Thursday, 27/07/2023, 10:48.
Well, I will just post this here, but I will keep editing later (I can barely edit anymore because I already wrote so much stuff).
Just because It would be of great help if someone were to give suggestions.
Even though I stuffed this project log with options, I'm still divided between hydraulics and the hoist mechanism.
Hydraulics are a proven design in the real world and it has a lot of information on the subject, but it needs a lot of precision to avoid leaks. Precision that I may or may not be able to achieve in a DIY setup.
I asked online if making high precision hydraulics using molds would be realistically, people answered that cylinder fail can lead to death and on top of that, casted parts need furthuer machining to meed required tolerances (PS: I don't know what are th required tolerances).
The hoist linear mechanism is cheap and easy to make, but it doesn't have a proven design/example on the real world, and thus, I can't find a proper way of calculating its efficiency, and even if the efficiency was to be good, I still don't know how long its mechanical pieces would last...
We are talking about 3000kg of force/weight being deposited in a DIY mechanical system, an hydraulic one would take the force easily, but a mechanical one...
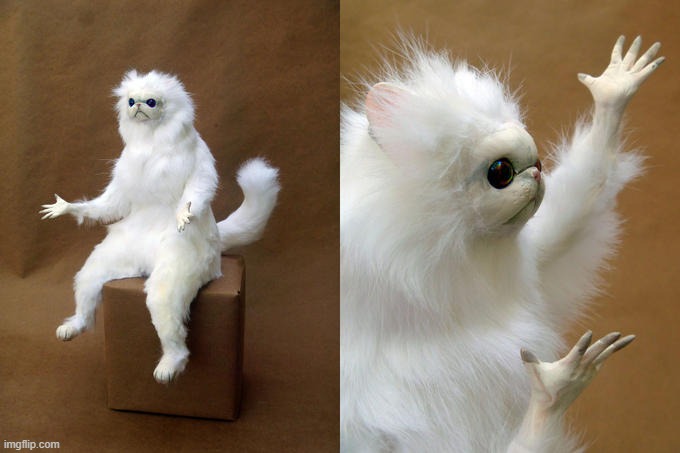
What do I do now?
----------------------------------------------------------------------------------------------------------------------------------
Well, there was a giant text here talking a myriad of things about linear actuators, but in the end it was the same problem that I always make with my project logs: I keep posting random ideas and random videos that I found and I never actually finish the actual 3D model that I'm supposed to do.
I will try to 3D model something similar to this, then, later I will try to make a telescopic actuator.
---------------------------------------------------------------------------------------------------------------------------------
One thing that is kinda chipping off my mind is the twisting motions that the linear motor would suffer under loads, this is already a significant problem for conventional linear motors, now imagine a telescopic one, were each part would be support by a little bit of contact metal.
How do I avoid such thing? I am overthinking its impacts on the structure? After all, everything will be in a stewart platform with universal joints, and on top of it, all the objects would have at least 10mm of thickness for extra resilience...
I was actually thinking on make something akin to this, but with hoists instead of a belt drive, since belt drives aren't meant for high torque appliactions.
Also, I was wondering if scissor actuators would be a good choice... They are even more compact than telescopic actuators, and quite simple aswell...

This circular scissor mechanism actuates by rotating one of the two plates at the bottom and/or at the top, increasing or decreasing the angle between the scissor linkages.
Althought I think it is an incredible type of mechanism, I don't really know if it faces the same problems as conventional scissor mechanisms (explained in the paragraph bellow) or if it is simply too complex.
Source: http://robotics.estec.esa.int/ASTRA/Astra2006/Papers/ASTRA2006-2.3.1.01.pdf
I was seriously giving this mechanism a thought, since after messing with an online calculator, I found out that the bigger the amount of degrees (past 45º), the less force you need to lift/ push the load.
However, bellow 45º angle, the more and more force you need to apply in order to lift something, for example, at 5º I would need 35 tons of force to lift 3 tons.
It would only be an efficient option if the device were designed to stay at the start at 45º.
Maybe this is a solution?
Of course, just replace the weird looking disk with a linear actuator.
I couldn't find any information on the subject, but I would guess that it has a relation between torque and linear speed similar to a gear ratio, after all, for every unit of distance you input, it multiplies accordingly to the number of stages, and thus, I would guess that the torque/force is divided by the number of stages also.
I only came to this conclusion because if it wasn't like this, then I would be basically creating energy out of thin air. And that is not possible.
The relation between travel distance and force must have some kind of affect on the mechanism.
I asked around and my suspicion was correct, I received some answers stating that the amount of stages proportionally increases the amount of torque required for lifting the load in this configuration, just like the linear distance increases proportionally to the number of stages.
... Although, even with this limitation, I do think it could be a really great actuator for this specific case of a mech/exosuit.
Simply put, I need something close to a telescopic actuator, and all types of telescopic actuators need to be connected with smaller and smaller sections that only increases the weakenesses of the overrall mechanism.
But with a scissor mechanism, on the other hand, I could achieve way bigger lengths without the need for sub-sections... Such mechanism would be able to double and/or even triplicate its length.
The only problem is exactly the initial torque/force required to make it "break" the inital resistance.
... I thought on using spring compensators, but the weight you would need to compensate for would be in the tens of tons...
Also, I was kinda considering electrohydraulic actuators.
I was skeptical of how well I would make the hydraulic system if every actuator were an hydraulic cylinder because of chances of leakeages and loss of efficiency at the hoses and so on.
But I think that using actual electro-hydraulic actuators in which the pump would be directly connected to the cylinders would be way simpler and better overrall.
I mean, an hydraulic cylinder has 95% of efficiency and a hydraulic gear pump has 70% to 90%, with less energy/torque requirements for lower pressures.
The gear pumps in the market can achieve up to 30-40 liters per minute at 1000-1750 rpm and each actuator would need around 10 to 15 liters per minute individually at more or less 100 bar, if you decrease the bar to half and increase the bore diameter, you would need more fluid, but way less torque.
Although it doesn't sound intuitive to replace a mechanical actuator to a hydraulic actuator, you're simply changing the wear and tear of solid metal to an oil.
You would still need to take care of gaskets/seals throughout the armature tho...
Chat GPT and the tolerances in Hydraulic Cylinders:
"The tolerances or margins of error in hydraulic cylinders can vary based on the specific application, manufacturing processes, and quality standards. However, I can provide you with a general guideline on what tolerances might typically be expected for hydraulic cylinders with output forces ranging from 1 to 5 tons (approximately 9.8 kN to 49 kN) in metric units:
Straightness and Alignment: The cylinder's piston rod should be straight and aligned with the cylinder bore. Tolerances for straightness are often expressed in micrometers per meter (μm/m). Common tolerances might be around ±50 μm/m to ±100 μm/m. Cylinder Bore Diameter: The bore diameter of the cylinder needs to be within specified limits to ensure proper sealing and performance. Tolerances might be in the range of ±0.1 mm to ±0.3 mm. Piston Rod Diameter: Similar to the bore, the piston rod diameter needs to be controlled for proper sealing and strength. Tolerances might be in the range of ±0.1 mm to ±0.3 mm. Piston Rod Runout: Runout refers to any wobbling or eccentricity of the piston rod as it moves in and out of the cylinder. Tolerances might be in the range of ±0.05 mm to ±0.1 mm. Sealing and Leakage: Hydraulic cylinders need to maintain proper sealing to prevent fluid leakage. The tolerance for acceptable leakage rates will depend on the application and specific requirements. Surface Finish: The surface finish of the cylinder bore and piston rod can impact sealing and friction. Surface finish tolerances might be in the range of Ra 0.4 μm to Ra 0.8 μm. Pressure Rating: The cylinder should be able to handle the specified pressure without failure. This isn't exactly a tolerance but an important consideration for hydraulic systems. It's important to note that these tolerances are general guidelines and can vary depending on factors such as the intended use of the cylinder, manufacturing methods, quality standards, and the specific manufacturer's practices. When designing or purchasing hydraulic cylinders, it's advisable to consult with the manufacturer or supplier to understand the exact tolerances they adhere to for the desired output force range.
Micrometers (μm) and micrometers per meter (μm/m) are units of measurement commonly used in precision engineering and manufacturing to express very small distances or changes in dimension.
1 micrometer (μm) is equal to 0.001 millimeters (mm), or in other words, 1 μm = 0.001 mm.
Micrometers per meter (μm/m) is a measure of how much a dimension changes over a certain distance. It represents the change in micrometers for every meter of length. So, if you have a tolerance of ±50 μm/m on a dimension, it means that for every meter of length, the dimension can deviate by up to 50 micrometers in either direction.
For example, if you have a straightness tolerance of ±50 μm/m on a piston rod that is 1 meter long, it means that the end of the rod could deviate up to 50 micrometers from a perfectly straight line over the entire length of the rod."
... Crap, I'm doing it again...
---------------------------------------------------------------------------------------------------------------------------------
Well, although I gave up on screw actuators before, I still think it is a good bet to make taking into consideration the amount of weight the actuator will be under.
When it comes to high loads, you have very limited options that allows for high efficiency and high force output (as far as I could find, I may be wrong).
Now, for the linear screw actuator, I will make a linear one on blender that also allows for bearings.
Basically, there is a "Screw" effect built on blender, and I will try to make it the same way one would make slew bearings.
Basically, a roller bearing with the same amount of diameter and height, so it more or less fit inside a square.
In this video it shows how it works with ball bearings, but I don't know if it would work for roller bearings...
Better stick to what it already works...
For some weird reason, I had an idea for an equally weird mechanism.
Basically, I was thinking on a mechanical replacement for a hydraulic actuator, so I thought: "Hydraulics are about moving liquid stuff under solid stuff, so why not just use bearings?".
So the idea was to "just" use a sprocket mechanism were ball bearings would fill the space between the sprocket's teeths, filling up the space between the hydraulic champers without the need to high precision/high resilience seals.
I could even use hoses for feeding up the bearings.
But you know, such mechanism just sound proposterous.
But I only thought of that because of the ball screw actuator, simply because I thought it would be easier to make the bearings move instead of the entire thing.
... But as you could guess, I don't know how to calculate the ins and out of such thing.
Well, I also thought on trying to make the screw actuator itself with a reduction ratio of 10:1.
The mathematics elude me, but I know that 30 RPM equals to 0.5 rotation per second, and thus, since I want 15cm per second of linear speed, I would make an spiral that would take 5 rotations per second (0.5 RPS x 10 = 5 RPS, 5 RPS x 60 = 300 RPM) in a 15cm tall and 10cm wide cylinder.
So, with 300 rpm, the output would be 30 rpm and the torque 10 times greater.
Although I don't know how well this logic proceeds.

I've made it on blender, and funnily enough, it lefts enough space for giant bearings, which I could make buy a single unit and make molds from it.

By the way, I didn't explain it very well, but basically, you just create a circle and add the modifier, the spring will be made.
That's why it is quite easy to make the profile just like in the video in the beginning, even by an idiot like me.
Then I will "just" make the boolean modifier to "carve" the shape in the cylinder in order to make a screw.
---------------------------------------------------------------------------------------------------------------------------------
No matter how much I hink about the subject, I simply can't reach a conclusion. I just don't know what to do, how to proceed and so on.
All alternatives sound really good and I don't know which type I should try out...
Screw linear actuators? Hoist driven linear actuators? Scissor acuators? Hydraulics? Pinion and Racks?
The Screw linear actuator looks really sturdy and resilient, but I don't know if it will be good enough, if it will have too much friction or any other problems...
The hoist/belt driven linear actuator looks like it is the fastest and the easiest to make a telescoping version, but I don't know its efficiency and how well it would actually handle the loads. The armature could be thicker and stronger, but how well it would endure in the long run?
Scissor actuators look way simpler to build and maintain, but I don't know if it would be the best choice...
Hydraulics are simpler, but not easier to build, they need a lot of precision and I don't know what would be its efficiency.
Pinions and Racks are the most (supposedly) efficient option, but I don't know how well these would survive loads from 500kg to 3 tons...
Oh yeah, I forgot about this detail also... The actuators on the arms would be only under maximum 1000kg, but the legs would be suffering 3 times more (or even beyond that, assuming the mech/exosuit jumps and/or falls).
Well... I would guess that the hoist driven is the winner, I suppose, I doubt the screw actuator would be back-driveable and/or even be good with impacts...
---------------------------------------------------------------------------------------------------------------------------------
Well, assuming that the final result would be a cylinder with 10-20cm of diameter and 15cm of height made out of solid aluminium (which won't), it would weight 3 to 13 kg each (10cm diameter to 20cm diameter).
Giving a total of 30 actuators out of these, and you would have a 99kg or 390kg of weight in total.
With the iron-air battery that weights around 200kg, it would already reach 300kg, with the "pilot" with 80 to 100kg, 400kg. lol
---------------------------------------------------------------------------------------------------------------------------------
Why I'm even fricking out this much?
I just said that a 5 ton hydraulic cylinder has a thickness of 1cm. I just need to double or triple the thickness of every part in order to stay within aluminium's strength and achieve the same results.
And I say "just" double the thickness because of this video:
My brain just needs to work properly...
Well, guess what? My brain is not working properly, but I've made a sketch. A crappy one.

So, each sketch is a possible way of making the linear hoist actuator.
The first one from the left to the right is if every hoist is connected to a single shaft supported by bearings, the pulley wheels on the top, at the side of the rod are responsible for the pushing motion of the actuator, but these are merely for redirectioning the motion of the base hoist.
Although in every version, the center wheel is responsible for pulling the linear actuator back to the base.
On the second/middle, the sequence of hoists are connected by hoists instead of transmission gears or a single shaft. This idea makes me doubt the efficiency of transmission of the hoists and may lead to inconsistent loads.
The third, on the right, is the actuator that I first imagined and the reason why I was so doubtful of the hoist actuator, simply because the hoists responsible for the pushing motion aren't centered and on top of that, need two pulley wheels for redirectioning the load/motion.
And as you can guess, it is just an overcomplicated version of the first sketch on the left.
That's the reason why you draw sketches of your idea before actually making a 3D of it, but, as you can guess, I'm not very smort.
---------------------------------------------------------------------------------------------------------------------------------
About the speed of actuation required to a human-like motion of 30 rpm:
Let's remember that each actuator will be at one third of the length of the limb, meaning that I will lose 3 times the torque and increase the speed for 3 times.
Mechanical advantage of a lever is kind like a gearbox.
Meaning that even though the linear speed is 15cm per second, the speed of the entire limb will be different.
So, if we take a RPM to linear speed calculator and just insert the triple of 15cm per second, 45cm/s, we would achieve an rpm of around 14 rpm, meaning that we "only" have to input twice the initial value.
Meaning that each part would "just" need 12 horsepower instead of 6 or 5, giving 36 horsepower in total for the entire thing instead of 189hp.
Meaning² that the 200 kw iron-air battery will last for around 7 hours instead of 10.
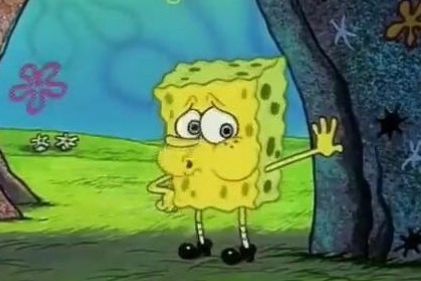
---------------------------------------------------------------------------------------------------------------------------------
Well, in any way, I think I will be going on with the electro-hydraulic idea simply because I think it will be the easier to find information about.
I mean, the most promising idea is the linear hoist mechanism for its simplicity, but I can't find the actual efficiency of such system for the life of me.
In any case, even though I gave up on hydraulic piston pumps before, I do believe that I was thinking of those in the incorrect manner.
Basically, the bigger the area of the piston, the more force needs to be applied to the thing.
So, the "ideal" hydraulic piston pump would be to make those really thin and move really fast.

For example, a piston with 50mm (5cm) of diameter would need to fight the force of the fluid at 100 bar, which would be applying the equivalent of around 2000kg of force.
However, a piston pump with 10mm (1cm) of diameter would only face a resistance of around 80kg at the same 100 bar of pressure.
I would need to make this piston pump to rotate with around 40 Nm of torque (which is really close to gear pumps I can find on the market) at 1000 RPM (4kw or 5hp), a single piston would achieve around 8 liters per minute, but if I make a multiple piston pump of 5 piston heads, I would achieve around 40 liters per minute.
However, with that I create another problem: now multiple pistons will also be under force in order to make the fluid to flow.
Assuming that "just" 3 of those pistons were being pushed in order to pump, I would need around 120 Nm of torque (3 times more), meaning that now I'm at 12kw or 16hp.
Of course, there are some caveats to this.
I'm assuming that the piston has a radial crankshaft in which every piston is attached to a distance of more or less 5cm from the center, meaning that I need more torque and less speed, but if I were to change such distance or the configuration of such displacement, I could change the requirements.
Of course, tripling the RPM instead of the torque will still give 12kw/16hp, but that is in a radial configuration.
I didn't think of a conventional axial configuration because it needs really high tolerances.

An axial piston pump separates the high pressure from the lower pressure side only using a low tolerance flat plate, which I'm dobtful I would be able to replicate in a DIY setup.
However, I could try the wobbling version:
However, I don't quite like the wobbling of the plate itself, but I think I got a better version:
This engine is kinda like a wobbling plate, but without the complicated bearing for the wobbling plate.
And if you didn't watch the video from the guy, basically, he says (while showing details from the video) that this kind of combustion engine has poor torque at lower speeds because of the lack of mechanical advantage, which is great for a pump to win the force of the pressure.
The only problem that I know of is that this kind of mechanism needs the wobbling disk to have a fixated diameter, or else the bearings will be forced against a fairly narrow wave, which can wear down the surfaces.
This guy made a bycicle like this and he mentions it:
By the way, I forgot to talk about the efficiency of the hydraulic piston pump.
In resume, if I would need a 60 rpm disk with 10cm of diameter, I would need 1500 Nm of torque, which would be around 12 horsepower or 9,000 watts.
But as you could see in the final result I previously talked about, I would need a hydraulic pump that uses 1000 rpm and around 120 Nm of torque, giving a final potency of 16 Horsepowr or 12,000 watts.
This means that this hyphotetical pump loses around 34% of efficiency, giving a total of around 66% of efficiency.
I know that the 9000 watts is the theoretical maximum efficiency, and nothing is 100% efficient, but this is quite disapointing to me, to be honest.
Even with the weird plate pump, I still think the final result won't change much.
Besides, we are not even counting the inneficiencies of the electric motor or the real inneficiencies of the final thing, with its seals and tolerances that I may or may not mess up.
Also, I don't know if such statement would be true or not, after all, radial pumps are said to be 95% efficient and axial pumps 90% in general (for some reason the source is on the citations).
The hydraulic gear pumps also have a similar problem as in the axial piston pump in which the high pressure side and the low pressure side are separated by a low tolerance flat surface.
It is said that their efficiency is more or less around 85%, not great, not terrible.
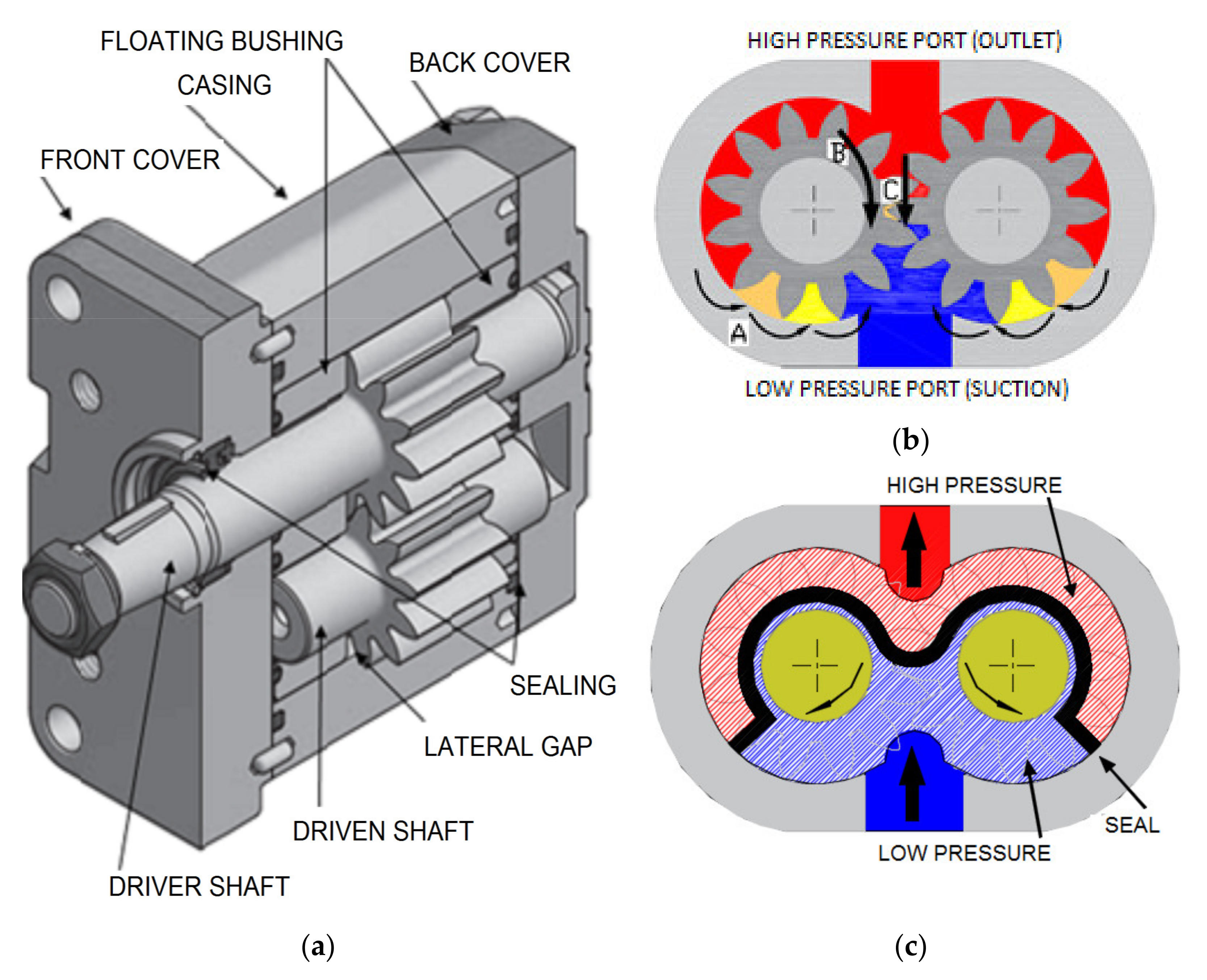
However, I think it is for the better if I at least try to copy the gear pumps that I can easily find online instead of the untested design of an axial wobble plate pump.
Maybe I'm just imagining its working principle incorrectly.
On slower animations you can see that only one piston is being fully driven per revolution, such as this one:
Unfortunately, I really can't find an affordable piston pump, axial or radial. These cost around 600 dollars up to 1000 dollars, and since 1 dollar is more or less 5 reais, then you can imagine how expensive it is for me.
I think that for a radial pump, I would be forced to modify a radial piston engine instead of the previous conventional radial pump.
Because the distance of travel is strictly proportional to the diameter of the central bearing, while in an engine, even a radial one, the distance of travel is proportional to the diameter of the crankshaft.
This means that in a conventional radial pump, I would only have a limited amount of piston travel, meaning that I would have a limited amount of fluid flow while not benefiting from the mechanical advantage, needing more torque and more speed to rotate.
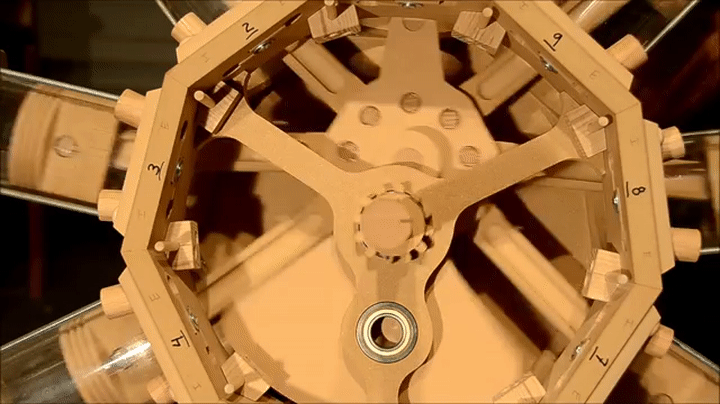
But even still, I'm conflicted between the piston pump and the gear pump.
The gear pump has a proven design that I can easily copy and find off-the-shelf pieces, but it has lower efficiency compared to a piston pump.
The piston pump needs to be built from scratch, may need custom or unique pieces that I may or may not mess up, but it would be easier to garantee/build the sealing in a cylindrical shape, unlike the high precision flatness of the gear pump (supposedly).
Also, I was thinking on instead of using one-way valves, using mechanically activated valves.
The only reason for that would be to make the pump reversebly operated, so if I want the hydraulic cylinder to extend or retract, I would just revert the electric motor instead of relying on a solenoid valve.
Solenoid directional valve for hydraulic system, which would be necesary to change the flow from connecting to the pump, the tank and the two parts of an actuator.
---------------------------------------------------------------------------------------------------------------------------------
Also, I forgot to talk about the new power requirement.
The 4500 watts (6hp) will be used to apply 3000kg to each of 3 actuators on the legs to be able to lift 1 ton of weight on the body and/or the carrying capacity.
The upper body will only need to apply 1 third of that, 1500 watts (2 hp) and the arms aswell..
Giving a total of 22500 watts (30hp) per hour.
If you add the extra cost of one of the legs/arms moving without weight, let's say, half of this wattage, it would be 33750 watts (45 horsepower).
If you add the inneficiencies, let's say 20% to 30%, you would need 40,500 watts/54 hp to 43,875 watts/58.5 hp.
The 200,000 watts iron-air battery would last for around 5 hours.
Of course, this doesn't count the attempts of efficiency, such as letting the torso with more or less passive suspension and/or the reversibility of the compressor between the high pressure parts of the actuator. But I would bet these would save around 5-10% at best.
---------------------------------------------------------------------------------------------------------------------------------
Well, I was thinking on how I would make an hydraulic pump that could change the fluid flow depending in which direction it works, but I couldn't think on anything but gear pumps, and actually, I think hydraulic gear pumps aren't meant for this kind of job.
I would either need a complicated (and expensive) direction control valve or a servo ball-valve in which the direction of flow would change on how much one turns the valve:

However, I'm still not satisfied.
So I thought on the concept of an "alternating one-way valve" that is way simpler.

Well, I hope it is clear, but the image is just an illustration, on an actual alternating one-way valve, the size would be way smaller.
(I think this guy made a better version than mine, lol)
I would need to put two of these in order to achieve the same thing, I believe.
It is still way better than my original idea.
I need to find a way of making hydraulic hoses on the cheap and DIY.
I thought on using conventional rubber hoses as a liner and then adding metallic fibers as an improvised braided sleeve, adding layers of rubber and at each tip, the walls of the hose would turn into a flat pancake with a hole in the middle.
Then at the ends of what would be the hydraulic connections, a screwing hollow nut would be added, so the "pancake" would be compressed between two metal nuts, making a strong seal.
(I need to draw this)

I know I said that I wanted to avoid hoses because of the loss of efficiency and complexity of manufacturing the hoses and hydraulic accumulators, but making 30+ electric motors with hundreds, if not thousands of magnets is quite a pain the ass.
So better making it like that...?
Anyway, about the single electric motor driving a single pump for the sake of simplicity of actuators.
Each actuator would have the electricity evenly distributed to the system, meaning that every fluid flow, rpm and torque of each actuator will be automtically and proportionally divided.
So, how do I achieve the best fluid flow for the entire system? Yes, I can add a hydraulic accumulator that will be opened to each actuator, avoiding unnecessary expend of energy, however, what if the motor can't provide enough flow?
I was kinda thinking here on how much fluid flow and pressure I would be able to achieve with the final 58.98 horsepower, and basically, I would need a radial hydraulic piston pump in which each piston has 20mm of diameter, a 100mm of stroke and a pressure of 90 bar or less, I would achieve 450 liters per minute of fluid flow.
Now I will try to see how much fluid flow the "divided system" (the electro-hydraulic actuators were the electric motor and pump are directly connected to the hydraulic actuators) achieves:
1- each pump will be driven by at maximum 40nm-50nm of torque and maximum 1000 RPM.
Assuming that the piston pump has 10mm of inner diameter and 100mm of stroke, each piston would have 0.008 liters.
0.008 liters times 5 pistons times 1000 RPM = 43 liters per minute.
2- On one leg there will be at least 3 pumps working at same time, so 130 liters per minute in one leg.
3- On the arm and torso I would need less torque, but the same RPM, so still 43 liters times 3 plus the same for the torso, resulting in 260 liters per minute + 130 = 390.
Even though the other half will be working with half the wattage, the torque will be lesser, but the rpm, and thus, the fluid flow, will be the same, so, 130 + 130 + 130 = 390.
So, in total 390 + 390 = 780 liters per minute in total.
... Dang... I guess that is really a big difference, huh? No "central pump" idea then.
-----------------------------------------------------------------------------------------------------------------------------------------
By the way, I need to make every bolt, nut and screw custom made, since I have no fricking idea of what is the standard issue for hydraulic cylinders and even if I had, I wouldn't be able to buy, neither make copies precise enough for this work.
I also need to make the hydraulic pump and all of its components.
About the electro-hydraulic actuator:
In this specific version I won't make a proper 3D model of a telescopic cylinder simply because I need to have any kind of change in the overrall shape to be "laser cutable" so to speak.
If there is a "bump" on the design, the bump will be a totally different object smashed on the original object, and thus glued to the final mold. Of course, I will try to make a less... Convoluted piece after I'm finished, but I'm making no promises.
Besides, I will try to make everything with a thickness of at least 10mm, just like the steel 5ton-rated hydraulic cylinder.
Also, while I was looking at hydraulic cylinders on GrabCad, I saw some models which had sensors for pressure inside of the cylinder, which I thought it was a cool idea.
So I will try to make/add both sensors for pressure and maybe for linear positioning, the pressure is the easiest one, the sensor for positioning, not so much.
Basically, I will make a hole with a smaller piston, so the force applied to the little piston will be proportional to the pressure inside of it.
For example, if this micro-piston has 8.5 mm of diameter force of 18.0198 kg will be applied to it when the system reaches 90 bar of pressure, so I could use a cheap load cell for this task.

Well, since the encoder is a wire-based one, I don't see why not just put it on the outside, lol.
Explaining in a simple way: telescopic hydraulic cylinders have a big empty space under the stages, so instead of letting these spaces empty, I will add an extra column in the middle, so I need less fluid flow to fill the actuator up.
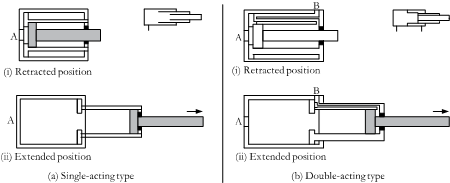
Of course, in the image the last stage is a solid piston for the sake of simplicity, but I will try to make a hollow one for the aforementioned reason.
Also, the increase in surface area may result in less pressure and thus, less heat. So I can keep the system in a closed-loop without the fear of overheating the oil.
Open-loop = after the oil exits the actuator it goes to a oil reservoir, the closed-loop don't have that and may need active cooling for the oil, reducing efficiency of the overrall system.
Also², I was thinking on adding a car-spring hydraulic accumulator connected to the central pump and a smaller springed hydraulic accumulator on each side of the hydraulic cylinders for damping impacts.
So, the "central" hydraulic accumulator is for saving energy when the mech/exosuit isn't moving and the smaller hydraulic accumulators are meant to work a damping mechanism for impacts, not impacts on the piston, but "fluid impacts" so to speak.
Let's say, if I jump or fall over a hydraulic cylinder, the piston will compress the fluid inside the cylinder, absurdely increasing the inside pressure of the thing, going beyond the internal pressure in which the mechanism was made to withstand.
With a hydraulic accumulator directly connected to the cylinder, the impact will be damped by the spring/gas, since these are compressible, unlike the fluid (if you don't know, fluids aren't compressible, that's why hydraulics are so powerful).
Although, I don't like the idea of three hydraulic accumulators on total (more parts = more pieces to make), so I think I will make a double hydraulic accumulator with the spring mechanism in the center (I say "spring mechanism" because car dampers are basically pneumatic-hydraulic hybrid springs).

So, well, the idea is to put this double hydraulic accumulator between the hydraulic input of both ends and connected to the single pump, but I forgor to draw it like that.

Or I could just use a less complicated version of this:
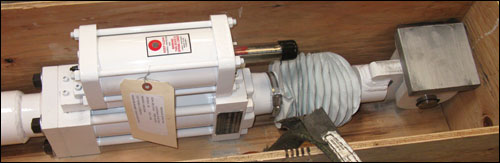
This video kinda looks interesting, instead of a basis from where the cylinder rises, the cylinder goes towards both directions, making a somewhat simpler telescopic cylinder.

Also², couldn't I just add a car spring to the axis instead of add an extra thing to the system?
... I feel like I'm just getting more and more complicated on the subject of electro-hydraulic actuators. The electric-mechanical version of this system wouldn't even need half of the extra stuff these need...
---------------------------------------------------------------------------------------------------------------------------------
Dunno if anyone cares, but I just saw this actuator and it blew my mind:
The electromagnetic coupling would actually use a little bit of energy, since locking electromagnets can lift hundreds of kg with a few watts and the seals would be easier to make, since I don't have to make a hole on it in order to pass the piston rod.
However, I don't know how a telescopic version of this would work...
Also, there are hydraulic, pneumatic and electrical rodless cable cylinders, the pneumatics are 20 to 30% efficient, hydraulic is 80-90%, electrical 90-95%. :|
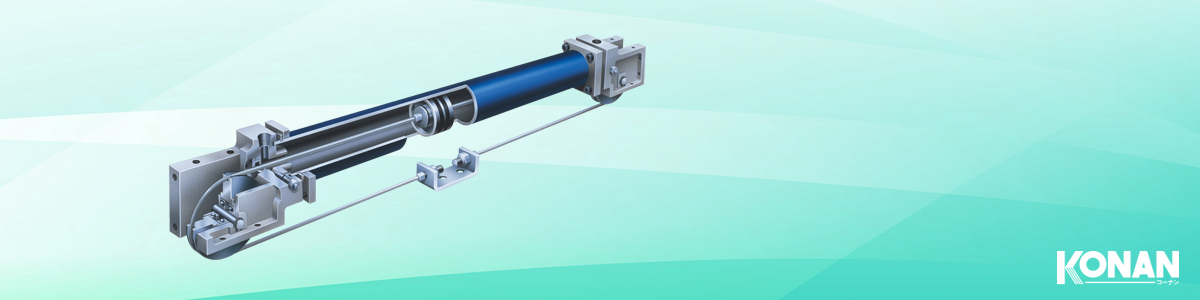
In order to make these telescopic, one would need to attach a new rodless actuator to the moving table.

Like this, I suppose...
---------------------------------------------------------------------------------------------------------------------------------
The 10:1 maximum reduction ratio in an electro-mechanic system serves precisely to act like a spring action for the system, but in a electro-hydraulic system, I would need an actual spring action hydraulic accumulator and/or a snubber with extra seals.
With an electro-hydraulic system I would need solenoids, valves, pumps actuated by electric motors and a myriad of different seals and the structural integrity on top of all of that, in an electrico-mechanical version I just need to worry about bearings and the structural integrity of the system in which would be directly coupled by electric motors.
The positives of an electro-hydraulic system compared to the electrical counter part is that the hydraulic system does not need energy just to stay still, doesn't need reduction gears and doesn't need to deal with the inertia of reverting the system.
In fact, I think I got the whole pump concept wrong, for example, one could use a smaller, but way faster brushless motor for a more compact system (of course, with the proper consideration for cavitations and overheating).
I would guess that it would be a great system for a heavy duty mobile application, but is lifting 3 tons a heavy duty application?
I don't even know what to do right now.
I wasted so much time questioning which direction to go that I could've finished something by now.
A lot of youtubers (and friends of mine) always say that mistakes and the time spent learning about new things is very useful.
But to be honest, I just feel dumb and like I wasted time looking into options that clearly wouldn't work.
It makes me wonder if I'm being too harsh on myself tho...
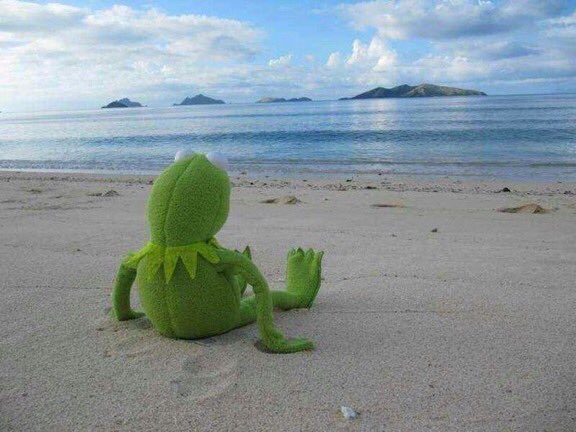
---------------------------------------------------------------------------------------------------------------------------------
Also, now that I have a little more knowledge on hydraulics/pneumatics in general, I went back to check out the MckIbben muscles and see how much energy those would use.
Well, I took the 20%-30% efficiency ratio for the pneumatic ones, because pneumatics really are inefficient in general.
For what I could calculate, I would more or less use half of the wattage for more or less the same amount of work and fluid flow than a conventional hydraulic cylinder.
I would basically use 40-50 bar of pressure (taking the Hacksmith video on McKibben muscle) to apply 1000kg of force, meaning that I would need 120 bars of pressure in a single muscle for a 3000kg force muscle.
(well, I guess that the low efficiency matches, since I would need such amount of pressure, and thus, power/torque/energy to apply the same amount of force)
In any way, Even though I absolutely love artificial muscles, I would only move 7 cm in length, while a telescopic hydraulic cylinder would be travelling around 20cm or more in a smaller package.
The advantage is that hydraulic muscles are light (even lighter than aluminium cylinders), relatively simple to make and somewhat safer to use around humans (I think).
Still, I would need 2250 watts for every 1 ton McKIbben muscle if such muscle were to be used with a pump directly connected to it.
So, counting the wattage in only one side of the mech/suit would be the same stewart platform scheme for every limb, so 9 muscles using 2250 watts each for the lower body + the 3 muscles using 2250watts each on the torso and the 3 muscles on the arms using the same amount of energy:
I would basically be using around 33750 watts/45 horsepower in total.
Its efficiency is 66% compared to the hydraulic cylinder, and both values are meant to be the ideal result of energy conversion, if not 100%, and even then, the muscle lacks compared with conventional actuators. In reality, its efficiency would be way lesser. Thus, meaning that the value of 20% to 30% efficiency is correct.
Or my calculation may be incorrect, since I'm assuming that 100kg of force at 4-5 bar of pressure is the ideal efficiency, after all, it was based on a pneumatic McKibben muscle.
I already posted this article on various project logs, but I don't know what was the final energy efficiency, what he talks about is "190% of Transduction efficiency", which I don't quite understood what this means. Maybe that it is 1.9 times more efficient than a 30% efficient muscle? Meaning 57% efficiency?
This one says that the above article said it achieved 80% efficiency, maybe it is a bad interpretation?
It seems like reversibly actuated muscles are way more efficient (achieving 88% efficiency without counting losses) than McKibben muscles. Source (it is said to be pneumatic, dunno if an hydraulic version would be even better or not).
This one is hydraulic and it is said to be 61% efficient and it uses silicone tube, I would bet that by wrapping everything on teflon (or other low-friction material) you could increase the efficiency.
For how much? I don't know.
It would need to be more anatomical and complex, and well... I already got messed up by its complexity in early project logs...

Holy crap, artificial muscles really are cool...
Also, while looking online for new Hydraulic McKibben muscles I saw a self-contained hydraulic muscle where a screw actuator would push the fluid into the muscle.
One could add the linear screw pump inside the muscle (assuming the muscle is big enough).
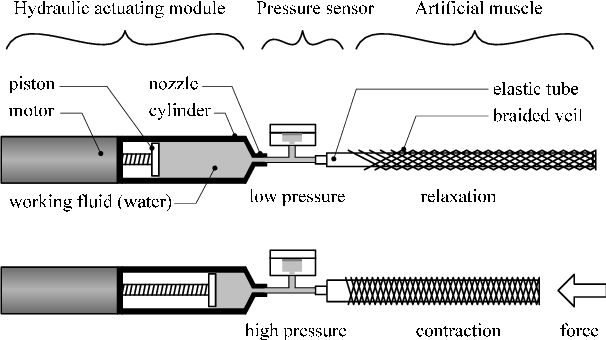
There were other links/papers/websites suggesting that it would be better if there were a single linear pump for an entire bundle of thin muscles in which the pump would be enveloped/hidden/protected.
Also, I found this flexible hdyraulic cylinder, one could turn it in a flexible hydraulic pump if the wire were pulled by an electric motor.
Source: https://iopscience.iop.org/article/10.1088/1742-6596/1820/1/012068/pdf
But at that point, wouldn't be easier to "just" attach the electric motor directly to the limb?
I think I would need a micro piezoelectric hydraulic pump...

Or maybe a solenoid micro pump... humm
(I posted a gif showing said pump, but it seems that I wrote so much stuff in this Project log that it is already deleting text)

I was thinking here, depending on how you work with this, you could put the solenoid pump on two muscles and due to the alternating one-way valves (that would also be solenoids), you could simply activate both muscles at same time with a single pump.
On top of that the whole thing could be inside a bag full of hydraulic oil, which would help cool down the solenoids and the fluid.
And this gif kinda gives me an idea how directional valves work, the thing with solenoids is that the core will always be magnetically attracted to the center of the coil, so you need multiple coils which would attract the core in different positions.
Also, I was kinda wondering how well it would work if you replaced the core with a permanent magnet...
This micro pump can still be used in either artificial muscles or cylinders.
So I think this little tangent was worth the trouble, I guess...
Discussions
Become a Hackaday.io Member
Create an account to leave a comment. Already have an account? Log In.