We printed a holder for the bike suspension, it was made with 20% gyroid infill to withstand the compressive force of the spring.
We sanded the inside, inserted the suspension inside and tried to compress the spring by using the previously bought steel pipe.
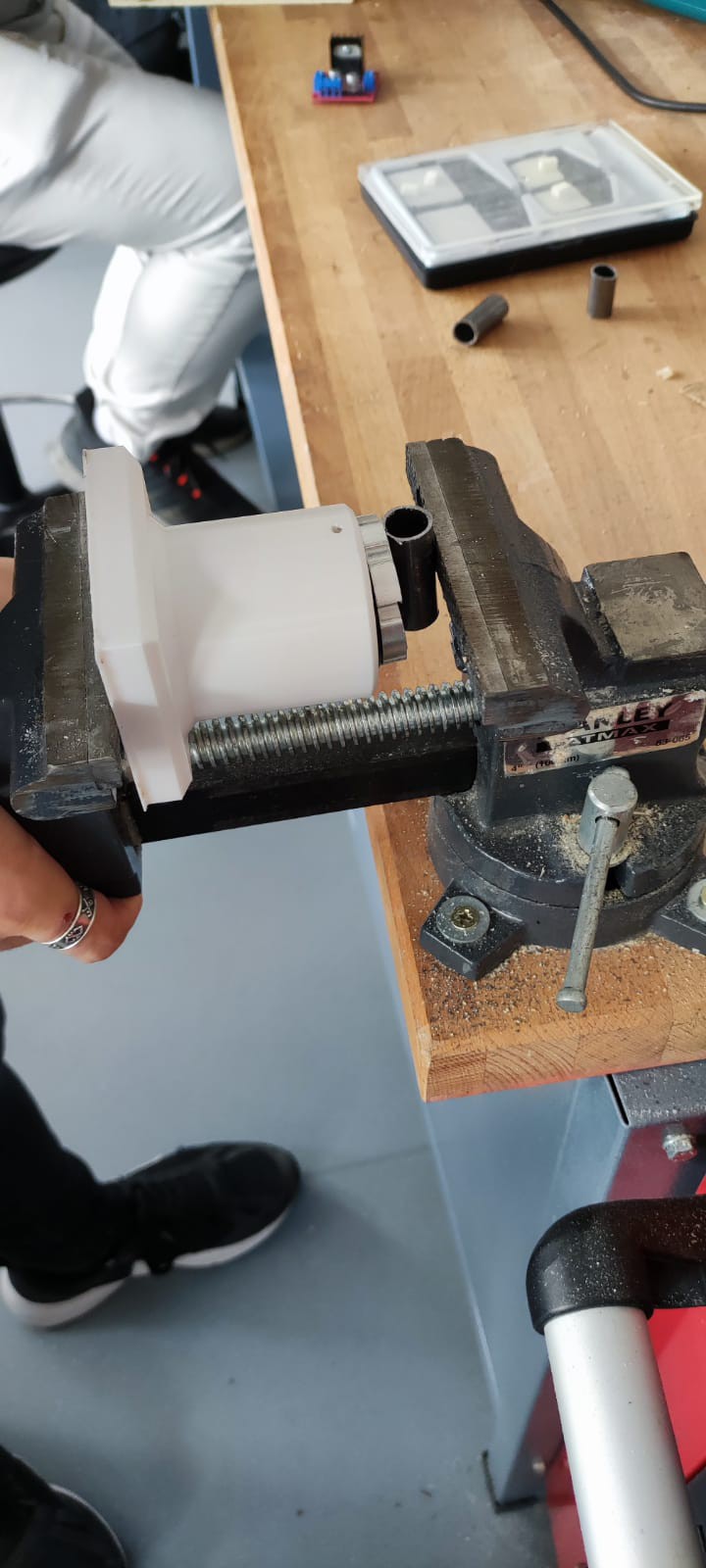
We tried different orientation and even multiple pipes but they got bent in all cases, so we switched to a 3D printed part with 20% triangle infill.
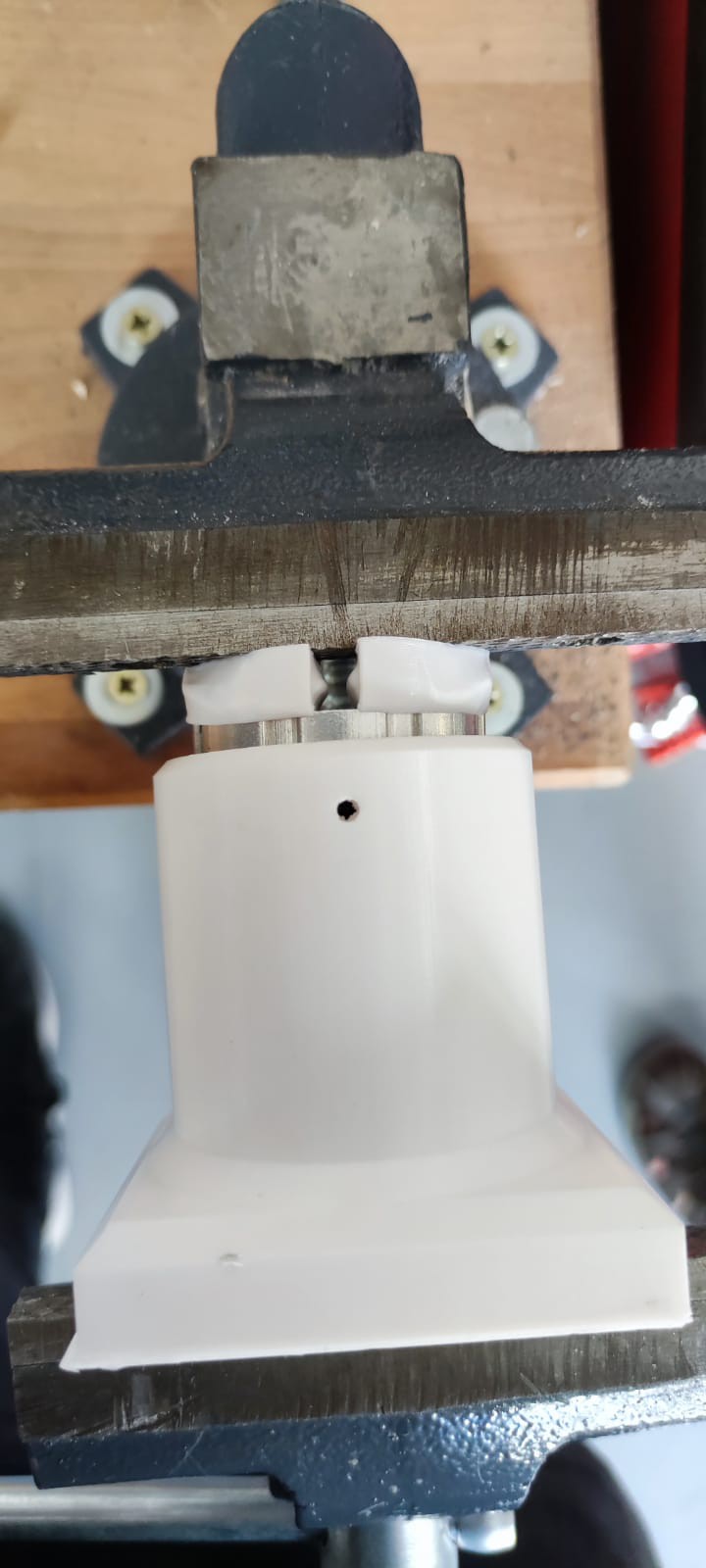
Then 25% infill with concentric infill due to it supposedly high compressive resistance.
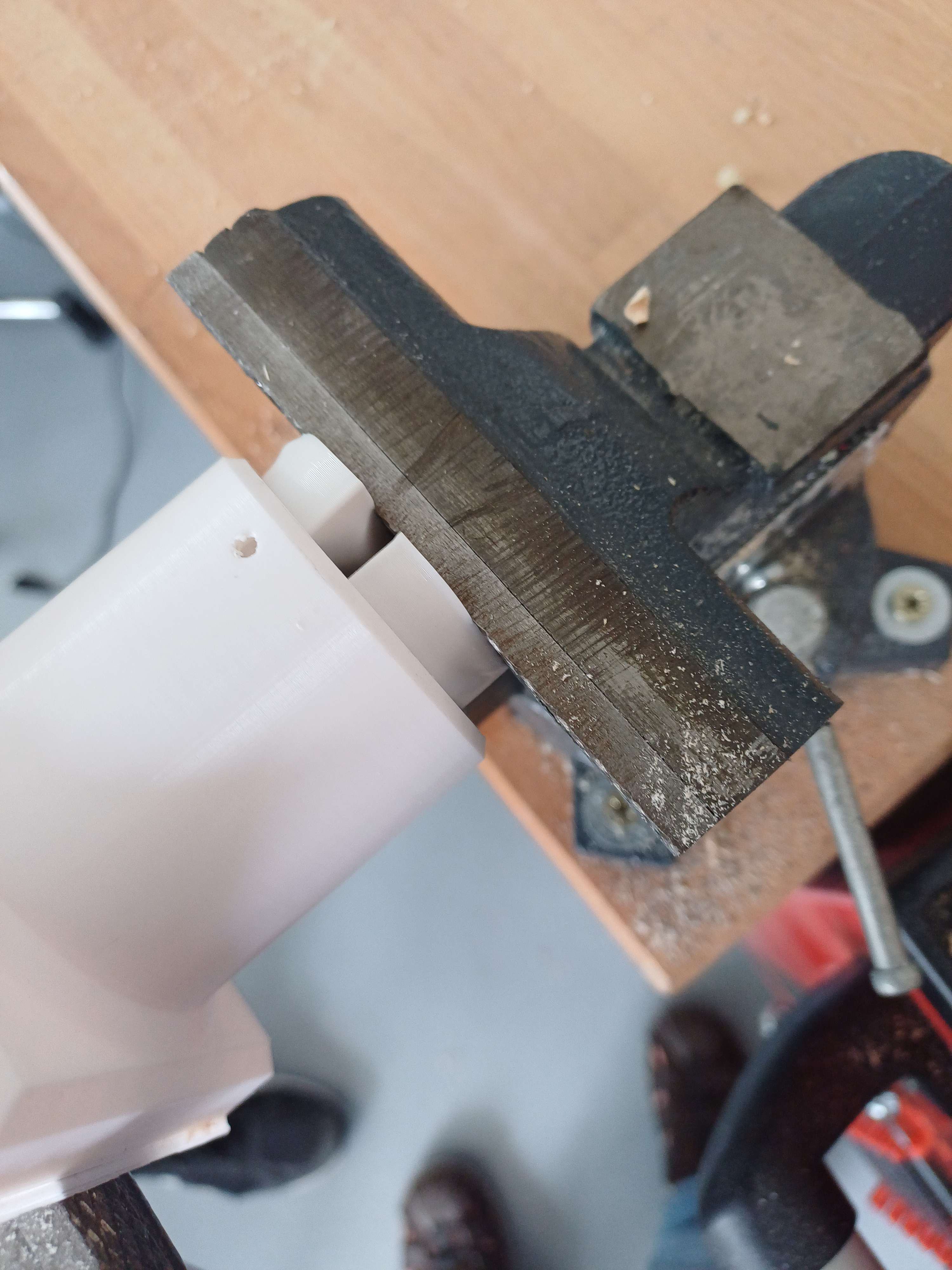
Due to our inability to compress the spring, this part of the project is temporally halted.
We could make this part longer, but this will create additional problem since it's already quite tall and need to be positioned through the skateboard body like so.
If we didn't have a issue with compressing the spring, we would have started to install the quick-release mechanism, consisting of a fixed cutter's blade on the suspension holder and another cutter's blade at the front of the moving rack.
They should be installed in a way that when the rack move (at thus trigger the bolt-mechanism), the string retaining the suspension will be stuck in between the blades and cut, releasing the suspension that will strike the ground.
We updated the necessary components and the electric schematic.
Discussions
Become a Hackaday.io Member
Create an account to leave a comment. Already have an account? Log In.