Tuesday, 09/07/2024, 16:11
I’m writing this here on google docs first.
Well, soon or later I would need to figure out how to make a PCB for controlling the mech.
I kept avoiding it because I really don’t know how I would wrap my head around these concepts. In fact, I already tried multiple times to learn how to make the control board, but with no success…
Depending on the result of this “serious” attempt may or may not result in the possibility of a brushless linear actuator instead of a sliding contact one like I was babbling about in the previous project log. After all, both the ESC and the energy supply would do basically the same thing, changing the voltage, amperage, frequency and which actuators receive it.
Also, I don’t know if all this work I had making a rough estimation of the coils strength would actually be useful, since, you know, the energy would be divided by all actuators and rarely a single one would actually use all the 200,000 watts of power.
And I also doubt the system would even survive such energy input… Maybe I’m really over-engineering this thing with all these 40 ton cylinders.
… Bruh, 9 days in and I still didn’t even start to research this subject. I’m procrastinating too much…
Bruh² my drawing table with a display from Huion stopped working out of nowhere. 😐
Luckily I’m still within the time duration for a refund.
Now I don’t know what to do… Do I try to buy another table from a different seller or just… Keep going with this project…?
I bought a used one for ⅓ of the price, lol.
… I've been procrastinating for so long, and this project has already taken so uselessly long that I’m wondering if I should hire someone to design this garbage can for me.

Oh yeah, I tried it before, they asked for AT LEAST 30,000 reais (5400 dollars).
ACTUAL WORK:
Goddang it, I hate how I procrastinate so much, but I think I can trick my mind into properly working right now.
Basically, I was literally saving a bunch of videos explaining the literal basics to advanced concepts involved in electronic systems, so it was a daunting task for me from the beginning. SO, my “brilliant” idea was to actually take already existing units of what I need and find a DIY material that can survive the insane temperatures I need it to withstand.
For example, the first system I was thinking of studying/designing/building is the DC to AC inverter for the molten fuel cell.
The molten fuel cell will be at around 400ºC to 650ºC, so I can’t just buy a commercial inverter. However, I could copy the system schematic of a commercial one and replace the materials with high melting point ones.
On top of that I can only predict so much without actually building anything, and that applies to the molten fuel cell.
For example, this article states that its 10 kilowatt fuel cell produced 56 volts without stating its amperage, but doing the math, you can find that it is 178.5 amps. But it uses cells in a well produced cell, not this amalgamation of inconel and stainless steel that I intend on making.
And I NEED to make the cell this way, because if I’ve made it the traditional way, it would be the size of a truck.
… Now that I think about it… In a molten carbonate fuel cell, how the amount of electrolyte is determined by the amount of energy I need for it to output? What is the calculation for this?
WebGPT keeps saying out of its butt that the Molten Carbonate Fuel Cell needs around 0.1 to 1 liters of electrolyte per kilowatt, but never gives a source for that.
So, 300 liters of electrolyte = 660 kilograms, 0.1 x 30 = 30 liters = 66kg.
Of course, ASSUMING it is correct, which probably isn’t.
In other GPT’s available on the same website they tend to say that the higher the temperature, the less electrolyte is required. But I don’t know how true is that, since the truck-sized 250 kw molten fuel cell is also at 650ºC
However, in all articles the power generated both in watts, amps and volts are based on the SURFACE AREA, not the amount of VOLUME, nor WEIGHT. So I’m PROBABLY alright as long I allow the fuel cell to have as much surface area as possible proportional to the output energy.
“The peak current density achieved was 120 mA/cm2 at 0. 8 V and 800 °C (96 mW/cm2 power density, 80% efficiency) with furnace black. This power density is of the same order as gas fed molten carbonate fuel cells that generally operate around 120 mW/cm2 [180], however, the efficiency of DCFC is significantly higher. The results also showed that nano-structured (crystallographic) disorder of the carbon particles, electrical conductivity and reactive site density control the rate of electrochemical oxidation and efficiency of the cell with the purity of carbon fuel being less critical”
Source: https://www.sciencedirect.com/science/article/abs/pii/S0360128512000044
Since the wattage is 120 mW/cm2, then I would need
In the Project Log 80 I calculated that the hydroxide fuel cell (which works just like molten carbonate fuel cell) would need 1kg of inconel/stainless steel wire with 0.8mm of thickness to fulfill the 20 square meters of surface area.
Since the value of 250 m² is around 13 times more than the previous calculation, I would need 13kg worth of wire. And I was intending on using the wire because I would organize everything in an hexagonal pattern.
BUT, if we take the density of 120 milliwatts per square centimeter, and divide it by 300,000 watts, then the size in square meters would be around 4774m². Well, at first this seems like a lot, but if you take the value of 250x250 meters in an area calculator, it gives 62,500m².
If you add the 4775 m², it will give 69,1 meters on each side (nice).
In the truck-sized molten fuel cell I talked about it is stated that the closer to peak power the cell produces, the higher its efficiency and performance. So maybe it would be interesting to have a cell for every 100 kilowatts of output power.
so, each one of the 3 cells will have an area of 1.600 m², which would be around a square of 40x40 meters.
If we take the rectangle volume calculator and add the 40x40 meters and 1mm of thickness (like this is a supersized cell), it will have around 1,6 m³. Taking this volume and the density of lithium carbonate and inserting on the density to weight calculator, I would need around 3,376 kg of electrolyte.
The same goes for the stainless steel cathode/anode, which would weigh 12,800 kg or 25,600 in total for both.
I was thinking of using an hexagonal pattern for maximum usage of surface area with the 0.8mm wires, so I would “just” need 477.5 kilograms of wire to reach that desired surface area.

Source: https://www.sciencedirect.com/science/article/abs/pii/S0378775316316214
I would need to reduce the thickness of both by at least 100 times, or 10 micrometers. And I inserted the new values in the density to the weight calculator, and it would still weigh 33kg and the cathode/anode would weigh 256 together. I would need literally 1 micrometer for this to be “just” 3.3kg and 25kg.
And that is from a single 100 kw cell, the three cells would weigh 84.9 kg.
I would need one of these to check its thickness:
Good thing they aren’t that expensive, now the problem is: would the cathodes and anodes even survive the extreme conditions of a molten fuel cell while having just 0.01/0.001 mm of thickness?
Should I just switch back to the charcoal engine or keep going?
… The fact that I procrastinated this much just to understand how much I screwed up is just…

Well, I do intend on incasing everything into silicates such as sodium silicate, potassium silicate, lithium silicate etc.
So, maybe by spreading the powder of either material inside the silicates, then you wouldn't need to worry that much about thickness as long you have the powder proportional to the surface area you want to achieve.
I would need to measure it by its weight and/or amount of volume (milliliters, milligrams etc) and then spread the cursed paste as thinly as possible.
... But I don't know...
Whatever I have to do with this piece of crap to make it work is way simpler and easier than making the charcoal engine.
I guess I will just keep going and see where it leads me...
I don't know if this idea would work, but I was wondering: what about high surface area materials?
Sponges, 3D printed materials or whatsoever, they could be used to make this work, no?
For example, since I intend on mixing everything up in sodium silicate, then everything is technically a liquid coating.
I could dilute the silicates and the materials in a really thin liquid and switch between baths covering a 3D printed high surface area object.

Source: https://www.sciencedirect.com/science/article/pii/S2352710224011999?dgcid=rss_sd_all
If you add an electrode to each end, and each bath will only touch one of the endings, then you could make it work, no?
Although, it would be a pain in the ass to continuously switch between baths and drying periods. Because I do think that if you just dip it in sodium silicate without first heating up the layer, the coatings would mix.
The problem is: how the fuel will travel through these microscopic channels?
Maybe you could make the two channels in a factral pattern, or just a conventional spiral pattern with the surface area that you require (4775 m²), this way you could maybe make both the coatings in a practical manner and the channels too?
I'm just brainstorming here.
I Just checked the area of cylinder calculator, and a channel with 1mm of inner diameter would need around 150 meters of length in order to reach the surface area of 4775 m².
Obviously, this is assuming that all the area of the wire is used, but in reality you would need around 3 times more wires to make 3 or more coils of wires connecting on each other.
So, the steps:
- Make a 3D model of the air and fuel channels in spirals that can be moved around.
- 3D print it with a resin printer or a fdm printer.
- Use the Silicate bath to cover the cathodes and anodes with their respective layer of conducting material + catalyser + stabilizers.
- Once dried, cover both in a layer of silicate with the electrolyte or just shove both of these in a bath of silicate with electrolyte.
- Dry the silicate again.
When I say "dry it up" I mean heat treat it, once sodium silicate solidifies you need to further heat it to 100ºC so the structure.
My only issue with this idea is that I have no idea how effectively will the powdered materials stick to the tubes/channels. I suggested dilluting it first, but I'm not so sure right now.
But do I really need to make it a 1mm thick wire tho? I could "just" make it a 1mm thicker plate/cylinder and so on...
I also made a mistake, it seems like the 1kg of 0.8 mm stainless steel wire for the electrodes would indeed just weight 1kg for each electrode.
So there is that...
… BUT I don’t think the steel will survive, being honest with you.
I think that maybe it will be better to use the magnetohydrodynamic generator, it only has an efficiency of 30%-20%, unlike the Molten Carbonate fuel cell, which can reach around 60% or even 80% depending on the design.
So, how would that be better?
Because of the key phrase here: “depending on the design”
My design is literally made out of scrap and trash, made with no regards to precision, durability or long-term use.
And the high 80% efficiency is achieved through carefully planned heat recovery in steam systems, on by itself you can expect a maximum efficiency of 40%-45%.
So, why bother with a charcoal engine that will be super complex, a molten carbonate fuel cell that will be a hell of a labor-intensive work instead of “just” working with the plasma-furnace that is the MHD generator?
The only thing that kinda gives me hope on this design for the molten fuel cell is this paper that states that their corrugated plates are made in the micrometer thickness, literally reaching the same conclusion I reached about the ideal thickness of the components for the fuel cell.
However, this other article shows what the corrosion can do, specially in the oxygen electrodes.
They literally oxide really fast because of the presence of oxygen in a high temperature environment, meaning that I will need to either find another material for the oxygen side or scrap the idea all together.
I say this because anything containing nickel is AT LEAST 5 times more expensive than stainless steel, even nichrome, which is cheaper because only contains around 30%-20% nickel is already 5 times more expensive.
I could use graphite+sodium silicate as the electrode... I'm stupid.
Wait, I'm stupid², the graphite electrode would run the risk of being consumed while working.
No, I'm being stupid³, the article in which I linked stated that their cell experienced rapid deterioration AFTER they started doing electrolysis, not the regular work.
"The possibility of producing hydrogen from molten carbonate steam electrolysis using the well-established Molten Carbonate Fuel Cell (MCFC) technology was explored in this work. For this purpose, a 81 cm2 MCFC single cell assembled with conventional cell materials was operated under alternated fuel cell/electrolysis conditions at 650°C in a binary eutectic Li2CO3-K2CO3 electrolyte for about 400 h after an initial period of 650 h in which the cell worked only in the usual MCFC mode. A rapid cell performance loss in terms of cell internal resistance and electrode polarization was observed as soon as the cell started to work in the alternated fuel cell/electrolysis mode. "
It is literally in the introduction, but I didn't pay attention.
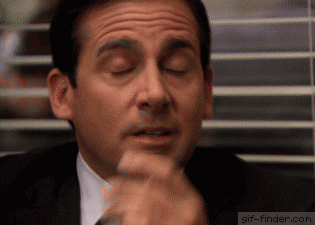
Now I'm absolutely in doubt.
The response time to change in wattage output of the Molten carbonate fuel cell can range from seconds to minutes. Essentially, if I'm adding a certain amount of fuel and out of nowhere rapidly increases its input due to higher demand in energy, the fuel cells would take whole seconds or even minutes to deliver that extra energy.
You could use lead-acid batteries and capacitors in order to deal with these spikes, but we are talking about 100,000 watts of power and peak power outputs into 300,000 to 400,000 watts. That is around 300 kilojoules of power spikes.
Lead-acid batteries are expensive and equally heavy, I literally cannot fit a power pulse system of such size magnitude of power in a mech.
I could use a flying wheel system, but that would also increase another loss of efficiency...
I mean, even a normal capacitor/battery system would decrease its efficiency...
Maybe I should actually work with the MHD generator...
Well, assuming an efficiency of around 30% and the energy density of charcoal being 30 megajoules per kilogram, if I want to output 100 horsepower for an entire hour, I would need 30kg of fuel, in a total of 300kg of fuel for 10 hours of continuous output of 100 horsepower.
In 1 minute, I would need to insert 5kg of charcoal, and in 1 second, I would need to input 0.083 kg of fuel.
This means that the MHD generator would instead need to be really, really tiny.
Of course, this is just taking into consideration that this would be the space required to react 83 grams of fuel in a stellarator configuration.
The stronger the magnetic field, the more efficient the MHD generator, and the smaller the distances between everything, the stronger the magnetic field.
Wouldn’t that mean that I could get away by buying and using smaller magnets or just electromagnets for high tesla magnetic fields?
For example, this video teaches how to reach that:
However, if you take the principle of a MHD generator, it is indeed required to have a large surface area for its electrodes. Since it is how it is able to convert the heat and flow into electricity.
Google didn’t show me much about something like an electrodeless MHD generator, which would be just perfect for this. The idea of an electrodeless MHD generator would be that the ripples on plasma itself would make ripples on the coils and magnetic field, just like an alternator/dynamo, and that is how you would extract energy.
I still need to get a grasp on it in order to check if it is efficient or even possible to do that.
Well, my gut feeling is telling me that is not possible.
If we use the alternator/dynamo analogy, either the coils or the magnets are the ones rotating while the other is stationary. This means that for the perspective of either the stationary or the rotating part, the other part is rotating its magnetic fields. These magnetic fields traveling through the coils, a potential difference is produced into the coils. Like ripples or waves that go through a hydro turbine.
If the coils are stationary and the magnetic field is also stationary, what would change in the system? If you assume the plasma to work like the coils, it will rotate and ripple, but it needs to be connected to the system somehow to transfer that energy, thus the electrodes.
If there is no electrode, then how will the plasma transmit its energy?
I could only think of turning the plasma in an induction coil, just like a wireless induction energy transfer.
But how would you make this work?
I tried to search for induction magnetohydrodynamic generators, because that is exactly what it is. But…
This article says that this generator is not viable.
“The observed response of the generator is in accord with the theory. The fairly close agreement indicates that the assumptions made in the analysis were justified. It has been found that this generator is not a practical power generator. An output power of 10W is very low in comparison with that which has been obtained from electrode-type MHD genera-tors, for example by PAIN and SMY.”
Another way I could think of making this work would be if the plasma mirrors the magnetic field in the chamber, creating the ripple into the magnetic field without moving other parts.
But I’m really not sure how that would work.
Google only showed me a couple of papers about inductive MHDG’s.
This one is just a simulation of a proposed design that SEEMS to work fine without the extreme conditions found inside conventional MHD generators, but they didn’t talk about its expected efficiency:
https://www.researchgate.net/publication/320431128_Simulink_model_of_an_iductive_MHD_generator
This other paper states that a 300 kilowatt version of the proposed MHDG would have 70% of efficiency, but you would need really high speed gases with equally high temperatures.
https://www.rand.org/content/dam/rand/pubs/papers/2008/P3837.pdf
This one uses an arc generator of 2000 amps and 500 volts (1 megawatt) to make the system work, and I’m not very sure if I understood the efficiency of the whole system.
https://apps.dtic.mil/sti/pdfs/AD0403369.pdf
These two articles discusses the simulation of a inductive MHDG just like the first option, but with higher performance, slightly above ambient pressure and speeds below and above sonic speeds.
https://ieeexplore.ieee.org/document/5544810
https://fupubco.com/futech/article/download/119/88/654
I think it is best for me to stick with the Molten Fuel Cell, the MHD is way too complex for me.
(I mean, both types are super complex and I'm just taking a simplified approach)
I hate how indecisive I am…
Off-topic:
On a unrelated note, I just saw this artwork of a car cockpit, but for some reason I can only think of it as a mech cockpit. Maybe I will use that as inspiration, lol.
But now that I stopped to think about it… I think in the end the mech will be heavier than the target I wanted. For example, in the previous project log I talked about the weight of the 14mm thick coils, and they would weight 150kg in total, then you add the weight of the polymer structure of the actuator +90kg (or a little less), then the pilot +100kg (more or less), then the fuel +200kg, then the fuel cell + 50kg, then extra structure to keep everything together, I didn’t design it yet, but I’m willing to bet around +100kg.
So, 150+90+100+200+50+100 = 690kg. Almost 700kg.
I could change the sizes, reduce the weight here and there, like cutting the fuel to 100kg and reducing the shapes of the actuators to around 40% less weight depending on what you do, like adding graphene fibers etc. Well, with all of that, it could be reduced to around 500kg or less. I could further reduce it by reducing the number of actuators per limb, instead of 6 per limb, just 4.
On a similar note, I still think about the possibility of using continuum robot limbs (tentacle Dr. Ock style arms), I do wonder if making the tubes slightly flexible would allow them to be used just like artificial muscles. But what always keeps me away from this option is precisely the lack of simple predictability. I can copy hydraulic actuators and linear motors, but what can I copy a continuum robot from?
Well, after thinking about it all afternoon instead of doing what I’m supposed to do, I think the continuum robot could be used for the fingers instead… I think…
But I have to admit, continuum robots always keep my imagination active, I can’t help but wonder how a mech with this mechanism would work/look like. You could make them extend and contract just like Dr.Ock’s robot arms, but what if you wanted them to be as short as a human being’s limbs? Wouldn’t that essentially be a hybrid between mech and exosuit? Could you do the same thing with the rigid telescopic actuators I previously suggested?
I just saw this video here, I really can’t see a mechanism like this lifting a ton of weight or doing anything remotely strong at all.
And on top of that, if I were to build something like a continuum robot meant for heavy duty applications I can’t think of it as a safe to be around machine. It would need to be really, really rigid and heavy.
A good example is him showing how the continuum robot would just fall without any stiffness, but you could avoid it by pulling another cable in the opposite direction, forcing a compression load. However, if you do that, how much of the force applied would be just fighting against its own weight? How much of the force applied would be just fighting against the opposite actuator? How much of the remaining force would be enough to lift something heavy?
An ideal scenario would be to have a pulling and pushing actuator on opposite sides, but the problem is that you can’t really make a flexible pushing actuator, can you? You would need to make it absurdly stiff, no?
The only ones that I could find that would work like that would be articulated/spine-like continuum robots, which wouldn’t allow for a human-safe machine.
Perhaps attaching the actuators proportionally to the limb’s length would help, for example: making the diameter of the tentacle ⅓ of its length, this way it would work just like a lever. If not for its entire length, at least for the majority of it, getting smaller at the tip and wider at the tip to compensate for the distribution of loads (you need to apply more force the farther away from the tip, just like a lever).
Maybe you could do a segmented continuum robot using non-extensible ropes/knots, but I couldn’t find anything like that to copy/use as an example.
I mean, imagine one of those super thick naval ropes, they are so thick that they are almost rigid. You could achieve the same with a really, really dense knot, no?

I mean, there are basket ropes that seem quite solid:
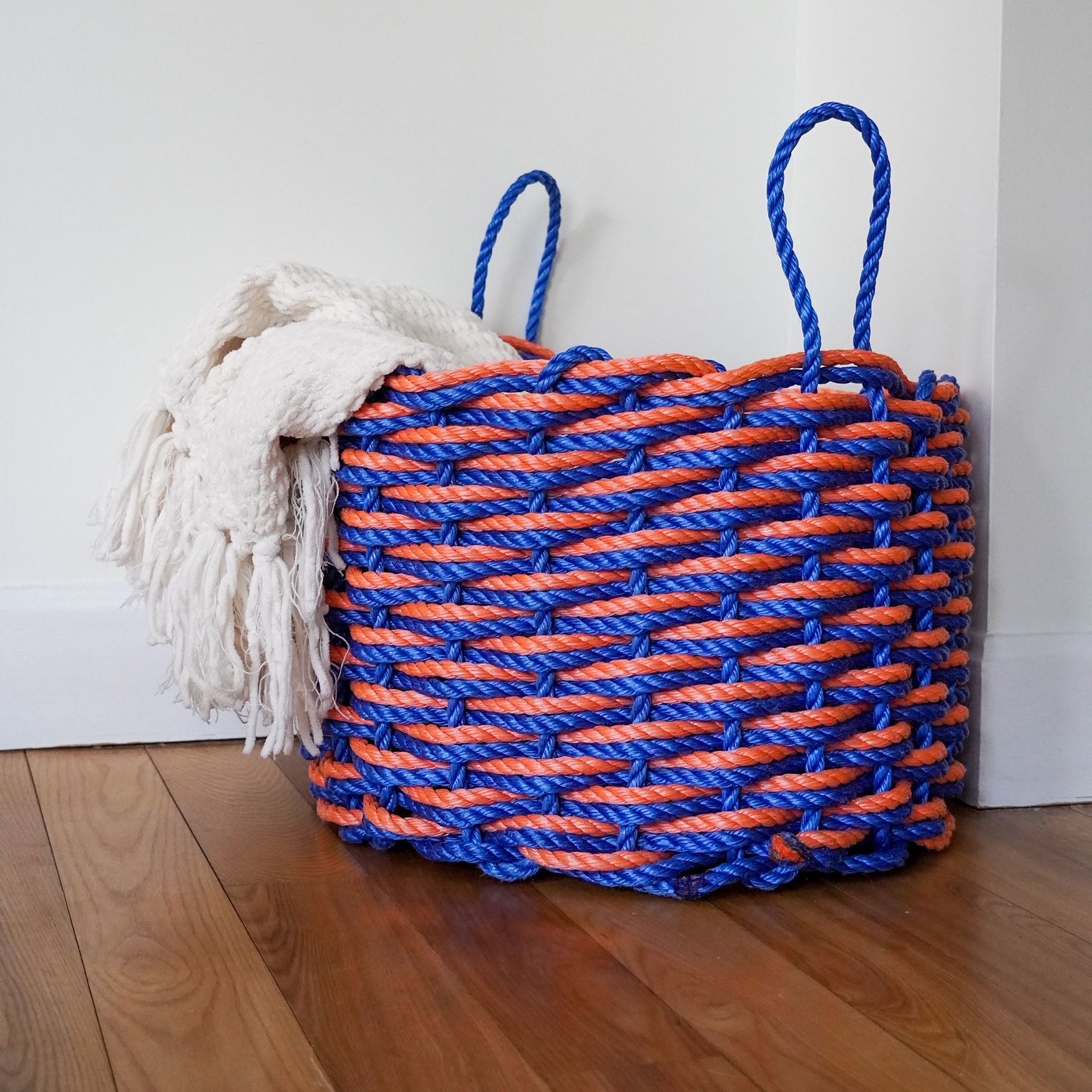
But I still have difficulty imagining it sustaining around 1000kg of weight and maintaining its shape…

Pneumatic jacks exist and I could totally see those lifting something as heavy as this target in a continuum configuration, but they are pneumatic and inherently inefficient…

MAYBE one could make use of a pneumatic syringe compressor/pump (or just that hydrolysis pneumatic muscles), just like those syringe robot arms. I don’t know if it would be efficient or practical though, it works in hydraulics because of the non compressibility of liquid. With a gas, maybe you would need to make it high pressure for increased efficiency in power transmission.
However… Do I really need a pneumostatic transmission or anything that crazy? I could literally just have a balloon-like segmented body and insert the electric flexible actuators inside/around its body.
… But even if I make it like this, would it even be a stable mechanism? The idea is to make a low-mass and flexible body for safety around humans, so any impact would be like being hit by a pillow Wouldn’t that mean the entire mech/exosuit would be super wobbly and unstable?
And in the end, whatever design I choose, a Baymax balloon-like mechanism or a solid spinal mechanism, why would I choose this continuum mech instead of the conventional one?
The only benefits that I can think of would be:
- If you imagine it as a very long stewart platform, you only need to worry about the position of the base and the position of the top-base. So it could be simpler to make the fingers while keeping them safe to humans, I THINK. I also thought that it could be interesting to add a balloon-like outer shell to the mech to avoid injury to humans nearby.
- The segments would be exactly the same shape, but in different sizes, so it would be easier to mass-produce them with fewer molds.
- Since the actuators would be in a different place to the body, I think it would be simpler to produce them, keep them safe and to maintain them.
- I wouldn’t make them a telescopic linear coil, like that radial sliding contact motor I talked about in the previous project log. Such a motor would rotate a hoist-like mechanism that in turn would pull the “ligaments” to the continuum limbs. But in such configuration I would need to add the balloon segments for extension and compression…
I feel like I talked about this so many times and I’m already repeating myself needlessly in this project log…
Kinda unrelated, but I asked a friend of mine why the hell someone would want a mech/exosuit with continuum arms and he suggested that it would be a good mechanism for climbing buildings. I thought it was a really interesting idea.
Also, look at this cool snake/tentacle/continuum-tank
https://www.flickr.com/photos/lord_dane/48785087506
Well, I made up my mind, an exoskeleton with the same power output as this mech (or rather, mini-mech, since it “just” has 3 meters of height) would be insanely cramped. Imagine fitting 6 actuators with 10 to 20 cm of diameter in each shoulder and thigh?
I hate to admit it, but the only reason I never truly get over the idea of making an exoskeleton like that is because of the terminator in Warhammer 40k.
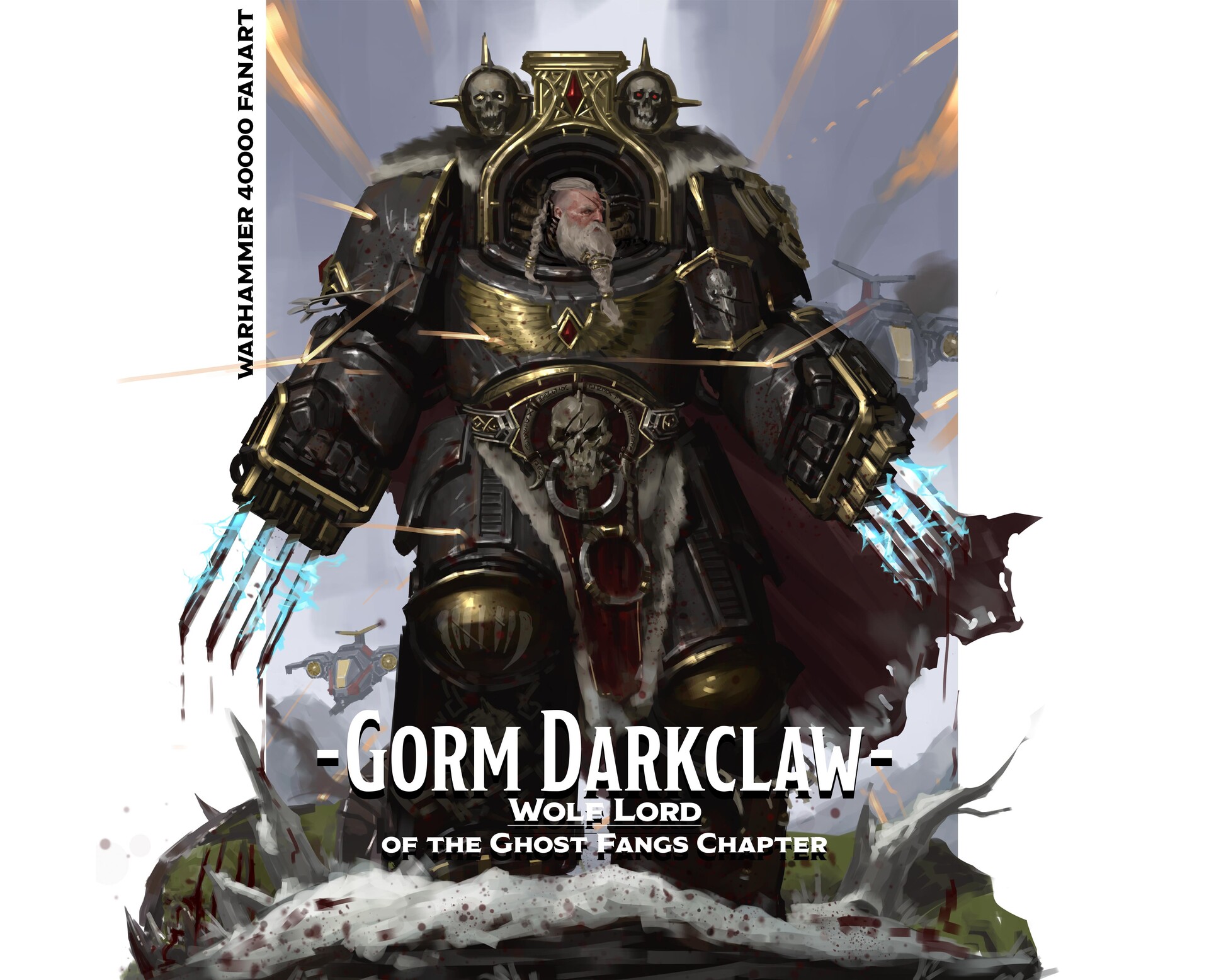
Source: https://www.artstation.com/artwork/g0VOdP
Look at how cool this thing is!
They’re like the middle-man between exoskeletons and mechsuits, lol.
(accordingly to ~le lore~, the terminator armor was originally an exoskeleton used for working in hazardous environments [and it is also nuke-proof])
Only power armor that can be more power armor than the ones in Warhammer 40k is this one, lol:
Ok, I’m done procrastinating. I need to finish this project log asap.
… But before that, I just want to say that I was wondering about artificial/synthetic cells. Essentially, I wonder if it would be possible to make biomimetic machines that imitate cells, not necessarily nanorobots and the like.
https://en.wikipedia.org/wiki/Artificial_cell
The closest thing that was actually built in real life was the “xenobot”, that thing scientists made using frog cells to make organic materials work in artificially pre-programmed ways.
https://en.wikipedia.org/wiki/Xenobot
It would really be convenient if we could “just” grow robots and machines in a tank instead of building everything from the ground up.
This really tempts me into researching the subject and even maybe starting a project on its own, actually, every idea I have is kinda like that. Unfortunately, I’m not knowledgeable, skilled, nor dedicated enough to make such things.
Maybe a matryoshka machine would work? Essentially, it would be a machine that makes a smaller copy of itself, and that copy makes an even smaller copy, until it reaches a maximum practical point (you can’t really build things smaller than atoms). And it got me wondering how I would make a 3D printer that could make smaller versions of itself, including electronics, actuators, filaments, etc.
… But maybe I’m overthinking this?
For example, there is a thing called “Pantograph” that is a mechanism that can be used to make smaller copies of a drawing:
Maybe you could use it to build micro-machines/synthetic cells.
Obviously, the already most used approach is lithography. Which is used in the production of microchips and the like, but these need a ton of chemicals that may not be accessible/practical to make half a ton of micromachines.
Unfortunately I kept thinking about it instead of doing what I’m supposed to do…
Well, I thought on the subject, and maybe the idea of “simply filling a tank with chemicals and letting the synthetic cells do all the work” wouldn’t work as simply as that. You would need to literally make a synthetic parallel for every part of the human body down to its very DNA, which would result in a synthetic human clone and not necessarily a robot. And if anyone ever makes an actual conscious “syntheth” human using this absurdly complex method, I just hope they don’t enslave the poor creature.
The “best” idea I had would be to keep the “Pantograph machine” mass-producing the micromachines necessary for every major function and another class used specifically and only for organizing these micromachines in place.
The micromachines would essentially be like those origami micro-robots used in medical applications.
Imagine every single micro-machine a “cell”, and those cells would be built for a single, limited role with the most basic function possible.
Essentially separating between actuator “cells” (used as muscles), energy storage “cells”, energy transmission “cells”, energy generation “cells” (if you use fuel cells instead of batteries), control pathways “cells” (essentially neurons/nerves that directly connect to a USB port or anything like that, maybe system board cells would be needed), structural “cells” (various types of machines/materials that would act as different types of binders and insulators for bones, ligaments, tendons, muscles, nerves etc) and finally the “organizer cells”. By the way, I was thinking of the energy generation cells being micro molten fuel cells that take the fuel around it (like charcoal powder, mineral oil, etc) and provide energy to surrounding cells.
Every type of synthetic cell would need to perform a function and have a sensor array for position feedback and function feedback, while the organizer cells would need to consume the energy-cells in some way and be remotely connected to the program controlling everything. I have no idea how the energy would be transmitted and how the cells would be powered, either you would remotely power/control everything using electromagnetic waves or every cell would have a wireless transmission coil to transmit power to everything. Basically, the outer surface of the “cell” would have these coils, and unless they are using it, they re-transmit to the other cells around it. It would be very inefficient to just allow the waves to travel everywhere until they find a cell that actually needs it, so you would need another cell to specifically connect to the central system and transmit that energy where it is needed. Either using it or storing it.
The computer would need to painstakingly monitor and control every organizer cell position and state, constantly changing malfunctioning cells of any type. I don’t really think that it would be possible to make the synthetic organism system recycle and replace these malfunctioning cells by itself with a built-in factory or something. So you would need to collect the malfunction cells (like poop, lol) and feed it more healthy cells.
Ideally, you would let the system board and control be a decentralized group of cells completely encased into the synthetic organism. But being honest, I’m not really sure how you would make such a thing in a viable way.
I just saw this hacksmith video where they use a coating that is so strong it can withstand the tensile force of around 4444 pounds (2 tons), and they showed it being tested:
It is a “proprietary alloy”, so unfortunately, I have no idea how it is made. And if I knew how, it would probably be super mega expensive and complex…
In the company's website it is said that it is something made out of cobalt and phosphorus, but without giving any details, of course.
https://www.integran.com/electroformed-alloys-and-components
So yeah, definitely expensive, anything with cobalt, that is.
Now that I calmed down about the subject, I can confidently say that I’m insultingly talking out of my ass and insultingly oversimplifying a very, very complex science. Everything I said is probably useless.
(just now that I finished writing all this crap I remembered that the actual name is photon propulsion)
One thing that I just saw these days was laser propulsion.
There are a lot of ways of ways that you can use lasers for propulsion, but I’m talking specifically about pulsed laser propulsion:
In the video, a really powerful laser pulses multiple times per second, the little aircraft model focuses the light in certain points, ionizing the air in what are essentially tiny explosions.
So, the idea is that if you have a sufficiently powerful energy source, and a sufficiently powerful (and efficient) lasers, you could propel any aircraft with it from earth to space without the need for ejecting mass. Fusion rockets and Fission rockets are the absolute option when it comes to efficiency and power output, but they need to eject mass. Either ionized gas (plasma) or steam. Increasing the weight/size of the spacecraft and limiting its range based on the amount of ejectable mass. And in the end, this would be a really strong weapon since photons can push stuff (which is the first way laser propulsion is planned to be used for [I do wonder which is more efficient: a coilgun or a laser propelled gun]).
However, if it was that simple to make something like this to work, then it would’ve been done.
First problem is that the on-board laser would need to work with nozzles for maximum efficiency. On top of that, these nozzles would work more like a pulsejet, where air comes in and it is detonated. You could use it to make a rotating detonation engine for more efficiency, but it would still need an air intake, be it through check valves or compressors (the latter which would be a waste of weight, and thus, energy). There are valveless pulsejets, but these are even less efficient than the already inefficient pulsejet. For precise numbers you would require research specifically for thrust efficiency, and I couldn’t find any.
The second problem is that, even though I talked about “no mass required”, the laser on the vacuum of space would PROBABLY have super, super low thrust (I say probably because I couldn’t find a single article talking about such possibility). So, to truly escape a planet’s gravity, you would need to either go super, super fast, or take some mass with you (be liquid, solid or gaseous) to eject in the pulsed laser thruster. Once you are in space, then you don’t really need that. But again, the thrust would be really, really, really small (I think). So, unless someone finds a solution to that, you would still need to eject mass.
From a forum that I found:
“Light propulsion does not give much thrust for the energy input. The formula is: F=P/c F is the force in newtons P is the power of the light beam in watts c is the speed of light in meters per second If you had a laser with 299,792,458 watts it would give a propulsion force of one newton. A newton is the amount of force required to accelerate a mass of one kilogram by one meter per second per second. This is equal to about 100 grams. To equal the Falcon Heavy thrust of 5.13 million pounds you would need a source of power equal to 7x10^15 watts. This is about 1400 times the currently installed electrical generating capacity of the world.”
The third problem would obviously be the efficiency of the laser, which is directly linked to its cost. Only diode lasers can reach efficiencies around 90%, and those are stupidly expensive. The only cheaper laser that can be easier to deal with would be the CO2 gas laser, but that one is infrared with an efficiency of 20%. Those 80% are converted into heat, something you really don’t want in a spaceship. Also, the best laser to ionize air in bursts are ultraviolet lasers. Not even to mention the cost, efficiency and weight of a nuclear fission reactor itself to keep this thing working.
Maybe in the end such spacecraft wouldn’t be useful for deep space exploration, but from earth to orbit operations/delivery/transport, which is already more than good enough in my meaningless opinion.
If your objective is just that, you don’t need to use a fission reactor with a 1 megawatt diode laser, you could still use conventional electrical generation units for heavy air travel.
Why would you want to do that? I don’t know.
I WOULD BECAUSE SPACESHIPS ARE FRICKING RAD
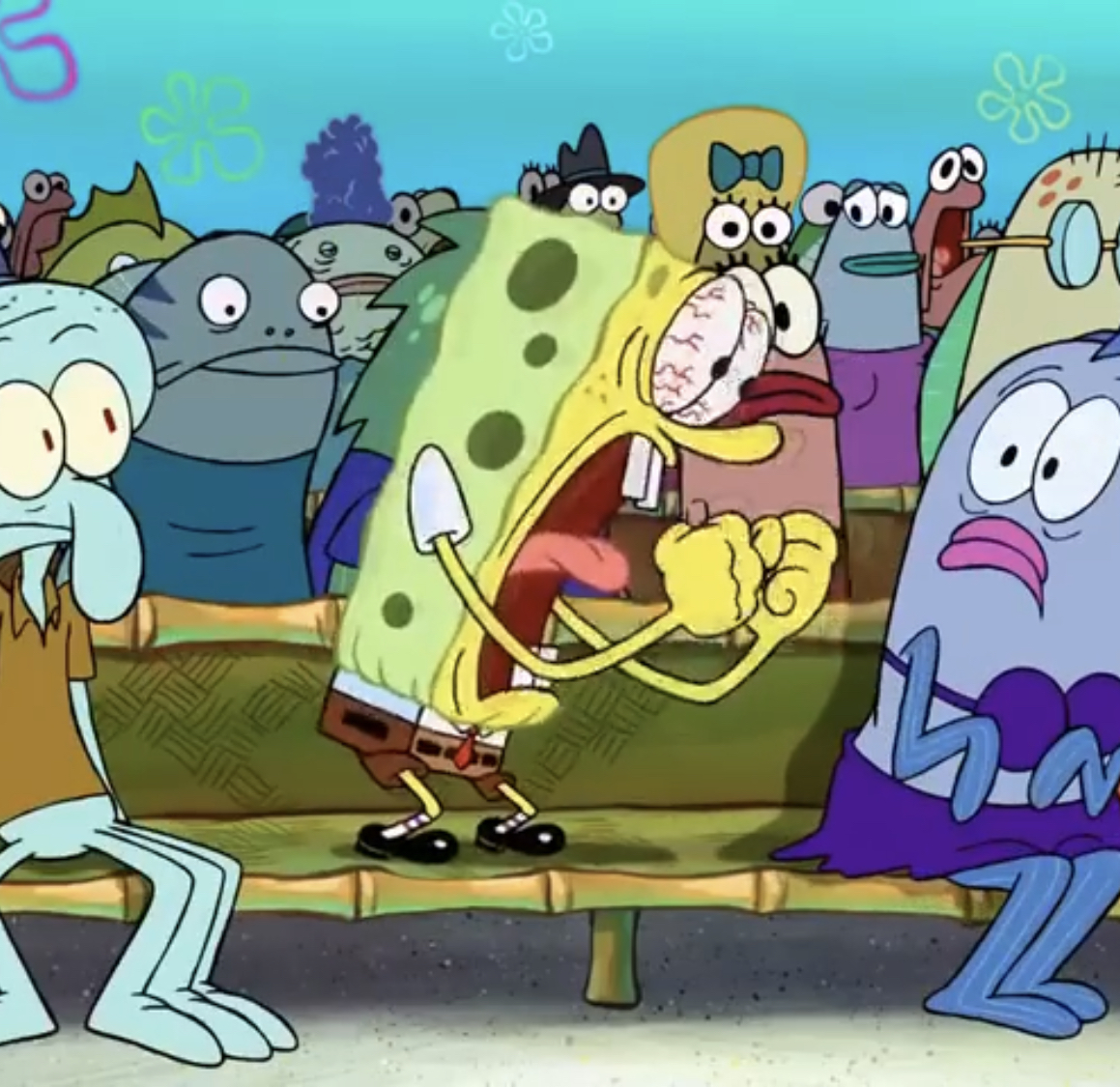
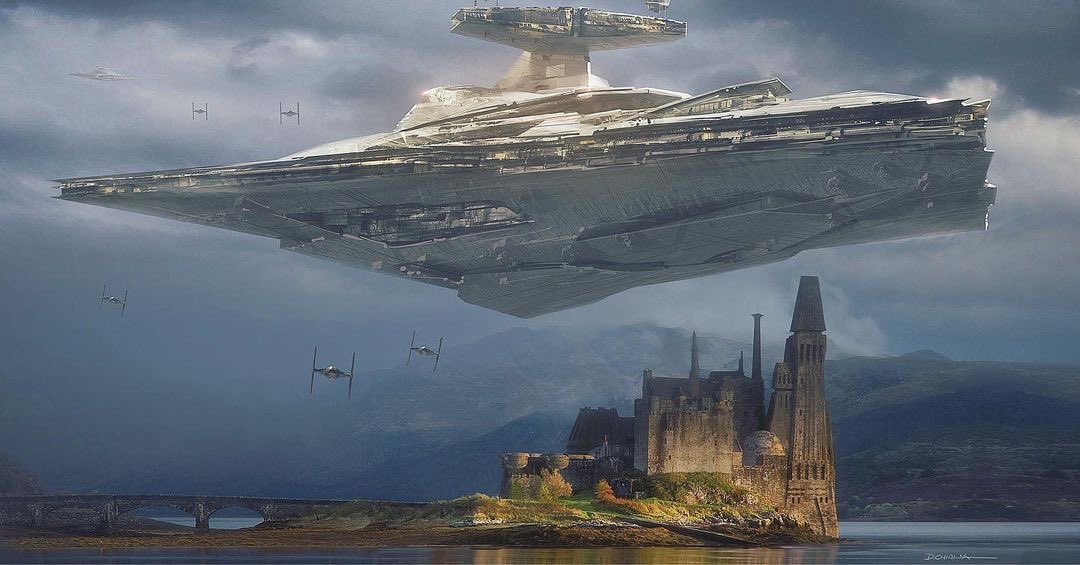
But seriously thought, I do think that we will find a way to make warp drives work by using lasers. If you focus enough energy in a spot the size of an electron, you can make a black hole, or a kugelblitz. But I’m probably talking out of my ass, because you can use any kind of energy, such as electromagnetic fields.
So, if you can create a subatomic blackhole with that, a natural phenomena in which you bend space and time, then you would need that to warp space and time.
But maybe I’m talking out of my ass, because of the way lasers work. In order to excite the gain medium (the thing responsible for making the laser beam), you need a way of converting electricity into light. Wouldn't it be more efficient to just skip the conversion and just use pure, brute electrical power to make the detonations?
The only thing that makes me think that the electrical discharges wouldn’t be as viable is the fact that they literally destroy the electrodes over time, while the laser could work continuously without much wear. I mean, you eventually need to replace the gas, but it would be easier than changing the entire structure.
Speaking of photon drives and photon weapons, I just saw this video:
I don’t know how one could make a weapon out of that thing, but I’d suppose that you could use really small leds continuously adding to a beam using mirrors and/or prisms.
But I always wondered if it would work by “simply” adding a mirrored tube and then the lenses?
Well, he posted a link for a light simulator and that just shut me up, lol. You really can’t focus it in a proper manner, just like he said (and I didn’t listen).
I found this other link where they added the equation for the fresnel lens: https://phydemo.app/ray-optics/gallery/fresnel-lens
And it still can’t make a single focal point, but a weird line.
I just found this article: https://www.mdpi.com/2076-3417/10/9/3257
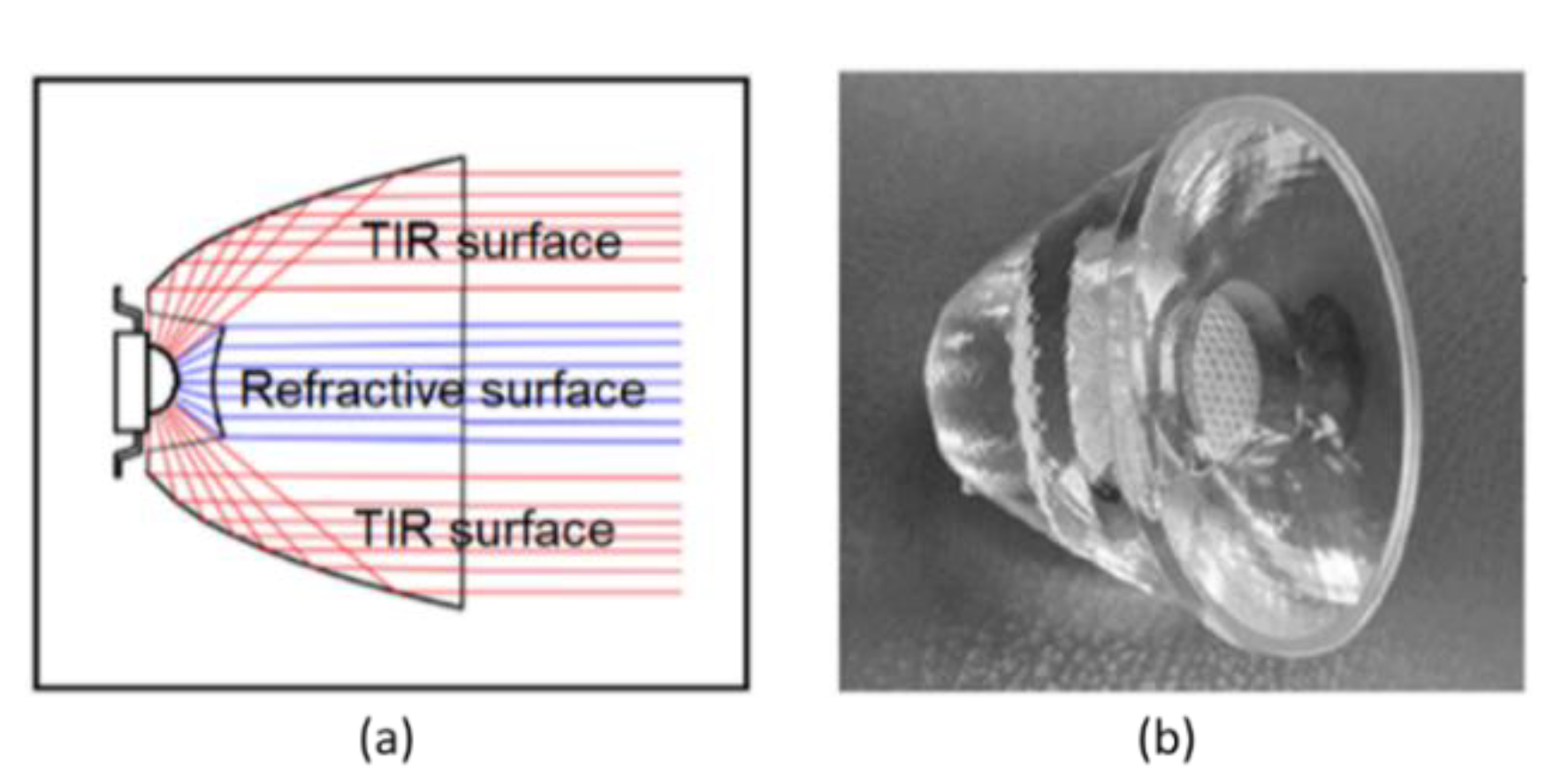
The easiest way to do an infrared laser would be to use a solid gaining medium such as Ruby rods or optical fibers, both are beyond my monetary reach.
In the end I think I would need an approach similar to the Webb Telescope system…
And I was confused about the difference between a laser and a photon:
“So in summary, the key differences are that laser weapons use a coherent, monochromatic beam of light that can be tightly focused, while photon weapons use a broader, less coherent beam of visible light. Lasers are generally more powerful and precise, but photon weapons can still be effective in some applications.”
I was wondering/calculating how many LED lights I would need to reach those 10 kilojoule rates for laser weapons, and it ends up that I would need 10,000 to 20,000 watts in LED lamps. It would cost around 1500 reais (275 dollars).
However… One thing that I forgot is that incandescent lights and metal vapor lights are more efficient in making invisible infrared light instead of the 75% of visible light the LEDs make, and they are SIGNIFICANTLY cheaper. Around 10 times cheaper.
This means that I don’t need the super complex CO2 laser that only has 20% of efficiency, just around… what? 10 to 20 incandescent/metal vapor 1000 Watt lamps and find a way of converting scattered light into coherent light. :|
Do I even need to buy it tho? The first filament light bulb was a fricking carbon filament made out of bamboo.
Well, I guess I would need to ink print a myriad of filaments with conductive graphite with the correct resistivity and then embed it in sodium silicate.
“The search results do not provide the specific length or diameter of a typical carbon filament light bulb. However, the example calculation [3] shows that for a 4 cm long tungsten filament with a resistance of 0.350 Ω, the diameter is around 0.09 mm.
Assuming a similar geometry for a carbon filament, we can estimate the ideal resistivity per meter as follows:
Resistivity per meter = Resistivity / Length
Resistivity per meter = 3.5 × 10^5 Ω·m / 0.04 m = 8.75 × 10^6 Ω/m
Therefore, the ideal resistivity per meter of a carbon filament light bulb is approximately 8.75 × 10^6 Ω/m.”
Well, I asked what would be the energy required to make the air detonation in order to generate 1000kg of thrust, and it said I would need around 1 trillion joules. :|
So much work for nothing I guess…
Actually, no.
I searched for the 1000kg thrust sugar rocket and took its weight (45 kg), energy density (17 MJ/kg) and the amount of time it keep flying (30 seconds) and it resulted in 25.5 megajoules.
So I “just” need to double or triple the energy output of said laser assuming the infrared laser has a 90% efficiency of converting electricity to emission, 90% of efficiency in converting the emission into an explosion and 90% of that explosion being converted into thrust.
If you need this little energy to make 1000kg of thrust, why then use legs? lol
Out of curiosity, a 50.cal BMG bullet has 10 kilojoules of energy. So this is not just blindingly dangerous, but super dangerous.
Out of curiosity², a tank gun (120mm) armor-piercing round has around 25 megajoules of kinetic energy.
The national ignition facility’s laser used for Laser Inertial Fusion reactor has 3 megajoules of power, while 1kg of TNT has 4 megajoules.
Of course, it is not that simple, a pulsed laser can divide all of that absurd energy between multiple sources and lenses without damaging the system, the National Ignition Facility delivers ALL of the 3 megajoules of power in a single millisecond pulse.
If achieving a 10 kilojoule laser was that easy… Wouldn’t it be even easier to make a 3 megajoule laser?
That is why I think I’m talking out of my ass.
By the way, I was looking for a 10 megajoule capacitor bank, it is the size of a entire room:
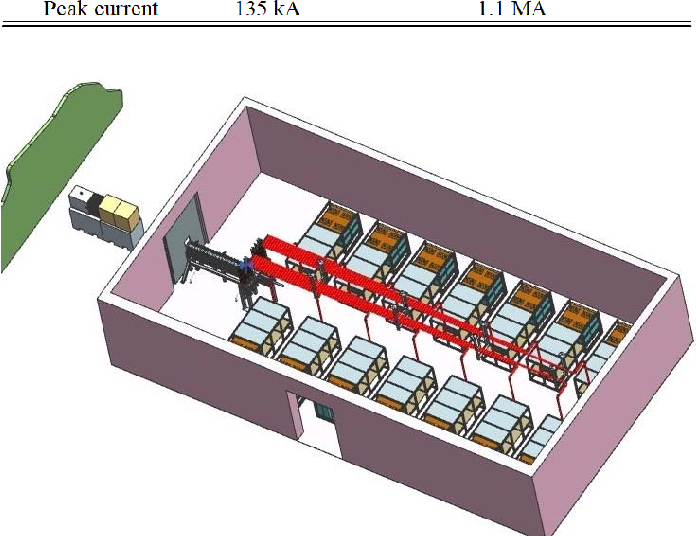
It is insane to think that gasoline has 4 times that energy in a single liter.
Also, the fusion was done using UV lasers with 2 megajoules in total for the fusion shot, it uses 100 times more energy because it is only 1% efficient, and the pulse duration is 1 nanosecond. I was searching and it seems like they use gold capsules for the fuel so it transforms the UV lasers into X-rays, huh.
“According to the search results, the conversion efficiency from the laser energy to x-rays in the National Ignition Facility (NIF) is around 15%:
The NIF laser generates 3 MJ of infrared laser energy, of which about 1.5 MJ remains after conversion to UV light. [1]
Another 15% of the UV light is then lost in the hohlraum (the metal cylinder surrounding the target capsule). [1]
This means that about 15% of the resulting UV light, around 150 kJ, is absorbed by the target's outer layers and converted into x-rays. [1]
So in summary, the NIF's UV lasers have a conversion efficiency of around 15% to x-rays that are then used to drive the implosion of the fusion target.“
I looked on google and if one day they actually make a inertial confinement fusion reactor that doesn’t use lasers with shitty 1% efficiency, they intend on making from 1 to 10 shots per second, so, around 1 to 10 megajoules per second, which would generate 10,000,000 watts in a hour.
Just a post-note: the pellets cost millions of dollars because they are made with super-ultra-duper-mega precision in order to make the fusion occur efficiently.
There are other approaches to inertial confinement fusion, like magneto-inertial fusion, which literally uses plasma railguns to shoot the magnetized target, resulting in an explosion without all the insane requirements for the laser type.

Source: https://www.researchgate.net/publication/284228265_Magneto-Inertial_Fusion
But the problem as everything else is tests and data, the National Ignition Facility was built in 1993 and only in 2022 it was able to generate fusion. Around 30 years of testing and development in order to just get that result.
Now think about all of these crazy fusion reactor concepts around the world/internet, how many of those are going to have millions of dollars invested in them? And if they do, will they live long enough to generate results? How many of the ones that lived long enough are going to be practical or even efficient?
I asked WebGPT and you could indeed suspend individual electrons in a magnetic field and once the magnetic field is deactivated, if they end up hitting an electrode, they would indeed make an electrical current through the system.
Wouldn’t that mean that you could use this system as some kind of capacitor? A super high density capacitor?
Well, this thing is essentially a particle accelerator and you would need a really, really strong magnetic field. In fact, equally proportional to the force of the electrons, because they would have the same charge and repel each other.
But I do wonder: would the increased speed of the electrons cause more charge? If so, wouldn’t it be possible to trap just a few electrons on a permanent magnet field in a vacuum? I just now remembered that electrons/particle accelerators need much more energy to make the electrons/particles to curve, that is why the bigger the particle accelerator the better. On such a note, I do wonder if instead of hitting an electrode, the electromagnetic field would contain the electrons spinning and once the electromagnetic field collapses, all those electrons start pushing against the field, generating a current…
Would I even need electrons for that though? The collapsing field would generate a ton of eddy current anyway and it would work just like a capacitor.
That is just an inductor. I’m stupid. lol
From what I readed only, the inductor outputs most of its energy in a high voltage pulse, while the capacitor outputs most of its energy in a high amperage pulse.
A Flywheel would be better than the capacitors and inductors
There are also explosive pulsed power generators, these use high explosives and the like. But I was wondering if you could use low-explosives like a gasoline/hydrolisis powered shock turbes or pulsed detonation engine or "just" compressed air.
But in both cases, I think flywheel may be the safest option.
Hackaday has a page about that: https://hackaday.com/2017/01/11/pulsed-power-and-its-applications/
Just now I remembered that if you add drops of water into liquid aluminium, the water will turn into steam so fast it can actually cause an explosion with the same power as C4.
It is just like droping water into boiling oil.
I say this, because if you control the amount of mass of liquid aluminium and water, you could have a "rechargeable explosive" for the explosive pulsed power generator.
Needless to say: don't try this at home.
... Wait a minute. If you can generate such strong explosion, wouldn't that mean that you could make a inertial confinment fusion reactor that uses this steam-liquid metal explosion to reach the same explosion the laser fusion does, but without the laser part?
But if it all these ideas were so easy to make, then why no one made them?
What I'm missing?
By the way, although I don't have the money to buy synthetic Ruby laser rods, it seems like you can "just" take neodymium oxide and/or yttrium oxide and mix with phosphate glass in order to make a gain medium for near infrared or short infrared lasers.
You can also use silicate glass for this, meaning you can literally "just" melt both in order to create it. Although I don't know if it would work with sodium silicate.
Discussions
Become a Hackaday.io Member
Create an account to leave a comment. Already have an account? Log In.
interesting discussions here, if you ever make a non-mech related blog i would follow it, also regarding that last question, a lot of projects you proposed seems very expensive to implement properly, considering most labs do not make their own equipment.
Btw that laser propulsion demonstration is very interesting, just being able to deliver payloads beyond the karman line would be good, and that should be possible using an IR laser from earth pointing at the payload, no need for the laser to be on board the spacecraft. There is a specific wavelength of IR that goes through the atmosphere with minimal interaction, perhaps a fluorescent coating on the spacecraft can convert the IR into higher frequency light, this way a lot of energy will reach the spacecraft and you can get away with cheaper lasers.
Also beyond the atmosphere the spacecraft would act more like a solar sail, no?
Are you sure? yes | no
"Also beyond the atmosphere the spacecraft would act more like a solar sail, no?"
Yeah, that is the idea of most laser propulsion systems with stationary laser sources like you proposed.
Are you sure? yes | no