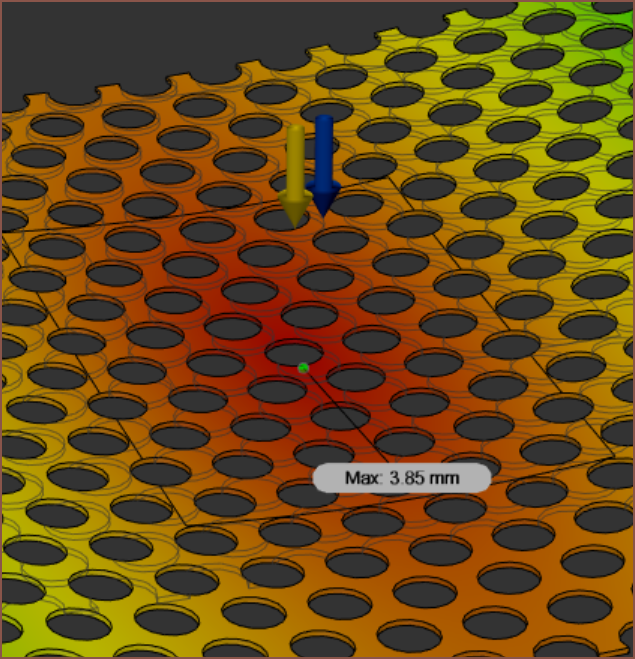
Youch if I thought the 2mm one was problematic, the 1.5mm thick sheet is a no go zone.
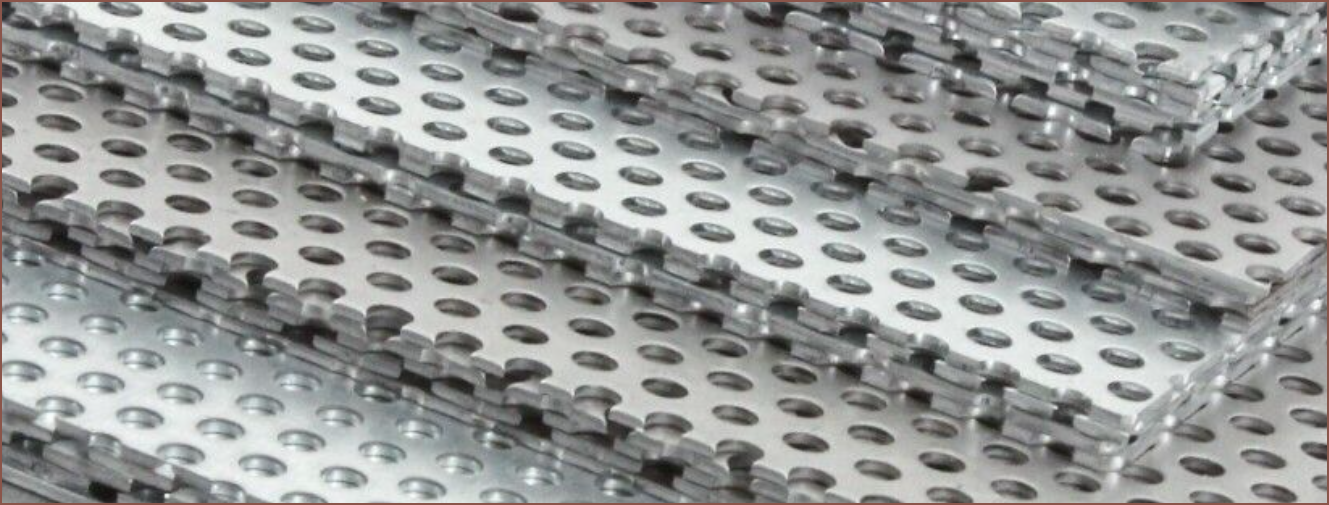
[19 Jan]
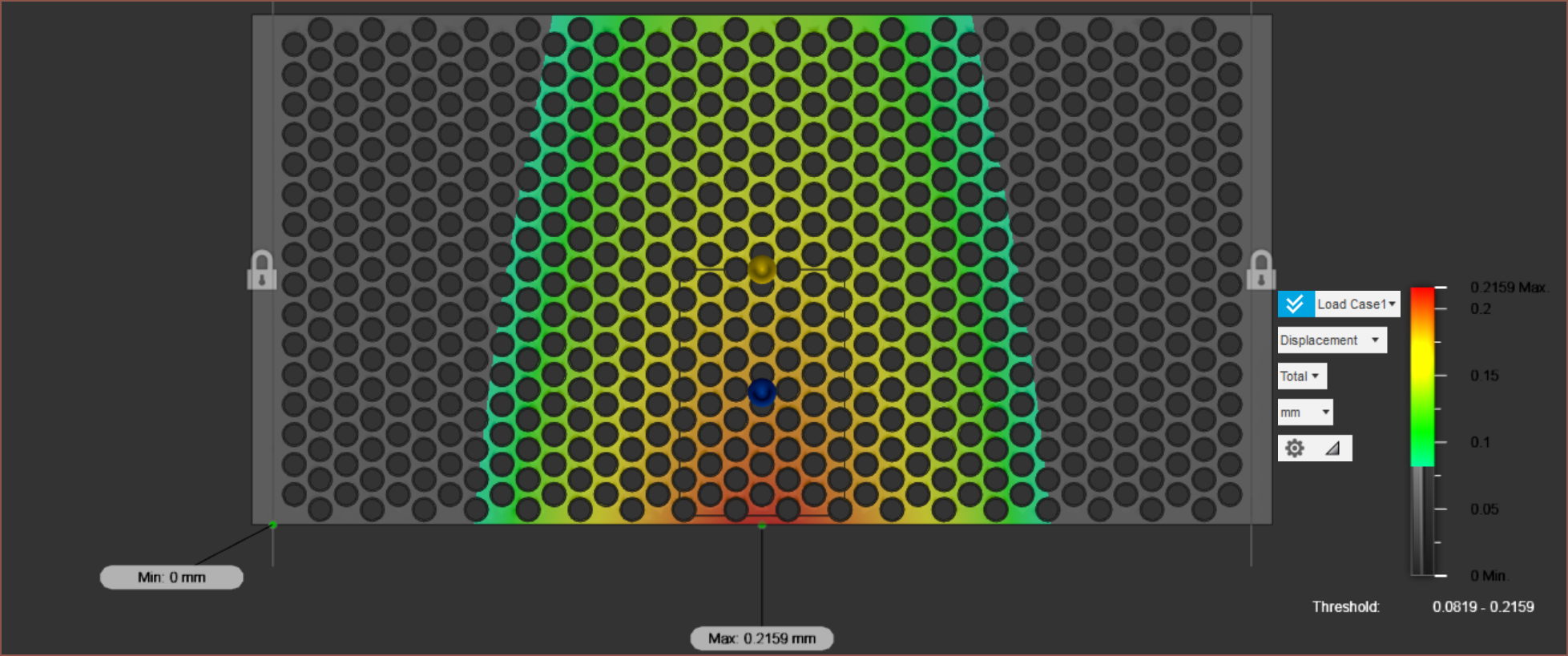
Unfortunately, the size of an M8 bolt is less than a millimetre smaller than the size of an M16 thread, so I'd need to aquire smaller bolts. Obviously, that's nowhere near as tedious as drilling 610 holes into a 680x340mm bed. I predict that it'll be some 8 hour process. Hopefully I only have to do it once because it'll be £100 a bed after VAT + shipping.
This is what the same design would be in 3mm 304 stainless:
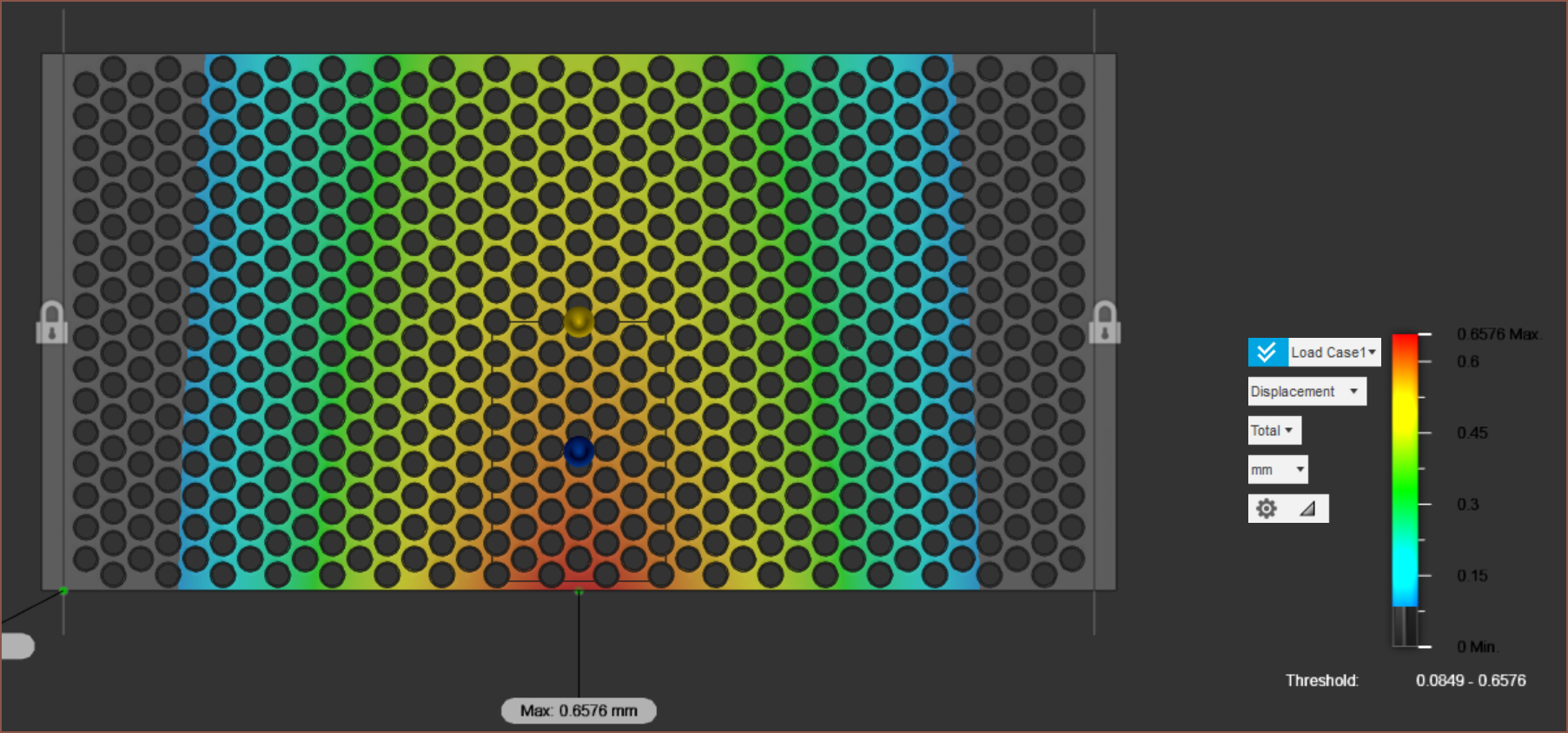
[22 Jan]
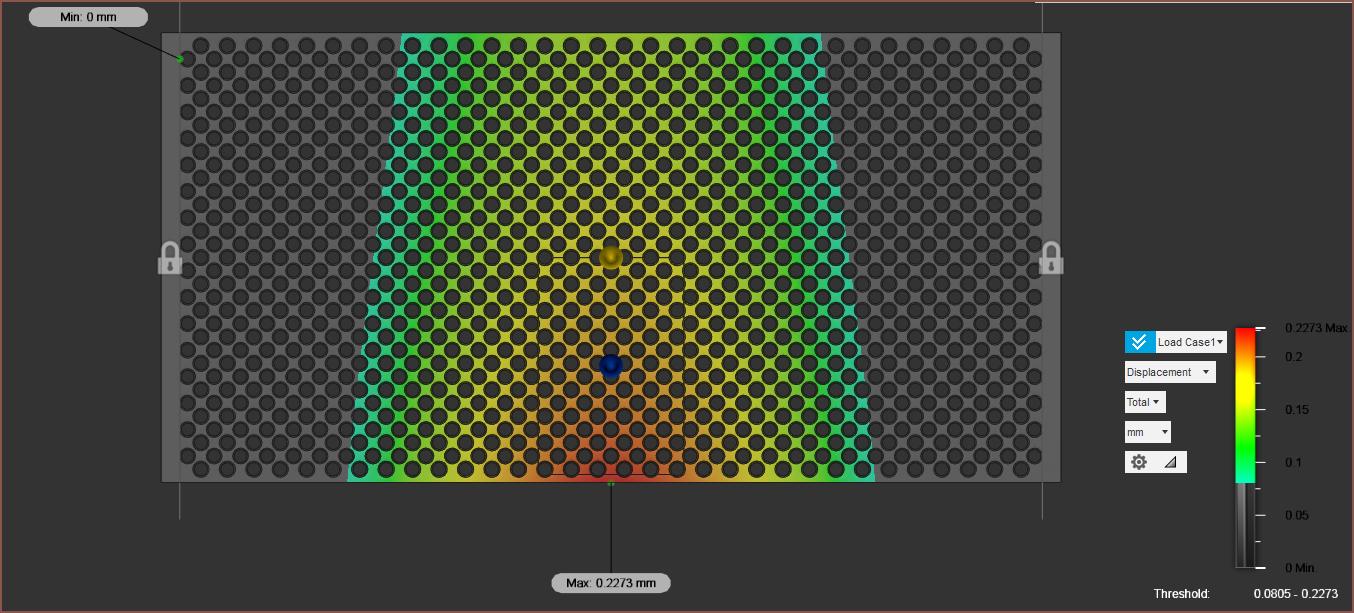
I've also tried the pattern seen on CNC fixing plates. Half of the holes are 10mm and the other half are M12 threads. Similar displacement, the holes are spaced out the same 20mm in X and Y, and the hole count is over 1000. There's slighty less surface area with this one, but the minimum thickness between holes is now a narrow 2mm, compared to almost 4mm for the M16 bed.
I might be able to use the CNC mill or waterjet my university just so happens to have, but if not I'd have a lot of holes to drill either way.
Discussions
Become a Hackaday.io Member
Create an account to leave a comment. Already have an account? Log In.