Tuesday, 12:03, 07/03/2023
Edit⁵:
As I said on the "Edit⁴" down bellow, I'm still calculating the idea of heating the gases compressed by the pneumaatic compressors, because when you heat a gas, it expands, so one could make a pneumatic compressorless that works by only heating gas.
But, I will say upfront that:
I calculated the stuff even more, with more alternatives, and even if I made composite casted hydraulic pumps, it wouldn't be enough.
The more I calculate the mechanical disadvantages of the humanoid body, the more force I need to make the sui move, and the more force I need, the more energy I need to input in the system.
And last time I tried to calculate stuff, I would need around 30 pumps and using just around 228 muscles.
Edit 7:
By the way, I decided to stick to the centrifugal water pump. Those are relatively cheap and can achieve 500 liters per minute with 8-9 bars of pressure.

The ones I saw were more like this one, but I'm kinda afraid of buying through the internet because I don't know how the centrifugal blades are.
For example, if thos have inlets, I don't think I will be able to make a casted copy of them, only a negative casting of a 3D printed one.
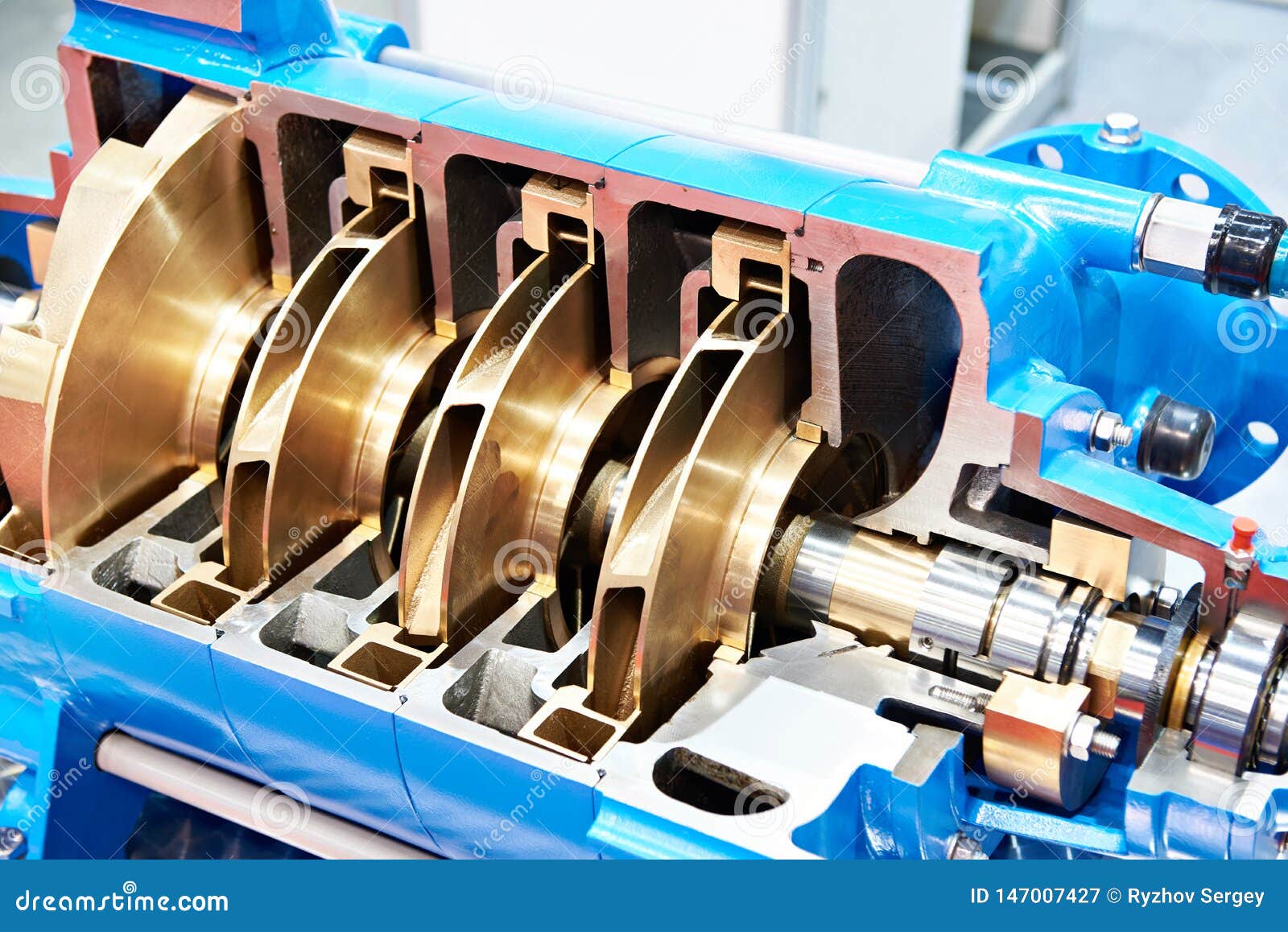
For each, I would only need 2-3 horsepower, and since I came to the conclusion that I would only need around 3-4 of those and 6-9 horsepower engines, which are relatively "cheap" (if you're not broke like me) and sold as landmower or kart engines.

Normally these cost around 1000 reais (+/-200 dollars) to 3000 reais (+/-600 or even 900 dollars).
Now the other headache is finding out how much power I will need for the servo-valves and if those would be strong/fast enough for the exosuit.
And you know that thing I said: "the lower part of the body needs to be 3 times stronger than the top half"?
So...
I was measuring the mechanical lever advantages and disadvantages of the body, and that is almost... Not enough.
Assuming that I have 9 to 10 1 inch diameter McKibben muscles giving 900-1000 kg of force on a mechanical lever with 20cm in length, and assuming (I actually measured) my leg has 90cm of length, if I were to push the entire leg, I would only achieve 100-200 kg.
Luckly, I have two muscles doing this same move.

Illustration showing what I described above.
Just pretend the grey lines are muscles, the blue lines are the exosuit and the orange point is the pivot/axis of this lever.
As you can imagine: "How can the thighs rotate with the muscles blocking its way?"
And the answer is: I don't know just yet >.>
Anyway, this means that even though I inputed 1 ton of force, it wouldn't be enough, so I would need 3 times the already 3 times stronger muscles that are already 3 times stronger than the upper body.
Meaning I would need to put 27 muslces per bundle on the legs...
Which actually gives me an idea on how stronger our bodies are, 1 ton McKibben artificial muscles moving at a third of a second and our body can still out-maneuver and out-strength these. 🤯
Edit³:
By the way, the amount of watts necessary was around 20-22 hp (16000 watts per hour) for every way I tried to calculate this.
Pneumatics, hydraulics, electromagnetism etc.
This means that, no matter what the heck I do, this is the exact same value I stumble across every time I calculate how much power I would need to run this exosuit/mechsuit.
I guess that this is the minimal energy required to make this crap to work, and no matter what approach I take, I can't run from physics itself.
That should give an interesting perspective on the subject.
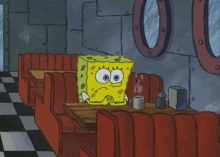
So... No matter what I use, direct electricity, hydraulics, pneumatics, it always come to this value...
Then, instead of fighting physics itself, I think I should seek the most simple and effective approach to this problem, no?
I was thinking of hydraulics because it is the safest one.
Pneumatics are a little cheaper than hydraulics, but those can explode and are noisy.
Electromagnetism is quiet and effecient, but is costly and can electrocute you to d*ath.
Hydraulics are just water/oil flowing, then why not I guess?
Edit 8:
I actually gave another try on calculating the Nylon/Polyethylene muscles, and more or less, I would need hundreds of kilometers of nylon lines in order to make something useful.

Some pictures of Nylon actuators.
The last time I calculated, I needed around 30-40 kg of nylon/polyethylene lines.
And don't even start me on how one would wind all these hundreds of kilometers on spirals, nor how much heating wire one would need to heat the muscles. lol
The only possible material for artificial muscles that *could* be light and efficient that require less energy would be carbon nanotubes.
I mean, I THINK.
I don't even actually know how much energy these carbon nanotubes would need and how strong they would actually be.
Unlike told in the video, carbon nanotubes are a fricking headache to make.
I actually contacted my old chemistry teachers (that are professionals on the field of chemistry-related "stuff", like petroleum refinement), and they said they would give me a hand on how to not k*ll myself while synthesizing carbon nanotubes, but never said anything ever since. :/
But... You know, Acetylene is explosive, flamable and toxic (I think it is toxic).
Acetylene is quite cheap to make/buy, the vacuum deposition step for the tungsten plate is also cheap and easy to do by hand.
The problem is the furnace, the explosion and combustion threat.
You see, Acetylene combusts at 2200 ºC, enough to melt tungsten. :|
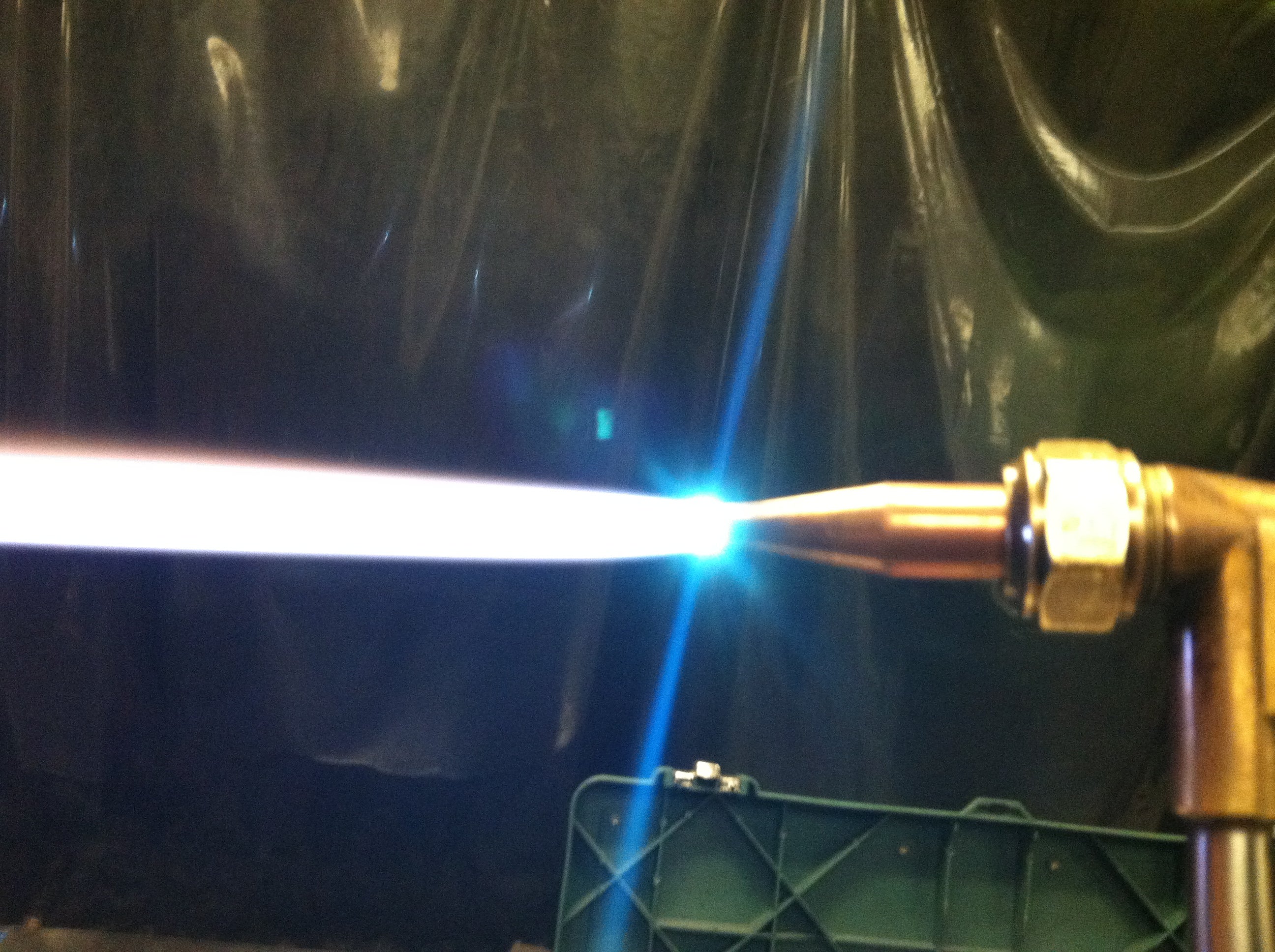
Actually, I sometimes wonder if I just enjoy making these Project Logs and the idea of Mechs more than the actual act of building mechs and finishing this project. Hum... 🤔
Because, just like I said on the project description: mechs aren't viable, and if there was a "trick" to actually make those to work, mechs would be a common thing among us already.
Edit²:
I was researching a little bit about pneumatic systems/pumps and so on, however, a single 30 liter compressed air tank would be enough to power the entire exosuit for about a minute.
The problem is that these pumps normally take around 1-3 minutes to fill this 30 liter tank at 8 bars...
So Pneumatics wasn't on the table...

... However... While I was researching for parts and other kinds of pumps and fluids to work with, I came across an old video that may or may not be useful.
Basically, this guy made an hydrolysis machine that breaks down water into oxygen and hydrogen gas and uses the gases generated to power up pneumatic McKibben muscles.
So he doesn't need a compressor.
I "asked around" like I always do, and got the answer that a cylinder with 300mm (30cm) in length and 10mm (1cm) in diameter would be able to hold 0,032 liters of Hydrogen gas pressurized at 8 bars (other answers said that I would only need 0.025 per muscle).
And well, since compressed air tends to expand, I would assume that the muscle would stay at 4-6 bars of pressure when contracted (but I can just double the amount of hydrogen generators and maybe double the amount of pressure...?).
Well, meaning that an electrolysis device can be used to produce the gas on the pneumatic muscle, and I would need around 4 liters of hydrogen at 8 bars in total...
Which means I would need 8 times more hydrogen/oxygen in order to compress it to 8 bars...
Meaning that I would need around 32 liters per minute.
And since the hydrolysis generators can produce only 1 liter per minute... I would need 32 of those 500 bucks things... That consume 400w each...
Ok. I didn't think this through. :|
I thought I was onto something interesting...
... But no...
Edit⁴:
GASES EXPAND WHEN HEATED.
I don't need 8 times the amount of generators, I just need to heat the gases to 8 times the amount of room temperature!
Actually, I could even heat it up to 8 times or 16 times and just have two HHO generators or pneumatic compressors.
But like I said, I would still need the same amount of energy (or more) to heat it up, which wouldn't change much the energy consumed.
Heaters aren't that efficient either, specially the induction heaters. Those usually need 3000 watts to work.
However, this also mean I would have to carry less weight to power the exosuit/mechsuit, after all, the 30 liter cylinder from pneumatic compressors can weight around 40kg, the hydraulic pumps can weight around 10kg per pump (yes, even the smaller ones).
And there are some problems that I didn't mention:
I would need special heat resistant braided sleeves and heat resistant inner bladders.
However², I could use the expanded gases to power a homemade air-driven hydraulic piston pump! So I wouldn't need to worry about braided sleeves and bladders melting up.
However³, I need to find out how much pressure/force these piston hydraulic pump would need to pump the hydraulic fluid to 8 bars and how much the gas will increase its pressure based on its temperature.
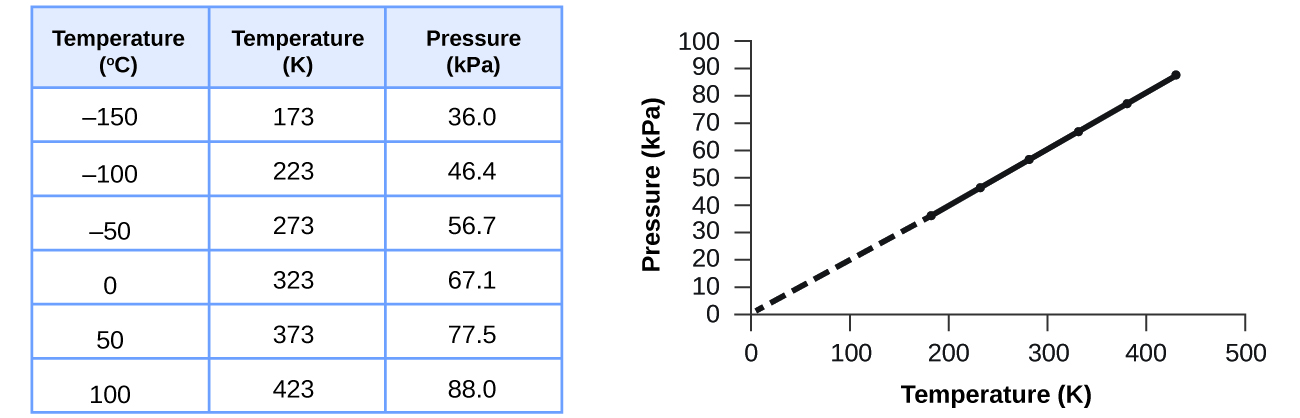
This is a graphic showing pressure of ideal gas based on its temperature.
Accordingly to this graph, the increase in temperature is somewhat linear to its temperature.
So, if I wanted to pressurise a gas to 800 kPa (8 bars), I would need (based on the graph that is not quite as truthful to reality) around 1000 degrees Celsius to achieve 8.8 bars.
I'm bad at math, but for some reason, when I multiply the 100 ºC by 10, it gives 1270 Kelvin, but when I multiply the 500 kelvin value by 10, I get 4700 ºC. :|
So... I need to heat a flamable gas to temperatures between 1000 to 4000 ºC.
How much energy to I need to do this again?
Edit ⁶:
That's not it guys...
The 30cm long, 10mm (1cm) diameter McKibben artificial muscle has a volume of 0.02 liters or 23.56 cm³ in volume.
A combustion piston is about 100mm in diameter and has 50mm of travel, i.e. a volume of 0.39 liters or 392.70cm³.
In the case of the first, it has 0.032 liters of hydrogen pressurized to 8 bars, that is, 8 times what it would normally fit.
At ambient pressure, 0.39 liters of hydrogen would fit inside of the piston.
Heated 8 or 10 times more: 3.07 liters of hydrogen.
Since each time hydrogen enters the piston, it expands, and then needs to be pushed out after expansion, I need 3000 RPM to reach 1179 liters per minute.
That means it's 50 rotations per second.
That is, one rotation in 1/50 of a second.
One full rotation (going up and down) 0.02 times per second.
That means I would need to fill the piston chamber 0.02 times per second.
Since I need 0.39 liters before heating it per revolution, I would need 1170 liters of hydrogen per minute...
Ok that is also not it.
Yes, I could also "just" heat it up even more, but we are already in the 1000 ºC of temperature.
Edit¹:
I should just use a common water centrifugal pump instead of using hydraulic oil...
I just started this "hydraulics craze" of mine just because I wanted a proportional pump using electromagnets instead of servo valves. :|
These centrifugal pumps are cheaper, use less energy and can achieve insane fluid flows.
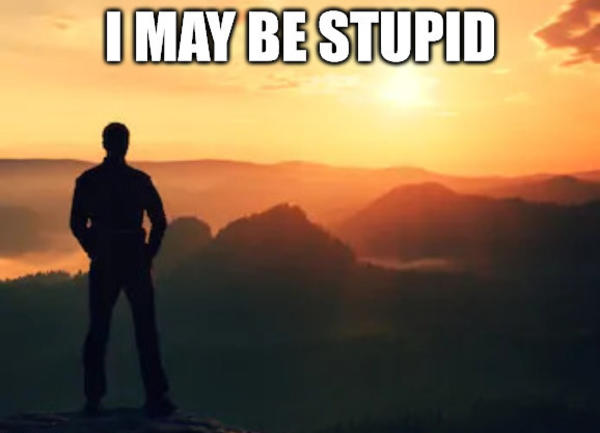
Good morning, good afternoon or good night.
So... I gave it some thought after my mood was kinda gloomy after the last Project Logs and I think I should give another try for the hydraulic pumps.
As you may know, hydraulic pumps are expensive as f-ck, around 500+ reais (100 dollars), and anything that reaches closer to 150 liters per minute costs around 4000-9000 reais (700-1700 dollars).
And on top of that, these pumps are meant for incredible high power output, something in the house of 300-700 bars of pressure.
And because of that, these pumps weights around 10 to more than 40kg (I've seen one that weighted around 500 kg).
However, I just need, at maximum, 8 bars of pressure.
And if I wasn't clear enough for how much power those piston pumps made out of car piston engines, let me explain:
The problem with those pumps is that those are pistons.
You know, the same kind of piston that goes at the end of those hydraulic pumps.
So, when it reaches a certain pressure, let's say 8 bars, the resistance it suffers is the same as if it was a hydraulic cylinder piston.
Basically, if you enter a certain amount of fluid with 8 bars of pressure in a piston with a certain diameter, it lifts around X weight (like 1 ton).
So, if you want to make the piston to pump hydraulic fluid instead, what you're going is pushing against 1 ton hydraulic cylinder, and you need to overcome that 1 ton of force in order to pump.
Unlike the gear pump, that goes little by little, but at at greater speeds.
So, taking into consideration that I just need 8 bars of pressure and I don't really need something super resilient, I thought on using 3D printed pumps.
For example, this guy made a 3D printed pressure washer...
... That works like crap (and he himself said that this project was a waste of time at the end, lol).
So I also discarded this idea for some time, because:
- Plastic is fragile and maleable.
- 3D printed plastic is even more fragile and maleable.
- I know that the pump will work, the problem is: for how long? It is just plastic.
But a friend of mine (thanks Alisson) actually gave a great idea: metal casting.
The idea would take some low melting point metal and cast it in a 3D printed mold/negative mold.
I mean, it is not like it will be that precise, nor that strong, but I don't really this think to be 1 ton strong, just strong enough.
Until now I can only think of Tin, Copper and Aluminium.
Some hydraulic pumps are actually made out of aluminium, a lot of aluminium, but still aluminium.
But I could use something else:
Forged carbon fiber and/or glass fiber (or even resistant resin by itself).
Of course, those wouldn't be as strong as the properly made carbon fiber/glass fiber objects out there, but these will be good enough and cheap enough to make at home.
Still, I don't think that a 3D printed part will have enough precision for these hydraulic pumps to be printed in a good enough quality/precision/margin of error.
I think the best way to do this would be to buy actual (and cheap) hydraulic pumps and make a silicon rubber mold out of those.
And yes, silicon molds can even copy stuff with microns of precision.
Of course, this video bellow is a good start to understand how gear pumps work:
Again, I will take a while to make some money so I can buy the stuff needed for this project.
Until then, I will continue to study about the subject and I won't be creating Project Logs any time soon.
(this time is serious, I swear y-y)
Discussions
Become a Hackaday.io Member
Create an account to leave a comment. Already have an account? Log In.