21/07/2023, Friday, 18:50.
Well, hello, this is me from the future and I need to add some informations about Iron-Air battery.
The theoretical energy density of iron-air battery is in the range of 1200 wh/kg and I optimiscally assumed that I could achieve at least 1000 wh/kg, which may or may not be too unrealistic.
From what I could find, even in the best laboratory attempts, the iron-air battery "only" achieved at best 750 wh/kg of energy density and conventional attempts achieved "only" 300 wh/kg (still higher than lithium-ion batteries [250 wh/kg], but far away from 1000wh/kg).
Even if I were to crush catalytic converters to use as catalysts, this is still a DIY setup and I doubt I would achieve crazy values such as 700 to 1000, which even scientists had difficulty achieving.
You could use this battery idea or you could look for other options.
I will get a look around and maybe change to lithium-air (achieved around 1500 wh/kg) batteries or aluminium air batteries (achieved 1300 wh/kg).
The aluminium air battery can be made in the exactly same way as the iron-air battery, although I would advise you to have great care with aluminium powder, it can expontaneously combust into thermite reaction, which can melt even tungsten.
However you don't need to make the aluminium anode out of aluminium powder, aluminium foil is enough.
By the way, I posted a few other fuel options for alkaline fuel cells (suggested by ChatGPT). You could even use ethanol.
The only problem is that ethanol is still a hydrocarbon, and once it reacts with the oxygen and generates electricity, it will also release the carbon dioxide molecules, which can poison the alkaline fuel cell.
The only way to use hydrocarbon fuels (fossil fuels) is by using the Steam Reforming process, but I can't find a way of miniaturizing it, neither making it safe to use.
I say this because ethanol is quite cheap and can be found/made almost anywhere, although high quality ethanol may not be that cheap.
It makes me wonder if increasing the water content per ethanol would help dissolve the CO2 generated in the water and avoid the Co2 poisoning of the KOH electrolyte...
---------------------------------------------------------------------------------------------------------------------------------------------
This is such a little bit of information that I tried to simply add to the Project Log 63, but it seems like I've been doing it so much that I can't even add text to that Project Log anymore, the website justs bugs out (I think I will do the same to this one).
By the way, I won't make the "69" joke when I reach the Project Log 69.
I'm not trying to post random posts about different things just to make a bulk. I'm just an unorganized idiot.
-------------------------------------------------------------------------------------------------------------------------------
One thing I also forgot to talk about in the previous Project Log about the Iron-Air battery is the vacuum box.
You don't really need actual vacuum to work with pure iron powder, you could use an argon and/or helium filled glove box in order to work with these highly reactant materials (like pure iron powder).
I just say this because it is very hard to maintain actual vacuum and inflating a giant transparent plastic box may be easier to build and use.
You could just use helium cans for party balloons or argon gas for wine storage:
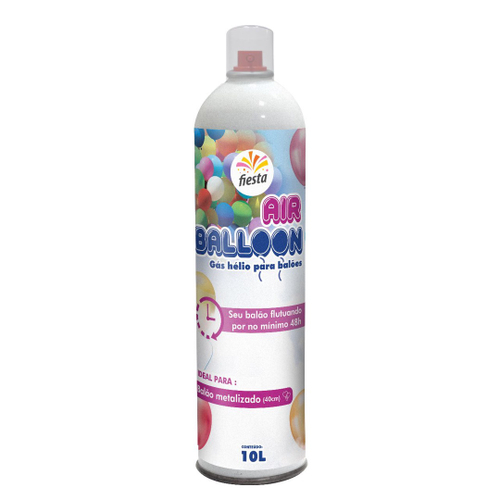

However the last option may not be as cost-effective as helium gas, since this argon for wine is still as expensive as an argon tank.
-------------------------------------------------------------------------------------------------------------------------------
I was trying to think in a way of mass producing the cells of the Iron-air batteries in a DIY setup.
Of course, this isn't that easy, but I got some ideas while searching on the internet.
More specifically, I was searching for 3D printable presses that I could use for the soft magnetic composites for the stators of the electric motors.
One of these presses wasn't meant for actually crushing things, but for gold stamping on paper. It looked like a cloth wringer, and that's exactly how I would "mass produce" the pieces of the Iron-air battery.

I would take the goop that would be the membrane and "just" press it through the machine multiple times, making a thin and uniform membrane that would look more like a long and transparent plastic. Then I would roll it and apply the solutions I described in previous project logs.
Then I would do the same to the iron electrode and air electrode, but I don't know how well it would work, sinc ethe iron electrode is a good and the air electrode needs to be cooked at 500ºC.
It would basically be like using a rolling pin to make the stuff.
Althought I don't think I would be able to make a wringer press, I think I could use a rolling pin.
-------------------------------------------------------------------------------------------------------------------------------
... To be honest, I don't feel like I thought this through (for a change).
When making the membrane, it takes up to 24 hours to dry out, and I don't what would happen if you were to take the goop while drying and then mess with it. Like molding it into shape and so on.
This person kinda does it, but it is for a totally different reason, it is for glue, not for an Ion Exchange Membrane. I don't know how well messing with this slime would be to the overall efficiency/performance of the Iron-Air battery.
-------------------------------------------------------------------------------------------------------------------------------
Well, I've been talking so much about how to make each part of an Iron-Air battery that I totally forgot about its structure.
Luckly, there are some open source 3d models on GrabCad.
... For fuel cells.
Well, like I said before, an Iron-air battery is basically an hydrogen fuel cell, but without the hydrogen, so these are useful the sasme way.
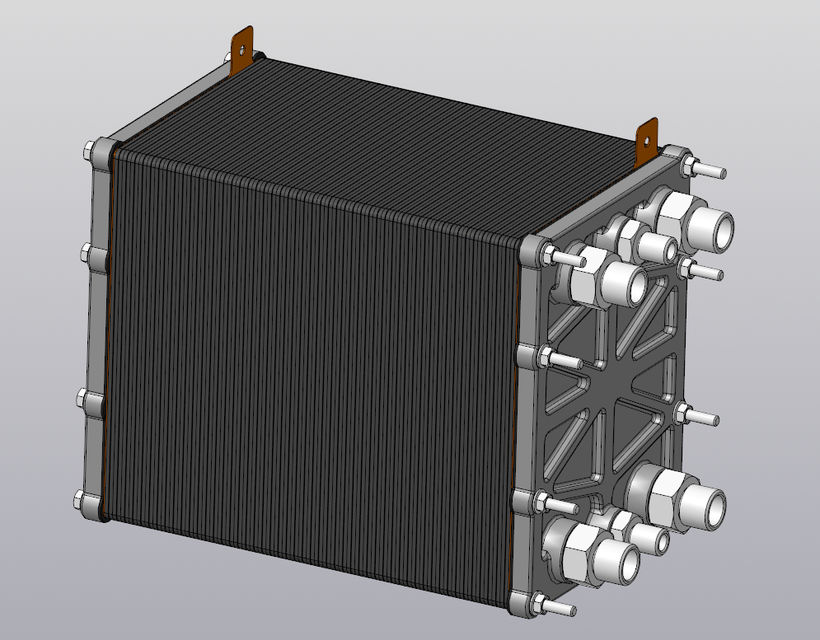
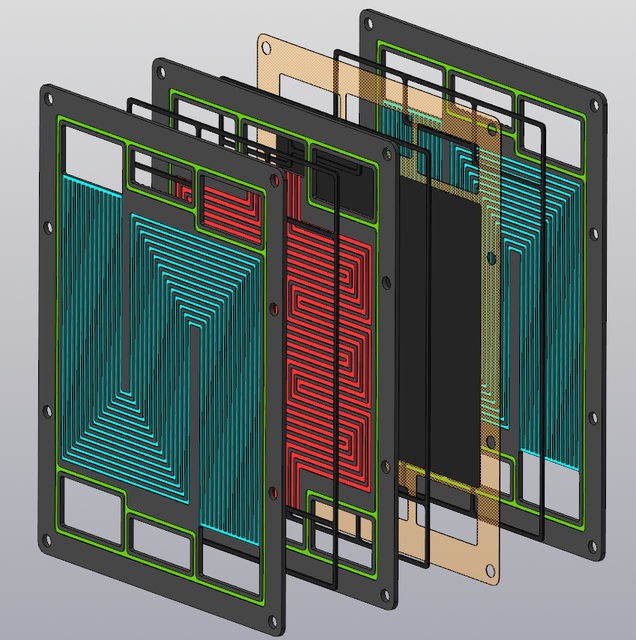
Images from this one: https://grabcad.com/library/pem-fuel-cell-1
This one is an HHO fuel cell tho, but you can modify it: https://grabcad.com/library/hho-generator-an-alternative-fuel-1
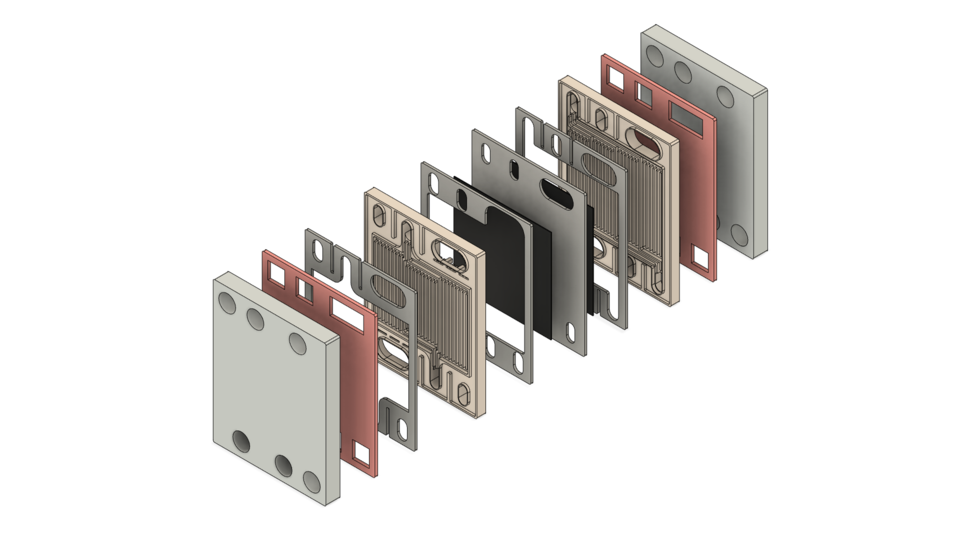
Source: https://grabcad.com/library/proton-exchange-membrane-fuel-cell-1
There are more on GrabCAD, but these are the best ones I could find.
Besides, I will try to make my own 3D model later on blender.
-------------------------------------------------------------------------------------------------------------------------------
"In the presence of Sodium Hydroxide (NaOH) and Potassium Hydroxide (KOH), some conductive metals are more resistant to corrosion than others. Among the commonly used metals, the following are known to be relatively resistant to corrosion in alkaline environments:
- Stainless Steel: Certain types of stainless steel, especially those containing high amounts of chromium (e.g., 316 stainless steel), offer good resistance to corrosion in both Sodium Hydroxide and Potassium Hydroxide solutions.
- Nickel: Nickel and its alloys, such as Monel (a nickel-copper alloy) and Inconel (a nickel-chromium alloy), exhibit good corrosion resistance in alkaline solutions.
- Titanium: Titanium is generally resistant to corrosion in alkaline environments, including those containing Sodium Hydroxide and Potassium Hydroxide.
- Tantalum: Tantalum is highly resistant to corrosion in a wide range of chemical environments, including strong alkaline solutions.
- Hastelloy: Hastelloy is a family of corrosion-resistant alloys that contains varying amounts of nickel, molybdenum, and chromium. Some grades of Hastelloy offer good resistance to alkalis.
It's important to note that even these resistant metals may experience some level of corrosion over extended exposure to strong alkaline solutions, but their resistance is notably better compared to other commonly used metals like carbon steel or aluminum.
Always consider the specific concentration and temperature of the alkaline solution, as well as the duration of exposure, as these factors can influence the corrosion resistance of metals. If you require a high level of resistance, it's advisable to consult with materials engineers or specialists to select the most appropriate metal for your specific application."
-------------------------------------------------------------------------------------------------------------------------------
Me:
What are cheap sources of precious metals that can easily be purified?
For example, titanium by itself is expensive, but titanium dioxide is cheap and can be exposed to reduction reaction by exposing it to hydrogen gas at high temperatures.
ChatGPT:
While I can provide general information, I want to emphasize that working with precious metals and their extraction involves specialized knowledge and can be potentially hazardous. Always ensure you have the proper equipment, safety measures, and knowledge before attempting any purification processes.
That said, here are a couple of examples of inexpensive sources of precious metals and potential purification methods:
- Silver Recovery from Photographic Films and X-ray Plates: Photographic films and X-ray plates contain a thin layer of silver compounds. The silver can be recovered through a process called electrolysis, where the film is immersed in a solution and an electric current is passed through it. The silver dissolves and deposits onto a cathode.
- Copper Anode Slimes for Gold and Silver: During the electrorefining of copper, slimes containing small amounts of gold and silver can be generated. These slimes can be processed to extract the precious metals. One method involves treating the slimes with nitric acid to dissolve the silver and gold, then precipitating them using other chemicals.
- Electronic Waste (E-Waste) for Precious Metals: Electronic waste, such as discarded computer components and printed circuit boards, can contain valuable metals like gold, silver, and palladium. Various methods, including chemical leaching and electrolysis, can be used to recover these metals from e-waste.
- Catalytic Converters for Platinum Group Metals: Catalytic converters in vehicles contain platinum, palladium, and rhodium. Although the extraction process can be more complex, these metals can be recovered from spent catalytic converters through smelting and refining.
- Sewage Sludge for Precious Metals: Sewage sludge can contain trace amounts of precious metals, including gold and silver, due to their presence in household waste. Researchers have explored techniques like bioleaching to extract these metals from sewage sludge.
- Gold and Silver from Ore Leaching Residues: After traditional gold and silver extraction processes, residues may contain trace amounts of these precious metals. Additional processing steps, such as cyanide leaching, can help recover these residual metals.
Remember, the purification of precious metals requires specialized knowledge and equipment. Additionally, legal and environmental considerations are important when dealing with these materials. Always research and adhere to local regulations and safety guidelines before attempting any extraction or purification processes.
There are several methods used for extracting platinum and other precious metals from catalytic converters and other sources. These methods can vary in complexity, efficiency, and environmental impact. Here are a few alternative methods:
- Pyrometallurgical Methods:
- Smelting: High-temperature smelting can be used to melt down the catalytic converter material, separating the metals based on their melting points. This method is commonly used in industrial settings.
- Hydrometallurgical Methods:
- Acid Leaching: Apart from aqua regia, other acid solutions like sulfuric acid or hydrochloric acid can be used to selectively dissolve platinum and other precious metals.
- Alkaline Leaching: Alkaline solutions like sodium cyanide can be used to leach out platinum and other metals. However, this method can be hazardous due to the use of toxic chemicals.
- Ionic Liquids: Specialized ionic liquids can be used to selectively dissolve platinum and other metals while minimizing the environmental impact.
- Biotechnological Methods:
- Biomining: Certain microorganisms can be used to selectively extract metals from ores and waste materials. This method is being researched for its potential application in recovering precious metals.
- Electrometallurgical Methods:
- Electrolysis: Electrolytic methods involve passing an electric current through a solution containing platinum, causing the metal to deposit onto an electrode. This can be used for refining purposes.
- Solvent Extraction and Precipitation:
- Solvent Extraction: Organic solvents can be used to selectively extract platinum from a solution. The extracted platinum is then recovered from the solvent.
- Precipitation: Chemical agents can be used to selectively precipitate platinum from a solution, allowing for its separation.
- Ion Exchange:
- Ion Exchange Resins: These resins can selectively adsorb platinum ions from a solution, allowing for easy separation and recovery.
It's important to note that these methods are often used in combination, and the choice of method depends on factors such as the composition of the catalytic converter material, the desired purity of the recovered metals, and environmental considerations.
Due to the complexity and potential hazards associated with these methods, it's strongly recommended that individuals without proper training and equipment do not attempt to extract precious metals from catalytic converters or other sources. Instead, catalytic converter recycling companies and specialized precious metal refining facilities should be consulted for safe and responsible metal recovery.
Electrometallurgical methods, including electrolysis, can indeed be used to extract platinum and other metals from solutions containing dissolved metals, such as those obtained from crushed catalytic converters. However, the specifics of the process, including the choice of electrolyte (the fluid used in the process), depend on various factors and require a good understanding of electrochemistry.
In the context of catalytic converter recycling, the following steps could be involved in an electrolytic extraction process:
- Dissolution: The catalytic converter material is first dissolved using an appropriate chemical process, such as acid leaching, to create a solution containing platinum and other metals.
- Electrolysis Setup: The solution is then used as an electrolyte in an electrolysis setup. Electrolysis involves passing an electric current through the electrolyte, causing metal ions to migrate and deposit onto an electrode (cathode).
- Electrodeposition: In the electrolytic cell, a suitable electrode material (often a conductive metal like graphite or platinum) is used as the cathode. When the current flows through the cell, platinum ions in the solution will migrate towards the cathode and be reduced (gain electrons), leading to the deposition of platinum metal on the electrode surface.
- Collection and Purification: The platinum deposited on the cathode can be collected and further purified through additional refining steps.
The choice of electrolyte depends on factors such as the concentration of platinum and other metals, the desired deposition rate, and the overall electrochemical conditions. Common electrolytes include various acid solutions or even ionic liquids, which offer unique properties for specific applications.
It's important to note that while electrometallurgical methods can be effective for metal recovery, they require careful control of process parameters and a good understanding of electrochemistry to achieve desired outcomes. Handling electrolytic processes also requires safety considerations due to the potential for chemical reactions and the generation of gases at the electrodes.
As previously mentioned, attempting these processes without proper knowledge and equipment can be dangerous and environmentally harmful. If you have catalytic converters or other sources of precious metals that you wish to recover, it's recommended to work with specialized recycling companies or experts who have the necessary expertise in metal extraction and refining techniques.
The choice of acid for use in metal extraction processes, such as recovering platinum from catalytic converters, can vary based on factors like the specific application, the nature of the materials being processed, and the desired outcomes. In the context of platinum recovery, aqua regia and hydrochloric acid are commonly used.
Hydrochloric Acid (HCl): Hydrochloric acid alone is also used for dissolving platinum and other precious metals. While it may not be as aggressive as aqua regia, it can still effectively dissolve platinum and form soluble chloro-platinum complexes.
The choice of electrolyte for an electrolytic extraction process, such as recovering platinum from solutions obtained from catalytic converters, depends on factors such as the specific electrochemical conditions, the type of electrodes being used, and the solubility of platinum compounds. In general, electrolytes used for platinum recovery may include various acid solutions or ionic liquids. Here are a few examples:
- Sulfuric Acid (H2SO4): Sulfuric acid is a strong acid commonly used as an electrolyte in various electrochemical processes. It can be used for platinum recovery if suitable conditions are established. Sulfuric acid can help dissolve platinum compounds and facilitate the migration of platinum ions during electrolysis.
- Hydrochloric Acid (HCl): Similar to sulfuric acid, hydrochloric acid can be used as an electrolyte. It can help in dissolving platinum and promoting platinum ion migration during electrolysis.
- Ionic Liquids: Ionic liquids are molten salts that are liquid at or near room temperature. They have gained interest as electrolytes due to their unique properties and the ability to be tailored for specific applications. Some ionic liquids may be designed to selectively dissolve platinum compounds and allow for efficient electrodeposition.
The choice of electrolyte should be made based on a thorough understanding of the electrochemical behavior of platinum and other materials involved. Additionally, safety considerations, environmental regulations, and proper waste disposal methods should be taken into account when working with electrolytes, especially those that contain hazardous chemicals.
It's important to emphasize that working with electrolytes and electrochemical processes requires expertise in electrochemistry and the proper handling of chemicals and equipment. If you're interested in platinum recovery or any other metal extraction process, it's strongly recommended to seek guidance from professionals or specialized companies that have experience in these areas.
Although each video is really useful for extracting these types of material, I would advise to not do it.
You could simply clean up the catalytic converters using either proper cleaners and/or vinegar bath.
The catalytic converter comes in a ceramic matrix honeycomb tructure for ideal surface area contact for the catalytic reactions that occur, you could either crush it to a fine powder or cut it in order to add to the iron electrode slime in order to use it as a catalytic converter.
Not everyone (including me) has the capacity to actually melt this thing just to remelt it with the iron, not to mention that other videos suggest using nitric acid, which is highly toxic and dangerous to use.
So I would advise using a proper cleaner or just a DIY method to get the "juice" that you need.
This guy uses a cleaner called "purple power", it is an "industrial strength" cleaner.
This one just uses a vinegar bath.
And this one uses a lacquer thinner, but I think it is a little bit expensive, a single bottle is like, 100 reais (+/- 20 dollars), although thte guy said at the end of the video it didn't work, I wonder if it would work if you let the catalytic converter submerged in a bath made out of this.
Besides, other people use carburator cleaner to clean the catalytic converter.
-------------------------------------------------------------------------------------------------------------------------------
Me:
"How many liters of pure oxygen at ambient pressure and/or at 4 bar of pressure in order to fully oxidize 200kg of pure iron?"
The reaction between iron (Fe) and oxygen (O2) to form iron oxide (Fe2O3), commonly known as rust, can be represented by the following balanced chemical equation:
4 Fe + 3 O2 -> 2 Fe2O3
From the balanced equation, we can see that 4 moles of iron react with 3 moles of oxygen gas to produce 2 moles of iron oxide.
First, let's calculate the molar mass of iron (Fe) and oxygen (O2):
- Molar mass of Fe: 55.85 g/mol
- Molar mass of O2: 2 * 16.00 g/mol = 32.00 g/mol
Now, let's calculate the moles of iron in 200 kg:
Moles of iron = Mass / Molar mass Moles of iron = 200,000 g / 55.85 g/mol ≈ 3581.74 moles
Using the stoichiometric ratio from the balanced equation, we can calculate the moles of oxygen required:
Moles of O2 = (3/4) * Moles of iron ≈ (3/4) * 3581.74 ≈ 2686.30 moles
Now, let's calculate the volume of oxygen gas required at both ambient pressure and 4 bar pressure. The ideal gas law equation is:
PV = nRT
Where: P = pressure (in atmospheres or bar) V = volume (in liters) n = moles of gas R = ideal gas constant (0.0821 L.atm/mol.K or 0.0831 L.bar/mol.K) T = temperature (in Kelvin)
Assuming room temperature (around 298 K), we can calculate the volume of oxygen required at both ambient pressure and 4 bar pressure:
For ambient pressure (1 atm): V_ambient = (2686.30 moles * 0.0821 L.atm/mol.K * 298 K) / 1 atm ≈ 65,733.62 liters
For 4 bar pressure: V_4bar = (2686.30 moles * 0.0831 L.bar/mol.K * 298 K) / 4 bar ≈ 16,456.74 liters
So, you would need approximately 65,733.62 liters of pure oxygen at ambient pressure or 16,456.74 liters of pure oxygen at 4 bar pressure to fully oxidize 200 kg of pure iron. Please note that this calculation assumes ideal behavior of gases and does not take into account any potential side reactions or impurities."
-------------------------------------------------------------------------------------------------------------------------------
I'm asking this because a CO2 scrubber will only add unnecessary weight to the system, and it would a pain in the butt to make it work with a compressor.
So I think it would be for the best if I were to simply make a self-contained vessel in which the iron-air battery could be in the presence of pure oxygen.
Not to mention that the production of hydrogen and its reaction with the iron oxide wouldn't generate extra water.
It would more or less look like this:
Being honest, I don't like the content of this guy that much because he always take the proposterous claims of cash-grab companies as true. So he basically have a video about a "revolutionary" technology every week.
However, it is a NASA battery, so maybe it has some value on it.
-------------------------------------------------------------------------------------------------------------------------------
Me:
"What fuels can and cannot be used on alkaline fuel cells?
For example, iron-air batteries are basically an alkaline fuel cell were iron is used instead of hydrogen."
"Alkaline fuel cells (AFCs) are versatile in terms of the fuels they can potentially use. They are not limited to hydrogen like some other types of fuel cells. However, the choice of fuel can affect the efficiency, performance, and overall operation of an alkaline fuel cell. Here are some fuels that can and cannot be used in alkaline fuel cells:
Fuels that Can be Used in Alkaline Fuel Cells:
- Hydrogen (H2): Hydrogen is the most common and efficient fuel for alkaline fuel cells. It produces electricity through the electrochemical reaction of hydrogen ions and oxygen, resulting in the formation of water as the only byproduct.
- Ethanol (C2H5OH): Ethanol can be used as a fuel in alkaline fuel cells. It undergoes oxidation at the anode to produce electricity. Ethanol fuel cells have been researched and can potentially offer advantages in terms of availability and ease of handling compared to hydrogen.
- Methanol (CH3OH): Methanol can also be used as a fuel in alkaline fuel cells. Similar to ethanol, methanol undergoes oxidation at the anode to generate electricity. However, methanol fuel cells often face challenges related to the crossover of methanol through the electrolyte, which can reduce efficiency.
- Formic Acid (HCOOH): Formic acid is another potential fuel for alkaline fuel cells. It can be oxidized at the anode to produce electricity. Formic acid has attracted interest due to its high energy density and potential for use in portable and backup power applications.
- Zinc: Zinc-air batteries are a well-known type of metal-air battery. Zinc undergoes oxidation at the anode and oxygen from the air is reduced at the cathode.
- Aluminum: Aluminum-air batteries have also been investigated. Aluminum reacts with oxygen to generate aluminum hydroxide, releasing energy in the process.
- Lithium: Lithium-air batteries have potential for high energy density, but they face challenges related to the stability of the electrolyte and cathode materials.
Fuels that May Have Challenges in Alkaline Fuel Cells:
- Hydrocarbons (e.g., gasoline, diesel): While it is theoretically possible to use hydrocarbons as fuels in alkaline fuel cells, these fuels often require reforming processes to extract hydrogen, which can introduce complexity and reduce overall efficiency.
- Ammonia (NH3): Ammonia has been investigated as a potential fuel for alkaline fuel cells. However, its high toxicity and challenges associated with handling and storage have limited its practical use.
- Other Organic Compounds: While various organic compounds can undergo oxidation in alkaline environments, their practical use as fuels in alkaline fuel cells may be limited by factors such as reaction kinetics, crossover issues, and overall efficiency.
- Methanol (CH3OH): Methanol is one of the most widely studied organic compounds for use in fuel cells, including AFCs. It is a simple alcohol that can undergo electrochemical oxidation at the anode to produce electricity. Methanol fuel cells have been explored for applications such as portable electronics and backup power systems. However, they can face challenges related to fuel crossover, which can reduce overall efficiency and pose safety concerns.
- Ethanol (C2H5OH): Ethanol is another alcohol that has been investigated for use in AFCs. Similar to methanol, ethanol can be oxidized at the anode to generate electricity. Ethanol fuel cells have the advantage of using a less toxic and more readily available fuel source compared to methanol.
- Formic Acid (HCOOH): Formic acid is a simple carboxylic acid that can serve as a fuel for AFCs. It can undergo oxidation at the anode to produce electricity and water. Formic acid has attracted attention due to its high energy density and potential use in portable and backup power applications.
- Glycerol (C3H8O3): Glycerol is a triol (a compound with three hydroxyl groups) that can be derived from the biodiesel production process. Glycerol has been explored as a potential fuel for AFCs, as it can undergo electrochemical oxidation at the anode to produce electricity.
- Ethylene Glycol (C2H6O2): Ethylene glycol is a diol (a compound with two hydroxyl groups) commonly used as antifreeze. It has been investigated as a potential fuel for AFCs, with its oxidation at the anode contributing to electricity generation.
- Lactic Acid (C3H6O3): Lactic acid is a carboxylic acid produced during fermentation processes. It has been studied as a potential fuel for AFCs, where it can undergo electrochemical oxidation at the anode.
The example you provided of iron-air batteries is an interesting one. Iron-air batteries operate similarly to alkaline fuel cells but use iron as the fuel source instead of hydrogen. In an iron-air battery, iron undergoes oxidation at the anode to generate electricity, and oxygen from the air is reduced at the cathode to form iron oxide (rust). Iron-air batteries are known for their potential high energy density and could offer advantages in terms of cost and safety compared to some other energy storage technologies.
It's worth noting that research and development in the field of fuel cells are ongoing, and new fuels and technologies continue to be explored. The feasibility and practicality of using specific fuels in alkaline fuel cells may vary based on technological advancements and specific application requirements.
"In an alkaline ethanol fuel cell, the primary reactions involve the oxidation of ethanol to produce electricity, along with the generation of carbon dioxide (CO2) and water. The CO2 generated as a byproduct needs to be managed to prevent undesirable interactions with the electrolyte (often a potassium hydroxide, KOH, solution). One way to handle the CO2 is to use a carbon dioxide absorber or scrubber within the system. Here are a few options to consider:
- Ammonia Solution (Ammonia Scrubbing): Ammonia (NH3) can react with carbon dioxide to form ammonium carbamate, which is soluble in water. This reaction helps to remove CO2 from the system. The ammonium carbamate can then be further processed or neutralized as necessary.
- Soda Lime: Soda lime is a mixture of sodium hydroxide (NaOH) and calcium oxide (CaO). It's commonly used to absorb carbon dioxide from exhaled air in medical applications. The sodium hydroxide in soda lime can react with carbon dioxide to form sodium carbonate, which is water-soluble and doesn't interfere with the KOH electrolyte.
- Amine Solutions: Certain amine compounds can react with carbon dioxide to form solid or liquid compounds that can be removed from the system. For example, monoethanolamine (MEA) can react with CO2 to form a water-soluble compound that can be separated from the electrolyte.
- Solid Sorbents: There are various solid sorbent materials designed to capture and store carbon dioxide. These materials can be integrated into the fuel cell system to absorb the CO2 and prevent its interaction with the electrolyte.
- Carbonate Formation: If carefully controlled, the carbon dioxide could potentially be allowed to react with any excess potassium hydroxide (KOH) in the system to form potassium carbonate (K2CO3), which is more soluble and less likely to cause issues with the electrolyte.
It's important to note that the specific choice of materials and methods will depend on factors such as the operating conditions of the fuel cell, the concentrations of CO2 generated, the compatibility of the chosen materials with the fuel cell components, and the overall system design.
Before implementing any CO2 capture or neutralization method, it's advisable to conduct thorough testing and analysis to ensure that the chosen approach effectively prevents undesirable interactions between CO2 and the electrolyte while maintaining the fuel cell's performance and stability."
------------------------------------------------------------------------------------------------------------------------------
By the way, something that I forgot to talk: gas diffusion layers.
Well, at first I thought "yeah, it is just a porous layer, that's it", but it is not that simple.
My fear is that the carbon material (like the carbon sponge I suggested making) may poison the Potassium Hydroxide electrolyte, because CO2 can poison it, so why not a literal sponge made out of carbon?
So I would suggest using the room-temperature sintering process and a wire mesh for that.
Translation: you just take the "ingredients" required for each electrode, such as the catalytic powder and polyvinil alcohol (basically transparent PVA glue) mix both on Acetone and/or Ethanol, spray it on the wire mesh and wait the acetone/ethanol drying out.
Although I'm not very confident with this method, you could still use Sodium Silicate mixed with the catalystics and other materials (such as the conducting material) and the "sacrificial material", then put it in a furnace/oven so the sacrificial material evaporates/burns out leaving only the useful stuff that you want.
------------------------------------------------------------------------------------------------------------------------------
"During the sintering process, sacrificial materials are used to create voids or channels within a material that will be removed during sintering, leaving behind a porous structure. These sacrificial materials should have a lower melting point, sublimation point, or burn out at a temperature lower than the sintering temperature of the primary material. Here's a list of potential sacrificial materials you can consider:
- Organic Materials:
- Starch: Starch-based materials can burn out at relatively low temperatures, leaving behind voids.
- Cellulose-based materials: These can also decompose at lower temperatures.
- Salts:
- Ammonium salts: Ammonium compounds like ammonium bicarbonate or ammonium chloride can decompose and release gases at moderate temperatures.
- Sodium bicarbonate: Also known as baking soda, it releases carbon dioxide upon heating.
- Potassium carbonate: This can decompose and release carbon dioxide at elevated temperatures.
- Polymers:
- Polyethylene glycol (PEG): PEG can melt and evaporate at relatively low temperatures.
- Polyvinyl alcohol (PVA): PVA can be used as a water-soluble sacrificial material.
- Polystyrene microspheres: These can be used to create pores in the material.
- Metals:
- Zinc powder or particles: Zinc can sublime at high temperatures, leaving behind pores.
- Tin powder or particles: Tin can also sublime at elevated temperatures.
- Ceramic Materials:
- Calcium carbonate: This can decompose to calcium oxide and carbon dioxide at higher temperatures.
- Calcium sulfate: Also known as gypsum, it can decompose to calcium oxide and sulfur dioxide.
- Foaming Agents:
- Blowing agents: These are compounds that release gases upon heating, causing the material to expand and form voids.
- Natural Fibers:
- Wood fibers: These can burn out at elevated temperatures.
- Waxes:
- Paraffin wax: Paraffin can melt and evaporate at relatively low temperatures.
Remember that the choice of sacrificial material depends on the specific application, the sintering temperature of the primary material, and the desired properties of the final product. It's important to conduct thorough testing and optimization to ensure that the sacrificial material effectively creates the desired porosity or channels without negatively affecting the structural integrity of the final product. Additionally, ensure proper ventilation and safety precautions when working with materials that release gases or fumes during processing."
Like I said, there are a lot of methods you could use.
------------------------------------------------------------------------------------------------------------------------------
I found this blog from an actual chemist that was able to make a nafion-comparable DIY Ion exchange membrane:
And thus, I guess I could in fact achieve something closer to 50% instead of 30-40% with the other type of membrane.
And the better part is that it doesn't need to be in an alkaline fluid, meaning that I don't really need Co2 scrubber neither to carry around caustic soda and caustic potassium in a bag. :)
The recipe:
The process for preparing these membranes is as follows:
- Prepare a solution by adding 15g of PVA to 200mL of water (solution A).
- Place solution A in a fridge for 48 hours, with occasional stirring/shaking. Surprisingly, cold conditions are much better for dissolving PVA because they discourage agglomeration.
- Wait till solution A is fully homogeneous, keep longer in fridge and shake/stir as needed.
- Prepare another solution by using 0.5mL of phosphoric acid (81%), 0.5g of citric acid and 15mL of solution A. This solution is stirred until everything is completely homogeneous (solution B).
- Dip a filter paper in Solution B. I used Stony Lab 101 but other fine grain filter papers should work just as well. Make sure all excess has dripped off and tap with paper towels to remove any excess.
- Place on a hot plate at 80C for 3min
- Flip it to the other side for another 3 minute.
- Use a brush to paint solution B on the filter paper while on the hot place.
- Wait for 3 minutes.
- Flip the filter paper and paint the other side, wait another 3 minutes.
- Repeat steps 8-10 three times.
- Increase the temperature to 150C.
- Flip the membrane every 10 minutes for one hour or until the membranes appear fully black. Put a petri dish on top if needed to keep the membrane flat.
- Allow the membrane to cool to room temperature.
- Place the membrane in a solution with 10g/L of potassium or sodium carbonate to neutralize any remaining acid, they can be stored in a 0.5M NaCl solution.
The membranes that result from this process are black in nature. However they do not feel like charcoal and do not crumb easily. Instead, they have the feeling of a piece of plastic film, which is exactly what we are looking for. Several papers discussing citric acid crosslinking of different polymers do have resulting black films, so this isn’t necessarily a bad thing.
The other type of membrane made with the membrane from lead acid batteries (that are cheaper to make:
An improved DIY cation exchange membrane with less degradation using a Daramic PE microporous separator as base
11 Replies
In my previous posts about cation exchange membranes, I created a membrane using cross-linked PVA over a cellulose support. For this purpose, I used a filter paper and then applied successive layers of a solution with PVA, phosphoric acid and citric acid, which I then heated to 150C to create the final cross-linked membrane. This procedure created a membrane that had high permselectivity, decent in-plane conductivity and that could be produced for very low cost.
The problem however, came from the fact that the membrane degraded in the presence of Mn3+ , which was generated when the Mn|Fe chemistry I am testing is cycled. The degradation became apparent as the red color of the Mn3+ faded with time, although no crossing of the Mn3+ across the membrane happened. There were also a lot of bubbles generated on the membrane on the Mn side, which is further evidence supporting this degradation mechanism.
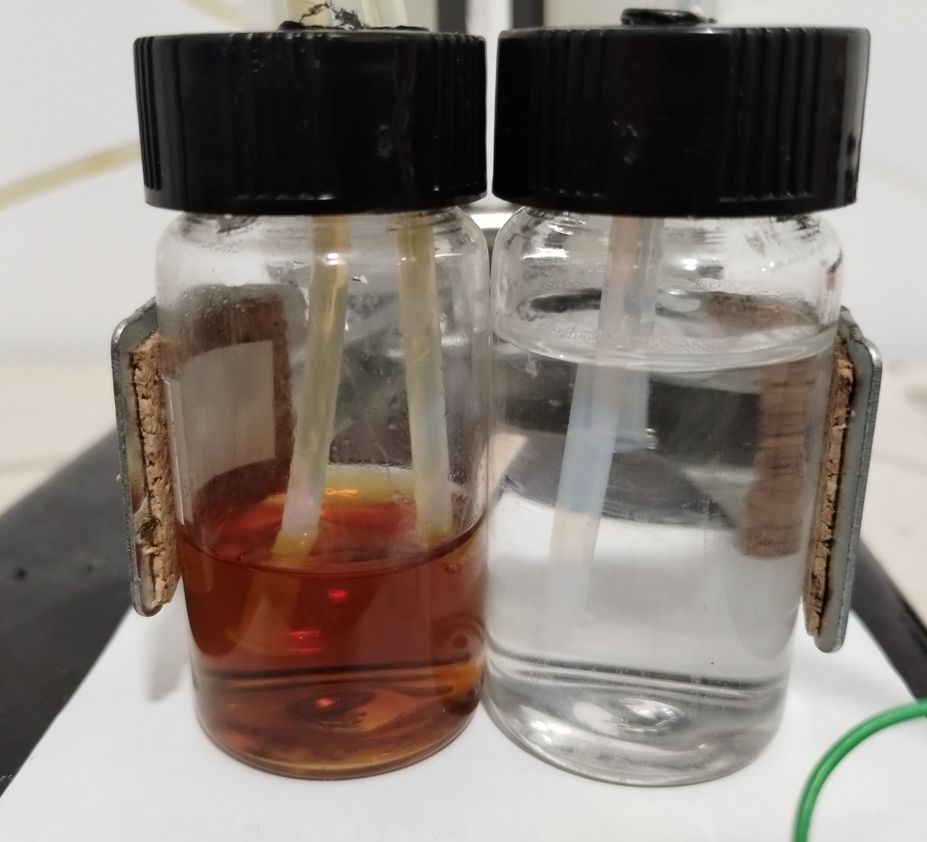
I think that this degradation happened mainly because of the cellulose, which is the most reactive part of the structure. To try to alleviate this problem, I decided to move away from the cellulose support and try to cross-link the PVA over a more stable substrate. To achieve this I performed the same cross-linking process, but this time doing it over a daramic polyethylene separator as support.
The Daramic is a microporous polyethylene separator – commonly used in lead acid batteries – which can be purchased for very little cost (only a few dollars per square meter). The daramic has a well defined pore size that can be filled with the PVA solution. Upon heating and reapplication of the solution, the pores can be filled with the cross-linked cation exchange material, with the daramic matrix providing the main source of structural support.
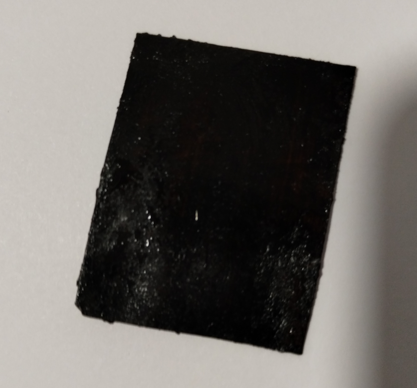
After the material has been saturated, heated to dryness and resaturated/redried multiple times with the polymer solution (10mL 14% H2SO4, 15g PVA, 8g citric acid, 250mL of water), the Daramic is then heated to 150C for one hour to finalize the process. The Daramic film created is black and has a permselectivity greater than 95%, measured in a cell with 0.1M KCl | 0.5M KCl. The first image in this post also shows how absolutely no cross-over of an Fe-EDTA salt is seen after running by this PVA+Daramic separator for more than 24 hours. When using just the Daramic microporous separator, cross-over is seen within minutes.
The great news is that the Daramic support is made of polyethylene, so it is very unreactive. The crosslinked PVA is also way less reactive than the cellulose, enough so that it now doesn’t react with Mn3+. I generated some of this material through electrolysis of an Mn-EDTA solution, and the crosslinked daramic didn’t bubble or degrade the Mn3+ after a couple of hours.
Sadly my potentiostat broke due to a small lab accident (spilled liquid over it), so I am waiting for a new potentiostat to be delivered to perform the first cycling experiments using this new cation exchange separator.
Well, I asked a couple of questions with the author in the website (you can even see it on his website), but it seems like it may not be the best option (as it is now).
In his words, it is a Nafion comparable membrane in the matter of permeability, not conductivity and durability.
I think you/I will need to make do with that old idea of simply mixing membranes and passing them through a crosslink/chemical bath.
For example, I can only find PBI resins for reverse osmosis membranes, but I would need to make a phosphoric bath in order to properly turn those into a good proton exchange membrane.
Plus, I would need to mix other types of membranes, such as PES-based membranes that are normally sold as syringe filters.
I will try to find a way of making these membranes more conductive, but I'm not very confident.
"To increase the electrical conductivity of a DIY membrane based on PVA (Polyvinyl Alcohol) and PVP (Polyvinylpyrrolidone), you can consider incorporating certain conductive additives. Here are a few options you can explore:
- Graphene: Graphene is a highly conductive material consisting of a single layer of carbon atoms. Adding graphene to the PVA/PVP membrane can significantly enhance its electrical conductivity.
- Carbon nanotubes: Carbon nanotubes (CNTs) are cylindrical carbon structures with excellent electrical conductivity. Incorporating CNTs into the membrane can improve its conductivity.
- Conducting polymers: Polymers such as polyaniline, polypyrrole, and poly(3,4-ethylenedioxythiophene) (PEDOT) are known for their inherent electrical conductivity. Blending these conducting polymers with PVA/PVP can enhance the overall conductivity of the membrane.
- Metal nanoparticles: Adding metal nanoparticles, such as silver (Ag) or gold (Au), to the membrane can improve its electrical conductivity. The nanoparticles can create conductive pathways within the membrane matrix.
It's important to note that the choice and concentration of the conductive additive will depend on the specific requirements of your application. Additionally, the fabrication process of the membrane and the dispersion of the additives within the PVA/PVP matrix can also impact the final conductivity. Experimentation and optimization may be necessary to achieve the desired conductivity while maintaining good membrane permeability."
Assuming that ChatGPT isn't talking crap, then I could "just" mix this to the lead-acid separator and increase its conductivity and durability at same time, since I can just make milk graphene and/or buy conductive silver paste from electronic stores.
Obviously, an KOH based membrane/electrolyte wouldn't have this issue, since it is already fairly conductive and efficient
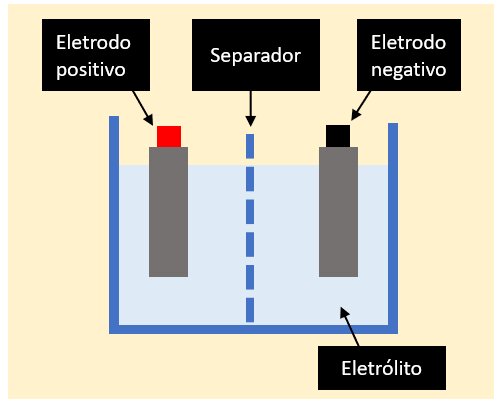
It is in brazilian portuguese, but basically, the electrodes are submerged in an electrolyte while being separated by the microporous Separator.
You may not even need a membrane in this case, but the only reason I want to avoid alkaline fuel cells is precisely because it is based on highly acidic materials such as Potassium Hydroxide, Hydrochloric Acid and Sodium Hydroxide.
All are fairly cheap to buy and relatively easy to maintain, but still, acidic stuff, acid burns, hazardous fumes etc.
Now the remaining question is: how many cells I will need for 10kw to 20kw per hour, totallying 100kw to 200kw?
For now I can only think of total weight.
For example, some hydrogen fuel cells that I can find online, such as the one below, has 4kg of weight and delivers 1,000 watts per hour while consuming 14 liters of hydrogen at 5bar of pressure.

You buy from them on your risk, I'm just showing the fuel cell as a reference.
So, if I wanted 10kw of power per hour, I would need to take 40kg of material and make the most amount of fuel cells as possible.
Not very precise, but it is a good rule of thumb.
I've sent an email to the company asking how many cells are there in each 1000 watts stack, but I would bet that there are at least 2,000 to 5,000 individual cells.
(I received an answer and they said it has 60 cells in total, totally different than what I expected, huh)
Just calculating the efficiency of the previously mentioned fuel cell:
So, taking into consideration the energy density of hydrogen at 681 bars of pressure being 39,405.6 wh/Liter, so, at 100 times less pressure, one would have 394 watt hour per liter, giving 5516 wh/l in total.
So this fuel cell would be around 20% efficient.
Discussions
Become a Hackaday.io Member
Create an account to leave a comment. Already have an account? Log In.