I bought a £5 bar of 330x25x5mm SS304 and got it watercut along with the new hotend holder design:
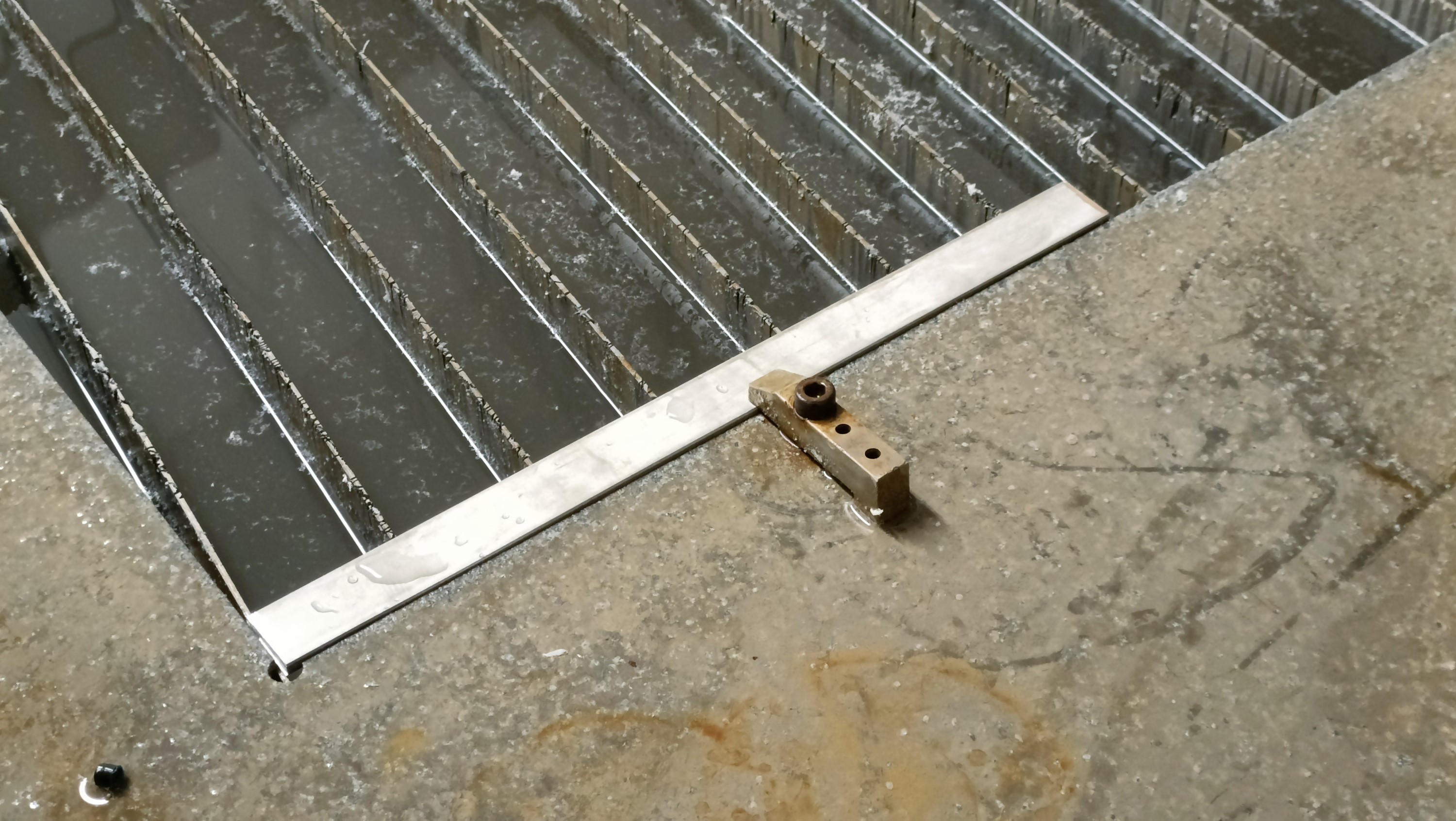
The edges of the stainless parts have an almost perfectly matte satin finish and looks quite nice.
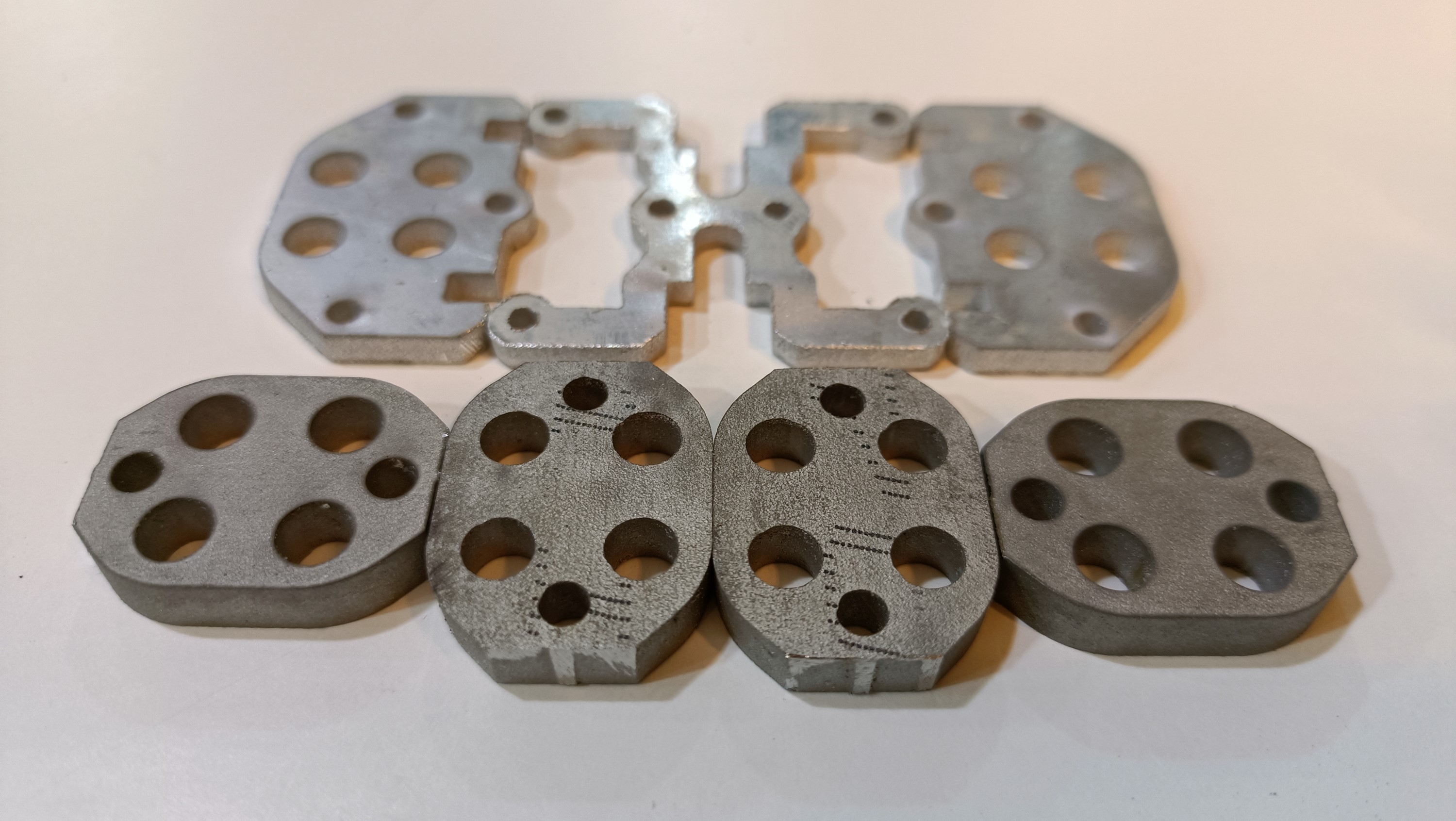
Tapping was tough, but that was mainly me learning the best ways to coat the tap in cutting grease, the importance to align the tap and strongly tighten the clamp and how to apply torque to the tap holder.
It felt like:
- Starting the tapped hole was very easy.
- Ramp up of torque required until it reached "MaxT".
- (coined from MaxQ I hear in SpaceX launches)
- I just had to grow the confidence that the tap wasn't going to snap, especially when the material itself makes "something snapped"-sounding squeaks every so often.
- Lastly, the torque falls off, leaving me with a very smooth-feeling thread.
The offset in the CAD was -0.075mm and I've now doubled it to -0.15mm in an attempt to reduce the torque requirements.
Speaking of hole offsets, when I was tapping the hotend holder top plate, the M3 holes seemed kinda small. Turned out I accidentally applied threads to them in Fusion, but a technician just happened to have a 3.2mm drill bit and a drill press:
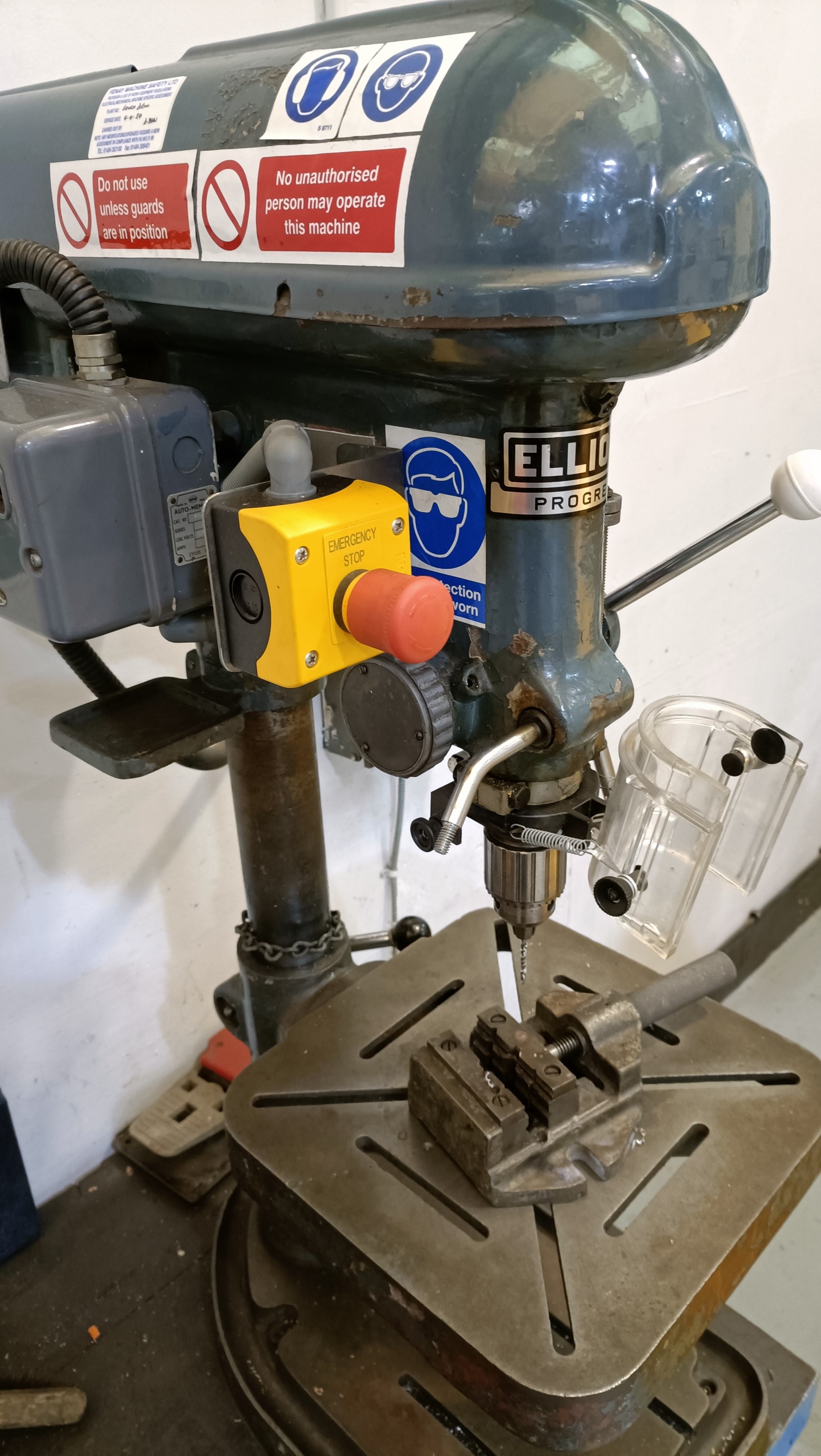
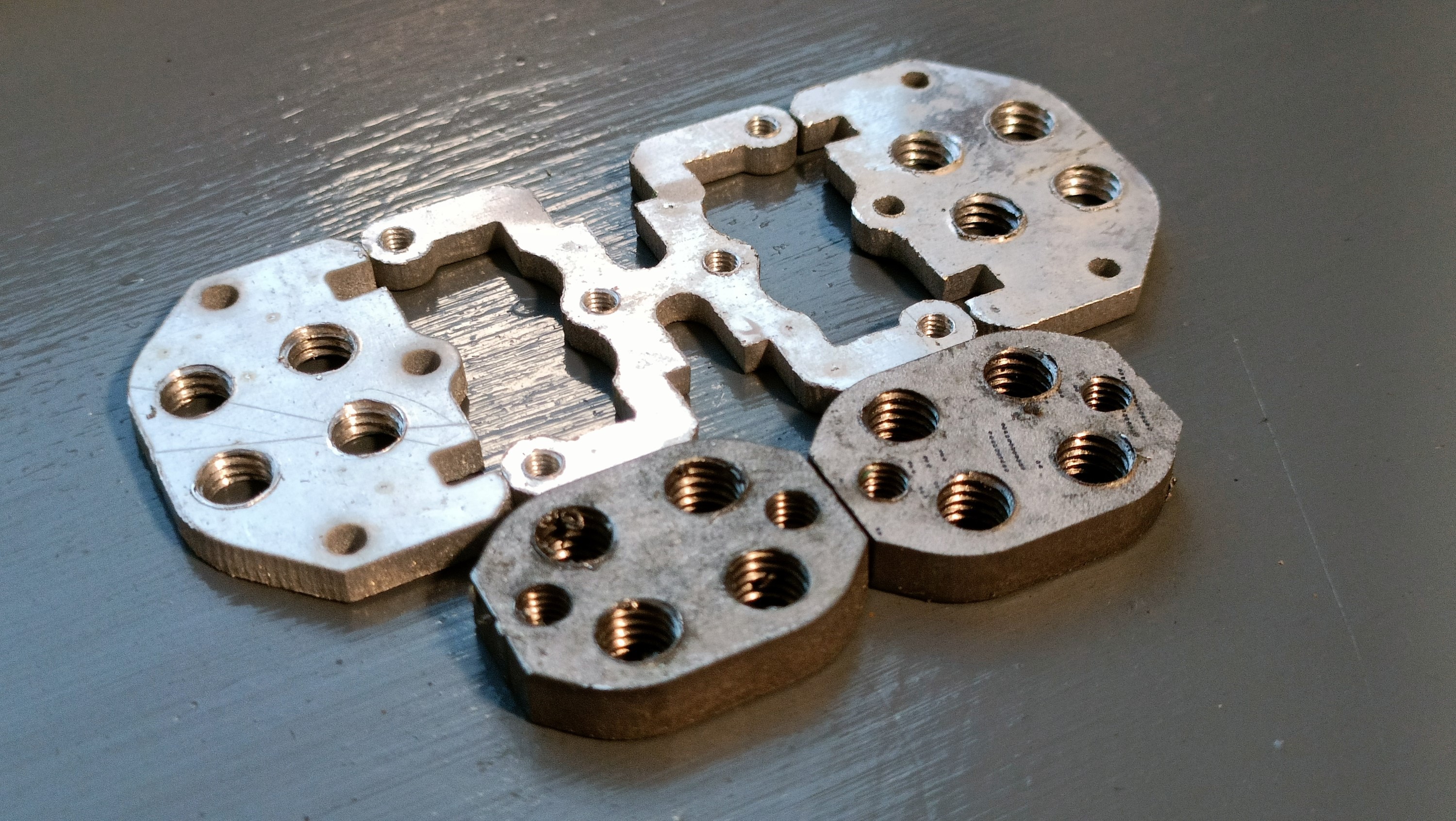
Discussions
Become a Hackaday.io Member
Create an account to leave a comment. Already have an account? Log In.